Top 29 Manufacturing Project Engineer Interview Questions and Answers [Updated 2025]
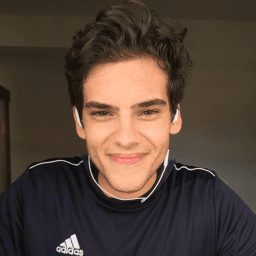
Andre Mendes
•
March 30, 2025
Preparing for a Manufacturing Project Engineer interview can be daunting, but having the right guidance can make all the difference. In this blog post, we delve into the most common interview questions encountered in this field, offering insightful example answers and practical tips to help you respond with confidence and clarity. Whether you're a seasoned professional or just starting, this guide will equip you with the tools to impress your interviewers and secure your desired position.
Download Manufacturing Project Engineer Interview Questions in PDF
To make your preparation even more convenient, we've compiled all these top Manufacturing Project Engineerinterview questions and answers into a handy PDF.
Click the button below to download the PDF and have easy access to these essential questions anytime, anywhere:
List of Manufacturing Project Engineer Interview Questions
Technical Interview Questions
What project management tools have you used to track manufacturing projects?
How to Answer
- 1
Identify specific project management tools you have experience with
- 2
Mention how you used these tools in manufacturing settings
- 3
Discuss the benefits these tools provided in tracking progress
- 4
Include examples of successful projects where these tools were used
- 5
Be prepared to explain any challenges faced and how you overcame them
Example Answers
I have used tools like Microsoft Project and Trello to track manufacturing projects. For instance, I used Microsoft Project to create Gantt charts for a new product line, which helped the team meet deadlines by visualizing tasks and dependencies.
What methods do you use to identify and implement process improvements in a manufacturing setting?
How to Answer
- 1
Conduct regular process audits to identify inefficiencies
- 2
Utilize data analysis to track performance metrics
- 3
Engage with team members for feedback on current processes
- 4
Apply the Plan-Do-Check-Act (PDCA) cycle for systematic improvement
- 5
Implement Lean and Six Sigma methodologies for waste reduction
Example Answers
I regularly conduct process audits and gather data on key performance metrics. For instance, in my last role, I noticed high defect rates in assembly. I gathered team feedback and applied Lean techniques to streamline the workflow, resulting in a 20% reduction in defects.
Don't Just Read Manufacturing Project Engineer Questions - Practice Answering Them!
Reading helps, but actual practice is what gets you hired. Our AI feedback system helps you improve your Manufacturing Project Engineer interview answers in real-time.
Personalized feedback
Unlimited practice
Used by hundreds of successful candidates
How have you used Lean Six Sigma principles to improve manufacturing efficiency?
How to Answer
- 1
Identify a specific project where Lean Six Sigma was applied.
- 2
Briefly describe the problem or inefficiency in the process.
- 3
Explain the Lean Six Sigma tools you used (e.g., DMAIC, 5S, Kaizen).
- 4
Discuss measurable outcomes or improvements achieved.
- 5
Highlight how this experience enhanced your engineering skills.
Example Answers
In my previous role, I led a project using DMAIC to reduce cycle time in our assembly line. We identified bottlenecks during the Measure phase and implemented 5S to organize workstations. As a result, we reduced cycle time by 20% over three months, significantly increasing throughput.
What CAD software are you experienced with, and how have you used it in your projects?
How to Answer
- 1
Identify specific CAD software you have used.
- 2
Briefly describe a project where you applied this software.
- 3
Highlight any specific features of the software that were beneficial.
- 4
Mention any team collaboration aspects or how it improved project efficiency.
- 5
Keep your answers focused and relevant to the job description.
Example Answers
I have extensive experience with SolidWorks. In my last project, I designed a custom bracket, utilizing the assembly features to ensure it fit seamlessly with existing components. The ability to run simulations in SolidWorks helped me optimize the design for strength and weight.
Explain how you have integrated automation technologies into manufacturing processes.
How to Answer
- 1
Describe a specific project where you used automation.
- 2
Mention the technology or tools you implemented.
- 3
Explain the impact on efficiency or productivity.
- 4
Use metrics or data to quantify improvements.
- 5
Highlight any challenges faced and how you overcame them.
Example Answers
In my last role, I integrated a robotic arm into our assembly line, which reduced the cycle time by 30%. We used an ABB robot for precision assembly, and the added efficiency cut labor costs significantly. Initially, we faced calibration issues, but I led a team to troubleshoot, improving our setup time by 20%.
What strategies do you use to ensure quality control in manufacturing projects?
How to Answer
- 1
Implement a detailed quality management plan at the start of the project
- 2
Use statistical process control methods to monitor production processes
- 3
Conduct regular inspections and audits during manufacturing
- 4
Incorporate feedback loops to address quality issues promptly
- 5
Provide training for all team members on quality standards and procedures
Example Answers
I begin with a comprehensive quality management plan outlining our quality goals and metrics. I also use statistical process control to monitor key processes and implement regular inspections to catch issues early.
How do you approach troubleshooting a technical issue that impacts manufacturing operations?
How to Answer
- 1
Identify and define the problem clearly
- 2
Gather relevant data and feedback from the team
- 3
Analyze the potential root causes systematically
- 4
Develop a plan for addressing the issue
- 5
Implement the solution and monitor the results
Example Answers
First, I clearly define the problem by gathering all relevant data and input from the team involved. Once I have a solid understanding, I systematically analyze possible root causes. After identifying the most likely causes, I develop a plan and implement a solution, closely monitoring the results to ensure the issue is resolved.
How do you decide which materials to use in a manufacturing project?
How to Answer
- 1
Evaluate the project requirements including strength, weight, cost, and environmental factors.
- 2
Research material properties and compatibility with manufacturing processes.
- 3
Consider supplier availability and lead times for selected materials.
- 4
Assess the lifecycle impact of materials, including recyclability and sustainability.
- 5
Conduct tests or simulations to verify material performance for the intended use.
Example Answers
I analyze the project's specifications to ensure the chosen materials meet strength and weight criteria, then I look for cost-effective options while considering supplier reliability.
What is your approach to maintaining manufacturing equipment to prevent downtime?
How to Answer
- 1
Implement a scheduled maintenance program with regular check-ups
- 2
Utilize predictive maintenance using data analysis to foresee potential failures
- 3
Train operators to recognize early signs of equipment issues
- 4
Keep a well-documented history of maintenance activities and repairs
- 5
Have spare parts readily available to reduce repair times
Example Answers
I believe in a proactive maintenance strategy. I implement a scheduled maintenance program to ensure that equipment is regularly checked and serviced. Additionally, I leverage predictive maintenance tools to analyze equipment data for potential issues before they cause downtime.
Behavioral Interview Questions
Describe a time when you successfully led a cross-functional team in a manufacturing project.
How to Answer
- 1
Choose a specific project as an example
- 2
Highlight your role and contributions
- 3
Explain the impact of your leadership on the team
- 4
Include any challenges faced and solutions implemented
- 5
Mention outcomes and lessons learned
Example Answers
In my last project, I led a team of engineers and production staff to streamline a bottleneck in our assembly line. I organized daily stand-ups to align our efforts and tackled communication barriers by setting up a collaborative tool. As a result, we reduced assembly time by 20% within three months.
Tell me about a complex manufacturing problem you faced and how you resolved it.
How to Answer
- 1
Identify a specific problem that had a significant impact.
- 2
Explain the steps you took to analyze the situation.
- 3
Describe the solution you implemented and why it was effective.
- 4
Mention any collaboration with team members or stakeholders.
- 5
Highlight the results and what you learned from the experience.
Example Answers
In my previous role, we faced a major quality issue with a product line that was leading to increased returns. I conducted a root cause analysis and discovered that a supplier's material was subpar. I coordinated with the supplier to improve their quality control and implemented additional in-house testing. This reduced our return rate by 40% over three months.
Don't Just Read Manufacturing Project Engineer Questions - Practice Answering Them!
Reading helps, but actual practice is what gets you hired. Our AI feedback system helps you improve your Manufacturing Project Engineer interview answers in real-time.
Personalized feedback
Unlimited practice
Used by hundreds of successful candidates
Describe a situation where you had a conflict with a team member on a project. How did you handle it?
How to Answer
- 1
Stay calm and professional during the conflict.
- 2
Identify the root cause of the disagreement.
- 3
Listen actively to the other person's perspective.
- 4
Propose a compromise or solution that benefits the project.
- 5
Follow up to ensure the issue is fully resolved.
Example Answers
In a recent project, I disagreed with a colleague about the best approach to streamline our workflow. I remained calm and sought to understand his viewpoint. After discussing our differing ideas, we identified that both approaches had merits. We compromised by integrating elements of both methods, which ultimately improved our efficiency.
What techniques do you use to keep manufacturing projects on schedule and within budget?
How to Answer
- 1
Prioritize effective communication with all stakeholders
- 2
Use project management software to track progress and budgets
- 3
Implement regular status meetings to address issues promptly
- 4
Break projects into smaller tasks with clear deadlines
- 5
Engage in risk management to identify and mitigate potential delays
Example Answers
I prioritize communication by holding regular check-ins with the team and stakeholders to ensure everyone is aligned with project goals and timelines.
Provide an example of how you effectively communicated a difficult decision to your team.
How to Answer
- 1
Choose a specific situation where you communicated a tough decision.
- 2
Explain the decision briefly and its impact on the team or project.
- 3
Describe how you prepared for the communication, including gathering necessary information.
- 4
Share how you delivered the message and addressed team concerns.
- 5
Conclude with the outcome and any follow-up actions taken.
Example Answers
In a previous project, I had to inform my team that we were cutting two positions due to budget constraints. I gathered all the relevant information beforehand and prepared materials to explain the reasoning. During the meeting, I communicated the decision clearly, ensuring everyone understood the reasons behind it. I encouraged questions and addressed concerns, which helped us stay unified. In the end, I followed up individually with team members to support them through the transition.
Situational Interview Questions
How would you foster innovation within a team that is resistant to change?
How to Answer
- 1
Encourage open communication and create a safe space for ideas.
- 2
Introduce small, incremental changes to show benefits.
- 3
Recognize and celebrate quick wins to build momentum.
- 4
Involve the team in the decision-making process to gain buy-in.
- 5
Provide training or resources to help team members adapt.
Example Answers
I would start by facilitating an open discussion where team members can express their concerns and ideas. By creating a trusting environment, we can identify barriers and potential solutions together. Once we have some small wins, like streamlining a process, I would celebrate those achievements to show the value of change.
A new technology is available that could improve production efficiency. How would you evaluate and implement it?
How to Answer
- 1
Identify the specific benefits the technology offers
- 2
Assess the compatibility with current production processes
- 3
Engage key stakeholders for feedback and insights
- 4
Conduct a cost-benefit analysis to justify investment
- 5
Create a pilot program to test the technology before full implementation
Example Answers
First, I would identify how the new technology improves efficiency, such as faster production times or reduced waste. Next, I would check how well it fits with our existing processes and systems. I would involve team members to gain their insights and gather concerns. Then, I would perform a cost-benefit analysis to assess whether the investment is worthwhile. Finally, I would propose a pilot program to test it on a small scale before a full rollout.
Don't Just Read Manufacturing Project Engineer Questions - Practice Answering Them!
Reading helps, but actual practice is what gets you hired. Our AI feedback system helps you improve your Manufacturing Project Engineer interview answers in real-time.
Personalized feedback
Unlimited practice
Used by hundreds of successful candidates
You are behind schedule on a critical project. What steps would you take to get back on track?
How to Answer
- 1
Assess the current project status and identify specific delays
- 2
Prioritize tasks based on their impact on the overall project timeline
- 3
Communicate with the team to gather feedback and potential solutions
- 4
Develop a revised plan with clear milestones for recovery
- 5
Monitor progress closely and adjust the plan as necessary
Example Answers
First, I would analyze the project timeline to identify where the delays are occurring. Then, I would prioritize the critical tasks that need to be completed next and communicate with my team to brainstorm solutions. Based on this input, I would create a revised action plan with specific deadlines and keep tracking our progress along the way.
How would you handle a safety compliance issue that arises in the middle of a project?
How to Answer
- 1
Assess the situation immediately and ensure the safety of all personnel
- 2
Identify the specific compliance issue and gather relevant information
- 3
Communicate with the project team and management about the issue
- 4
Take corrective action to resolve the compliance issue as per industry standards
- 5
Document the issue and the steps taken to prevent future occurrences
Example Answers
If a safety compliance issue arises, the first thing I would do is ensure everyone is safe and remove any hazards. Then, I would quickly identify the issue, discuss it with the team, and involve management to devise a corrective plan based on regulatory requirements.
You encounter unexpected costs during a project. How do you manage the budget effectively?
How to Answer
- 1
Quickly identify the source of the unexpected costs.
- 2
Communicate with stakeholders about the budget impact.
- 3
Look for areas to cut costs without compromising quality.
- 4
Consider reallocating budget from less critical tasks.
- 5
Monitor and revise the budget frequently with a contingency plan.
Example Answers
First, I would analyze where the unexpected costs are coming from. Then, I would inform the stakeholders about the issue and discuss adjusting the budget. I would seek to cut costs in non-essential areas and possibly reallocate funds from lower priority tasks to cover necessary expenses.
How would you manage a situation where a key supplier fails to deliver on time?
How to Answer
- 1
Communicate immediately with the supplier to understand the issue.
- 2
Evaluate alternative suppliers or backup plans that can be activated.
- 3
Prioritize the impact on the project and inform stakeholders.
- 4
Explore options for temporary solutions to mitigate delays.
- 5
Document the situation for future reference and continuous improvement.
Example Answers
I would first reach out to the supplier to gain clarity on the delay and understand their timeline for resolution. Then, I would assess alternative suppliers to see if we can source the required materials quickly. It's crucial to keep my team and management informed about the situation and its potential impact on our project timeline.
What would you do if a client requests a major change near the end of a project?
How to Answer
- 1
Acknowledge the client's request calmly and professionally
- 2
Assess the potential impact of the change on timeline and budget
- 3
Communicate with your team about feasibility and resources
- 4
Present the client with options regarding the change and possible consequences
- 5
Document the discussion and agreements reached with the client
Example Answers
I would start by acknowledging the client's request and showing understanding. Then, I would evaluate how this change impacts our current timeline and budget. I would communicate with my team to see what resources are needed and then present the client with options including any delays or cost adjustments that might occur.
Imagine your team is understaffed for an upcoming project. How would you manage resources?
How to Answer
- 1
Assess current team capabilities and skills
- 2
Prioritize critical tasks and deadlines
- 3
Identify and utilize any cross-training opportunities within the team
- 4
Consider bringing in temporary resources or interns if necessary
- 5
Communicate openly with stakeholders about potential impacts
Example Answers
I would first evaluate the skills of my current team to ensure we focus on tasks that align with their strengths. Then, I would prioritize the most critical aspects of the project that must be completed first.
How would you approach analyzing production data to identify the root cause of a recurring issue?
How to Answer
- 1
Review historical production data for patterns and trends
- 2
Use statistical methods to analyze deviations from standard performance
- 3
Collaborate with the production team for qualitative insights
- 4
Identify correlation between variables and the recurring issue
- 5
Document findings and propose actionable solutions
Example Answers
I would start by reviewing the production data over the past few months to spot any patterns related to the recurring issue. Then, I would apply statistical analysis to see if there are specific times or conditions when the issue occurs more frequently. I would also discuss with the operators to gather their insights on potential root causes before identifying correlations and proposing solutions.
You identify a potential risk in a project. How do you assess and mitigate this risk?
How to Answer
- 1
Identify the nature of the risk and its potential impact on the project.
- 2
Gather data on the likelihood of the risk occurring using historical data or expert opinions.
- 3
Develop a risk mitigation plan that includes both prevention strategies and contingency plans.
- 4
Engage stakeholders to ensure alignment on risk assessment and mitigation strategies.
- 5
Regularly review and update the risk assessment as the project progresses.
Example Answers
I first identify the risk, such as a supply chain disruption, and assess its impact by analyzing how it could delay project timelines. Then, I gather data on past supply issues and engage with suppliers to understand their reliability. I create a mitigation plan that includes sourcing alternative suppliers and building a buffer stock to minimize impact if the risk occurs. I ensure all stakeholders are informed and maintain regular risk reviews to update our strategies as necessary.
Don't Just Read Manufacturing Project Engineer Questions - Practice Answering Them!
Reading helps, but actual practice is what gets you hired. Our AI feedback system helps you improve your Manufacturing Project Engineer interview answers in real-time.
Personalized feedback
Unlimited practice
Used by hundreds of successful candidates
How would you coordinate with other departments to ensure the success of a manufacturing project?
How to Answer
- 1
Establish clear communication channels with each department involved.
- 2
Set regular meetings to discuss project progress and address concerns.
- 3
Use project management tools to keep track of timelines and responsibilities.
- 4
Foster collaboration by inviting feedback and suggestions from team members.
- 5
Align project goals with the objectives of other departments to ensure buy-in.
Example Answers
I would set up a weekly meeting with representatives from design, procurement, and quality assurance to ensure we are aligned on project status and any issues we face.
You notice skill gaps in your team affecting production. How would you address this?
How to Answer
- 1
Identify specific skill gaps through assessments or observations
- 2
Develop a targeted training plan that addresses these gaps
- 3
Encourage mentorship and knowledge sharing within the team
- 4
Implement regular feedback mechanisms to track progress
- 5
Measure the impact of training on production outcomes
Example Answers
I would first assess the team's skills to pinpoint what is lacking. Once identified, I would create a focused training program tailored to those needs. This could include workshops and on-the-job training. Additionally, I'd pair less experienced team members with seasoned professionals to promote knowledge sharing.
How would you incorporate sustainability practices into a manufacturing process?
How to Answer
- 1
Evaluate current processes for waste and inefficiency
- 2
Implement energy-efficient machinery and renewable energy sources
- 3
Develop a materials recycling program
- 4
Design products with lifecycle sustainability in mind
- 5
Engage employees in sustainability initiatives through training
Example Answers
I would start by assessing the existing manufacturing workflow to identify areas of waste, such as excess energy use or materials that could be recycled. Then, I would introduce energy-efficient machines and consider solar panels to power operations inherently.
How would you integrate customer feedback into your manufacturing processes?
How to Answer
- 1
Establish a system to collect feedback regularly from customers.
- 2
Analyze the feedback to identify common issues or suggestions.
- 3
Collaborate with cross-functional teams to discuss feedback insights.
- 4
Implement changes in manufacturing processes based on validated feedback.
- 5
Monitor the impact of changes and follow up with customers for further input.
Example Answers
I would set up a feedback loop where customers can easily report their experiences and suggestions. After collecting feedback, I would analyze it to pinpoint key improvement areas, discuss these with the design and production teams, and implement the necessary changes in our processes.
Manufacturing Project Engineer Position Details
Recommended Job Boards
These job boards are ranked by relevance for this position.
Related Positions
- Manufacturing Engineer
- Manufacturing Systems Engineer
- Manufacturing Process Engineer
- Manufacturing Specialist
- Lean Manufacturing Engineer
- Facility Engineer
- Manufacturing Project Manager
- Manufacturing Manager
- Manufacturing Operations Manager
- Manufacturing Technologist
Similar positions you might be interested in.
Ace Your Next Interview!
Practice with AI feedback & get hired faster
Personalized feedback
Used by hundreds of successful candidates
Ace Your Next Interview!
Practice with AI feedback & get hired faster
Personalized feedback
Used by hundreds of successful candidates