Top 32 Production Leader Interview Questions and Answers [Updated 2025]
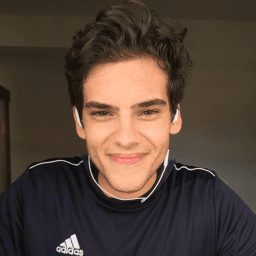
Andre Mendes
•
March 30, 2025
Navigating the competitive landscape of the 'Production Leader' role requires thorough preparation, and our updated blog post is here to help. Dive into the most common interview questions tailored for aspiring production leaders, complete with example answers and expert tips to help you respond effectively. Equip yourself with the insights needed to stand out and secure your next leadership position in production management.
Download Production Leader Interview Questions in PDF
To make your preparation even more convenient, we've compiled all these top Production Leaderinterview questions and answers into a handy PDF.
Click the button below to download the PDF and have easy access to these essential questions anytime, anywhere:
List of Production Leader Interview Questions
Behavioral Interview Questions
Can you describe a time when you had to lead a team through a significant production challenge? What was your approach?
How to Answer
- 1
Identify a specific production challenge you faced.
- 2
Explain your role and the team's dynamics during this challenge.
- 3
Detail the action steps you took to address the issue.
- 4
Highlight the outcomes and how they benefited the team or organization.
- 5
Reflect on what you learned from the experience.
Example Answers
In my previous role, we faced a major delay in production due to equipment failure. I coordinated a cross-functional team to diagnose the issue and implement temporary fixes, while also communicating transparently with upper management. We managed to catch up by reallocating resources effectively and finished the production run on time, which taught me the importance of adaptability in crisis management.
Tell me about a conflict you had with a team member. How did you handle it?
How to Answer
- 1
Describe the context and nature of the conflict succinctly
- 2
Focus on your role and actions taken to resolve the issue
- 3
Emphasize communication and understanding differing perspectives
- 4
Highlight the positive outcome or lesson learned
- 5
Be concise and avoid blaming the other person
Example Answers
In a project meeting, a team member and I disagreed on the timeline for deliverables. I approached him privately to discuss our views and realized he had valid concerns. We revised the timeline collaboratively, enhancing our project's efficiency. This conflict improved our teamwork and communication moving forward.
Don't Just Read Production Leader Questions - Practice Answering Them!
Reading helps, but actual practice is what gets you hired. Our AI feedback system helps you improve your Production Leader interview answers in real-time.
Personalized feedback
Unlimited practice
Used by hundreds of successful candidates
Give an example of a successful team project you led. What role did you play in its success?
How to Answer
- 1
Choose a specific project and outline its goals.
- 2
Describe your leadership role and responsibilities clearly.
- 3
Highlight a challenge you faced and how you overcame it.
- 4
Mention measurable outcomes or results achieved.
- 5
Wrap up with what you learned from the experience.
Example Answers
I led a team project to reduce production downtime. My role was to coordinate between departments and ensure communication. We identified key issues causing delays and implemented a new scheduling system. This led to a 20% reduction in downtime, greatly improving efficiency. I learned the importance of cross-departmental collaboration.
Describe a time when you introduced a process improvement in production. What impact did it have?
How to Answer
- 1
Identify a specific process you improved
- 2
Explain the challenge the process faced
- 3
Describe the steps you took to implement the improvement
- 4
Quantify the results or benefits where possible
- 5
Highlight any team involvement and feedback
Example Answers
In my previous role, we faced excessive downtime due to equipment failures. I introduced a preventive maintenance schedule, which reduced downtime by 30%. This also boosted team morale as everyone felt more reliable in their roles.
How have you motivated your team during a particularly challenging production period?
How to Answer
- 1
Share a specific challenge and its impact on the team
- 2
Highlight communication strategies you used to keep morale high
- 3
Emphasize teamwork and collaboration initiatives you promoted
- 4
Discuss recognition and rewards to boost motivation
- 5
Mention how you adapted to feedback from team members
Example Answers
During a peak season, my team faced severe equipment failures. I held daily briefings to update everyone and encourage open dialogue about issues. We worked in small groups to tackle problems together, and I recognized outstanding contributions with small rewards.
Can you give an example of a time when you prioritized safety in a production environment? What measures did you implement?
How to Answer
- 1
Choose a specific incident that highlights your commitment to safety.
- 2
Describe the situation clearly, focusing on the safety concern.
- 3
Explain the steps you took to address the safety issue.
- 4
Highlight the results and improvements achieved.
- 5
Emphasize teamwork and communication during the process.
Example Answers
In my previous role, I noticed that the loading area had insufficient signage for safety. I implemented bright, visible signs indicating hazards and safe practices. As a result, we saw a 40% decrease in near-miss incidents over the next quarter.
Describe a situation where you had to adapt quickly to changes in production demand. How did you manage it?
How to Answer
- 1
Identify a specific instance where demand changed unexpectedly.
- 2
Explain the steps you took to assess the situation.
- 3
Describe how you communicated changes to your team.
- 4
Highlight any new strategies or processes you implemented.
- 5
Share the results and any lessons learned.
Example Answers
In my last role, we experienced a sudden 30% increase in demand due to a promotional event. I quickly analyzed production schedules and shifted resources to the most affected lines. I communicated the changes to my team in a brief meeting and delegated tasks to ensure everyone was clear on their roles. We adjusted our processes to double our output for that week and ended up meeting customer demand without compromising quality.
Describe a situation where you had to be resourceful to meet production goals.
How to Answer
- 1
Choose a specific example that highlights your resourcefulness.
- 2
Mention the challenges faced that required innovative solutions.
- 3
Explain the actions you took and why you chose them.
- 4
Quantify the outcomes, if possible, to demonstrate impact.
- 5
Highlight any teamwork or collaboration involved in the solution.
Example Answers
At my previous job, we faced a sudden shortage of materials that could have delayed our production. I quickly sourced alternative suppliers and negotiated expedited shipping, which allowed us to meet our deadline without compromising quality. This effort saved us a week in production time.
Don't Just Read Production Leader Questions - Practice Answering Them!
Reading helps, but actual practice is what gets you hired. Our AI feedback system helps you improve your Production Leader interview answers in real-time.
Personalized feedback
Unlimited practice
Used by hundreds of successful candidates
Can you provide an example of how you implemented feedback from your team to improve production processes?
How to Answer
- 1
Choose a specific feedback instance from the team.
- 2
Explain the production process that was impacted.
- 3
Describe the action you took based on the feedback.
- 4
Highlight measurable outcomes or improvements.
- 5
Reflect on the value of team input in decision-making.
Example Answers
In a recent project, my team suggested refining our scheduling system. We switched to a digital tool based on their feedback, which reduced downtime by 20%. This change not only improved our efficiency but also boosted team morale as they felt heard.
Technical Interview Questions
What key performance indicators (KPIs) do you use to measure production efficiency?
How to Answer
- 1
Identify specific KPIs relevant to your industry, like OEE or throughput.
- 2
Explain how you track and analyze these KPIs over time.
- 3
Discuss how KPIs guide your decision-making and process improvements.
- 4
Mention any tools or software you use for KPI tracking.
- 5
Share a brief example of a KPI you improved and the impact it had.
Example Answers
I focus on Overall Equipment Effectiveness (OEE) and cycle time. I track these KPIs weekly using our production software, which helps me identify bottlenecks. For instance, I improved our OEE by 15% last quarter by addressing downtime issues.
Could you explain the principles of Lean Manufacturing and how you have applied them in your previous roles?
How to Answer
- 1
Define Lean Manufacturing clearly and concisely
- 2
Mention specific principles like Value Stream Mapping, 5S, or Just-In-Time
- 3
Provide a brief example from your experience to illustrate each principle
- 4
Focus on results achieved through Lean practices
- 5
Conclude with how these principles can benefit the prospective role
Example Answers
Lean Manufacturing is about maximizing value by minimizing waste. In my last role, we implemented 5S to organize our workspace, which increased productivity by 20%. Additionally, we used Value Stream Mapping to identify bottlenecks, resulting in a 30% reduction in lead times.
Don't Just Read Production Leader Questions - Practice Answering Them!
Reading helps, but actual practice is what gets you hired. Our AI feedback system helps you improve your Production Leader interview answers in real-time.
Personalized feedback
Unlimited practice
Used by hundreds of successful candidates
What strategies do you implement to ensure proper maintenance of production equipment?
How to Answer
- 1
Establish a routine preventive maintenance schedule to inspect and service equipment regularly
- 2
Train team members on best practices for equipment use and maintenance
- 3
Utilize technology for monitoring equipment performance and predicting maintenance needs
- 4
Create a system for logging maintenance activities and equipment issues
- 5
Engage suppliers and manufacturers for support and updates on equipment care
Example Answers
I implement a strict preventive maintenance schedule that includes regular inspections and servicing to catch issues early. Additionally, I ensure my team is trained on maintenance practices to enhance their understanding of equipment care.
How do you establish and maintain quality control standards in production?
How to Answer
- 1
Define clear quality standards and expectations from the beginning.
- 2
Implement regular training programs for the production team on quality protocols.
- 3
Utilize data analysis to track quality performance and identify areas for improvement.
- 4
Incorporate feedback mechanisms for both staff and customers to enhance quality.
- 5
Conduct periodic audits to ensure compliance with the established quality standards.
Example Answers
I establish quality control standards by defining clear expectations and providing regular training to the team. Data analysis helps us track our performance, while feedback mechanisms allow us to keep improving.
What experience do you have in managing production budgets and controlling costs?
How to Answer
- 1
Highlight specific examples of budget management in previous roles
- 2
Discuss any cost-saving initiatives you implemented
- 3
Emphasize collaboration with finance or other departments
- 4
Mention tools or software used for budget tracking
- 5
Share measurable outcomes from your cost control efforts
Example Answers
In my previous role, I managed a production budget of $2 million and consistently came in under budget by 10% through careful planning and negotiating with suppliers.
What tools or software have you used for production planning and scheduling?
How to Answer
- 1
Identify specific software you are familiar with like SAP, Oracle, or Microsoft Project.
- 2
Mention any experience with data analysis tools such as Excel for forecasting.
- 3
Highlight any custom-built systems or unique tools your previous employers used.
- 4
Discuss how you used these tools to solve production challenges.
- 5
Share examples of successful projects or outcomes achieved with these tools.
Example Answers
In my previous role, I used SAP for production planning to optimize resource allocation and schedule workflows effectively, resulting in a 15% increase in on-time delivery.
How do you coordinate with the supply chain team to ensure uninterrupted production?
How to Answer
- 1
Establish regular communication with the supply chain team to discuss inventory levels and material availability
- 2
Use data analytics to forecast production needs and align with supply chain schedules
- 3
Implement a system for early warning alerts on supply disruptions or delays
- 4
Collaborate on contingency plans for critical materials to avoid production halts
- 5
Participate in cross-functional meetings to share updates and address potential bottlenecks
Example Answers
I coordinate by holding weekly meetings with the supply chain team to review inventory and forecast needs. This ensures we are aligned on what is available and what’s required for uninterrupted production.
What experience do you have with regulatory compliance in a production environment?
How to Answer
- 1
Identify specific regulations relevant to your industry.
- 2
Share examples of how you implemented compliance protocols.
- 3
Discuss any training you've conducted related to compliance.
- 4
Mention how you monitor compliance and address violations.
- 5
Highlight successful outcomes from maintaining compliance.
Example Answers
In my previous role, I ensured compliance with OSHA regulations by conducting quarterly safety audits and training sessions, resulting in a 20% reduction in workplace incidents.
How do you stay informed about technological advancements that could impact production processes?
How to Answer
- 1
Follow industry publications and blogs related to manufacturing technology
- 2
Attend trade shows and conferences to see new innovations in action
- 3
Network with industry professionals to share insights on recent trends
- 4
Participate in online forums and discussion groups focused on production technology
- 5
Utilize online courses and webinars to further your knowledge of emerging tools
Example Answers
I regularly read industry publications like Manufacturing Weekly and follow relevant blogs to keep up with new technologies. Additionally, I attend annual trade shows where I can see innovations firsthand and network with other professionals.
What techniques do you use for effective inventory management in production?
How to Answer
- 1
Utilize inventory tracking software for real-time visibility
- 2
Implement Just-In-Time (JIT) practices to reduce excess stock
- 3
Conduct regular audits and cycle counts to maintain accuracy
- 4
Employ demand forecasting to align inventory with production needs
- 5
Establish strong supplier relationships to improve lead times and flexibility
Example Answers
I use inventory tracking software to gain real-time visibility and ensure we always have the right amount of stock on hand. This helps us avoid both shortages and overages.
Don't Just Read Production Leader Questions - Practice Answering Them!
Reading helps, but actual practice is what gets you hired. Our AI feedback system helps you improve your Production Leader interview answers in real-time.
Personalized feedback
Unlimited practice
Used by hundreds of successful candidates
What is your experience with automation in production and how has it changed your approach?
How to Answer
- 1
Describe specific automation tools or technologies you have used.
- 2
Explain the direct impact of automation on production efficiency.
- 3
Discuss how automation has influenced team dynamics and communication.
- 4
Share an example of a successful automation project and its outcomes.
- 5
Highlight any challenges faced with automation and how you overcame them.
Example Answers
In my previous role, I implemented a robotic process automation system that reduced packaging time by 30%. This experience taught me how to leverage technology for efficiency and improved team collaboration.
Situational Interview Questions
If you discovered a significant flaw in a production batch just before shipping, what steps would you take?
How to Answer
- 1
Immediately halt the shipping process to prevent flawed products from reaching customers.
- 2
Notify your supervisor and relevant stakeholders about the issue and its potential impact.
- 3
Conduct a quick assessment to identify the cause of the flaw and the extent of the affected batch.
- 4
Implement corrective actions to fix the flaw, or isolate the affected products for further evaluation.
- 5
Document the incident and review processes to prevent future occurrences.
Example Answers
I would immediately stop the shipping process and inform my supervisor about the significant flaw. Next, I would assess the batch to identify the cause and figure out how many units are affected. After that, I'd take corrective actions and isolate the flawed products while documenting everything to improve our processes.
Imagine two team members are consistently clashing over production responsibilities. How would you resolve this?
How to Answer
- 1
Listen to both team members to understand their perspectives
- 2
Facilitate a meeting to encourage open communication
- 3
Identify common goals and redefine responsibilities collaboratively
- 4
Establish a follow-up plan to monitor progress and address any further issues
- 5
Encourage a culture of respect and teamwork within the team
Example Answers
I would start by meeting individually with each team member to hear their concerns. Then, I would facilitate a joint meeting where they can discuss their viewpoints openly, helping them to focus on our common production goals. Together, we could redefine their responsibilities to ensure clarity, followed by regular check-ins to prevent future misunderstandings.
Don't Just Read Production Leader Questions - Practice Answering Them!
Reading helps, but actual practice is what gets you hired. Our AI feedback system helps you improve your Production Leader interview answers in real-time.
Personalized feedback
Unlimited practice
Used by hundreds of successful candidates
What would you do if a critical machine breaks down in the middle of a production run?
How to Answer
- 1
Assess the situation quickly and ensure safety first
- 2
Communicate immediately with the team about the breakdown
- 3
Implement emergency protocols or switch to a backup machine if available
- 4
Identify the root cause of the breakdown and document it for analysis
- 5
Establish a plan for resuming production as soon as possible
Example Answers
First, I would ensure everyone's safety and assess the situation. Then I would inform the team and check if we have a backup machine to continue production. I would also start troubleshooting the issue while documenting the breakdown.
If you had a team member who consistently underperformed, how would you address this issue?
How to Answer
- 1
Identify specific performance issues with clear examples
- 2
Initiate a private, constructive conversation with the team member
- 3
Listen to their perspective to understand any underlying issues
- 4
Set clear expectations and create an improvement plan
- 5
Follow up regularly to track progress and provide support
Example Answers
I would first review their performance metrics to pinpoint specific areas of underachievement. Then, I would have a private discussion to understand any challenges they might be facing. From there, I'd set clear expectations and develop an improvement plan together, ensuring we have regular check-ins to review progress.
How would you adjust production priorities if there was a sudden surge in customer demand?
How to Answer
- 1
Assess current production capacity and limitations immediately
- 2
Communicate with the team and stakeholders to gather insights
- 3
Prioritize key products that align with customer demand
- 4
Implement flexible scheduling or overtime to boost capacity
- 5
Monitor supply chain and resource availability to avoid bottlenecks
Example Answers
I would first evaluate our current production capabilities and identify any constraints. Then, I would discuss with my team and stakeholders to understand the situation better. Based on customer demand, I would prioritize the most critical products and consider flexible scheduling or overtime to increase output. I would also keep a close eye on our supply chain to ensure we can meet these demands efficiently.
You need to onboard new team members quickly. What training strategies would you implement?
How to Answer
- 1
Create a structured onboarding checklist for new hires.
- 2
Utilize mentorship programs pairing new hires with experienced team members.
- 3
Implement a mix of online training modules and hands-on practice.
- 4
Schedule regular feedback sessions during the onboarding process.
- 5
Encourage team-building activities to foster relationships early.
Example Answers
I would develop a detailed onboarding checklist to ensure all essential training is covered. Pairing new hires with experienced mentors would offer them guidance and support. Additionally, I would use a mix of online training and practical work to reinforce learning.
How would you handle a situation where resources are limited, but production needs are high?
How to Answer
- 1
Assess the current situation to identify critical needs and constraints
- 2
Prioritize tasks based on production impact and urgency
- 3
Engage and communicate with your team for ideas and support
- 4
Explore options for optimizing existing resources and processes
- 5
Consider temporary adjustments like overtime or cross-training staff
Example Answers
In a high-demand situation with limited resources, I would first prioritize production tasks based on their urgency. Then, I'd work closely with my team to brainstorm ways to optimize our workflow. For example, we could implement lean practices to reduce waste and increase efficiency.
If you notice team morale is low, what actions would you take to improve it?
How to Answer
- 1
Organize a team feedback session to understand concerns
- 2
Implement small team-building activities to foster camaraderie
- 3
Recognize individual contributions publicly to boost confidence
- 4
Ensure open communication channels for ongoing support
- 5
Set clear, achievable goals to give the team a sense of purpose
Example Answers
I would start by organizing a feedback session to hear the team’s concerns, followed by team-building activities to strengthen relationships.
How would you respond to negative feedback about production efficiency from upper management?
How to Answer
- 1
Acknowledge the feedback and express appreciation for the input
- 2
Assess the validity of the feedback by examining production data
- 3
Identify specific areas for improvement and develop action plans
- 4
Communicate openly with the team about the feedback and engage them in problem-solving
- 5
Provide regular updates to management on progress and adjustments made
Example Answers
I appreciate the feedback and will review our production metrics to identify inefficiencies. I'll collaborate with my team to create a targeted action plan and ensure we address these concerns effectively.
How would you foster a positive workplace culture in your production team?
How to Answer
- 1
Establish open communication channels for feedback and ideas.
- 2
Recognize and celebrate team achievements regularly.
- 3
Encourage team bonding through social activities or team-building exercises.
- 4
Promote a safe and inclusive environment where everyone feels valued.
- 5
Provide opportunities for professional development and skill enhancement.
Example Answers
I would create open communication channels where team members feel comfortable sharing ideas. Regular recognition of achievements would help boost morale, and I would organize team-building activities to strengthen relationships.
Don't Just Read Production Leader Questions - Practice Answering Them!
Reading helps, but actual practice is what gets you hired. Our AI feedback system helps you improve your Production Leader interview answers in real-time.
Personalized feedback
Unlimited practice
Used by hundreds of successful candidates
Production Leader Position Details
Recommended Job Boards
CareerBuilder
www.careerbuilder.com/jobs/production-leaderZipRecruiter
www.ziprecruiter.com/Jobs/Production-Leader/These job boards are ranked by relevance for this position.
Related Positions
- Line Leader
- Production Worker
- Production Line Worker
- Production Line Assembler
- Production Assembler
- Body Maker
- Harnessmaker
- Line Operator
- Sign Maker
- End Maker
Similar positions you might be interested in.
Ace Your Next Interview!
Practice with AI feedback & get hired faster
Personalized feedback
Used by hundreds of successful candidates
Ace Your Next Interview!
Practice with AI feedback & get hired faster
Personalized feedback
Used by hundreds of successful candidates