Top 30 Process Engineering Technician Interview Questions and Answers [Updated 2025]
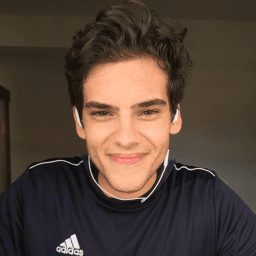
Andre Mendes
•
March 30, 2025
Navigating the competitive landscape of process engineering technician interviews demands thorough preparation and confidence. In this blog post, you'll discover the most common interview questions tailored for this dynamic role, along with insightful example answers and effective answering strategies. Whether you're a seasoned professional or a newcomer, these curated tips and responses will equip you to leave a lasting impression and boost your chances of success.
Download Process Engineering Technician Interview Questions in PDF
To make your preparation even more convenient, we've compiled all these top Process Engineering Technicianinterview questions and answers into a handy PDF.
Click the button below to download the PDF and have easy access to these essential questions anytime, anywhere:
List of Process Engineering Technician Interview Questions
Behavioral Interview Questions
Describe a time when you identified a bottleneck in a process and how you resolved it.
How to Answer
- 1
Think of a specific example from your previous work experience.
- 2
Clearly define what the bottleneck was and how you identified it.
- 3
Explain the steps you took to analyze the bottleneck.
- 4
Describe the solution you implemented and its impact.
- 5
Focus on quantifiable results if possible to show effectiveness.
Example Answers
In my previous job, I noticed that our assembly line was slowing down significantly during shift changes. I tracked the process and found that workers were not receiving adequate training on the new equipment. I organized a quick training session to address their concerns, and we reduced downtime by 30%.
Can you provide an example of a time you worked closely with a team to improve a process?
How to Answer
- 1
Choose a specific project or task.
- 2
Describe your role and contributions clearly.
- 3
Highlight the team collaboration aspect.
- 4
Include the outcome or improvements achieved.
- 5
Use metrics or concrete results if possible.
Example Answers
In my previous role, I was part of a team tasked with reducing production downtime. I suggested implementing a new scheduling process and worked with my colleagues to develop a shared calendar system. As a result, we reduced downtime by 20% over three months.
Don't Just Read Process Engineering Technician Questions - Practice Answering Them!
Reading helps, but actual practice is what gets you hired. Our AI feedback system helps you improve your Process Engineering Technician interview answers in real-time.
Personalized feedback
Unlimited practice
Used by hundreds of successful candidates
Give an example of a process improvement you initiated that led to significant savings or efficiency gains.
How to Answer
- 1
Identify a specific process you improved.
- 2
Describe the problem or inefficiency clearly.
- 3
Explain the steps you took to implement the improvement.
- 4
Quantify the results, such as time saved or cost reduced.
- 5
Highlight any team collaboration or support received.
Example Answers
I noticed our material handling process took too long, so I implemented a new layout that reduced travel distance. This saved us two hours per shift, leading to a cost reduction of $5,000 monthly.
Describe a situation where you had a disagreement with a colleague about a process change and how you resolved it.
How to Answer
- 1
Choose a specific example with clear context
- 2
Explain the differing opinions without naming names
- 3
Focus on your role in the resolution process
- 4
Highlight collaboration and compromise
- 5
Conclude with the positive outcome and what you learned
Example Answers
In a previous job, a colleague suggested a new workflow that I felt would slow down production. I arranged a meeting to discuss our perspectives. We identified the main concerns and compromises, such as trialing the new process on a small scale. The pilot was successful, and we learned to balance innovation with efficiency.
Tell me about a time you had to quickly adapt to a change in the process you were managing.
How to Answer
- 1
Describe the process change clearly and briefly.
- 2
Explain the impact of the change on your work and the team.
- 3
Discuss how you assessed the situation and decided on your response.
- 4
Highlight the actions you took to adapt to the change.
- 5
Mention the results of your actions and any lessons learned.
Example Answers
In my last role, we had an unexpected change in the production schedule due to a supplier delay. I communicated quickly with my team to assess how this affected our current workflow. By reallocating resources and adjusting priorities, we maintained our output without compromising quality. This taught me the importance of flexibility and teamwork in adapting to process changes.
Give an example of how you effectively communicated a complex process change to non-technical staff.
How to Answer
- 1
Identify a specific process change you communicated.
- 2
Explain your audience's background and their potential concerns.
- 3
Describe the methods you used to simplify the information.
- 4
Highlight any feedback mechanisms you used to ensure understanding.
- 5
Share the outcome of the communication and its impact.
Example Answers
In my previous job, we introduced a new inventory management software. I organized a workshop for the sales team, where I used simple visuals and avoided technical jargon. I provided handouts summarizing key changes and encouraged questions. After the session, I followed up with a survey to assess their understanding, which indicated a positive response and improved efficiency in their processes.
Provide an example of a time you led a process improvement project and the outcome.
How to Answer
- 1
Choose a specific project relevant to process improvement.
- 2
Explain your role and leadership in the project.
- 3
Describe the challenges faced during the project.
- 4
Outline the steps you took to implement improvements.
- 5
Share measurable outcomes that resulted from the project.
Example Answers
In my last position, I led a project to reduce cycle time in our manufacturing process. My role involved mapping the current process and identifying bottlenecks. We faced challenges with team resistance, but I facilitated workshops to gather input and buy-in. Ultimately, we reduced cycle time by 20%, leading to a significant increase in productivity.
Can you describe a situation where you had to learn a new technology or process quickly?
How to Answer
- 1
Choose a specific technology or process you learned.
- 2
Explain the context or reason for learning it quickly.
- 3
Describe the steps you took to learn it effectively.
- 4
Mention any resources or support you utilized.
- 5
Share the outcome or how it improved your work.
Example Answers
In my last job, we needed to implement a new software for inventory management on short notice. I quickly enrolled in an online training course and studied the software's manual. I also reached out to a colleague who was familiar with it for tips. Within a week, I was able to train my team and enhance our inventory tracking significantly.
Tell me about a difficult decision you had to make in optimizing a process and the factors that influenced your choice.
How to Answer
- 1
Select a specific process and a clear challenge you faced.
- 2
Discuss the data or feedback you analyzed that influenced your decision.
- 3
Mention the outcome of your decision and how it improved the process.
- 4
Highlight any team collaboration or communication involved.
- 5
Reflect on what you learned from the experience.
Example Answers
In my previous role, we faced inefficiencies in a production line causing delays. I analyzed throughput data and discovered that equipment downtime was a major factor. I proposed a preventive maintenance schedule, which required balancing production runs. After implementing this, we reduced downtime by 30%, significantly boosting productivity.
Describe how you manage your time and prioritize tasks in a fast-paced environment.
How to Answer
- 1
Identify urgent and important tasks first using a priority matrix.
- 2
Use a digital task management tool to keep track of duties.
- 3
Set specific time blocks for deep work and minimize distractions.
- 4
Regularly review your task list and adjust priorities as needed.
- 5
Communicate with your team about expectations and deadlines.
Example Answers
I prioritize tasks by first identifying what is urgent and important with a priority matrix. I use a task management app to organize my work. I set aside dedicated time for complex tasks and keep distractions to a minimum.
Don't Just Read Process Engineering Technician Questions - Practice Answering Them!
Reading helps, but actual practice is what gets you hired. Our AI feedback system helps you improve your Process Engineering Technician interview answers in real-time.
Personalized feedback
Unlimited practice
Used by hundreds of successful candidates
Technical Interview Questions
What methods do you use to evaluate the efficiency of a process?
How to Answer
- 1
Identify key performance indicators that measure process efficiency.
- 2
Use data analysis techniques to assess current process performance.
- 3
Apply methods like Six Sigma or Lean to identify waste and improve efficiency.
- 4
Conduct regular process audits to gather insights and track improvements.
- 5
Benchmark against industry standards to understand where your process stands.
Example Answers
I evaluate process efficiency by tracking key performance indicators such as cycle time and yield. I use data analysis tools like Pareto charts to identify bottlenecks, and I implement Lean techniques to eliminate waste and streamline operations.
What types of data analysis have you performed to support process improvement initiatives?
How to Answer
- 1
Identify specific tools or methods you've used for analysis.
- 2
Mention any data sets or metrics you worked with.
- 3
Describe a concrete example of a project or initiative.
- 4
Highlight the results or improvements achieved.
- 5
Emphasize teamwork or collaboration in your analysis process.
Example Answers
In my last role, I performed statistical analysis using Minitab to identify process inefficiencies. I focused on cycle time data and discovered a bottleneck that, once addressed, improved overall throughput by 20%.
Don't Just Read Process Engineering Technician Questions - Practice Answering Them!
Reading helps, but actual practice is what gets you hired. Our AI feedback system helps you improve your Process Engineering Technician interview answers in real-time.
Personalized feedback
Unlimited practice
Used by hundreds of successful candidates
What is lean manufacturing, and how can its principles be applied in process engineering?
How to Answer
- 1
Define lean manufacturing clearly and concisely.
- 2
Mention key principles such as waste reduction and continuous improvement.
- 3
Explain how these principles apply to process engineering specifically.
- 4
Provide a real-world example of applying lean principles in a process.
- 5
Keep your answer structured and focused on practical application.
Example Answers
Lean manufacturing is a methodology aimed at reducing waste and improving efficiency. In process engineering, we can apply its principles by identifying and eliminating non-value-adding activities. For instance, in a manufacturing line, we can streamline workflows to minimize delays and enhance throughput.
What is statistical process control, and how do you use it in process engineering?
How to Answer
- 1
Define statistical process control clearly and concisely
- 2
Explain its purpose in maintaining and improving process quality
- 3
Describe specific tools used in statistical process control, like control charts
- 4
Provide a practical example of how you applied it in a process engineering scenario
- 5
Highlight the benefits of using statistical process control in your work
Example Answers
Statistical process control is a method used to monitor and control a process by using statistical methods. In process engineering, I use control charts to track variation in processes. For example, I once implemented control charts for a mixing process, which helped us identify when the process was going out of the desired range and allowed us to take corrective actions before defects occurred.
How have you used process simulation software in your previous roles?
How to Answer
- 1
Describe the specific software you used and the context of your work.
- 2
Mention a particular project where simulation was key to the process design.
- 3
Emphasize the benefits achieved from using the software, such as efficiency or cost reduction.
- 4
Include any collaboration with team members or departments during the simulation process.
- 5
Highlight your ability to interpret simulation results and implement changes based on them.
Example Answers
In my previous role at XYZ Corp, I used Aspen Plus to simulate a chemical process for a new production line, which helped us identify bottlenecks before the actual implementation, improving efficiency by 20%.
What techniques do you use for root cause analysis in process engineering?
How to Answer
- 1
Start with defining root cause analysis and its importance.
- 2
Mention specific techniques like 5 Whys, Fishbone diagram, or FMEA.
- 3
Provide a brief example of how you applied a technique in a past project.
- 4
Discuss any tools or software you use that assist in analysis.
- 5
Highlight how your findings led to process improvements.
Example Answers
I utilize the 5 Whys technique to dig deeper into process failures. For instance, when our production rate dropped, I asked 'why?' five times to uncover a machine calibration issue. This led to timely adjustments and increased efficiency by 20%.
What is the importance of equipment calibration in maintaining process accuracy?
How to Answer
- 1
Define equipment calibration and its role in process engineering.
- 2
Explain how calibration impacts measurement reliability and accuracy.
- 3
Discuss the consequences of not calibrating equipment.
- 4
Mention the industry standards or practices relevant to calibration.
- 5
Highlight your experience with calibration processes if applicable.
Example Answers
Equipment calibration ensures that measurement devices are accurate, which is crucial for maintaining process control. Without calibration, incorrect measurements could lead to product defects and safety issues. Regular calibration following industry standards helps prevent these problems.
What safety procedures are crucial in process engineering, and how do you implement them?
How to Answer
- 1
Identify key safety regulations relevant to the industry
- 2
Discuss conducting regular safety audits and risk assessments
- 3
Mention the importance of training staff on safety protocols
- 4
Emphasize the role of personal protective equipment (PPE)
- 5
Explain how to report and investigate safety incidents
Example Answers
In process engineering, crucial safety procedures include following OSHA regulations and conducting weekly safety audits to assess potential hazards. I ensure staff are trained on proper PPE usage, and any incidents are reported immediately for investigation.
What is the role of process documentation, and how have you ensured its accuracy?
How to Answer
- 1
Explain the purpose of process documentation in maintaining consistency and efficiency.
- 2
Discuss methods used to review and update documentation regularly.
- 3
Mention tools or software that have helped you track changes or ensure accuracy.
- 4
Provide an example of a specific documentation process you've worked on.
- 5
Highlight collaboration with team members to verify accuracy of documentation.
Example Answers
Process documentation is crucial for ensuring consistency and efficiency in operations. I regularly review our SOPs to make sure they are up-to-date and reflect any changes. For example, I implemented a monthly review system where team members check and validate key documents, ensuring everyone is on the same page.
How do you create and use process maps to identify areas for improvement?
How to Answer
- 1
Start by clearly defining the process and its boundaries.
- 2
Gather input from team members and stakeholders involved in the process.
- 3
Use standardized symbols to create a flowchart that visually represents the process steps.
- 4
Identify bottlenecks or redundancies by analyzing the flow of the process map.
- 5
Propose improvements based on insights gained from the process map.
Example Answers
I begin by outlining the process's boundaries and consulting with the team to gather insights. Then, I create a flowchart using standard symbols to visualize each step. While reviewing the map, I look for bottlenecks, which often reveal where time or resources are wasted. Finally, I suggest targeted improvements to streamline operations.
Don't Just Read Process Engineering Technician Questions - Practice Answering Them!
Reading helps, but actual practice is what gets you hired. Our AI feedback system helps you improve your Process Engineering Technician interview answers in real-time.
Personalized feedback
Unlimited practice
Used by hundreds of successful candidates
Situational Interview Questions
Suppose you are tasked with designing a new process to improve production speed. What steps would you take to begin this project?
How to Answer
- 1
Identify current production bottlenecks by analyzing existing data.
- 2
Engage with operators and supervisors to gather insights on pain points.
- 3
Research best practices and technologies in process improvement.
- 4
Create a feasibility study for potential solutions.
- 5
Develop a draft plan with timelines and resources needed.
Example Answers
First, I would analyze current production data to identify the main bottlenecks that slow down the process. Then I would talk to operators to understand their challenges. After that, I would look at industry best practices and technologies. Next, I'd assess the feasibility of the identified solutions and finally draft an implementation plan with clear timelines.
A process you are managing suddenly starts producing defective products. How would you address this issue?
How to Answer
- 1
Check the process control data to identify when the defects began.
- 2
Gather a team to diagnose potential causes including materials, equipment, and procedures.
- 3
Implement temporary controls to rectify immediate production issues while investigating.
- 4
Communicate with quality assurance to understand defect specifications.
- 5
Document all findings and actions taken for future reference and continuous improvement.
Example Answers
First, I would review the process data to pinpoint when the defects started. Then, I would bring together key team members to discuss possible causes. While we investigate, I would implement temporary measures to stabilize production. After identifying the root cause, I would coordinate with quality assurance to ensure the corrective actions meet specifications.
Don't Just Read Process Engineering Technician Questions - Practice Answering Them!
Reading helps, but actual practice is what gets you hired. Our AI feedback system helps you improve your Process Engineering Technician interview answers in real-time.
Personalized feedback
Unlimited practice
Used by hundreds of successful candidates
You notice a recurring issue in a process. How would you implement continuous improvement strategies to address it?
How to Answer
- 1
Identify the root cause of the issue using data analysis.
- 2
Engage stakeholders for input and support on potential improvements.
- 3
Develop a clear action plan outlining steps and responsibilities.
- 4
Implement changes on a small scale first to test effectiveness.
- 5
Monitor results and refine the process based on feedback.
Example Answers
First, I would analyze the process data to identify the root cause of the recurring issue. Then, I’d collaborate with my team to gather their insights and suggestions for improvement. After that, I would create an action plan with specific steps and assign roles. I’d implement the changes in a pilot program and assess the results closely, making adjustments as needed.
If you were asked to assess the risks of a new process implementation, what factors would you consider?
How to Answer
- 1
Identify potential safety hazards associated with the new process
- 2
Evaluate the impact on product quality and consistency
- 3
Consider the reliability and maintainability of new equipment
- 4
Assess the training needs for staff to handle the new process
- 5
Analyze the compliance with regulatory standards and industry guidelines
Example Answers
I would assess safety hazards first, ensuring that operating the new process won't pose risks to workers. Then, I would look at how the new process might affect product quality and if it meets our standards.
You have limited resources to implement a critical process change. How would you prioritize and manage the available resources?
How to Answer
- 1
Identify the key objectives of the process change
- 2
Assess the impact of each resource on achieving these objectives
- 3
Create a priority list based on impact and feasibility
- 4
Allocate resources to high-priority tasks first
- 5
Continuously monitor and adjust based on progress and challenges
Example Answers
I would start by clearly defining the key goals for the process change. Then, I would evaluate which resources are critical to achieving those goals. Once I have that, I'd prioritize the tasks that directly contribute to the objectives and allocate resources accordingly, ensuring to monitor progress and adapt as necessary.
Your team is conducting final process validation before full-scale production. What steps will you ensure are completed?
How to Answer
- 1
Review the validation protocol to ensure all criteria are met
- 2
Conduct a risk assessment to identify potential failure points
- 3
Perform a dry run to simulate full-scale production conditions
- 4
Collect data on key process parameters during validation runs
- 5
Document all findings and ensure all team members are aligned
Example Answers
I will start by reviewing the validation protocol to confirm that all required criteria are met. Then, I'll conduct a thorough risk assessment to identify any potential failure points before proceeding with a dry run to simulate full-scale production. During this run, I'll collect data on key process parameters and ensure proper documentation of our findings for future reference.
How would you handle an emergency situation where a critical piece of equipment fails during a production process?
How to Answer
- 1
Stay calm and assess the situation quickly.
- 2
Immediately notify the supervisor or manager.
- 3
Follow the established emergency protocols for equipment failure.
- 4
Evaluate if there is a way to temporarily bypass the issue.
- 5
Document the incident and report it after the emergency is handled.
Example Answers
In the event of a critical equipment failure, I would remain calm and quickly assess the issue before notifying my supervisor. I would follow the emergency protocols in place and see if there is any way to safely bypass the problem to minimize downtime.
A new quality standard requires updating existing processes. How would you go about ensuring compliance?
How to Answer
- 1
Identify the specific new quality standards and requirements.
- 2
Review existing processes to assess current compliance levels.
- 3
Develop a detailed action plan for updating processes.
- 4
Implement changes and train staff on new procedures.
- 5
Establish a monitoring system to ensure ongoing compliance.
Example Answers
First, I would thoroughly understand the new quality standards and then evaluate how our current processes measure up. Next, I’d create a clear plan to update the processes, involve stakeholders in the training, and set up a review system to regularly check compliance.
You need to work with an external vendor to improve a process. How would you ensure effective collaboration?
How to Answer
- 1
Establish clear communication channels from the start
- 2
Set shared goals and objectives for the collaboration
- 3
Regularly schedule check-ins to monitor progress
- 4
Ensure all parties understand their roles and responsibilities
- 5
Be open to feedback and flexible in approach
Example Answers
I would start by setting up a communication plan that includes regular meetings and progress updates, ensuring everyone is on the same page. Setting shared goals would help align our efforts towards the process improvement.
A new technology is being introduced into the process you are managing. How would you integrate it effectively to enhance performance?
How to Answer
- 1
Assess the current process and identify integration points for the new technology
- 2
Involve all stakeholders in discussions about the technology to get their input
- 3
Develop a comprehensive training plan for users to ensure smooth adoption
- 4
Create a pilot program to test the technology before full implementation
- 5
Monitor performance metrics post-integration to evaluate effectiveness
Example Answers
I would start by reviewing the existing process to find where the new technology can fit in effectively. I would gather feedback from the team and ensure everyone is comfortable with the change by providing adequate training.
Don't Just Read Process Engineering Technician Questions - Practice Answering Them!
Reading helps, but actual practice is what gets you hired. Our AI feedback system helps you improve your Process Engineering Technician interview answers in real-time.
Personalized feedback
Unlimited practice
Used by hundreds of successful candidates
Process Engineering Technician Position Details
Salary Information
Recommended Job Boards
These job boards are ranked by relevance for this position.
Related Positions
Ace Your Next Interview!
Practice with AI feedback & get hired faster
Personalized feedback
Used by hundreds of successful candidates
Ace Your Next Interview!
Practice with AI feedback & get hired faster
Personalized feedback
Used by hundreds of successful candidates