Top 30 Product Quality Engineer Interview Questions and Answers [Updated 2025]
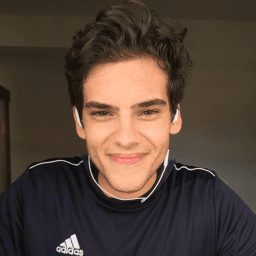
Andre Mendes
•
March 30, 2025
Preparing for a Product Quality Engineer interview can be daunting, but we're here to help streamline the process. In this post, you'll discover some of the most common interview questions for this role, along with example answers and insightful tips on how to respond effectively. Whether you're a seasoned professional or a newcomer, these insights will equip you with the confidence to excel in your interview.
Download Product Quality Engineer Interview Questions in PDF
To make your preparation even more convenient, we've compiled all these top Product Quality Engineerinterview questions and answers into a handy PDF.
Click the button below to download the PDF and have easy access to these essential questions anytime, anywhere:
List of Product Quality Engineer Interview Questions
Behavioral Interview Questions
Can you describe a time when you identified a persistent quality issue in a product and how you resolved it?
How to Answer
- 1
Think of a specific example that highlights your analytical skills.
- 2
Explain the issue clearly, including its impact on quality.
- 3
Describe the steps you took to investigate and identify the root cause.
- 4
Outline the solution you implemented and its outcomes.
- 5
Keep it focused on your actions and the results achieved.
Example Answers
In my previous role, I noticed a recurring defect in our product's software updates that caused user complaints. I traced the issue back to a specific part of the code that wasn't being tested thoroughly. I implemented a new testing protocol that added automated checks, and after its adoption, user-reported issues dropped by 40% within a month.
Tell us about a time you worked closely with a team to achieve a quality milestone.
How to Answer
- 1
Choose a specific project or milestone to discuss
- 2
Highlight your role and contributions
- 3
Mention team collaboration tools or methods used
- 4
Focus on the quality outcome and its impact
- 5
Keep it concise and structured using STAR method (Situation, Task, Action, Result)
Example Answers
In a recent project, our team aimed to reduce defects in a product launch by 20%. I collaborated closely with the design and manufacturing teams to analyze defect data. We held weekly meetings to track progress and adjusted processes based on feedback. As a result, we not only met our goal but exceeded it with a 25% reduction in defects.
Don't Just Read Product Quality Engineer Questions - Practice Answering Them!
Reading helps, but actual practice is what gets you hired. Our AI feedback system helps you improve your Product Quality Engineer interview answers in real-time.
Personalized feedback
Unlimited practice
Used by hundreds of successful candidates
Describe a situation where you initiated a change in quality process that led to improved product reliability.
How to Answer
- 1
Select a specific example where you identified a quality issue.
- 2
Explain the change you proposed and how you implemented it.
- 3
Detail the positive impact on product reliability and any metrics used.
- 4
Be clear about your role in the initiative.
- 5
Conclude with lessons learned or next steps for continuing improvement.
Example Answers
In my previous role, I noticed that our product returns were high due to a specific component failure. I initiated a review of our supplier's quality processes and proposed stricter incoming inspection criteria. After implementing these changes, our return rate dropped by 30%, significantly improving product reliability.
Describe a time when you had a disagreement with a colleague regarding quality standards, and how you resolved it.
How to Answer
- 1
Focus on a specific situation and avoid generalizations.
- 2
Clearly outline the differing opinions on quality standards.
- 3
Describe the steps you took to address the disagreement.
- 4
Emphasize the importance of collaboration and finding common ground.
- 5
Share the outcome and what you learned from the experience.
Example Answers
In a project to improve product durability, my colleague and I disagreed on the acceptable drop test result. I proposed we gather data from past test results, and we held a meeting to discuss them. By reviewing data together, we found a compromise that incorporated both of our perspectives, leading to a new testing protocol that improved product standards.
Can you give an example of how you led a team through a challenging quality project?
How to Answer
- 1
Start with a brief overview of the project and its goals.
- 2
Explain specific challenges the team faced.
- 3
Describe your leadership role and actions taken to address challenges.
- 4
Highlight the outcome and any improvements made.
- 5
Emphasize teamwork and collaboration among team members.
Example Answers
In my last role, I led a team tasked with reducing product defects by 30% within six months. We faced resistance to new quality protocols. I organized training sessions for the team to ensure everyone understood the changes. Through regular check-ins and feedback, we increased collaboration, and ultimately reduced defects by 40%.
Describe how you communicate complex quality issues to stakeholders with varying levels of technical expertise.
How to Answer
- 1
Identify the audience's technical level before communicating.
- 2
Use simple language and avoid jargon for non-experts.
- 3
Use visual aids like charts or graphs to illustrate key points.
- 4
Tailor the depth of information based on the stakeholder's needs.
- 5
Encourage questions to ensure understanding and engagement.
Example Answers
When I need to communicate a complex quality issue, I first assess the technical background of the stakeholders. For example, I might explain a defect using visual aids like a chart that highlights the issue and its impact. I always encourage questions to clarify and ensure everyone understands the implications.
Can you discuss a situation where you had to adapt quickly to a change in quality procedures?
How to Answer
- 1
Identify a specific instance where quality procedures changed
- 2
Explain your initial reaction and how you assessed the situation
- 3
Describe the actions you took to adapt to the new procedures
- 4
Highlight the outcome and any positive results from your adaptation
- 5
Emphasize your ability to remain flexible and proactive during changes
Example Answers
In my previous role, our team was notified about a new quality inspection standard. I quickly reviewed the new requirements, coordinated a team meeting to align everyone's understanding, and we implemented the changes within a week. This proactive approach helped us meet our deadlines without compromising quality.
Describe your approach to managing a long-term quality assurance project.
How to Answer
- 1
Start by outlining the project's goals and requirements.
- 2
Implement a structured timeline with milestones and deadlines.
- 3
Use data-driven metrics to monitor progress and quality.
- 4
Ensure clear communication with the team and stakeholders regularly.
- 5
Adjust strategies as needed based on feedback and results.
Example Answers
In my approach to managing a long-term quality assurance project, I first define the goals and requirements clearly. Then, I create a timeline with key milestones to track progress. I use metrics to assess quality and communicate regularly with the team to ensure everyone is aligned. If challenges arise, I’m flexible and ready to adjust our strategies.
Don't Just Read Product Quality Engineer Questions - Practice Answering Them!
Reading helps, but actual practice is what gets you hired. Our AI feedback system helps you improve your Product Quality Engineer interview answers in real-time.
Personalized feedback
Unlimited practice
Used by hundreds of successful candidates
Technical Interview Questions
What methodologies do you use for root cause analysis in quality engineering?
How to Answer
- 1
Mention specific methodologies like 5 Whys, Fishbone Diagram, or FMEA.
- 2
Explain how you have applied these methods in past projects.
- 3
Discuss the importance of data collection and analysis in root cause identification.
- 4
Highlight teamwork and communication during the root cause analysis process.
- 5
Provide a brief example of a successful root cause analysis outcome.
Example Answers
I often use the 5 Whys methodology to drill down into issues. For example, in a project where we had recurrent defects, I used 5 Whys to identify a missing step in our process, leading to a 30% reduction in defects.
How do you apply statistical process control in maintaining product quality?
How to Answer
- 1
Explain the concept of statistical process control (SPC) clearly.
- 2
Discuss specific tools used in SPC like control charts and process capability analysis.
- 3
Provide examples of how you've implemented SPC in previous roles.
- 4
Mention the importance of data collection and analysis for ongoing process improvement.
- 5
Highlight collaboration with cross-functional teams to ensure adherence to quality standards.
Example Answers
I utilize statistical process control by implementing control charts to monitor critical product characteristics. For instance, in my previous role, I tracked a manufacturing process using X-bar and R charts, which helped us maintain product quality and reduce defects by 30%.
Don't Just Read Product Quality Engineer Questions - Practice Answering Them!
Reading helps, but actual practice is what gets you hired. Our AI feedback system helps you improve your Product Quality Engineer interview answers in real-time.
Personalized feedback
Unlimited practice
Used by hundreds of successful candidates
What experience do you have with ISO 9001 and other quality standards?
How to Answer
- 1
Identify specific roles where you implemented ISO 9001.
- 2
Highlight any certifications or training related to quality standards.
- 3
Mention measurable outcomes or improvements due to your efforts.
- 4
Discuss your familiarity with audits and compliance processes.
- 5
Connect your experience to the specific needs of the role.
Example Answers
In my previous role at ABC Corp, I was responsible for implementing ISO 9001, which led to a 20% reduction in product defects over two years. I also completed a certification course on ISO 9001 standards.
What techniques do you employ for Failure Mode and Effects Analysis (FMEA)?
How to Answer
- 1
Understand the process thoroughly before starting FMEA
- 2
Identify and prioritize potential failure modes based on severity
- 3
Use a cross-functional team to bring diverse insights
- 4
Apply a standardized FMEA template for consistency
- 5
Regularly update the FMEA based on new data or findings
Example Answers
In conducting FMEA, I start by gathering a cross-functional team to discuss the process and identify potential failure modes. We prioritize these based on their severity and then use a standardized template to document our findings and recommendations.
What tools and techniques do you use for quality data analysis?
How to Answer
- 1
Mention specific statistical tools like Minitab or Excel for data analysis.
- 2
Highlight techniques like root cause analysis or control charts.
- 3
Include data visualization tools such as Tableau or Power BI.
- 4
Discuss your experience with process improvement methodologies like Six Sigma.
- 5
Be prepared to give examples of how these tools helped solve quality issues.
Example Answers
I often use Minitab for statistical analysis and root cause analysis to identify issues. Control charts are part of my toolkit to monitor performance over time.
Which quality management tools are you proficient in?
How to Answer
- 1
Identify key quality management tools you have used
- 2
Provide examples of how you've used these tools in past roles
- 3
Mention any certifications or training related to these tools
- 4
Focus on tools relevant to the role of Product Quality Engineer
- 5
Keep your answer concise and to the point
Example Answers
I am proficient in Six Sigma and have utilized DMAIC methodology to improve product quality in my previous job, which resulted in a 20% reduction in defects.
What continuous improvement techniques do you use to ensure product quality?
How to Answer
- 1
Identify specific continuous improvement methodologies you are familiar with, like Six Sigma or Lean.
- 2
Discuss how you apply tools like root cause analysis or failure mode effects analysis (FMEA).
- 3
Share a short example of a successful improvement initiative you led or participated in.
- 4
Emphasize teamwork and collaboration in driving quality improvements.
- 5
Mention metrics or KPIs you use to measure the effectiveness of improvements.
Example Answers
I often use Lean methodologies to identify waste in production processes. For example, I led a cross-functional team to reduce defect rates by 20% through a focused root cause analysis and implementing corrective actions.
What inspection techniques do you find most effective for product quality control?
How to Answer
- 1
Identify specific inspection techniques relevant to the industry
- 2
Discuss any relevant tools or technologies you use
- 3
Mention both qualitative and quantitative methods
- 4
Provide examples of how these techniques improved product quality
- 5
Emphasize the importance of data in decision-making
Example Answers
I find visual inspection combined with automated optical inspection highly effective. For example, using camera systems in production has significantly reduced defect rates by catching errors early in the process.
Which software tools do you prefer for documenting and analyzing quality metrics?
How to Answer
- 1
Identify specific tools you have experience with.
- 2
Explain the purpose of each tool in quality metrics.
- 3
Mention any relevant certifications or training in the tools.
- 4
Relate your preferred tools to the company's current practices, if known.
- 5
Be prepared to discuss why these tools improve quality outcomes.
Example Answers
I prefer using Minitab for statistical analysis and Excel for documentation. Minitab helps me to visualize defects and trends effectively, while Excel is great for creating detailed reports and dashboards.
What testing methodologies do you employ to ensure product quality?
How to Answer
- 1
Discuss various testing methodologies like manual testing, automated testing, and exploratory testing
- 2
Mention specific tools or frameworks you are familiar with
- 3
Emphasize how you choose methodologies based on project requirements
- 4
Provide examples of when you applied these methodologies in past projects
- 5
Highlight the importance of continuous integration and testing in your approach
Example Answers
I use a combination of automated testing with tools like Selenium and manual exploratory testing to ensure product quality. For example, in my last project, I implemented a CI/CD pipeline that included automated tests, which helped catch bugs early.
Don't Just Read Product Quality Engineer Questions - Practice Answering Them!
Reading helps, but actual practice is what gets you hired. Our AI feedback system helps you improve your Product Quality Engineer interview answers in real-time.
Personalized feedback
Unlimited practice
Used by hundreds of successful candidates
Situational Interview Questions
If tasked with improving the quality assurance process in a new product line, what steps would you take?
How to Answer
- 1
Assess current quality assurance processes and identify weaknesses
- 2
Gather feedback from stakeholders and team members
- 3
Implement automated testing where feasible to increase efficiency
- 4
Develop a set of measurable quality metrics to track improvements
- 5
Conduct regular reviews and adapt strategies based on results
Example Answers
First, I would evaluate the existing QA processes to pinpoint inefficiencies. Then, I would involve the team in discussions to gather their insights and suggestions. Next, I would introduce automated testing to enhance coverage and reduce manual work. Additionally, I would establish clear quality metrics to monitor our progress over time. Finally, I would implement a cycle of regular reviews to ensure continuous improvement.
How would you handle receiving a customer complaint about a recurring defect?
How to Answer
- 1
Acknowledge the customer's concern and thank them for reaching out
- 2
Gather detailed information about the defect from the customer
- 3
Investigate the root cause of the defect with your team
- 4
Communicate transparently with the customer about the findings and the steps being taken
- 5
Follow up with the customer after resolving the issue to ensure satisfaction
Example Answers
I would first acknowledge the customer's complaint and express my gratitude for their feedback. Then, I would ask for specific details about the defect they encountered and conduct an investigation with the team to identify the root cause. Once we have a solution, I would inform the customer of our findings and the corrective actions we will take. Finally, I would follow up with them to ensure they are satisfied with our response.
Don't Just Read Product Quality Engineer Questions - Practice Answering Them!
Reading helps, but actual practice is what gets you hired. Our AI feedback system helps you improve your Product Quality Engineer interview answers in real-time.
Personalized feedback
Unlimited practice
Used by hundreds of successful candidates
Imagine you find discrepancies in a quality audit result. How would you address this with your team and management?
How to Answer
- 1
Review the discrepancies in detail before addressing anyone.
- 2
Gather relevant data to support your findings.
- 3
Communicate openly and factually with your team.
- 4
Propose a meeting to discuss the discrepancies with all stakeholders.
- 5
Suggest actionable steps to resolve the issues identified.
Example Answers
I would first carefully review the audit results to understand the discrepancies. Then, I would gather supporting data and evidence, and present it in a meeting with my team to discuss our findings and brainstorm solutions together.
Suppose a key supplier consistently provides subpar materials. How would you manage this issue?
How to Answer
- 1
Communicate directly with the supplier to understand the root cause of the issue
- 2
Implement a temporary alternative supplier to mitigate risk
- 3
Develop a corrective action plan outlining specific quality standards
- 4
Schedule regular audits and reviews with the supplier to monitor improvement
- 5
Escalate the issue to management if no resolution is achieved after attempts
Example Answers
I would start by having a direct conversation with the supplier to identify why the materials are not meeting our standards. Based on this discussion, I would assess whether we need a temporary alternative supplier to ensure continuity. I would also create a corrective action plan with clear quality metrics for them to improve.
How would you respond if a major defect is discovered in a recently released product?
How to Answer
- 1
Assess the defect's impact and scope immediately.
- 2
Gather a cross-functional team to analyze the issue.
- 3
Communicate transparently with stakeholders about the defect.
- 4
Develop an action plan that includes a timeline for resolution.
- 5
Monitor the resolution process and follow up with the team regularly.
Example Answers
I would first assess the defect to understand its impact on users and the product. Then, I would convene a meeting with the product, engineering, and quality teams to analyze the defect. After that, I would communicate the findings to stakeholders, ensuring they are aware of the situation. We would then create an action plan to resolve the defect including a timeline, and I'd keep track of our progress.
If a quality process fails during production, what immediate actions would you take?
How to Answer
- 1
Assess the situation quickly to understand the extent of the failure.
- 2
Stop the production line to prevent further defects.
- 3
Communicate the issue to the team and relevant stakeholders immediately.
- 4
Investigate the root cause of the failure using available data.
- 5
Implement containment measures to address the immediate impact.
Example Answers
First, I would stop the production line to prevent any further defective products. Then, I would gather my team to communicate the issue and start an investigation into what caused the quality process to fail. While we analyze the data, I would also implement temporary measures to contain any ongoing issues.
How would you prioritize quality issues in a scenario with limited resources?
How to Answer
- 1
Identify the impact of each quality issue on the product and customers
- 2
Assess the frequency of occurrence for each issue
- 3
Consider regulatory compliance and safety related issues as top priorities
- 4
Evaluate the resources required to address each issue
- 5
Communicate with stakeholders to ensure alignment on priorities
Example Answers
I would first assess each issue's impact on product functionality and customer satisfaction. Then, I would consider how often each issue occurs, prioritizing those that affect a high number of users or critical features. Compliance and safety issues would take precedence, followed by others based on required resources to resolve them.
How would you handle a situation where data suggests the opposite of your team's quality beliefs?
How to Answer
- 1
Acknowledge the data and its source
- 2
Encourage open discussion within the team about the findings
- 3
Explore the reasons behind the data and what it indicates
- 4
Suggest conducting further analysis or testing to validate the data
- 5
Propose adjusting quality beliefs if necessary based on the evidence
Example Answers
I would first acknowledge the data and ensure the team understands its source. Then, I'd facilitate a discussion to explore how this data contrasts with our beliefs, encouraging everyone to share their perspectives.
How would you facilitate a quality improvement workshop with a multidisciplinary team?
How to Answer
- 1
Set clear objectives for the workshop to focus the discussion.
- 2
Use facilitation techniques like brainstorming and fishbowl to encourage participation.
- 3
Ensure every team member's voice is heard by using structured turn-taking.
- 4
Document ideas and action items in real time for clarity and follow-up.
- 5
Conclude with a summary of key points and assign responsibilities.
Example Answers
I would start by defining clear objectives for the workshop. Then, I would use brainstorming sessions to gather input, making sure everyone can contribute. I would keep notes visible throughout, summarizing ideas, and assign follow-up tasks before closing the session.
If you identify a potential risk in the product design phase, how would you address it?
How to Answer
- 1
Analyze the risk to understand its impact on product quality.
- 2
Collaborate with the design team to discuss findings and gather input.
- 3
Propose solutions or modifications to mitigate the risk.
- 4
Document the risk assessment and proposed actions clearly.
- 5
Follow up to ensure implementation of the proposed solutions.
Example Answers
Upon identifying a risk, I would first assess its potential impact on product quality. Then, I would schedule a meeting with the design team to discuss this risk and gather their feedback. Based on our discussions, I would suggest modifications to the design to mitigate the risk, ensure all stakeholders are aware, and document everything for future reference.
Don't Just Read Product Quality Engineer Questions - Practice Answering Them!
Reading helps, but actual practice is what gets you hired. Our AI feedback system helps you improve your Product Quality Engineer interview answers in real-time.
Personalized feedback
Unlimited practice
Used by hundreds of successful candidates
Product Quality Engineer Position Details
Recommended Job Boards
CareerBuilder
www.careerbuilder.com/jobs/product-quality-engineerThese job boards are ranked by relevance for this position.
Related Positions
Ace Your Next Interview!
Practice with AI feedback & get hired faster
Personalized feedback
Used by hundreds of successful candidates
Ace Your Next Interview!
Practice with AI feedback & get hired faster
Personalized feedback
Used by hundreds of successful candidates