Top 30 Line Runner Interview Questions and Answers [Updated 2025]
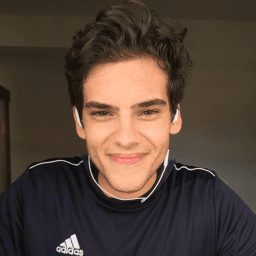
Andre Mendes
•
March 30, 2025
Navigating the competitive landscape of the Line Runner role can be daunting, but preparation is key. In this updated blog post, we delve into the most common interview questions to help you stand out. Discover insightful example answers and effective tips to confidently tackle each question, ensuring you're ready to impress and secure the position. Get ready to elevate your interview game!
Download Line Runner Interview Questions in PDF
To make your preparation even more convenient, we've compiled all these top Line Runnerinterview questions and answers into a handy PDF.
Click the button below to download the PDF and have easy access to these essential questions anytime, anywhere:
List of Line Runner Interview Questions
Behavioral Interview Questions
Tell me about a time when you had to work closely with a teammate to complete a task on the line.
How to Answer
- 1
Choose a specific example from your past experience.
- 2
Highlight your role and responsibilities in the teamwork.
- 3
Emphasize communication or problem-solving skills used.
- 4
Mention the outcome and what you learned from the experience.
- 5
Keep it concise and relevant to the line runner position.
Example Answers
In my previous job, I worked with a teammate to streamline the assembly process on the line. I communicated daily to ensure we were on track and identified a bottleneck which we resolved by rearranging our workflow. This collaboration led to a 20% increase in our output, and I learned the importance of adaptability in teamwork.
Describe a situation where you encountered a significant issue while running the line. How did you handle it?
How to Answer
- 1
Identify a specific issue you faced while running the line.
- 2
Explain the impact of the issue on operations or workflow.
- 3
Describe the steps you took to resolve the issue.
- 4
Highlight any teamwork or communication involved.
- 5
Conclude with the outcome and any lessons learned.
Example Answers
During a busy shift, I noticed a bottleneck in production due to a malfunctioning machine. I quickly assessed the situation and communicated with the maintenance team to fix the issue. Meanwhile, I redirected my team to focus on other tasks to minimize downtime. The machine was repaired within 30 minutes, and we met our production goals that day.
Don't Just Read Line Runner Questions - Practice Answering Them!
Reading helps, but actual practice is what gets you hired. Our AI feedback system helps you improve your Line Runner interview answers in real-time.
Personalized feedback
Unlimited practice
Used by hundreds of successful candidates
Can you provide an example of when you had to quickly adapt to a change in process or equipment while running the line?
How to Answer
- 1
Choose a specific instance from your experience.
- 2
Explain the change that occurred clearly.
- 3
Describe your immediate reaction and actions taken.
- 4
Highlight the outcome and what you learned from it.
- 5
Keep it concise and focused on your adaptability.
Example Answers
During a production shift, the conveyor belt broke down. I quickly assessed the situation, informed my supervisor, and switched to a backup manual assembly process to keep the line moving, which minimized downtime.
Have you ever taken the lead during a challenging operation on the line? What was the outcome?
How to Answer
- 1
Describe a specific situation where you took the lead.
- 2
Highlight the challenges you faced during the operation.
- 3
Explain the actions you took to address the challenges.
- 4
Discuss the outcome and any positive impacts.
- 5
Conclude with what you learned from the experience.
Example Answers
In my previous role, we faced a sudden equipment failure. I took the lead by quickly coordinating with the maintenance team and reallocating tasks among my colleagues. As a result, we minimized downtime and completed our production targets for the day. From this experience, I learned the importance of swift communication and teamwork.
Explain a time when you had to communicate a complex issue to your team. How did you ensure they understood?
How to Answer
- 1
Identify the complex issue clearly
- 2
Use simple language and avoid jargon
- 3
Break down the issue into manageable parts
- 4
Encourage questions for clarity
- 5
Provide a summary to reinforce key points
Example Answers
In my last role, we had to implement a new software system that many team members found confusing. I organized a meeting where I explained the main features in simple terms, divided the system into sections, and used visuals to illustrate my points. I then opened the floor for questions and followed up with a document summarizing the key features for everyone to refer back to.
Can you give an example of when you took initiative to improve the line's performance?
How to Answer
- 1
Think of a specific situation where your actions had a direct impact.
- 2
Describe the issue or challenge the line was facing.
- 3
Explain what steps you took to address the issue.
- 4
Highlight the positive outcome or results from your initiative.
- 5
Use metrics or feedback if possible to demonstrate improvement.
Example Answers
In my previous role, I noticed that the line was experiencing frequent delays due to equipment malfunctions. I took the initiative to schedule regular maintenance checks, which reduced downtime by 30% over two months.
Describe a time when you helped train a new coworker. What did you focus on?
How to Answer
- 1
Choose a specific training experience.
- 2
Highlight key skills or processes you taught.
- 3
Emphasize how you adapted to the coworker's learning style.
- 4
Mention the outcome or improvement seen.
- 5
Keep it concise and focused on your impact.
Example Answers
I trained a new coworker on the packing line. I focused on showing them the proper techniques to handle fragile items and how to optimize packing speeds. I noticed they learned better with hands-on practice, so I let them pack alongside me for a few shifts. They quickly became efficient, and we reduced error rates by 20%.
Tell me about a time you faced repeated failures on the line. How did you maintain motivation?
How to Answer
- 1
Identify a specific challenge you faced on the line.
- 2
Explain the impact of the repeated failures on your work.
- 3
Share strategies you used to stay motivated, such as focusing on learning or teamwork.
- 4
Conclude with a positive outcome or lesson learned from the experience.
- 5
Keep your answer focused and concise, highlighting your resilience.
Example Answers
During a busy production month, we had several issues with equipment malfunctions that slowed down the line. I felt frustrated, but I kept my focus on improving my skills in troubleshooting. I also rallied my team for brainstorming sessions to support each other, which boosted our morale. In the end, we found solutions together and increased our efficiency by 20%.
Describe a time when a project you were working on did not go as planned. What did you learn?
How to Answer
- 1
Choose a specific project that faced challenges and was not successful.
- 2
Explain the situation and what went wrong clearly and concisely.
- 3
Focus on your role and contributions to the situation.
- 4
Highlight the lessons learned and how you applied them in future projects.
- 5
Keep a positive tone, showing that you can grow from setbacks.
Example Answers
In my last role, we were tasked to deliver a new product within three months. Halfway through, we realized that our market research was flawed, leading to a product that did not meet customer needs. I learned the importance of validating assumptions early and we adjusted our approach by conducting customer interviews, which I now implement in all projects.
Have you ever dealt with a production request from a customer that required a quick turnaround? How did you manage it?
How to Answer
- 1
Share a specific instance to demonstrate your experience.
- 2
Outline the steps you took to assess the request quickly.
- 3
Emphasize communication with the team and the customer.
- 4
Highlight any tools or processes you used to expedite production.
- 5
Conclude with the positive outcome and customer satisfaction.
Example Answers
At my previous job, we received a last-minute order for a large batch of custom parts. I quickly assessed the inventory, communicated with my team, and prioritized the work. We utilized our existing stock to speed up the process, and I kept the customer updated. We delivered the order ahead of schedule, and the customer was very pleased.
Don't Just Read Line Runner Questions - Practice Answering Them!
Reading helps, but actual practice is what gets you hired. Our AI feedback system helps you improve your Line Runner interview answers in real-time.
Personalized feedback
Unlimited practice
Used by hundreds of successful candidates
Technical Interview Questions
What types of machinery have you operated while running a production line?
How to Answer
- 1
List specific types of machinery you have experience with.
- 2
Mention the role of each machine in the production process.
- 3
Include any technical skills related to machinery operation.
- 4
Highlight your ability to troubleshoot and maintain the equipment.
- 5
Connect your experience with the requirements of the position.
Example Answers
I have operated automated conveyor belts, packaging machines, and labeling machines. My role included ensuring smooth operation and quick troubleshooting to minimize downtime.
How do you ensure quality control while running the line?
How to Answer
- 1
Regularly inspect products at different stages of the line
- 2
Maintain clear communication with team members about quality standards
- 3
Utilize checklists to verify equipment and process functionality
- 4
Document and address any quality issues immediately
- 5
Provide consistent training on quality control practices to the team
Example Answers
I ensure quality control by regularly inspecting products along the line and communicating any defects to my team instantly, so we can address issues before they escalate.
Don't Just Read Line Runner Questions - Practice Answering Them!
Reading helps, but actual practice is what gets you hired. Our AI feedback system helps you improve your Line Runner interview answers in real-time.
Personalized feedback
Unlimited practice
Used by hundreds of successful candidates
What methods have you implemented in the past to improve line efficiency?
How to Answer
- 1
Identify specific processes you streamlined or automated
- 2
Discuss any team training or skill enhancement you implemented
- 3
Mention tools or technology you employed to track efficiency
- 4
Share metrics or results from your improvements
- 5
Emphasize teamwork and communication efforts that supported changes
Example Answers
I implemented a digital tracking system that monitored line speed and efficiency metrics in real-time, which helped us identify bottlenecks and reduce downtime by 15%.
What safety protocols do you follow while operating machinery on the line?
How to Answer
- 1
Always wear appropriate personal protective equipment like gloves, goggles, and hearing protection.
- 2
Conduct a pre-operation inspection of the machinery to check for any defects or malfunctions.
- 3
Follow the standard operating procedures (SOPs) for the machinery you are using.
- 4
Stay aware of your surroundings and communicate with co-workers to avoid accidents.
- 5
Report any safety issues or near misses to your supervisor immediately.
Example Answers
I always wear my safety gear, do a pre-inspection of the machine, and follow agreed SOPs to ensure I operate safely on the line.
Describe your approach to diagnosing a malfunctioning piece of equipment on the line.
How to Answer
- 1
Start by observing the equipment and identifying any visible issues.
- 2
Listen for unusual sounds or vibrations during operation.
- 3
Check for error messages or indicator lights on the machine.
- 4
Consult the equipment manual for troubleshooting steps.
- 5
Test components systematically to isolate the problem.
Example Answers
I begin by visually inspecting the equipment and listening for any abnormal sounds. If I see any error lights or messages, I note those down. Then, I refer to the manual for guidance before testing individual components to pinpoint the malfunction.
What strategies do you use to manage load balancing in line production?
How to Answer
- 1
Assess the workload and identify bottlenecks regularly
- 2
Implement cross-training for team members to increase flexibility
- 3
Utilize real-time monitoring tools to track production flow
- 4
Adjust resource allocation based on demand and capacity
- 5
Encourage open communication among team members to address issues quickly
Example Answers
I regularly assess workload and identify bottlenecks by analyzing production data, allowing me to redistribute tasks effectively. For instance, if one station is overloaded, I can assign team members from less busy areas to help out.
How do you use data to assess line performance?
How to Answer
- 1
Identify key performance indicators (KPIs) relevant to line performance.
- 2
Collect data systematically, including production rates, downtime, and quality metrics.
- 3
Analyze trends over time to spot issues or opportunities for improvement.
- 4
Compare current performance against historical data to measure progress.
- 5
Use data visualization tools to communicate findings to the team.
Example Answers
I use KPIs like production rate and quality defects to assess line performance. I collect data daily and analyze trends to identify patterns that might indicate issues. By comparing this data against our targets, I can quickly spot when we need to address a problem.
What industry regulations do you need to comply with while operating the line?
How to Answer
- 1
Research specific regulations for the industry, like OSHA for safety standards.
- 2
Highlight the importance of compliance to ensure a safe working environment.
- 3
Mention any relevant certifications or training you have received.
- 4
Discuss how you stay updated on changing regulations.
- 5
Provide examples of how you have applied these regulations in past experiences.
Example Answers
In the manufacturing industry, we need to comply with OSHA regulations to ensure safety standards are met. I regularly review safety protocols and attend training to stay compliant.
Are you familiar with any production line management software? How have you used it?
How to Answer
- 1
Identify specific software you have used.
- 2
Briefly explain your role with the software.
- 3
Share outcomes or improvements made using the software.
- 4
Mention teamwork or collaboration if applicable.
- 5
Be honest if you haven't used specific software.
Example Answers
I have used ProductionPro for managing our assembly line. In my role, I monitored production metrics, which helped reduce downtime by 15%. I collaborated with team members to optimize workflows based on the data.
Can you explain your understanding of workflow processes on a production line?
How to Answer
- 1
Identify key components of a production line.
- 2
Explain the importance of each step in the workflow.
- 3
Discuss how efficiency can be measured.
- 4
Mention the role of communication among team members.
- 5
Include examples of common issues and solutions.
Example Answers
A production line consists of distinct steps: material handling, assembly, quality control, and packaging. Each step is crucial for ensuring that the product meets quality standards. Efficiency can be measured by tracking cycle time and output rates, and good communication helps to quickly address any issues that arise.
Don't Just Read Line Runner Questions - Practice Answering Them!
Reading helps, but actual practice is what gets you hired. Our AI feedback system helps you improve your Line Runner interview answers in real-time.
Personalized feedback
Unlimited practice
Used by hundreds of successful candidates
Situational Interview Questions
If two team members were arguing about a procedure, how would you handle the situation?
How to Answer
- 1
Stay calm and listen to both sides without interruption.
- 2
Acknowledge their feelings and the importance of the issue.
- 3
Encourage a collaborative discussion to find common ground.
- 4
Redirect the focus to the procedure and its purpose.
- 5
Offer to mediate a solution or consensus if needed.
Example Answers
I would first listen to both team members equally and understand their perspectives. Then, I would acknowledge their concerns and encourage them to discuss it together while guiding the conversation back to the procedure's goals.
Imagine the production line has stopped unexpectedly. What steps would you take to troubleshoot and resume operations?
How to Answer
- 1
Quickly assess the situation and identify any visible issues
- 2
Check the control panel for error messages or alerts
- 3
Communicate with team members to gather information
- 4
Try to reset machinery or equipment as needed
- 5
Document the incident and inform supervisors after resolving the issue
Example Answers
First, I would look for any obvious signs of trouble, like a jammed component. Then, I would check the control panel for any alerts. I'd talk to my teammates to see if anyone noticed anything unusual before the stop. If safe, I would reset the machine and see if that resolves the issue. Finally, I would document everything and let my supervisor know what happened.
Don't Just Read Line Runner Questions - Practice Answering Them!
Reading helps, but actual practice is what gets you hired. Our AI feedback system helps you improve your Line Runner interview answers in real-time.
Personalized feedback
Unlimited practice
Used by hundreds of successful candidates
If you have multiple tasks to complete on the line with tight deadlines, how would you prioritize your work?
How to Answer
- 1
List all tasks and their deadlines clearly.
- 2
Evaluate the impact of each task on the line's operation.
- 3
Communicate with the team for input on priorities.
- 4
Focus on high-impact tasks first to ensure smooth workflow.
- 5
Stay flexible and ready to adjust if priorities change.
Example Answers
I would start by listing all tasks and their deadlines. Then, I would assess which tasks are critical for the line's performance and tackle those first. I would keep my team informed and ask if they have insights on priorities to ensure we are aligned.
During peak hours, how would you handle stress while ensuring productivity on the line?
How to Answer
- 1
Stay organized by prioritizing tasks and creating a workflow.
- 2
Communicate effectively with team members to delegate responsibilities.
- 3
Take short breaks to clear your mind and regain focus.
- 4
Use stress management techniques like deep breathing or visualization.
- 5
Maintain a positive attitude to boost team morale and collective productivity.
Example Answers
I would prioritize the tasks on the line and communicate clearly with my team to delegate where necessary. Taking short breaks would also help me manage stress and stay focused.
How would you approach integrating a new team member into your team during a busy production shift?
How to Answer
- 1
Introduce the new member to the team quickly and warmly.
- 2
Assign a buddy from the team to help them learn their tasks.
- 3
Provide a brief overview of the workflow and priorities for the shift.
- 4
Encourage them to ask questions and offer them immediate feedback.
- 5
Check in with them frequently throughout the shift to ensure they're comfortable.
Example Answers
I would start by introducing the new member to the team, ensuring they feel welcomed. Then, I would assign a buddy to walk them through their tasks and answer any questions they have. I’d also provide a quick summary of our priorities for the shift to help them understand where to focus.
If there was an emergency situation on the line, what immediate actions would you take?
How to Answer
- 1
Stay calm and assess the situation quickly
- 2
Notify your supervisor immediately
- 3
Activate the emergency stop if necessary
- 4
Assist any injured personnel and call for medical help
- 5
Follow the company's emergency protocols
Example Answers
First, I would remain calm and quickly assess the emergency to understand its nature. Then, I would immediately notify my supervisor. If the situation requires, I would activate the emergency stop to prevent further issues and assist any injured team members while calling for medical assistance if necessary.
If you need assistance from other departments to solve a problem on the line, how would you approach that?
How to Answer
- 1
Identify the specific issue clearly before reaching out.
- 2
Determine which department can help and their key contacts.
- 3
Communicate the problem succinctly and explain its impact on production.
- 4
Be respectful of their time and ask for a specific type of assistance.
- 5
Follow up graciously and provide updates on the situation.
Example Answers
I would first identify the exact problem on the line, then reach out to the maintenance department since they handle equipment issues. I'd explain the downtime caused by the problem and ask for their expertise to fix it promptly.
If you notice inefficiencies in the current process, what steps would you take to modify the process?
How to Answer
- 1
Identify the specific inefficiencies and analyze their impact.
- 2
Gather input from team members about the process and their experiences.
- 3
Propose practical changes to address the inefficiencies.
- 4
Test the proposed changes on a small scale before full implementation.
- 5
Monitor the results and adjust as necessary based on feedback.
Example Answers
I would first pinpoint the inefficiencies by observing the process and collecting data. Then, I would discuss with my team to understand their perspectives and how the process affects them. Based on that, I would suggest specific changes, like adjusting the workflow to reduce bottlenecks, and test these changes with a small team.
How would you motivate your team during a particularly tough production schedule?
How to Answer
- 1
Communicate openly about the challenges and the importance of teamwork
- 2
Recognize individual and team efforts regularly
- 3
Set achievable milestones to create a sense of progress
- 4
Offer incentives or rewards for meeting tough goals
- 5
Encourage breaks and team-building activities to maintain morale
Example Answers
I would hold a meeting to discuss the production schedule and emphasize the crucial role each team member plays. Recognizing hard work and setting small milestones can help everyone stay motivated.
If you received negative feedback from a supervisor about your line management, how would you respond?
How to Answer
- 1
Acknowledge the feedback without being defensive
- 2
Ask for specific examples to understand the issue better
- 3
Express willingness to improve and seek solutions
- 4
Outline a plan for addressing the feedback
- 5
Follow up after implementation to show commitment to growth
Example Answers
I would first thank my supervisor for their feedback and reassure them that I take it seriously. I'd ask for specific examples of the issues they noticed. After that, I would create an action plan to address those concerns and ensure that I implement it, then check back in with them to discuss my progress.
Don't Just Read Line Runner Questions - Practice Answering Them!
Reading helps, but actual practice is what gets you hired. Our AI feedback system helps you improve your Line Runner interview answers in real-time.
Personalized feedback
Unlimited practice
Used by hundreds of successful candidates
Line Runner Position Details
Recommended Job Boards
CareerBuilder
www.careerbuilder.com/jobs/line-runnerZipRecruiter
www.ziprecruiter.com/Jobs/Line-RunnerThese job boards are ranked by relevance for this position.
Related Positions
- Line Operator
- Line Puller
- Line Inspector
- Line Locator
- Line Leader
- Linesman
- Car Runner
- Board Runner
- Runner Man
- Line Producer
Similar positions you might be interested in.
Ace Your Next Interview!
Practice with AI feedback & get hired faster
Personalized feedback
Used by hundreds of successful candidates
Ace Your Next Interview!
Practice with AI feedback & get hired faster
Personalized feedback
Used by hundreds of successful candidates