Top 30 Lean Manufacturing Engineer Interview Questions and Answers [Updated 2025]
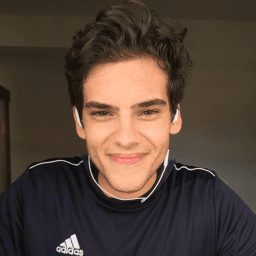
Andre Mendes
•
March 30, 2025
Preparing for a Lean Manufacturing Engineer interview can be daunting, but with the right guidance, you can navigate it with confidence. This blog post covers the most common interview questions you might face in this role, complete with example answers and practical tips on responding effectively. Dive in to enhance your interview skills and make a lasting impression on potential employers.
Download Lean Manufacturing Engineer Interview Questions in PDF
To make your preparation even more convenient, we've compiled all these top Lean Manufacturing Engineerinterview questions and answers into a handy PDF.
Click the button below to download the PDF and have easy access to these essential questions anytime, anywhere:
List of Lean Manufacturing Engineer Interview Questions
Behavioral Interview Questions
Can you tell us about a time you successfully implemented a lean initiative as part of a team?
How to Answer
- 1
Choose a specific lean initiative, such as 5S, Kaizen, or waste reduction.
- 2
Explain the situation, the challenge your team faced, and what prompted the lean initiative.
- 3
Describe your role in the implementation and how you collaborated with your team.
- 4
Share the results achieved and any measurable improvements.
- 5
Highlight any lessons learned or follow-up actions taken.
Example Answers
In my previous role, our team noticed significant delays in our production line. We initiated a 5S project to organize the workspace. I led the team in categorizing tools and materials. We reduced search time by 40% and increased efficiency by 20%. This project taught us the importance of continuous organization.
Describe a situation where you identified a wasteful process and how you addressed it.
How to Answer
- 1
Think of a specific example from your past work experience.
- 2
Clearly define the wasteful process you identified.
- 3
Explain the impact of this waste on efficiency or costs.
- 4
Describe the actions you took to address the waste.
- 5
Share the results or improvements that followed your actions.
Example Answers
At my previous job, I noticed that our assembly line had a long waiting period due to inefficient layout. I mapped out the flow of materials and rearranged the stations to minimize movement. As a result, we reduced assembly time by 20%.
Don't Just Read Lean Manufacturing Engineer Questions - Practice Answering Them!
Reading helps, but actual practice is what gets you hired. Our AI feedback system helps you improve your Lean Manufacturing Engineer interview answers in real-time.
Personalized feedback
Unlimited practice
Used by hundreds of successful candidates
Have you ever led a cross-functional team to achieve a manufacturing improvement? What was your approach?
How to Answer
- 1
Start with a brief description of the team and its members.
- 2
Explain the specific manufacturing issue you aimed to improve.
- 3
Describe the approach you used to coordinate and motivate the team.
- 4
Highlight the tools or methodologies applied, such as Lean or Six Sigma.
- 5
Conclude with the measurable results or improvements achieved.
Example Answers
I led a team of engineers, operators, and quality inspectors to reduce waste in our assembly line. We identified excess movement as a major issue. I facilitated regular meetings to brainstorm ideas and used value stream mapping to pinpoint inefficiencies. As a result, we decreased cycle time by 15% and improved overall productivity.
Describe a time when you had to adjust a major project plan due to unexpected changes. What did you do?
How to Answer
- 1
Choose a specific project and clearly outline the unexpected change.
- 2
Explain your thought process in assessing the situation.
- 3
Describe the steps you took to adjust the project plan.
- 4
Highlight the outcome and any improvements made.
- 5
Reflect on what you learned from the experience.
Example Answers
In my last project, we faced a sudden supplier delay. I quickly communicated with the team to assess our timeline. We identified alternative suppliers and adjusted our delivery schedule. As a result, we completed the project just a week behind schedule, but maintained client satisfaction. I learned the importance of flexible planning.
Tell me about a time when you suggested an innovative solution that improved a process. What was the outcome?
How to Answer
- 1
Choose a specific example that showcases your problem-solving skills.
- 2
Describe the context and the challenge you faced.
- 3
Explain the innovative solution you proposed clearly.
- 4
Share the measurable outcome or impact of your solution.
- 5
Reflect briefly on what you learned from the experience.
Example Answers
In my previous role as a Lean Engineer, I noticed that our assembly line had excessive downtime due to unclear tasks for workers. I proposed a visual scheduling system using Kanban boards that highlighted daily tasks and priorities. This reduced downtime by 30% and improved overall efficiency. I learned that clear communication is vital in a team setting.
Have you worked with other departments (e.g., marketing, R&D) to implement lean practices? Share an experience.
How to Answer
- 1
Focus on a specific collaboration example with another department.
- 2
Highlight the problem you addressed using lean principles.
- 3
Explain the actions you took and who you worked with.
- 4
Describe the outcome and improvements achieved.
- 5
Emphasize teamwork and communication in your response.
Example Answers
In my previous role, I collaborated with the marketing team to streamline our promotional material process. We identified that approval delays were causing bottlenecks. By applying lean techniques, we created a standardized checklist for approvals which reduced lead time by 30%.
Describe an instance where a project or initiative did not go as planned. How did you handle it?
How to Answer
- 1
Choose a specific project with clear challenges.
- 2
Explain the initial plan and what went wrong.
- 3
Detail the steps you took to address the issues.
- 4
Highlight what you learned from the experience.
- 5
Conclude with how it improved future projects.
Example Answers
In a recent assignment, we aimed to reduce waste in our production line. Midway through, we discovered the new process was not compatible with our existing equipment. I organized a team meeting to re-evaluate the project and switched to a phased implementation approach. This allowed us to gradually adapt the equipment while minimizing disruption. I learned the importance of compatibility checks before project kickoff.
How do you prioritize tasks when working on multiple lean projects simultaneously?
How to Answer
- 1
Identify project deadlines and critical deliverables early.
- 2
Assess the potential impact of each task on overall project goals.
- 3
Use a scoring system to rank tasks based on urgency and importance.
- 4
Communicate with stakeholders to understand their priorities.
- 5
Be flexible and ready to reassess priorities as projects evolve.
Example Answers
I start by listing all the tasks for each project and their deadlines. Then, I evaluate which tasks will have the most significant impact on project success. I might use a priority matrix to categorize tasks into urgent and important, ensuring I focus on high-impact tasks first.
Technical Interview Questions
Can you explain the concept of value stream mapping and how you've used it in past projects?
How to Answer
- 1
Define value stream mapping clearly and its purpose in identifying waste.
- 2
Share a specific project where you applied value stream mapping.
- 3
Discuss the steps you took in creating the value stream map.
- 4
Highlight the outcomes or improvements that resulted from your analysis.
- 5
Keep it concise and focus on how it benefited the team or project.
Example Answers
Value stream mapping is a visual tool that helps identify waste in processes. I used it in a project where we were experiencing delays in production. I mapped out the current state of our process, identified bottlenecks, and we implemented solutions that reduced lead time by 20%.
What is the difference between Lean and Six Sigma? How have you applied each in your work?
How to Answer
- 1
Define Lean as a methodology focused on eliminating waste.
- 2
Explain Six Sigma as a data-driven approach for reducing defects.
- 3
Provide a brief example of a Lean project you've led.
- 4
Mention a specific instance where you used Six Sigma tools like DMAIC.
- 5
Emphasize results achieved from both methodologies.
Example Answers
Lean focuses on eliminating waste to improve efficiency. For example, I implemented a 5S system in the production area, which reduced wasted motion and improved workflow. In terms of Six Sigma, I worked on a project where we utilized the DMAIC framework to reduce defects in a component, which decreased our error rate by 30%.
Don't Just Read Lean Manufacturing Engineer Questions - Practice Answering Them!
Reading helps, but actual practice is what gets you hired. Our AI feedback system helps you improve your Lean Manufacturing Engineer interview answers in real-time.
Personalized feedback
Unlimited practice
Used by hundreds of successful candidates
What is a Kaizen event and how would you facilitate one to improve a manufacturing process?
How to Answer
- 1
Begin by defining a Kaizen event as a focused, short-term project aimed at improving a specific process.
- 2
Identify the specific problem or area for improvement before the event.
- 3
Gather a cross-functional team with relevant stakeholders from different departments.
- 4
Use data and metrics to analyze the current process and identify waste.
- 5
Facilitate brainstorming sessions to develop and implement solutions, followed by a plan to measure results.
Example Answers
A Kaizen event is a structured approach to improve a process by focusing on a specific area over a short time. To facilitate one, I would first identify a process that needs improvement, then gather a team of stakeholders. Next, I would analyze the current process using relevant data to identify wastes, then facilitate brainstorming sessions to implement solutions, ensuring we have measurable outcomes to assess our improvements.
How do you conduct a root cause analysis to identify the source of inefficiencies in a production process?
How to Answer
- 1
Define the problem clearly and quantify the inefficiencies.
- 2
Gather data from the production process to support your analysis.
- 3
Use techniques like the 5 Whys or Fishbone diagram to identify root causes.
- 4
Involve team members for diverse perspectives and insights.
- 5
Test and validate the identified root causes before implementing solutions.
Example Answers
I start by defining the specific inefficiency, such as increased cycle times, and gather data to quantify it. Then, I apply the 5 Whys technique, asking why the delay occurs at each step until I identify the root cause, like a bottleneck in a specific machine.
What role does Total Productive Maintenance (TPM) play in lean manufacturing, and how have you implemented it?
How to Answer
- 1
Explain how TPM enhances equipment efficiency and reduces downtime.
- 2
Discuss the relationship between TPM and employee engagement in lean environments.
- 3
Provide a specific example of a TPM initiative you led or contributed to.
- 4
Mention measurable outcomes from implementing TPM, like reduced maintenance costs or increased production.
- 5
Keep the focus on continuous improvement and how TPM supports lean principles.
Example Answers
TPM is crucial in lean manufacturing as it ensures equipment is reliable and available, reducing downtime. In my last role, I led a TPM initiative that trained operators to perform daily checks on machines, which cut maintenance issues by 30% over six months.
Explain the 5S methodology and how you have implemented it in a workplace.
How to Answer
- 1
Define each of the 5S elements: Sort, Set in order, Shine, Standardize, Sustain.
- 2
Share a specific example of implementation in your workplace.
- 3
Highlight the outcomes or improvements post-implementation.
- 4
Mention any challenges faced and how they were overcome.
- 5
Keep your answer structured and concise to maintain clarity.
Example Answers
5S is a methodology that focuses on workplace organization and efficiency. In my last role, I led a team to implement 5S in our assembly line. We started by sorting and removing unnecessary tools, then organized the workspace for easy access. After cleaning, we standardized our procedures for a cleaner environment. This led to a 20% reduction in time spent looking for tools and improved overall productivity.
What approaches do you use to optimize flow efficiency in a manufacturing setting?
How to Answer
- 1
Identify bottlenecks and analyze the current process flow.
- 2
Implement Lean tools such as 5S, Value Stream Mapping, or Kaizen events.
- 3
Use data and metrics to track flow and identify areas for improvement.
- 4
Encourage cross-training to enhance flexibility in workforce utilization.
- 5
Foster a culture of continuous improvement and employee feedback.
Example Answers
To optimize flow efficiency, I first map the entire process to identify bottlenecks. Using Value Stream Mapping, I can visualize where delays occur and apply 5S to organize the workspace. I also track key performance indicators to monitor the improvements made.
Describe Just-In-Time (JIT) production and its significance in lean manufacturing.
How to Answer
- 1
Start with a clear definition of JIT production.
- 2
Explain the principles of reducing waste and improving efficiency.
- 3
Discuss how JIT affects inventory management and flow of materials.
- 4
Mention the role of JIT in meeting customer demand without excess.
- 5
Conclude with the impact of JIT on overall production costs and responsiveness.
Example Answers
Just-In-Time production is a strategy that aligns production with customer demand. It reduces waste by only producing what is needed, when it is needed, improving efficiency. JIT leads to lower inventory costs and a smoother flow of materials, which helps companies respond quickly to changes in demand.
What is process simulation in lean manufacturing, and when would you use it?
How to Answer
- 1
Define process simulation clearly and its role in lean manufacturing.
- 2
Explain its benefits, such as identifying inefficiencies and visualizing workflows.
- 3
Provide examples of situations where simulation is particularly useful.
- 4
Mention tools or software used for process simulation.
- 5
Wrap up by emphasizing its importance in continuous improvement.
Example Answers
Process simulation in lean manufacturing refers to creating a digital model of a manufacturing process to analyze and optimize performance. It's beneficial for identifying bottlenecks before implementation, especially in new production lines.
How does automation integrate into lean processes, and what has been your experience with it?
How to Answer
- 1
Explain how automation eliminates waste and enhances efficiency in lean processes.
- 2
Mention specific tools or technologies you've used, such as robotics or software systems.
- 3
Discuss how you have implemented automation in your previous roles to support lean principles.
- 4
Share measurable outcomes or improvements resulting from automation in lean settings.
- 5
Emphasize the importance of training and involvement of the workforce in automation efforts.
Example Answers
In my last role, I integrated robotic arms on the assembly line, which reduced cycle time by 30% and decreased defects. This supported our lean goal of minimizing waste and improving quality.
Don't Just Read Lean Manufacturing Engineer Questions - Practice Answering Them!
Reading helps, but actual practice is what gets you hired. Our AI feedback system helps you improve your Lean Manufacturing Engineer interview answers in real-time.
Personalized feedback
Unlimited practice
Used by hundreds of successful candidates
Which problem-solving tools do you find most effective for lean manufacturing and why?
How to Answer
- 1
Identify a few key tools you have used, like 5 Whys, Fishbone diagrams, or Value Stream Mapping.
- 2
Explain why each tool is effective in specific situations.
- 3
Use examples from your experience to demonstrate their application.
- 4
Focus on the impact these tools had on efficiency or waste reduction.
- 5
Be concise, clear, and directly relate your answers to lean principles.
Example Answers
In my experience, I find the 5 Whys particularly effective for root cause analysis. When we identified recurring quality issues, using the 5 Whys helped us drill down to manufacturing inconsistencies, leading to targeted improvements in our processes.
What is standard work in lean manufacturing, and how do you develop and implement it?
How to Answer
- 1
Define standard work clearly, focusing on its role in consistency and quality.
- 2
Explain the elements of standard work: work sequence, time, and inventory.
- 3
Describe the steps in developing standard work: observe, document, and validate.
- 4
Discuss the importance of team involvement in creating standard work.
- 5
Mention the need for regular review and updates to standard work.
Example Answers
Standard work is a key lean tool that defines the best-known way to perform a task, ensuring consistent output and quality. To develop it, I start by observing the current process, documenting the ideal work sequence, cycle time, and any necessary inventory. I involve the team in validating this process through practice. Finally, I ensure we regularly review and refine the standard work to adapt to changes.
Situational Interview Questions
You are tasked with reducing lead time by 20%. What process improvement strategies would you consider?
How to Answer
- 1
Identify bottlenecks in the current process using value stream mapping.
- 2
Implement just-in-time inventory to align production with demand.
- 3
Increase cross-training of employees to improve flexibility.
- 4
Standardize processes to eliminate variations and delays.
- 5
Utilize technology for automated tracking and reporting of process flows.
Example Answers
I would start by mapping the current processes to identify bottlenecks. Then, I would implement just-in-time inventory to reduce unnecessary stock and improve flow.
If you encounter resistance from a team member during a process change, how would you handle it?
How to Answer
- 1
Listen to the team member's concerns fully without interrupting.
- 2
Acknowledge their feelings and the validity of their perspective.
- 3
Provide clear information on the benefits and reasons for the change.
- 4
Involve them in the change process by seeking their input.
- 5
Follow up after the change is implemented to ensure ongoing support.
Example Answers
I would first listen to the team member's concerns to understand their resistance. It's important to acknowledge their feelings. Then, I would explain the benefits of the process change and why it is necessary for our goals. I would also invite them to share their thoughts on how we can improve the change to make it easier for everyone.
Don't Just Read Lean Manufacturing Engineer Questions - Practice Answering Them!
Reading helps, but actual practice is what gets you hired. Our AI feedback system helps you improve your Lean Manufacturing Engineer interview answers in real-time.
Personalized feedback
Unlimited practice
Used by hundreds of successful candidates
Imagine you are brought in to assess a failing production line. What steps would you take to identify and address the issues?
How to Answer
- 1
Conduct a thorough analysis of the current production data to identify bottlenecks.
- 2
Perform a walk-through of the production line to observe workflows and worker interactions.
- 3
Engage with operators and staff to gather insights on issues they face.
- 4
Implement root cause analysis for identified problems using tools like 5 Whys or Fishbone diagrams.
- 5
Develop a structured action plan with clear timelines and measurable goals.
Example Answers
First, I would analyze production data to identify any significant delays or inefficiencies. Then, I'd walk the line to observe the actual operations and discuss with team members for their input. This combined approach would help root out the core issues which we could then tackle systematically.
Present a strategy to reduce operational costs without compromising on quality.
How to Answer
- 1
Identify waste in the production process using Lean tools like value stream mapping.
- 2
Implement continuous improvement initiatives to enhance efficiency and reduce costs.
- 3
Train staff on best practices to ensure quality standards while using materials efficiently.
- 4
Utilize data analytics to monitor key performance indicators and address cost issues proactively.
- 5
Explore supplier partnerships to negotiate better pricing without sacrificing material quality.
Example Answers
By using value stream mapping, I would identify and eliminate waste in our production process, enabling us to reduce costs while maintaining quality. Continuous improvement initiatives would help us make incremental changes that lead to significant savings over time.
Suppose you're given data indicating an increase in defect rates. How would you investigate this issue?
How to Answer
- 1
Gather detailed defect data including time frame, location, and product type
- 2
Analyze the production process to identify changes or anomalies during the increase
- 3
Hold meetings with relevant stakeholders to gather insights and observations
- 4
Use root cause analysis techniques like Fishbone diagrams or 5 Whys to pinpoint issues
- 5
Implement corrective actions and monitor results to assess effectiveness
Example Answers
I would first collect and review defect data to identify when and where the spikes occurred. Then, I'd analyze the production process during those times to check for any changes. Engaging with the team to discuss observations would be critical, and I would use 5 Whys to drill down to the root cause before implementing fixes.
If faced with a supply chain disruption, how would you maintain lean operations?
How to Answer
- 1
Identify alternative suppliers quickly to mitigate reliance on a single source.
- 2
Use inventory management to prioritize critical components and reduce waste.
- 3
Implement flexible production schedules to adapt to changing material availability.
- 4
Engage cross-functional teams to communicate disruptions and collaboratively find solutions.
- 5
Continuously monitor supply chain metrics to identify potential issues early.
Example Answers
In case of a supply chain disruption, I would immediately assess our supplier network to find alternative suppliers. I would also analyze our inventory to prioritize the use of critical materials, minimizing waste while adapting our production schedule accordingly.
You're observing a quality issue on the production line. What steps do you take to resolve it?
How to Answer
- 1
Identify the root cause of the quality issue through observation and data analysis
- 2
Engage the team involved in the production process to gather insights and suggestions
- 3
Implement a temporary solution to mitigate immediate effects on production
- 4
Develop a long-term corrective action plan to address the root cause
- 5
Monitor the effectiveness of the implemented solutions and adjust as necessary
Example Answers
First, I would analyze the data related to the quality issue and observe the production process to identify the root cause. Then, I would discuss the issue with the team members involved to gather their input and insights. After that, I would implement a temporary fix to minimize disruptions while we work on a permanent solution. Finally, I would develop a corrective action plan and monitor its effectiveness over the following weeks.
If management is hesitant to support a lean initiative, how would you secure their buy-in?
How to Answer
- 1
Identify key pain points for management that lean can address.
- 2
Use data and case studies to demonstrate the benefits of lean.
- 3
Engage management in discussions to understand their concerns.
- 4
Propose a pilot project to showcase lean effectiveness.
- 5
Communicate the alignment of lean with organizational goals.
Example Answers
I would first understand management's specific concerns about the lean initiative. Then, I would present them with data and examples from similar companies that successfully implemented lean and achieved significant cost savings. I could propose a small pilot project to demonstrate the benefits without requiring full commitment up front.
How do you adjust lean manufacturing processes to accommodate a sudden increase in demand?
How to Answer
- 1
Assess current capacity and identify bottlenecks in the process
- 2
Engage cross-functional teams to discuss flexible resource allocation
- 3
Implement quick wins such as overtime or additional shifts
- 4
Consider temporary partnerships with suppliers for additional materials
- 5
Monitor and adjust KPIs to ensure quality and efficiency remain high
Example Answers
To handle a sudden demand increase, I first analyze the existing production flow to spot any bottlenecks. Then, I collaborate with teams to shift resources where needed, including increasing workforce hours. Short-term partnerships with suppliers can also help source materials quickly. Finally, I track KPIs to ensure we maintain quality while ramping up production.
A new technology is introduced in the industry. How would you evaluate its potential for integration into your processes?
How to Answer
- 1
Start with a thorough understanding of the technology and its capabilities.
- 2
Identify specific areas in your processes where the technology could be beneficial.
- 3
Consider the cost of implementation versus the expected benefits.
- 4
Engage with stakeholders to gather insights and feedback on the technology.
- 5
Plan a pilot project to test the technology in a controlled environment.
Example Answers
I would first research the technology to understand its features and functions. Then, I would analyze our current processes to find pain points where this technology could provide improvements. I would assess costs versus benefits and consult with my team to make sure we're aligned before running a pilot test.
Don't Just Read Lean Manufacturing Engineer Questions - Practice Answering Them!
Reading helps, but actual practice is what gets you hired. Our AI feedback system helps you improve your Lean Manufacturing Engineer interview answers in real-time.
Personalized feedback
Unlimited practice
Used by hundreds of successful candidates
Lean Manufacturing Engineer Position Details
Recommended Job Boards
These job boards are ranked by relevance for this position.
Related Positions
Ace Your Next Interview!
Practice with AI feedback & get hired faster
Personalized feedback
Used by hundreds of successful candidates
Ace Your Next Interview!
Practice with AI feedback & get hired faster
Personalized feedback
Used by hundreds of successful candidates