Top 30 Customer Quality Engineer Interview Questions and Answers [Updated 2025]
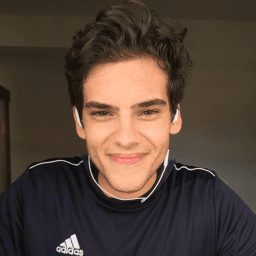
Andre Mendes
•
March 30, 2025
Navigating the intricate role of a Customer Quality Engineer requires a keen understanding of both technical and customer-focused skills. In this post, we delve into the most common interview questions for this role, providing you with insightful example answers and invaluable tips on how to respond effectively. Prepare to engage with key concepts and boost your confidence for your next interview.
Download Customer Quality Engineer Interview Questions in PDF
To make your preparation even more convenient, we've compiled all these top Customer Quality Engineerinterview questions and answers into a handy PDF.
Click the button below to download the PDF and have easy access to these essential questions anytime, anywhere:
List of Customer Quality Engineer Interview Questions
Situational Interview Questions
A process you oversee consistently results in high defects. How would you approach improving it?
How to Answer
- 1
Analyze current process data to identify defect patterns
- 2
Engage team members to gather insights on root causes
- 3
Implement a process improvement plan with clear metrics
- 4
Test changes on a small scale before a full rollout
- 5
Monitor results and adjust strategies as necessary
Example Answers
I would start by reviewing the defect data to pinpoint where the highest issues occur. Engaging with the team for feedback would help identify root causes. Then, I would develop an improvement plan and implement changes on a limited basis to evaluate effectiveness.
If a customer reports a defect in a product that you believe is not a quality issue, how would you handle the situation?
How to Answer
- 1
Listen carefully to the customer's concerns and acknowledge their experience.
- 2
Gather all relevant information from the customer regarding the defect.
- 3
Investigate the product in question to confirm if it is indeed a quality issue.
- 4
Communicate your findings clearly to the customer, explaining your reasoning.
- 5
Offer solutions or alternatives to address the customer's concerns if applicable.
Example Answers
I would first listen to the customer to fully understand their concerns and acknowledge their experience. Then, I would gather detailed information about the reported defect. After that, I would investigate the product to determine if it aligns with our quality standards and explain my findings back to the customer clearly while exploring any possible solutions.
Don't Just Read Customer Quality Engineer Questions - Practice Answering Them!
Reading helps, but actual practice is what gets you hired. Our AI feedback system helps you improve your Customer Quality Engineer interview answers in real-time.
Personalized feedback
Unlimited practice
Used by hundreds of successful candidates
Imagine you are part of a team launching a new product, and you identify a potential quality issue. What steps would you take to address it?
How to Answer
- 1
Identify and document the quality issue clearly.
- 2
Communicate the issue to the team and relevant stakeholders immediately.
- 3
Analyze the root cause of the issue to understand why it occurred.
- 4
Propose corrective actions to resolve the issue and prevent future occurrences.
- 5
Follow up on the implementation of the corrective actions and verify their effectiveness.
Example Answers
Upon identifying a quality issue, I would document it in detail, then immediately inform the team and stakeholders to ensure transparency. Next, I would work with the team to analyze the root cause and develop corrective actions, implementing them promptly and monitoring their effectiveness.
What would you do if a key supplier consistently fails to meet quality standards, impacting your company's product quality?
How to Answer
- 1
Assess the root cause of the quality issues with the supplier
- 2
Communicate directly with the supplier to address concerns
- 3
Collaborate with internal teams to find interim solutions
- 4
Implement a corrective action plan with the supplier
- 5
Consider alternative suppliers if issues persist
Example Answers
I would first investigate the root cause of the supplier's quality issues by reviewing their processes and materials. Then, I would arrange a meeting with their management to discuss these concerns and work collaboratively on a corrective action plan. If improvements are not seen in a reasonable timeframe, I would explore alternative suppliers to mitigate the risk.
How would you handle a situation where a customer demands a solution that is against company policies to solve a quality issue?
How to Answer
- 1
Acknowledge the customer's concern and understand their perspective
- 2
Explain the company policy clearly and why it exists
- 3
Explore alternative solutions that comply with company policies
- 4
Offer to escalate the issue to a higher authority if necessary
- 5
Ensure the customer feels heard and valued despite the limitations
Example Answers
I would first listen carefully to the customer's concerns and empathize with their frustration. Then, I would explain the specific company policy and its purpose. I would suggest alternative solutions that align with our policies, and if they are unsatisfied, I would offer to escalate to a manager for further review.
How would you respond to an urgent quality issue that could potentially halt production?
How to Answer
- 1
Quickly assess the situation to understand the root cause of the quality issue
- 2
Communicate immediately with the production team and relevant stakeholders
- 3
Implement a temporary stop of affected production lines if necessary to prevent further issues
- 4
Gather data and evidence regarding the quality issue to inform a long-term resolution
- 5
Develop and communicate an action plan for resolving the issue and resuming production
Example Answers
First, I would quickly investigate the issue to determine its cause, while informing the production team of the potential halt. If the issue is critical, I would pause production to prevent defective products. Next, I would collect relevant data to support our findings and outline an action plan to resolve the issue as quickly as possible.
A new regulation has been introduced that impacts product quality standards. How would you ensure compliance?
How to Answer
- 1
Review the new regulation thoroughly to understand all requirements.
- 2
Assess current quality processes and identify gaps in compliance.
- 3
Develop an action plan that includes necessary changes to processes.
- 4
Train relevant team members on the new standards and procedures.
- 5
Establish a monitoring system to ensure ongoing compliance.
Example Answers
First, I would carefully review the new regulation to understand its implications. Then, I would conduct an assessment of our current processes to identify any gaps. After that, I would create a detailed action plan to update our quality procedures and share this with the team for input. Training will be crucial, so I would organize sessions to ensure everyone is informed about the new standards. Finally, I would set up a monitoring system to regularly check that we remain compliant with the regulation.
How would you prioritize customer feedback for quality improvements when resources are limited?
How to Answer
- 1
Analyze feedback based on impact on customer satisfaction.
- 2
Identify trends and common themes in the feedback.
- 3
Consider the frequency of the issue reported.
- 4
Evaluate the feasibility of implementing changes with available resources.
- 5
Communicate with customers to understand their most pressing needs.
Example Answers
I would start by categorizing feedback based on its impact on overall customer satisfaction. Then, I'd look for trends to identify the most common issues and prioritize them. Issues that occur frequently and significantly affect user experience would be at the top of my list, and I'd assess which improvements are feasible given our resource limitations.
If faced with a decision where improving quality would significantly increase costs, how would you proceed?
How to Answer
- 1
Assess the cost-benefit ratio of the quality improvement.
- 2
Consider the long-term impacts on customer satisfaction and brand reputation.
- 3
Explore alternative solutions that may improve quality without significantly increasing costs.
- 4
Involve stakeholders in the decision-making process to ensure alignment and transparency.
- 5
Present a data-driven argument to support the decision or alternative options.
Example Answers
I would analyze the long-term customer satisfaction benefits against the immediate costs, ensuring stakeholders understand the value proposition. This might involve presenting data that shows how quality improvements lead to reduced returns and higher loyalty.
How would you develop a training program to ensure all employees understand new quality standards and procedures?
How to Answer
- 1
Assess current knowledge levels of employees regarding quality standards
- 2
Design a structured training program that includes both theoretical and practical components
- 3
Utilize various training methods such as workshops, e-learning, and hands-on sessions
- 4
Implement regular assessments to gauge understanding and retention of information
- 5
Encourage feedback from employees to continuously improve the training program
Example Answers
First, I would assess the employees’ current understanding of quality standards through surveys. Next, I would develop a structured training program that combines workshops and e-learning modules. After the training, I would conduct assessments to evaluate effectiveness and adjust the program based on employee feedback.
Don't Just Read Customer Quality Engineer Questions - Practice Answering Them!
Reading helps, but actual practice is what gets you hired. Our AI feedback system helps you improve your Customer Quality Engineer interview answers in real-time.
Personalized feedback
Unlimited practice
Used by hundreds of successful candidates
Behavioral Interview Questions
Can you describe a time when you identified a major quality issue in a product and how you resolved it?
How to Answer
- 1
Choose a specific example from your experience that had a measurable impact.
- 2
Clearly outline the problem you identified and its implications.
- 3
Explain the steps you took to investigate and resolve the issue.
- 4
Highlight any collaboration with team members or stakeholders.
- 5
Conclude with the results or lessons learned from the situation.
Example Answers
At my last job, we had a recurring defect in a critical component that caused product returns. I led a root cause analysis with my team, identified a manufacturing flaw, and worked with the supplier to improve their process. After implementing the changes, we reduced defects by 40% and improved customer satisfaction significantly.
Describe a situation where you had to work closely with a cross-functional team to address a quality issue?
How to Answer
- 1
Choose a specific quality issue you faced.
- 2
Identify the cross-functional teams involved, such as production and design.
- 3
Explain your role in the team during the process.
- 4
Highlight the steps taken to resolve the issue.
- 5
Mention the outcome and any lessons learned.
Example Answers
In my previous role, we noticed a recurring defect in a product. I collaborated with the design team, the production team, and the quality assurance team. I facilitated meetings to understand each team's perspective, leading to a redesign of a component that was causing the defect. As a result, we reduced the defect rate by 30% and improved customer satisfaction.
Don't Just Read Customer Quality Engineer Questions - Practice Answering Them!
Reading helps, but actual practice is what gets you hired. Our AI feedback system helps you improve your Customer Quality Engineer interview answers in real-time.
Personalized feedback
Unlimited practice
Used by hundreds of successful candidates
Tell me about a time when you had a conflict with a team member or department about a quality issue and how you resolved it.
How to Answer
- 1
Describe the specific quality issue that caused the conflict.
- 2
Explain your role and your perspective on the issue.
- 3
Detail the steps you took to address the conflict.
- 4
Highlight the outcome and any compromise reached.
- 5
Reflect on what you learned from the experience.
Example Answers
In my last project, we had a quality disagreement over the testing standards for a product. I found that my team's thorough testing was being deemed excessive by the development department. I organized a meeting to present data on the impact of previous defects. By aligning our goals and agreeing on a balance between speed and quality, we reached a consensus, and our subsequent product launch had a significantly lower defect rate.
Describe a time when you had to lead a quality improvement project. What was the outcome?
How to Answer
- 1
Identify a specific project where you had a leadership role.
- 2
Explain your goals and the quality issues you aimed to address.
- 3
Discuss the steps you took to implement changes and engage the team.
- 4
Share the outcome with measurable results or improvements.
- 5
Reflect on what you learned from the experience.
Example Answers
In my previous role, I led a project to reduce defect rates in our manufacturing process. We set a goal to reduce defects from 5% to 2%. I organized cross-functional meetings to analyze the root causes and implemented a new training program for technicians. As a result, we achieved a 50% reduction in defects within three months, improving product reliability and customer satisfaction.
Can you provide an example of how you communicated a complex quality issue to non-technical stakeholders?
How to Answer
- 1
Identify the key stakeholders involved and their level of understanding.
- 2
Break down the technical details into simple concepts.
- 3
Use visuals or analogies to explain the issue if possible.
- 4
Focus on the impact of the issue on the project or customers.
- 5
Invite questions and clarify any concerns to ensure understanding.
Example Answers
In my previous role, we identified a defect in the product that affected customer safety. I organized a meeting with the marketing and sales teams, used a simple chart to show how the defect could lead to customer complaints, and explained the steps we were taking to fix it.
Describe a situation where you improved customer satisfaction by addressing a quality issue proactively.
How to Answer
- 1
Think of a specific quality issue you identified early, before it affected customers.
- 2
Explain the steps you took to investigate and resolve the issue.
- 3
Mention any collaboration with other teams to ensure a comprehensive solution.
- 4
Quantify the improvement, if possible, such as metrics or customer feedback.
- 5
Focus on the positive outcome for the customers and the company.
Example Answers
In my previous role, I noticed a recurring defect in our product that had been causing customer complaints. I gathered data from support tickets, collaborated with the engineering team to identify the root cause, and implemented a change in the manufacturing process. After the change, customer satisfaction scores improved by 20% over the next quarter.
Tell me about a time you had to adapt quickly to changes impacting product quality. How did you handle it?
How to Answer
- 1
Identify a specific instance where changes occurred suddenly.
- 2
Describe the nature of the change and its impact on product quality.
- 3
Explain your immediate response and the steps you took to address the situation.
- 4
Highlight any collaboration with team members or stakeholders.
- 5
Conclude with the outcome and any lessons learned.
Example Answers
In my previous role, we faced a sudden supplier quality issue that affected our production schedule. I quickly assessed the defects and communicated with the supplier to understand the root cause. Collaborating with the production team, we modified our quality checks to catch defects early. As a result, we minimized rework and delivered the product on time, while also ensuring better supplier engagement for future quality assurance.
Give an example of a time you took initiative to solve a quality problem before it escalated.
How to Answer
- 1
Identify a specific quality issue you encountered.
- 2
Describe the steps you took to analyze and address the problem.
- 3
Emphasize your proactive approach and the impact of your actions.
- 4
Use metrics or results to show the effectiveness of your solution.
- 5
Conclude with what you learned from the experience.
Example Answers
In my previous role, I noticed that the defect rate in a product line was increasing. I proactively gathered data on the common defects, analyzed the production process, and discovered a miscalibration in the machinery. I coordinated with the maintenance team to recalibrate the equipment, which reduced defects by 30% in the following month. This experience taught me the importance of early intervention in quality management.
Describe a situation where your attention to detail helped prevent a significant quality issue.
How to Answer
- 1
Think of a specific project where you caught a mistake early.
- 2
Explain the context of the situation clearly.
- 3
Describe the specific actions you took to address the detail.
- 4
Highlight the positive outcome or the issue that was avoided.
- 5
Keep it concise and focus on your role in the success.
Example Answers
In my last role, while reviewing a product design document, I noticed a discrepancy in the material specifications. By flagging this issue early, we were able to change the order before production, preventing a costly recall due to material failure.
Don't Just Read Customer Quality Engineer Questions - Practice Answering Them!
Reading helps, but actual practice is what gets you hired. Our AI feedback system helps you improve your Customer Quality Engineer interview answers in real-time.
Personalized feedback
Unlimited practice
Used by hundreds of successful candidates
Technical Interview Questions
What are some key ISO quality standards that you have worked with in your previous roles?
How to Answer
- 1
Identify the specific ISO standards you are familiar with, such as ISO 9001 or ISO 13485.
- 2
Mention your experience in implementing or auditing these standards.
- 3
Provide examples of how these standards impacted quality management in your role.
- 4
Emphasize any specific achievements or improvements related to these standards.
- 5
Be ready to explain how you stay updated with ISO standards.
Example Answers
In my previous role, I worked extensively with ISO 9001, focusing on quality management systems. We implemented a new documentation process that improved compliance and reduced errors by 20%.
What methods do you use to perform root cause analysis for quality issues?
How to Answer
- 1
Use a structured approach such as 5 Whys or Fishbone diagrams.
- 2
Collect and analyze relevant data to identify patterns.
- 3
Involve cross-functional teams for diverse perspectives.
- 4
Test potential root causes to confirm their validity.
- 5
Document findings and revise processes to prevent recurrence.
Example Answers
I typically use the 5 Whys method, starting from the observed issue and asking 'Why?' multiple times until I reach the root cause. For example, if a product fails a test, I would trace it back to the materials used, examining supplier discrepancies as part of the analysis.
Don't Just Read Customer Quality Engineer Questions - Practice Answering Them!
Reading helps, but actual practice is what gets you hired. Our AI feedback system helps you improve your Customer Quality Engineer interview answers in real-time.
Personalized feedback
Unlimited practice
Used by hundreds of successful candidates
How do you utilize statistical methods in ensuring product quality?
How to Answer
- 1
Define the statistical methods you are familiar with and their relevance to quality.
- 2
Describe how you apply these methods in real-world scenarios, such as in testing or process improvement.
- 3
Provide examples of key metrics you track, like defect rates or process capability.
- 4
Mention any tools or software you use for statistical analysis.
- 5
Show understanding of how statistical methods lead to data-driven decision making.
Example Answers
I use techniques like control charts and hypothesis testing to monitor manufacturing processes. For instance, I track defect rates over time and apply statistical process control to identify trends.
Can you discuss your experience with quality tools like Six Sigma or Lean?
How to Answer
- 1
Define your familiarity with Six Sigma and Lean methodologies.
- 2
Share specific projects where you successfully applied these tools.
- 3
Mention any certifications or training you have completed.
- 4
Highlight measurable outcomes from your quality improvements.
- 5
Emphasize your teamwork and collaboration in quality initiatives.
Example Answers
I have utilized Six Sigma in my previous role at XYZ Corp, where I led a project that reduced process defects by 30%. I am a certified Six Sigma Green Belt and I worked with a cross-functional team to implement DMAIC principles.
What tools or systems have you used for defect tracking, and how effective have they been?
How to Answer
- 1
Identify specific defect tracking tools you have experience with.
- 2
Explain how you used these tools in your previous roles.
- 3
Discuss the effectiveness of these tools with examples of outcomes.
- 4
Mention any improvements or changes you implemented using these tools.
- 5
Relate your experience to the requirements of the Customer Quality Engineer position.
Example Answers
In my previous role, I used JIRA for defect tracking. It allowed us to prioritize issues effectively, and our team reduced defect resolution time by 30%.
Describe your experience with performing failure analysis and the techniques used.
How to Answer
- 1
Start by outlining your relevant experience in failure analysis clearly.
- 2
Mention specific failure analysis techniques you are familiar with, such as root cause analysis, 5 Whys, or FMEA.
- 3
Provide a brief example of a situation where you successfully identified and resolved a quality issue.
- 4
Highlight the tools or methods you used and the outcomes achieved.
- 5
Emphasize your analytical skills and attention to detail in your approach.
Example Answers
In my previous role as a Customer Quality Engineer, I conducted a thorough failure analysis on a defective product line. I used root cause analysis to identify that the issue was due to a manufacturing defect. This involved gathering data, performing a 5 Whys analysis, and collaborating with the production team to implement corrective actions, which reduced defects by 30%.
How do you analyze quality data to identify trends and areas for improvement?
How to Answer
- 1
Start by collecting relevant quality data from different sources.
- 2
Use statistical methods to analyze the data, such as control charts or regression analysis.
- 3
Look for patterns over time to identify recurring issues.
- 4
Prioritize areas for improvement based on impact and frequency of issues.
- 5
Communicate findings clearly with actionable recommendations.
Example Answers
I begin by gathering all quality data from production reports and customer feedback. Then, I apply control charts to monitor defects over time, identifying any upward trends. From this analysis, I prioritize the most frequent defects for targeted improvement efforts.
What inspection techniques do you find most effective for maintaining product quality?
How to Answer
- 1
Identify specific inspection techniques relevant to the industry.
- 2
Discuss why each technique is effective for product quality.
- 3
Mention how these techniques can prevent defects.
- 4
Include examples of tools or technologies used in inspections.
- 5
Emphasize the importance of continuous improvement and adaptability.
Example Answers
I find that visual inspection combined with automated optical inspection is highly effective. Visual checks allow for immediate identification of defects, while automated systems can process large quantities quickly, reducing human error.
Explain how Statistical Process Control (SPC) can be used to maintain quality standards.
How to Answer
- 1
Define SPC and its role in quality management
- 2
Mention key tools like control charts and process capability analysis
- 3
Explain how SPC helps in identifying trends and variations in processes
- 4
Discuss the importance of data collection and analysis for informed decision making
- 5
Provide an example of SPC improving a specific quality issue in a process
Example Answers
Statistical Process Control (SPC) is a method that uses statistical tools to monitor and control a process. Control charts are commonly used to visualize variations in the process over time. By identifying when a process goes out of control, companies can take corrective actions to maintain quality standards. For example, if a control chart shows an increasing trend in defects, engineers can investigate and rectify the root cause before it escalates.
How do you assess and manage risks associated with product quality?
How to Answer
- 1
Identify potential risks by analyzing failure modes using tools like FMEA.
- 2
Prioritize risks based on their impact and likelihood of occurrence.
- 3
Implement controls and preventive measures to mitigate risks effectively.
- 4
Monitor quality metrics continuously to detect new risks early.
- 5
Engage cross-functional teams to gather insights and improve risk management.
Example Answers
I assess risks by conducting FMEA to identify potential failure modes, prioritize them by their impact, and implement preventive controls such as process validations.
Don't Just Read Customer Quality Engineer Questions - Practice Answering Them!
Reading helps, but actual practice is what gets you hired. Our AI feedback system helps you improve your Customer Quality Engineer interview answers in real-time.
Personalized feedback
Unlimited practice
Used by hundreds of successful candidates
Customer Quality Engineer Position Details
Salary Information
Recommended Job Boards
CareerBuilder
www.careerbuilder.com/jobs/customer-quality-engineerThese job boards are ranked by relevance for this position.
Related Positions
Ace Your Next Interview!
Practice with AI feedback & get hired faster
Personalized feedback
Used by hundreds of successful candidates
Ace Your Next Interview!
Practice with AI feedback & get hired faster
Personalized feedback
Used by hundreds of successful candidates