Top 32 Production Line Worker Interview Questions and Answers [Updated 2025]
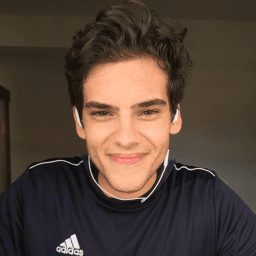
Andre Mendes
•
March 30, 2025
Preparing for an interview as a Production Line Worker can be daunting, but having the right questions and answers at your fingertips can make all the difference. In this updated guide, we delve into the most common interview questions for this role, offering example responses and effective strategies to help you stand out. Whether you're a seasoned professional or new to the field, this post is your key to interview success.
Download Production Line Worker Interview Questions in PDF
To make your preparation even more convenient, we've compiled all these top Production Line Workerinterview questions and answers into a handy PDF.
Click the button below to download the PDF and have easy access to these essential questions anytime, anywhere:
List of Production Line Worker Interview Questions
Behavioral Interview Questions
Can you describe a time when you worked as part of a team on the production line? What was your role and how did you contribute to the team's success?
How to Answer
- 1
Think of a specific project where teamwork was essential.
- 2
Focus on your specific role and tasks you managed.
- 3
Highlight how your actions benefited the team, such as improving efficiency.
- 4
Mention any challenges the team faced and how you helped overcome them.
- 5
Conclude with a positive outcome, like meeting production goals.
Example Answers
In my previous job, our team was tasked with increasing production output on a specific line. I was responsible for quality checks, ensuring products met standards. By organizing our checking process, we reduced errors by 15%, which boosted team efficiency and helped us meet our weekly targets.
Tell me about a situation where you identified a defect in the product. How did you handle it?
How to Answer
- 1
Describe the specific defect you found clearly
- 2
Explain how you discovered the defect logically
- 3
Detail the action you took to address the issue
- 4
Mention any steps you took to prevent future defects
- 5
Conclude with the outcome or lesson learned from the experience
Example Answers
During my time at XYZ Company, I noticed that several products had uneven edges. I found this while conducting routine inspections. I immediately reported it to my supervisor and halted the production line. We corrected the issue by adjusting the machinery settings. This experience taught us to check the equipment more frequently, leading to a 15% reduction in defects.
Don't Just Read Production Line Worker Questions - Practice Answering Them!
Reading helps, but actual practice is what gets you hired. Our AI feedback system helps you improve your Production Line Worker interview answers in real-time.
Personalized feedback
Unlimited practice
Used by hundreds of successful candidates
Describe a time when you had to adapt to a sudden change in production schedules or processes. How did you manage?
How to Answer
- 1
Identify specific change you faced in production schedules or processes.
- 2
Explain your initial reaction and how you assessed the situation.
- 3
Describe the steps you took to adapt quickly and effectively.
- 4
Highlight any tools or strategies you used to communicate with your team.
- 5
Mention the positive outcome resulting from your adaptability.
Example Answers
In my previous role, the production schedule changed when a key supplier delayed delivery. I quickly evaluated our current inventory and coordinated with my team to adjust our workflow, prioritizing tasks that could be completed with available materials. We communicated regularly to ensure everyone was aligned, and as a result, we minimized downtime and met our output goals.
Provide an example of how you effectively communicated with your team to ensure a smooth workflow during a busy shift.
How to Answer
- 1
Share a specific instance that highlights effective communication.
- 2
Describe the tools or methods used for communication, like verbal updates or checklists.
- 3
Explain the impact your communication had on team efficiency.
- 4
Mention any feedback you received from your team after the shift.
- 5
Keep the focus on teamwork and collaboration.
Example Answers
During a particularly busy shift, I organized a quick huddle at the start to discuss our priorities. We used a shared checklist to keep track of tasks, which helped everyone stay focused. I also checked in every hour to ensure we were on track, and everyone felt comfortable voicing concerns. As a result, we completed all orders on time and received positive feedback from our supervisor.
Tell me about a time you had to manage multiple tasks on the production line. How did you prioritize?
How to Answer
- 1
Identify a specific situation where you faced multiple tasks.
- 2
Explain how you assessed the urgency and importance of each task.
- 3
Discuss the method you used to prioritize (e.g., checklist, verbal communication).
- 4
Share the outcome of your actions and any improvements you made.
- 5
Conclude with what you learned from the experience.
Example Answers
In my last job, we had a sudden increase in orders and I was responsible for packing and labeling. I prioritized by checking which items were most time-sensitive and created a checklist. By delegating less critical tasks to colleagues, we met the deadline and improved our overall efficiency.
Describe a time when you took initiative to improve a process on the production line. What motivated you, and what was the result?
How to Answer
- 1
Think of a specific process you noticed could be improved.
- 2
Explain your reasoning and what motivated you to make the change.
- 3
Describe the actions you took to implement the improvement.
- 4
Share the measurable results or benefits that followed.
- 5
Keep it concise and focused on your role.
Example Answers
In my last job, I noticed that our packaging process was slowing down due to bottlenecks. I suggested rearranging the workstation layout to minimize movement. After implementing my idea, we reduced packaging time by 20%, allowing us to meet our production targets more consistently.
How do you cope with stress during peak production times? Can you provide a specific instance?
How to Answer
- 1
Stay organized and prioritize tasks to manage workload.
- 2
Communicate effectively with teammates to share responsibilities.
- 3
Take short breaks to recharge and maintain focus.
- 4
Use deep breathing techniques to stay calm under pressure.
- 5
Reflect on past experiences to identify successful coping strategies.
Example Answers
During peak production times, I make a detailed schedule to prioritize tasks. Last summer, we had an unexpected surge in orders. I organized daily morning briefs with my team to delegate tasks based on everyone’s strengths. This communication helped us meet deadlines without feeling overwhelmed.
What motivates you to maintain high productivity levels on the production line?
How to Answer
- 1
Identify personal goals related to the job
- 2
Emphasize teamwork and collaboration benefits
- 3
Mention commitment to quality and efficiency
- 4
Highlight pride in work and its impact
- 5
Share any rewards or recognition that motivate you
Example Answers
I stay motivated by setting personal performance goals and challenging myself to beat them every week.
Don't Just Read Production Line Worker Questions - Practice Answering Them!
Reading helps, but actual practice is what gets you hired. Our AI feedback system helps you improve your Production Line Worker interview answers in real-time.
Personalized feedback
Unlimited practice
Used by hundreds of successful candidates
Can you provide an example of a personal or team goal you set in your previous role? How did you achieve it?
How to Answer
- 1
Choose a specific goal related to production efficiency or teamwork.
- 2
Explain the steps you took to achieve the goal.
- 3
Include any tools or methods used to measure progress.
- 4
Mention the outcome or results of achieving the goal.
- 5
Highlight any teamwork or collaboration involved.
Example Answers
In my previous job, our team aimed to reduce production downtime by 20%. We analyzed our workflow and identified bottlenecks, then worked together to implement new scheduling techniques. By regularly tracking our progress, we managed to cut downtime by 25% within three months, significantly improving overall efficiency.
Technical Interview Questions
What types of machinery have you operated in previous production line roles, and what maintenance tasks were you responsible for?
How to Answer
- 1
List specific machinery types you have experience with.
- 2
Mention any relevant training or certifications for machinery operation.
- 3
Describe routine maintenance tasks you performed.
- 4
Highlight any safety protocols you adhered to.
- 5
Connect your experience to the job requirements.
Example Answers
I have operated automatic bottling machines and conveyor belts. My responsibilities included regular cleaning and lubricating the gears, as well as performing safety checks before shifts.
What safety protocols do you consider essential when working on a production line?
How to Answer
- 1
Identify specific safety equipment like gloves and goggles
- 2
Mention the importance of proper machine operation training
- 3
Highlight the need for regular safety audits and inspections
- 4
Emphasize the significance of clear communication among team members
- 5
Discuss adherence to emergency procedures and protocols
Example Answers
I believe using essential safety gear like gloves and goggles is critical, along with understanding how to operate machines safely. Regular training sessions ensure everyone knows the protocols.
Don't Just Read Production Line Worker Questions - Practice Answering Them!
Reading helps, but actual practice is what gets you hired. Our AI feedback system helps you improve your Production Line Worker interview answers in real-time.
Personalized feedback
Unlimited practice
Used by hundreds of successful candidates
How do you ensure that your work meets the quality standards expected in a manufacturing environment?
How to Answer
- 1
Understand the specific quality standards and guidelines for your role
- 2
Perform regular checks on your work and processes to catch issues early
- 3
Communicate with your team about quality expectations and any concerns
- 4
Use tools and equipment correctly to maintain quality output
- 5
Stay organized and follow protocols to reduce errors and ensure consistency
Example Answers
I make sure to familiarize myself with the specific quality standards for my position and conduct regular checks on my work to catch any defects early.
Can you explain a process improvement technique you have used in your previous work? What was the outcome?
How to Answer
- 1
Identify a specific process you improved.
- 2
Describe the technique or method clearly.
- 3
Mention your role in implementing the change.
- 4
Quantify the results or improvements if possible.
- 5
Share what you learned from the experience.
Example Answers
In my previous role, I improved the assembly line by implementing a 5S technique. I organized the workspace, reducing search time for tools by 30%. This led to increased efficiency and a safer working environment.
How do you diagnose issues when production machinery malfunctions?
How to Answer
- 1
Start by observing the machine for unusual sounds or movements.
- 2
Check error codes or indicators on the display panel.
- 3
Inspect the machinery for obvious signs of damage or wear.
- 4
Follow the standard troubleshooting checklist for the specific machine.
- 5
Consult with team members if the issue is complex or requires additional expertise.
Example Answers
I begin by listening for any unusual noises and looking for any alerts on the display. Then, I inspect for visible damage before referencing the troubleshooting checklist to pinpoint the issue.
What experience do you have with lean manufacturing principles and practices?
How to Answer
- 1
Mention specific lean practices you are familiar with like 5S or Kaizen.
- 2
Provide an example of a time you applied lean principles in a previous role.
- 3
Highlight any improvements you contributed to using lean methods.
- 4
Discuss teamwork and how collaboration enhanced lean initiatives.
- 5
Show your willingness to continue learning about lean practices.
Example Answers
I have experience with 5S from my previous job where I led an initiative to organize our workspace. This improved efficiency by reducing time searching for tools.
What key performance indicators (KPIs) do you think are most important for a production line worker?
How to Answer
- 1
Identify KPIs like production efficiency and quality control.
- 2
Mention accuracy in assembling or packaging products.
- 3
Discuss the importance of meeting safety standards.
- 4
Highlight the need for minimizing downtime.
- 5
Emphasize teamwork and communication as a vital KPI.
Example Answers
I believe key KPIs include production efficiency, ensuring we meet targets with minimal waste. Quality control is also critical to maintain high standards in our output.
What techniques do you use for efficient material handling on the production line?
How to Answer
- 1
Emphasize organization to reduce waste and downtime
- 2
Mention using standardized containers for easy transport
- 3
Discuss training team members on proper lifting techniques
- 4
Highlight the importance of regular equipment maintenance
- 5
Explain the role of clear communication in coordinating tasks
Example Answers
I focus on keeping the workspace organized, which minimizes material waste and downtime. Using standardized containers helps us transport materials quickly and efficiently.
What types of documentation and reporting have you been responsible for in previous jobs?
How to Answer
- 1
Identify specific types of reports you've created, like production logs or quality checks.
- 2
Mention any software or systems used for documentation, such as Excel or ERP systems.
- 3
Emphasize accuracy and attention to detail in your reporting.
- 4
Discuss how your documentation contributed to efficiency or problem-solving.
- 5
Share examples of teamwork, explaining how you collaborated on documentation.
Example Answers
In my last job, I maintained daily production logs using Excel, documenting output and defects to improve our quality control.
What production technologies are you familiar with, and how do they benefit efficiency?
How to Answer
- 1
Identify specific technologies you have worked with
- 2
Explain how each technology improves production processes
- 3
Use examples of past experiences to illustrate your point
- 4
Highlight any measurable results, like reduced downtime or increased output
- 5
Stay confident and articulate your understanding clearly
Example Answers
I am familiar with automated assembly lines, which reduce manual labor and speed up production. For instance, in my previous job, we implemented a robotic arm that increased our output by 30%.
Don't Just Read Production Line Worker Questions - Practice Answering Them!
Reading helps, but actual practice is what gets you hired. Our AI feedback system helps you improve your Production Line Worker interview answers in real-time.
Personalized feedback
Unlimited practice
Used by hundreds of successful candidates
Situational Interview Questions
What would you do if you and another team member disagreed on how to approach a task on the production line?
How to Answer
- 1
Acknowledge the disagreement calmly without escalating tensions
- 2
Listen actively to your team member's perspective to understand their reasoning
- 3
Share your own viewpoint clearly and provide rationale for your approach
- 4
Suggest finding a compromise or a way to test both methods if possible
- 5
Involve a supervisor if a consensus cannot be reached to ensure production continues smoothly
Example Answers
If a disagreement occurs, I would first listen to my colleague’s viewpoint to understand their reasoning. Then, I would share my perspective and suggest a trial of both methods to see which works better.
Imagine you are behind schedule on your production targets. How would you address this situation to catch up?
How to Answer
- 1
Assess the current production line to identify bottlenecks.
- 2
Prioritize tasks that have the highest impact on output.
- 3
Communicate with the team to rally support and encourage efficiency.
- 4
Consider temporary overtime or extra shifts to boost production.
- 5
Monitor progress consistently and adjust plans as needed.
Example Answers
I would first analyze the production line to pinpoint any bottlenecks and address them. Then, I'd collaborate with my team to prioritize critical tasks and ensure everyone is on the same page. If needed, I'd propose additional shifts to meet targets.
Don't Just Read Production Line Worker Questions - Practice Answering Them!
Reading helps, but actual practice is what gets you hired. Our AI feedback system helps you improve your Production Line Worker interview answers in real-time.
Personalized feedback
Unlimited practice
Used by hundreds of successful candidates
If you notice that a colleague is not adhering to safety protocols, what steps would you take?
How to Answer
- 1
Observe the situation discreetly to confirm the safety breach
- 2
Approach the colleague calmly and discuss your concerns
- 3
Encourage them to follow the safety protocols for their own safety and others'
- 4
If the behavior continues, report it to a supervisor or safety officer
- 5
Document the incident for reference if needed
Example Answers
I would first observe the situation to ensure it's a safety issue. Then, I would talk to my colleague privately, explaining why the safety protocol is important. If they don't change their behavior, I would inform a supervisor to address the issue.
Picture a scenario where the production process changes unexpectedly. How would you adapt to maintain productivity?
How to Answer
- 1
Stay calm and assess the situation quickly.
- 2
Communicate with your team immediately about the changes.
- 3
Identify the main issue and brainstorm solutions together.
- 4
Be flexible and willing to adjust your tasks as needed.
- 5
Focus on maintaining quality while adapting to the new process.
Example Answers
If the production process changes unexpectedly, I would first take a moment to assess the change. Then, I would gather my team to discuss how it affects our workflow and gather input on potential solutions. I would adapt by taking on different tasks if necessary and ensuring that we maintain our quality standards throughout the change.
If you were assigned to a new team that you have never worked with before, how would you build rapport with them?
How to Answer
- 1
Introduce yourself with a friendly attitude to create a welcoming environment
- 2
Listen actively to team members to understand their perspectives and demonstrate respect
- 3
Ask questions about their roles and experiences to show interest in their contributions
- 4
Share your own experiences related to the job to find common ground
- 5
Participate in team activities or initiatives to foster connections
Example Answers
I would start by introducing myself and sharing a bit about my background. I would make sure to listen carefully to my teammates' input and ask them about their roles, showing that I value their experience.
If your team was struggling with communication, what strategies would you implement to improve it?
How to Answer
- 1
Encourage open discussions to identify communication barriers
- 2
Implement regular team check-ins or huddles for updates
- 3
Use clear and simple language to avoid misunderstandings
- 4
Utilize visual aids or written instructions for clarity
- 5
Create a feedback loop where team members can express concerns
Example Answers
I would start by holding an open discussion to find out what issues we are facing. Then, I’d introduce regular team huddles to ensure everyone is on the same page. Additionally, I would use visual aids to support our communication.
How would you handle a sudden increase in production demand with limited resources?
How to Answer
- 1
Prioritize tasks based on demand urgency and resource availability
- 2
Communicate clearly with the team about expectations and adjustments
- 3
Identify and implement processes to improve efficiency
- 4
Consider temporary reallocations of staff from other areas if possible
- 5
Seek feedback and monitor progress to make necessary adjustments
Example Answers
In the face of increased demand, I would first assess which products need to be prioritized. I’d keep communication open with my team to set clear goals and expectations. Then, I would look for ways to streamline our processes to maximize output with the resources we have.
What actions would you take if a critical piece of machinery breaks down during a shift?
How to Answer
- 1
Immediately report the breakdown to your supervisor.
- 2
Identify and secure the area to ensure safety.
- 3
Check for any obvious issues that may be fixable.
- 4
Assist maintenance personnel with whatever support they need.
- 5
Document the breakdown and any actions taken for future reference.
Example Answers
If a machine breaks down, I would first inform my supervisor right away. Then, I would ensure the area is safe and clear. After that, I’d look for any obvious problems that might be quickly fixable while waiting for maintenance.
How would you approach a situation where you have a heavy workload and tight deadlines?
How to Answer
- 1
Prioritize tasks based on urgency and importance
- 2
Break down large tasks into smaller, manageable steps
- 3
Communicate with your team about workload challenges
- 4
Stay organized with tools like to-do lists or digital planners
- 5
Maintain a positive attitude to keep yourself motivated
Example Answers
I would start by prioritizing my tasks, focusing on the most urgent ones first. Then, I would break each task into smaller steps to make it easier to manage. Communication with my team would be key, so we can support each other and possibly redistribute some workload if needed.
If you observed a colleague intentionally bypassing a safety check, what would you do?
How to Answer
- 1
Stay calm and assess the situation before reacting
- 2
Prioritize safety and consider possible consequences
- 3
Address the colleague privately if you feel safe doing so
- 4
Report the behavior to a supervisor or safety officer if necessary
- 5
Follow up to ensure the issue is addressed
Example Answers
I would first assess the situation to ensure everyone is safe. If I felt comfortable, I might speak to my colleague privately about the importance of safety checks. If the behavior continued, I would report it to a supervisor to ensure it is addressed properly.
Don't Just Read Production Line Worker Questions - Practice Answering Them!
Reading helps, but actual practice is what gets you hired. Our AI feedback system helps you improve your Production Line Worker interview answers in real-time.
Personalized feedback
Unlimited practice
Used by hundreds of successful candidates
Production Line Worker Position Details
Recommended Job Boards
CareerBuilder
www.careerbuilder.com/jobs/production-line-workerZipRecruiter
www.ziprecruiter.com/Jobs/Production-Line-WorkerThese job boards are ranked by relevance for this position.
Related Positions
- Production Worker
- Production Line Assembler
- Line Leader
- Production Leader
- Line Operator
- Mechanical Assembler
- Box Worker
- Production Assembler
- Truck Assembler
- Furniture Assembler
Similar positions you might be interested in.
Ace Your Next Interview!
Practice with AI feedback & get hired faster
Personalized feedback
Used by hundreds of successful candidates
Ace Your Next Interview!
Practice with AI feedback & get hired faster
Personalized feedback
Used by hundreds of successful candidates