Top 32 Pharmaceutical Operator Interview Questions and Answers [Updated 2025]
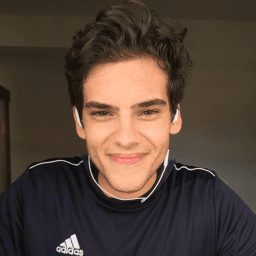
Andre Mendes
•
March 30, 2025
Navigating a pharmaceutical operator interview can be daunting, but preparation is key to success. This blog post compiles the most common interview questions for the role, providing not only example answers but also insightful tips to help you respond effectively. Whether you're a seasoned professional or a newcomer to the industry, dive in to boost your confidence and enhance your interview performance.
Download Pharmaceutical Operator Interview Questions in PDF
To make your preparation even more convenient, we've compiled all these top Pharmaceutical Operatorinterview questions and answers into a handy PDF.
Click the button below to download the PDF and have easy access to these essential questions anytime, anywhere:
List of Pharmaceutical Operator Interview Questions
Behavioral Interview Questions
Tell me about a time you had to adapt to a significant change in procedures or systems in your workplace.
How to Answer
- 1
Choose a specific example that showcases your adaptability.
- 2
Explain the context and the change that occurred.
- 3
Describe your immediate response to the change.
- 4
Highlight the steps you took to adapt effectively.
- 5
Conclude with the positive outcome or what you learned.
Example Answers
In my previous role, the company implemented a new inventory management system. Initially, I was unsure about the new software, but I took the initiative to attend training sessions. I also spent extra hours practicing the system. As a result, I was able to help my team transition smoothly and improve our inventory accuracy by 30%.
Can you describe a time when you worked as part of a team to solve a problem in a pharmaceutical setting?
How to Answer
- 1
Identify a specific problem you faced while working in a team.
- 2
Describe your role in the team and the actions you took.
- 3
Highlight the collaborative aspect and how team members contributed.
- 4
Explain the outcome and what you learned from the experience.
- 5
Make sure it relates directly to pharmaceutical operations.
Example Answers
In my previous role at XYZ Pharmaceuticals, our team faced a production delay due to equipment failure. I was responsible for coordinating with the maintenance team and communicating with production staff. We held a quick meeting to brainstorm solutions and decided to implement a temporary workaround while we scheduled repairs. This collaboration helped us resume production within 24 hours, minimizing downtime.
Don't Just Read Pharmaceutical Operator Questions - Practice Answering Them!
Reading helps, but actual practice is what gets you hired. Our AI feedback system helps you improve your Pharmaceutical Operator interview answers in real-time.
Personalized feedback
Unlimited practice
Used by hundreds of successful candidates
Describe a situation where you had to prioritize safety in the workplace. What actions did you take?
How to Answer
- 1
Identify a specific incident where safety was at risk.
- 2
Explain the steps you took to ensure safety.
- 3
Discuss the outcome and any lessons learned.
- 4
Emphasize the importance of safety protocols.
- 5
Mention how you communicated with the team about safety.
Example Answers
In my previous role, we noticed a chemical spill in the lab. I immediately informed my supervisor and activated the emergency response procedure. We cordoned off the area, evacuated non-essential personnel, and wore appropriate PPE to clean it up safely. As a result, we prevented any injuries and reviewed our spill response protocol afterward.
Have you ever had a conflict with a colleague regarding production processes? How did you resolve it?
How to Answer
- 1
Stay calm and professional when discussing the conflict
- 2
Focus on a specific example that illustrates the issue clearly
- 3
Explain the steps you took to address the conflict
- 4
Highlight the importance of communication and collaboration
- 5
Mention the positive outcome or what you learned from the experience
Example Answers
In one instance, I disagreed with a colleague about the best way to adjust machine settings. I requested a meeting to openly discuss our viewpoints. We laid out our reasoning and eventually agreed to test both methods, leading to an optimized process that improved production efficiency.
Can you provide an example of when you took the initiative to lead a project or task in your previous role?
How to Answer
- 1
Identify a specific project where you took the lead.
- 2
Explain your role and the initiative you took.
- 3
Describe the impact or results of your leadership.
- 4
Use metrics or outcomes to quantify your success.
- 5
Reflect on what you learned from the experience.
Example Answers
In my last role, I noticed that our inventory management was causing delays in production. I took the initiative to streamline the process by implementing a new tracking system, which improved our efficiency by 20% and reduced stock-outs.
Tell me about a time when you identified a quality issue in production. How did you handle it?
How to Answer
- 1
Start with a specific situation and set the context of the quality issue.
- 2
Explain the steps you took to identify the issue and its impact.
- 3
Describe how you communicated the issue to your team or supervisor.
- 4
Detail the corrective actions you implemented to resolve the issue.
- 5
Conclude with the results of your actions and any lessons learned.
Example Answers
In my previous role, I noticed that the batch consistency of a product was off during routine checks. I compared samples and identified that a specific machine was miscalibrated. I immediately informed my supervisor and led a team to recalibrate the machine. After adjustments, we tested the samples again, achieving the correct consistency. This not only resolved the issue but also improved overall production efficiency.
Describe an experience where you had to train a new team member on pharmaceutical processes. How did you ensure their understanding?
How to Answer
- 1
Start with a brief overview of the situation and the new team member's role.
- 2
Explain the training methods you used, such as hands-on training or shadowing.
- 3
Highlight how you assessed their understanding during the training.
- 4
Mention any resources or materials you provided for additional support.
- 5
Conclude with the outcomes of their training and any follow-up actions taken.
Example Answers
I trained a new operator who joined our team last summer. I started with a detailed orientation session and then had them shadow me during shifts. I provided a checklist of key processes and followed up with quizzes to assess their understanding. After two weeks, they confidently handled the tasks independently, which improved overall team efficiency.
Can you discuss a time when you received constructive feedback? How did you implement it?
How to Answer
- 1
Choose a specific example from your past work experience.
- 2
Describe the feedback clearly and how it was given to you.
- 3
Explain how you reacted to the feedback initially.
- 4
Detail the steps you took to implement the feedback in your work.
- 5
Conclude with the positive outcomes that resulted from making the changes.
Example Answers
In my previous role as a pharmaceutical technician, I received feedback from my supervisor that my documentation needed to be more detailed. I initially felt defensive but understood the importance of accurate records. I attended a training on documentation standards and revised my approach. As a result, my accuracy rate in compliance audits improved significantly.
Describe a proactive approach you have taken to improve safety or efficiency in your previous roles.
How to Answer
- 1
Highlight a specific problem you identified related to safety or efficiency.
- 2
Describe the steps you took to address the issue proactively.
- 3
Mention any collaborative efforts or teamwork involved.
- 4
Provide measurable results or positive outcomes from your actions.
- 5
Reflect on what you learned and how it impacted future practices.
Example Answers
In my last role as a pharmaceutical operator, I noticed that our equipment was often down for maintenance, leading to production delays. I took the initiative to implement a preventive maintenance schedule that involved daily checks and weekly reports. This reduced downtime by 30% over six months, improving our efficiency significantly.
Technical Interview Questions
What types of pharmaceutical production equipment are you familiar with? Describe your experience with them.
How to Answer
- 1
List specific equipment you have worked with.
- 2
Describe your role and responsibilities with each type of equipment.
- 3
Mention any relevant training or certifications you have.
- 4
Highlight any improvements or successes you achieved with the equipment.
- 5
Be prepared to discuss safety protocols related to the equipment.
Example Answers
I am familiar with tablet press machines and granulators. In my last position, I operated the tablet press, ensuring all settings were properly calibrated. I also completed a training course on GMP standards, which helped me maintain quality during production.
What regulatory compliance standards are crucial for pharmaceutical manufacturing and how do you ensure adherence to them?
How to Answer
- 1
Identify key standards like cGMP and ICH guidelines.
- 2
Mention specific protocols you follow for compliance.
- 3
Discuss your experience with audits and inspections.
- 4
Emphasize the importance of training and documentation.
- 5
Provide examples of how you resolve compliance issues.
Example Answers
Key compliance standards in pharmaceutical manufacturing include cGMP and ICH guidelines. I ensure adherence by conducting regular training for staff, maintaining thorough documentation, and performing internal audits. For example, I recently led a training session on cGMP principles which significantly improved our compliance ratings during the last audit.
Don't Just Read Pharmaceutical Operator Questions - Practice Answering Them!
Reading helps, but actual practice is what gets you hired. Our AI feedback system helps you improve your Pharmaceutical Operator interview answers in real-time.
Personalized feedback
Unlimited practice
Used by hundreds of successful candidates
Explain the step-by-step process you follow for the preparation and handling of pharmaceutical products.
How to Answer
- 1
Start by discussing the importance of adhering to standard operating procedures.
- 2
Outline the initial steps including planning and ensuring the workspace is clean and organized.
- 3
Explain how you measure and prepare ingredients accurately.
- 4
Detail the mixing and processing steps you follow for formulation.
- 5
Conclude with the importance of quality control and documentation.
Example Answers
I begin by following the standard operating procedures carefully to ensure compliance. I prepare my workspace by sanitizing surfaces and gathering all necessary materials. Then, I accurately measure and prepare the active ingredients. Next, I mix the components according to the formulation guidelines, ensuring even distribution. Finally, I conduct quality checks and document all stages to maintain traceability.
How do you ensure accurate documentation in line with good manufacturing practices?
How to Answer
- 1
Follow standard operating procedures closely at all times.
- 2
Double-check entries for accuracy and completeness before submission.
- 3
Use clear and legible handwriting or electronic systems for documentation.
- 4
Date and sign all documents to indicate who completed the entry.
- 5
Seek clarification if unsure about any documentation requirements.
Example Answers
I ensure accurate documentation by strictly following our SOPs and reviewing my work multiple times for errors before finalizing any documents.
Can you walk us through your troubleshooting process for equipment malfunctions during production?
How to Answer
- 1
Start by identifying symptoms of the malfunction.
- 2
Check equipment logs for any error codes or warnings.
- 3
Follow a systematic approach, isolating each component if necessary.
- 4
Consult the operation manual or troubleshooting guide for solutions.
- 5
Communicate any findings and actions taken to the team.
Example Answers
When troubleshooting equipment malfunctions, I first identify the symptoms such as unusual sounds or error messages. Then, I check the logs for any error codes. I isolate components if needed and refer to the troubleshooting manual. I also ensure to communicate all findings to my team and seek their input if necessary.
What experience do you have with formulation processes, and how do you ensure the consistency of the products?
How to Answer
- 1
Mention specific formulation processes you have worked on.
- 2
Describe how you measure and test for consistency.
- 3
Include any relevant tools or technologies you have used.
- 4
Discuss your experience with regulatory compliance in formulations.
- 5
Share an example of a challenge you faced and how you resolved it.
Example Answers
I have three years of experience in tablet formulation, where I utilized wet granulation techniques. I ensure consistency by implementing in-process controls and performing regular testing using HPLC. I also use SOPs aligned with GMP standards to maintain quality throughout production.
What methods of sterilization are you familiar with, and how do you apply them in your work?
How to Answer
- 1
List specific sterilization methods you have used, such as autoclaving, chemical sterilization, or radiation.
- 2
Explain how you implement these methods in your daily work processes.
- 3
Mention the importance of following standard operating procedures for sterilization.
- 4
Provide an example of a situation where sterilization was critical to your work.
- 5
Emphasize your understanding of the microbiological principles behind sterilization.
Example Answers
I am familiar with autoclaving and chemical sterilization. In my previous role, I regularly used autoclaving for equipment and glassware to ensure a sterile environment. I strictly followed SOPs to minimize contamination risks.
How do you assess the quality of raw materials before they are used in production?
How to Answer
- 1
Review the supplier's certificates of analysis.
- 2
Conduct visual inspections for any defects or contamination.
- 3
Perform preliminary tests for key quality attributes.
- 4
Ensure all materials meet regulatory and company specifications.
- 5
Keep accurate records of quality assessments for traceability.
Example Answers
I assess the quality of raw materials by first reviewing the supplier's certificates of analysis to verify compliance. Next, I conduct visual inspections to check for any defects or contamination and perform preliminary tests to ensure they meet our specifications.
What safety protocols do you follow when working with hazardous materials?
How to Answer
- 1
Always wear appropriate personal protective equipment (PPE) such as gloves, goggles, and masks.
- 2
Follow the Material Safety Data Sheets (MSDS) for all substances to understand risks and handling procedures.
- 3
Utilize fume hoods or other containment devices when working with volatile substances.
- 4
Regularly participate in safety training sessions to stay updated on protocols and emergency procedures.
- 5
Report any spills or incidents immediately and follow the established emergency protocols.
Example Answers
I always wear the required PPE, including gloves and goggles, and I ensure that I understand the MSDS for any hazardous materials I handle.
What challenges do you anticipate when scaling up a production process from pilot to full scale?
How to Answer
- 1
Identify potential technical challenges specific to the production equipment or process.
- 2
Consider variances in raw material quality and supply during scale up.
- 3
Address the need for enhanced quality control measures to meet regulatory requirements.
- 4
Anticipate workforce training and operational consistency issues with larger teams.
- 5
Plan for increased cost management and resource allocation during scale up.
Example Answers
One challenge I anticipate is ensuring that the equipment operates efficiently at a larger scale, as scaling up may expose limitations not seen during pilot tests. I'm also aware that sourcing raw materials could be more difficult, so I would work closely with suppliers to ensure consistency.
Don't Just Read Pharmaceutical Operator Questions - Practice Answering Them!
Reading helps, but actual practice is what gets you hired. Our AI feedback system helps you improve your Pharmaceutical Operator interview answers in real-time.
Personalized feedback
Unlimited practice
Used by hundreds of successful candidates
How do you utilize data analysis in monitoring production efficiency and effectiveness?
How to Answer
- 1
Identify key performance indicators (KPIs) relevant to production efficiency.
- 2
Use statistical tools to analyze production data and identify trends.
- 3
Implement regular reporting to track data over time and compare against targets.
- 4
Utilize root cause analysis when production metrics fall below expectations.
- 5
Collaborate with engineering and quality control to interpret data findings.
Example Answers
I monitor production efficiency by analyzing KPIs such as yield rates and cycle times. I use statistical software to track these metrics and create reports that highlight trends, which helps identify areas for improvement.
What experience do you have with process validation in pharmaceutical manufacturing?
How to Answer
- 1
Discuss specific projects you have worked on.
- 2
Highlight your role and responsibilities in the validation process.
- 3
Mention the types of validations (prospective, concurrent, retrospective) you've performed.
- 4
Include any relevant regulations or guidelines you followed.
- 5
Share outcomes or improvements resulting from your validation efforts.
Example Answers
In my previous role, I conducted process validation for a new oral solid dosage form. I led the prospective validation, following FDA guidelines and ensuring compliance with cGMP. My efforts resulted in a 15% reduction in production downtime.
What precautions and techniques do you use when handling potent chemical substances in production?
How to Answer
- 1
Always wear the appropriate personal protective equipment such as gloves, goggles, and lab coats.
- 2
Ensure proper ventilation in the workspace to minimize inhalation risks.
- 3
Follow standard operating procedures for handling potent chemicals and review safety data sheets.
- 4
Use containment systems like fume hoods or glove boxes to isolate hazardous substances.
- 5
Regularly attend safety training and drills to stay updated on best practices.
Example Answers
I always wear gloves and goggles when handling potent chemicals, and I make sure the workspace is well-ventilated. I strictly follow the SOPs and routinely review the safety data sheets for the chemicals I’m dealing with.
Situational Interview Questions
If you notice that a team member is not following safety protocols, how would you approach them?
How to Answer
- 1
Address the issue promptly but calmly.
- 2
Use a private setting to avoid embarrassment.
- 3
Be specific about which safety protocol was not followed.
- 4
Encourage dialogue by asking for their perspective.
- 5
Offer support for correcting the behavior.
Example Answers
I would approach the team member privately and say, 'I noticed you didn't wear your safety goggles while handling chemicals. Can we discuss this?' Then, I would listen to their side and offer help if they have questions about the protocols.
Imagine you are facing a tight deadline for production. How would you manage your time and resources to meet this deadline?
How to Answer
- 1
Assess the production schedule and identify critical tasks
- 2
Prioritize tasks based on urgency and importance
- 3
Communicate clearly with the team to allocate resources effectively
- 4
Monitor progress continuously and be flexible to adapt as needed
- 5
Use time management tools to keep track and stay organized
Example Answers
I would first review the production schedule to identify which tasks are critical and need immediate attention. I'd then prioritize these tasks and delegate responsibilities based on each team member's strengths, ensuring everyone knows their role and deadlines. Regular check-ins would help us stay on track and adjust if any issues arise.
Don't Just Read Pharmaceutical Operator Questions - Practice Answering Them!
Reading helps, but actual practice is what gets you hired. Our AI feedback system helps you improve your Pharmaceutical Operator interview answers in real-time.
Personalized feedback
Unlimited practice
Used by hundreds of successful candidates
If an unexpected issue arises during a production run, what steps would you take to assess and address the problem?
How to Answer
- 1
Remain calm and assess the situation quickly.
- 2
Gather data from the production monitoring system.
- 3
Identify the root cause by isolating variables.
- 4
Communicate the issue to the team and management.
- 5
Implement corrective actions and document the process.
Example Answers
First, I would remain calm and quickly assess the situation to understand the scope of the issue. Then, I would gather data from our production monitoring systems to pinpoint any anomalies. After identifying potential causes, I would communicate with the team about our findings and decide on corrective actions, ensuring everything is documented for future reference.
What would you do if you discovered that a batch of products did not meet quality standards after production?
How to Answer
- 1
Immediately report the issue to your supervisor or quality control team
- 2
Document all relevant details about the batch and the quality issues found
- 3
Follow protocols for quarantining the affected batch to prevent distribution
- 4
Assist in investigating the cause of the quality failure to prevent recurrence
- 5
Communicate transparently with stakeholders about the quality issue
Example Answers
If I found a batch that didn't meet quality standards, I would first report it to my supervisor and document the details. Then, I would ensure the batch was quarantined to stop it from being distributed, and I would collaborate with the quality control team to investigate the cause of the issue.
How would you communicate a production issue to your supervisor and recommend a solution?
How to Answer
- 1
Clearly state the issue with specific details.
- 2
Explain the impact of the issue on production.
- 3
Propose a straightforward solution based on facts.
- 4
Be ready to discuss alternative solutions if necessary.
- 5
Maintain a professional and solution-oriented approach.
Example Answers
I would first outline the production issue by noting that we are experiencing a delay due to a faulty piece of equipment. This delay has resulted in a 20% drop in our output. I would recommend that we schedule immediate maintenance on the equipment to resolve the issue quickly.
If you were tasked with improving an existing production process, what steps would you take to identify areas for enhancement?
How to Answer
- 1
Conduct an analysis of current metrics and performance data
- 2
Engage with operators to gather insights on challenges they face
- 3
Perform a value stream mapping to visualize the process flow
- 4
Identify bottlenecks and areas of waste in the production line
- 5
Research best practices and solutions used in similar environments
Example Answers
I would start by analyzing production data to identify trends and inefficiencies. Then, I would hold discussions with operators to understand their firsthand experiences. By mapping out the entire production process, I could visualize where delays or waste occur and prioritize those areas for improvement.
If you were responsible for identifying potential hazards in your work environment, how would you proceed?
How to Answer
- 1
Start with a thorough visual inspection of the area.
- 2
Consult safety data sheets for chemicals and materials used.
- 3
Engage with coworkers to gather insights on existing hazards.
- 4
Use checklists based on industry standards for systematic evaluation.
- 5
Document all findings and report them to management for action.
Example Answers
I would begin with a visual inspection of the work environment, looking for any obvious hazards. I would also refer to the safety data sheets for any chemicals we use to understand their risks better. Additionally, I would speak with my colleagues to learn about any hazards they have encountered.
How would you handle a situation where you had to work with limited resources to complete a project?
How to Answer
- 1
Assess the available resources to understand what you have to work with
- 2
Prioritize tasks to focus on what is most critical for project completion
- 3
Consider creative solutions or alternative methods to achieve project goals
- 4
Communicate openly with your team and stakeholders about constraints
- 5
Stay flexible and ready to adapt your plan as needed based on resource availability
Example Answers
In a previous role, I faced a shortage of materials. I assessed what we had and prioritized the critical portions of the project, using alternative materials where possible. I ensured to communicate our progress and constraints to the team, which helped us stay aligned and deliver on time.
If a teammate was struggling with their workload, how would you offer support without overstepping?
How to Answer
- 1
Observe their workload to understand the issue.
- 2
Approach them privately to offer assistance.
- 3
Ask open-ended questions to gauge their needs.
- 4
Offer specific help rather than a general offer.
- 5
Respect their autonomy and let them guide the conversation.
Example Answers
I would start by noticing if their workload seems overwhelming. Then, I’d approach them privately and say, 'I’ve noticed you have a lot on your plate, is there something specific I can help with?' This way, I offer support while giving them space to respond.
If you noticed unethical behavior in the production line, what steps would you take?
How to Answer
- 1
Stay calm and observe the behavior carefully.
- 2
Document the details of the unethical behavior.
- 3
Report the incident to your supervisor immediately.
- 4
Follow company procedures for reporting unethical behavior.
- 5
Avoid discussing the incident with colleagues until reported.
Example Answers
I would first observe the unethical behavior carefully to ensure that I understand what is happening. Then, I would document everything I witnessed. After that, I would report the issue to my supervisor following our protocols to ensure it is addressed properly.
Don't Just Read Pharmaceutical Operator Questions - Practice Answering Them!
Reading helps, but actual practice is what gets you hired. Our AI feedback system helps you improve your Pharmaceutical Operator interview answers in real-time.
Personalized feedback
Unlimited practice
Used by hundreds of successful candidates
Pharmaceutical Operator Position Details
Recommended Job Boards
CareerBuilder
www.careerbuilder.com/jobs/pharmaceutical-operatorThese job boards are ranked by relevance for this position.
Related Positions
- Pill Maker
- Chemical Worker
- Refinery Operator
- Bag Machine Operator
- Chemical Maker
- Turning Machine Operator
- Flexographic Press Operator
- Utility Operator
- Extruder Operator
- Chemical Compounder
Similar positions you might be interested in.
Ace Your Next Interview!
Practice with AI feedback & get hired faster
Personalized feedback
Used by hundreds of successful candidates
Ace Your Next Interview!
Practice with AI feedback & get hired faster
Personalized feedback
Used by hundreds of successful candidates