Top 30 Manufacturing Process Engineer Interview Questions and Answers [Updated 2025]
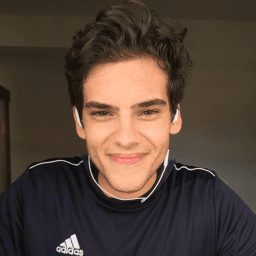
Andre Mendes
•
March 30, 2025
Preparing for a Manufacturing Process Engineer interview can be daunting, but mastering the most common interview questions can boost your confidence and set you on the path to success. In this post, we provide you with essential questions, example answers, and insightful tips to help you respond effectively. Dive in to enhance your understanding and readiness for securing your next role in manufacturing process engineering.
Download Manufacturing Process Engineer Interview Questions in PDF
To make your preparation even more convenient, we've compiled all these top Manufacturing Process Engineerinterview questions and answers into a handy PDF.
Click the button below to download the PDF and have easy access to these essential questions anytime, anywhere:
List of Manufacturing Process Engineer Interview Questions
Behavioral Interview Questions
Describe a time when you identified a process improvement opportunity in a manufacturing environment and how you implemented the change.
How to Answer
- 1
Use the STAR method: Situation, Task, Action, Result.
- 2
Be specific about the process you improved.
- 3
Include measurable outcomes to highlight success.
- 4
Explain the steps you took to implement the change.
- 5
Mention any team collaboration that occurred.
Example Answers
In my previous role at XYZ Manufacturing, I noticed that the assembly line was experiencing delays due to inefficient material handling. I analyzed the workflow and proposed a layout change, minimizing the distance traveled by workers. After implementing this change, we reduced assembly time by 15%, improving overall productivity.
Good Candidates Answer Questions. Great Ones Win Offers.
Reading sample answers isn't enough. Top candidates practice speaking with confidence and clarity. Get real feedback, improve faster, and walk into your next interview ready to stand out.
Master your interview answers under pressure
Boost your confidence with real-time practice
Speak clearly and impress hiring managers
Get hired faster with focused preparation
Used by hundreds of successful candidates
Tell me about a time when you worked as part of a cross-functional team to improve a manufacturing process.
How to Answer
- 1
Choose a specific project that involved multiple departments.
- 2
Highlight your role and contributions to the team effort.
- 3
Explain the problem you were addressing with the process improvement.
- 4
Discuss the outcome or results of your collaboration.
- 5
Mention any learned insights or skills gained from the experience.
Example Answers
In my last position, I worked on a cross-functional team to reduce waste in the assembly line. I collaborated with engineers and quality assurance to identify inefficiencies. We implemented a new layout and standardized procedures, resulting in a 15% reduction in waste within three months.
Have you ever led a team through a process change or improvement initiative? Describe your role and the outcome.
How to Answer
- 1
Describe the specific process change you initiated.
- 2
Explain your role and the responsibilities you had.
- 3
Highlight the methods you used to lead the team.
- 4
Discuss the measurable outcomes resulting from the initiative.
- 5
Share any lessons learned or future implications.
Example Answers
I led a team to implement a new quality control process in our production line. My role was to coordinate the training sessions and monitor progress. We reduced defects by 20% within three months, demonstrating the effectiveness of the new process.
Give an example of a time you had to handle a quality control issue. What was the problem and how did you address it?
How to Answer
- 1
Select a specific quality control issue you faced in your experience.
- 2
Briefly describe the impact of the issue on the production process.
- 3
Explain the steps you took to identify the root cause.
- 4
Discuss how you implemented a solution and the outcome.
- 5
Highlight any tools or methodologies you used during the process.
Example Answers
In my previous role, we identified a recurring defect in a critical component that was causing delays. I led a root cause analysis, using the 5 Whys method, which revealed a calibration issue in our machinery. I adjusted the calibration protocols and the defects were reduced by 80% within two weeks.
Describe a situation where you had to communicate a complex technical concept to non-technical team members.
How to Answer
- 1
Identify a specific technical concept you communicated.
- 2
Explain the audience's background to frame your explanation.
- 3
Use analogies or simple terms to break down the concept.
- 4
Highlight the methods you used for engagement, like visuals or hands-on examples.
- 5
Emphasize the outcome of your communication and how it benefited the team.
Example Answers
In a project to optimize our production line, I needed to explain the concept of Lean Manufacturing to the marketing team. I used a simple analogy comparing it to decluttering a room for efficiency. I presented visuals showing the before-and-after scenarios, which helped them grasp the benefits. This led to better collaboration during a product launch.
Tell me about a project you managed from conception through to completion. What challenges did you encounter and how did you overcome them?
How to Answer
- 1
Choose a specific project that highlights your skills as an engineer.
- 2
Outline the project objectives and your role clearly.
- 3
Mention at least two significant challenges and your strategies for overcoming them.
- 4
Include the outcome of the project and any lessons learned.
- 5
Be prepared to discuss the impact your project had on the company or team.
Example Answers
I led a project to redesign a manufacturing line to increase efficiency. The main challenge was integrating new machinery with existing systems. I overcame it by collaborating closely with both the machinery suppliers and our maintenance team, ensuring a smooth installation. The project finished ahead of schedule, increasing throughput by 20%.
Have you used data analysis to solve a manufacturing problem? Tell me about the situation and how data analysis helped.
How to Answer
- 1
Identify a specific manufacturing problem you faced.
- 2
Explain the data analysis methods you used.
- 3
Describe the insights gained from the data.
- 4
Discuss the actions taken based on your analysis.
- 5
Highlight the results and improvements achieved.
Example Answers
At my previous job, we were facing high defect rates in a product line. I used statistical process control charts to analyze the production data, which revealed a pattern of defects occurring during a specific shift. By adjusting the training for the night shift team, we reduced defects by 30%.
Describe a time when you had to quickly adapt to a significant change in the manufacturing process.
How to Answer
- 1
Identify a specific change you experienced.
- 2
Explain the context and why the change was necessary.
- 3
Detail your actions in response to the change.
- 4
Highlight the outcome of your actions and any improvements.
- 5
Discuss what you learned from the experience.
Example Answers
In my previous role, we encountered an unexpected machine failure that halted production. I quickly assessed the situation, coordinated with the maintenance team, and implemented a temporary workaround that allowed us to resume manufacturing with minimal downtime. This experience taught me the importance of agility and proactive communication.
Can you provide an example of an innovative solution you developed to optimize a manufacturing process?
How to Answer
- 1
Identify a specific manufacturing process you improved.
- 2
Describe the problem and why it needed an innovative solution.
- 3
Explain the innovative solution you implemented.
- 4
Highlight measurable results or improvements from your solution.
- 5
Conclude with what you learned or how it could be applied elsewhere.
Example Answers
At my previous job, we had a bottleneck in the assembly line causing delays. I introduced a dual-tasking workcell that allowed operators to manage two stations simultaneously. This reduced our cycle time by 30%. I learned that small changes can lead to significant improvements in efficiency.
Good Candidates Answer Questions. Great Ones Win Offers.
Reading sample answers isn't enough. Top candidates practice speaking with confidence and clarity. Get real feedback, improve faster, and walk into your next interview ready to stand out.
Master your interview answers under pressure
Boost your confidence with real-time practice
Speak clearly and impress hiring managers
Get hired faster with focused preparation
Used by hundreds of successful candidates
Technical Interview Questions
Explain the principles of Lean Manufacturing and how you have applied them in previous roles.
How to Answer
- 1
Start by defining Lean Manufacturing clearly and concisely.
- 2
Mention key principles such as value, waste elimination, and continuous improvement.
- 3
Provide specific examples from your experience where you've applied Lean techniques.
- 4
Discuss measurable outcomes or improvements that resulted from your Lean initiatives.
- 5
Conclude with your understanding of how Lean applies to the role you're interviewing for.
Example Answers
Lean Manufacturing focuses on maximizing value by minimizing waste. In my previous role at Company X, I implemented 5S principles to organize our workspace, reducing setup times by 20%.
What is Statistical Process Control (SPC) and how have you used it in your previous work?
How to Answer
- 1
Define SPC clearly and concisely as a method to monitor and control processes.
- 2
Describe specific tools associated with SPC like control charts.
- 3
Mention how you implemented SPC in past roles to improve quality or efficiency.
- 4
Use metrics to quantify the impact of SPC on process improvements.
- 5
Provide a real-world example that illustrates your hands-on experience.
Example Answers
Statistical Process Control (SPC) is a method utilized to monitor and control manufacturing processes through the use of control charts. In my previous role, I implemented SPC techniques by setting up control charts for our assembly line. This allowed us to identify variations early and reduce defects by 30% over six months.
Good Candidates Answer Questions. Great Ones Win Offers.
Reading sample answers isn't enough. Top candidates practice speaking with confidence and clarity. Get real feedback, improve faster, and walk into your next interview ready to stand out.
Master your interview answers under pressure
Boost your confidence with real-time practice
Speak clearly and impress hiring managers
Get hired faster with focused preparation
Used by hundreds of successful candidates
Can you describe your experience with Six Sigma methodologies in manufacturing?
How to Answer
- 1
Focus on specific projects where you implemented Six Sigma.
- 2
Mention tools used, such as DMAIC or SIPOC.
- 3
Quantify results, like percentage reductions in defects or costs.
- 4
Highlight team collaboration and leadership roles.
- 5
Share how you sustained improvements over time.
Example Answers
In my previous role at ABC Manufacturing, I led a Six Sigma project using the DMAIC framework to reduce defects in our assembly line. We achieved a 30% reduction in defects, which saved the company $50,000 annually.
Have you used simulation software to model manufacturing processes? Which tools have you used and how?
How to Answer
- 1
Identify specific simulation software you have experience with.
- 2
Explain your role in using the software for modeling.
- 3
Discuss the types of manufacturing processes you modeled.
- 4
Highlight any results or improvements achieved through simulation.
- 5
Be prepared to discuss challenges faced and how you overcame them.
Example Answers
I have used SolidWorks and AnyLogic for modeling manufacturing processes. In my previous job, I used SolidWorks to simulate assembly line layouts, which helped optimize space and workflow. As a result, we improved our production efficiency by 15%.
What types of manufacturing equipment are you most familiar with and what experience do you have troubleshooting them?
How to Answer
- 1
Identify specific types of equipment you have worked with
- 2
Mention any relevant certifications or training you have
- 3
Give examples of troubleshooting steps you've taken in the past
- 4
Highlight any improvements or solutions you implemented
- 5
Be prepared to discuss your understanding of maintenance procedures
Example Answers
I am most familiar with CNC machines and injection molding equipment. I have been trained in their operation and have hands-on experience troubleshooting issues such as misalignment in CNC setups. At my last job, I implemented a preventive maintenance schedule that reduced breakdowns by 20%.
How proficient are you with CAD software, such as AutoCAD, and how have you used it in manufacturing process design?
How to Answer
- 1
Start by stating your level of proficiency with CAD software.
- 2
Mention specific CAD tools you have experience with, like AutoCAD.
- 3
Provide examples of projects where you utilized CAD in process design.
- 4
Highlight any efficiencies or improvements you achieved through CAD.
- 5
Conclude with how your CAD skills contribute to team collaboration.
Example Answers
I am very proficient in AutoCAD, having used it for over 5 years. In my last project, I designed layouts for a new assembly line, which helped reduce workflow bottlenecks by 20%. My CAD designs are detailed and help my team visualize the production setup efficiently.
What methods do you use for root cause analysis of manufacturing defects or issues?
How to Answer
- 1
Start with defining the problem clearly and gather data to understand the scope.
- 2
Use established methods like 5 Whys, Fishbone Diagram, or Pareto Analysis to analyze issues.
- 3
Involve relevant team members to gain insights from different perspectives.
- 4
Document the findings and verify the root cause through testing or validation.
- 5
Propose actionable solutions and preventive measures based on the analysis.
Example Answers
In my previous role, I employed the 5 Whys technique to identify that a recurring defect was due to a calibration issue with a critical machine. By drilling down into why the calibration was off, I was able to implement a more rigorous maintenance schedule.
Describe your understanding of the supply chain and how it impacts manufacturing processes.
How to Answer
- 1
Explain what supply chain means in manufacturing context
- 2
Discuss key components of the supply chain like suppliers, logistics, and distribution
- 3
Highlight how delays or disruptions in the supply chain affect production schedules
- 4
Mention the importance of inventory management in balancing supply and demand
- 5
Conclude by relating supply chain efficiency to cost reduction and quality improvement
Example Answers
The supply chain in manufacturing includes everything from obtaining raw materials from suppliers, to transportation logistics, and distribution to end customers. Disruptions in any part of this chain, such as late deliveries of materials, can halt production and increase costs. Therefore, maintaining a well-coordinated supply chain is essential for optimizing manufacturing processes and ensuring timely product delivery.
What is your experience with regulatory compliance in manufacturing, such as OSHA or ISO standards?
How to Answer
- 1
Identify specific regulations you have worked with
- 2
Discuss your role in ensuring compliance
- 3
Mention any training or certifications related to compliance
- 4
Provide examples of successful audits or inspections
- 5
Highlight improvements made under compliance guidelines
Example Answers
During my time at XYZ Corp, I managed ISO 9001 compliance, ensuring our processes met quality standards through regular audits and staff training.
Explain how material properties can affect manufacturing processes and product quality.
How to Answer
- 1
Identify key material properties like hardness, ductility, and thermal conductivity.
- 2
Explain how each property influences a specific manufacturing process.
- 3
Discuss the impact of these properties on the final product quality.
- 4
Use real-world examples to illustrate your points.
- 5
Keep your answer structured: start with properties, then processes, then quality.
Example Answers
Material properties such as hardness and ductility significantly affect manufacturing processes. For example, hard materials may require more robust machining methods, while ductile materials are easier to form. This influences the final product's strength and durability.
Good Candidates Answer Questions. Great Ones Win Offers.
Reading sample answers isn't enough. Top candidates practice speaking with confidence and clarity. Get real feedback, improve faster, and walk into your next interview ready to stand out.
Master your interview answers under pressure
Boost your confidence with real-time practice
Speak clearly and impress hiring managers
Get hired faster with focused preparation
Used by hundreds of successful candidates
Situational Interview Questions
Suppose you are tasked with reducing cycle time for a high-volume manufacturing line. How would you approach this challenge?
How to Answer
- 1
Analyze the current cycle time data to identify bottlenecks
- 2
Engage with operators to gather insights on workflow inefficiencies
- 3
Evaluate equipment setup and maintenance schedules for potential improvements
- 4
Implement process automation where feasible to reduce manual efforts
- 5
Test and iterate changes, measuring impact on cycle time with continuous feedback
Example Answers
To reduce cycle time, I would start by analyzing our time studies to pinpoint the biggest bottlenecks. After identifying these areas, I would talk with the operators to understand their challenges. Implementing minor adjustments and perhaps some automation could streamline the process, which I would continuously measure for effectiveness.
If a critical piece of manufacturing equipment fails, how would you prioritize repairs and manage production interruptions?
How to Answer
- 1
Assess the impact of the equipment failure on production schedules and output.
- 2
Identify the key stakeholders and communicate the situation and potential delays.
- 3
Prioritize repairs based on equipment importance and availability of spare parts.
- 4
Implement temporary workarounds or alternative processes to minimize downtime.
- 5
Monitor the situation closely and adjust plans as repairs progress or new information arises.
Example Answers
In case of equipment failure, I would first determine how it affects production and communicate with my team and management about the expected delays. Then, I would prioritize repairs based on the importance of the equipment and the availability of parts, possibly implementing temporary measures to keep production flowing.
Good Candidates Answer Questions. Great Ones Win Offers.
Reading sample answers isn't enough. Top candidates practice speaking with confidence and clarity. Get real feedback, improve faster, and walk into your next interview ready to stand out.
Master your interview answers under pressure
Boost your confidence with real-time practice
Speak clearly and impress hiring managers
Get hired faster with focused preparation
Used by hundreds of successful candidates
Imagine you need to introduce a new manufacturing process. What steps would you take to ensure successful implementation?
How to Answer
- 1
Conduct a thorough needs assessment to understand the requirements of the new process.
- 2
Engage stakeholders early to gather input and address concerns.
- 3
Develop a clear project plan outlining timelines, responsibilities, and resources.
- 4
Pilot the new process in a controlled environment to identify issues before full implementation.
- 5
Gather feedback post-implementation and make necessary adjustments.
Example Answers
First, I would assess the current manufacturing capabilities and identify specific needs for the new process. Then, I would involve stakeholders like team leaders and operators to get their insights and ensure buy-in. After that, I would create a detailed project plan with timelines. Next, I would run a pilot program to test the process on a smaller scale before rolling it out completely. Finally, I'd solicit feedback from the team to refine the process based on real-world experiences.
If the company requires a 10% reduction in manufacturing costs, what strategies would you propose?
How to Answer
- 1
Identify key cost drivers in the manufacturing process.
- 2
Propose lean manufacturing techniques to eliminate waste.
- 3
Suggest automation or technology upgrades for efficiency.
- 4
Explore supplier negotiation for better material costs.
- 5
Encourage cross-training of employees to maximize workforce flexibility.
Example Answers
To achieve a 10% reduction in costs, I would first analyze the key cost drivers within the manufacturing process. Employing lean manufacturing principles would help us identify and eliminate waste. Additionally, I would consider investing in automation technologies that can increase efficiency and reduce labor costs over time.
You discover a recurring defect in one of the product lines. How would you investigate and rectify the issue?
How to Answer
- 1
Identify the specific nature of the defect and gather data on its occurrence.
- 2
Analyze the production process and identify potential causes of the defect.
- 3
Consult with team members and operators for insights and historical context.
- 4
Implement a test plan to verify potential solutions and monitor effects.
- 5
Document findings and standardize improvements to prevent future issues.
Example Answers
I would first review the defect reports to quantify how often the defect occurs and under what conditions. Then, I'd analyze the production line for any steps where errors may originate. I would collaborate with operators to gather insights on their experiences with the defect. After narrowing down potential causes, I'd test changes to the process and monitor results to ensure the defect is eliminated.
You are in a situation where two of your team members disagree on the best approach to a process improvement. How would you handle this?
How to Answer
- 1
Listen carefully to both team members' perspectives.
- 2
Encourage open dialogue to explore each approach's pros and cons.
- 3
Assess the impact of each approach on process efficiency and team goals.
- 4
Facilitate a discussion to find common ground or a combined solution.
- 5
If needed, involve a third party for additional insights or mediation.
Example Answers
I would start by listening to both team members to understand their viewpoints. Then, I would facilitate a discussion where they can express their pros and cons, guiding them to find a common ground or a compromise that incorporates the best of both ideas.
If you notice that inventory levels are consistently too high, what steps would you take to address this issue?
How to Answer
- 1
Analyze inventory data to identify patterns and causes of excess stock
- 2
Engage with supply chain and production teams to understand demand forecasts
- 3
Implement Just-In-Time (JIT) principles to align inventory levels with demand
- 4
Review procurement processes to reduce ordering frequency or adjust order sizes
- 5
Propose cycle counting to maintain accurate inventory records
Example Answers
I would start by analyzing inventory data to pinpoint why levels are high, then collaborate with production and sales teams to understand customer demand. By implementing JIT, we can minimize excess stock while meeting demand reliably.
You're asked to train staff on a new process. How would you ensure that the training is effective and well-received?
How to Answer
- 1
Understand the existing knowledge and skill level of the staff.
- 2
Use a hands-on approach with demonstrations and real-life examples.
- 3
Encourage questions and provide clear answers throughout the training.
- 4
Collect feedback during and after the training to adjust methods as needed.
- 5
Follow up with additional resources and check-ins to reinforce learning.
Example Answers
I would start by assessing the current skill levels of the staff to tailor the training material. Then, I'd use hands-on demonstrations to show the new process and encourage questions to clarify doubts. After the training, I would gather feedback and check in with the team to ensure they feel comfortable with the new procedures.
A manufacturing process fails unexpectedly, delaying production. What immediate actions would you take to mitigate the impact?
How to Answer
- 1
Assess the situation to identify the cause of the failure
- 2
Communicate with the team to inform them of the issue
- 3
Implement a temporary workaround to resume production
- 4
Prioritize critical components to minimize overall impact
- 5
Document the incident for future analysis and improvement
Example Answers
First, I would quickly assess the cause of the manufacturing failure by gathering data from the process and speaking with the operators involved. Then, I'd inform the team and stakeholders about the issue to keep everyone aligned. If possible, I would implement a temporary workaround to resume production until the main issue can be resolved. Finally, I'd document the incident thoroughly to identify lessons learned and avoid similar issues in the future.
You need to coordinate with the R&D department on implementing a new process. How would you facilitate effective collaboration?
How to Answer
- 1
Establish clear communication channels between teams
- 2
Set up regular meetings to discuss progress and challenges
- 3
Define roles and responsibilities of each team member
- 4
Share relevant data and insights transparently
- 5
Encourage feedback and active participation from R&D personnel
Example Answers
I would first set up a weekly meeting with the R&D team to check in on the project and discuss any challenges. Clear channels like shared documents would ensure everyone has access to the same information.
Good Candidates Answer Questions. Great Ones Win Offers.
Reading sample answers isn't enough. Top candidates practice speaking with confidence and clarity. Get real feedback, improve faster, and walk into your next interview ready to stand out.
Master your interview answers under pressure
Boost your confidence with real-time practice
Speak clearly and impress hiring managers
Get hired faster with focused preparation
Used by hundreds of successful candidates
Manufacturing Process Engineer Position Details
Salary Information
Recommended Job Boards
These job boards are ranked by relevance for this position.
Related Positions
Good Candidates Answer Questions. Great Ones Win Offers.
Master your interview answers under pressure
Boost your confidence with real-time practice
Speak clearly and impress hiring managers
Get hired faster with focused preparation
Used by hundreds of successful candidates
Good Candidates Answer Questions. Great Ones Win Offers.
Master your interview answers under pressure
Boost your confidence with real-time practice
Speak clearly and impress hiring managers
Get hired faster with focused preparation
Used by hundreds of successful candidates