Top 30 Quality Systems Specialist Interview Questions and Answers [Updated 2025]
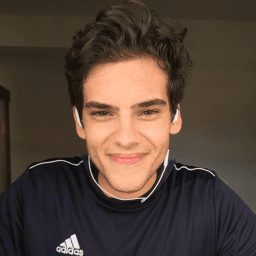
Andre Mendes
•
March 30, 2025
Are you preparing for a Quality Systems Specialist interview and eager to make a strong impression? This blog post is your ultimate guide, featuring a collection of the most common interview questions tailored for this pivotal role. Dive in to explore example answers and insightful tips on how to respond effectively, ensuring you're well-prepared and confident as you step into your interview.
Download Quality Systems Specialist Interview Questions in PDF
To make your preparation even more convenient, we've compiled all these top Quality Systems Specialistinterview questions and answers into a handy PDF.
Click the button below to download the PDF and have easy access to these essential questions anytime, anywhere:
List of Quality Systems Specialist Interview Questions
Behavioral Interview Questions
Can you give an example of a time when you implemented a quality improvement process? What was the outcome?
How to Answer
- 1
Choose a specific example from your past experience.
- 2
Describe the problem that needed improvement clearly.
- 3
Explain your specific role in the implementation process.
- 4
Focus on measurable results or positive outcomes achieved.
- 5
Use the STAR method: Situation, Task, Action, Result.
Example Answers
In my previous role at ABC Corp, we noticed an increase in customer complaints about product defects. I led a quality improvement initiative where we revised our inspection checklist. As a result, product defects dropped by 30% over the next quarter, significantly improving customer satisfaction.
Describe a situation where you led a team through a quality systems audit. What was your strategy, and what did you accomplish?
How to Answer
- 1
Use the STAR method: Situation, Task, Action, Result.
- 2
Describe your role clearly as the leader of the team.
- 3
Highlight specific strategies you implemented during the audit process.
- 4
Mention how you communicated and motivated the team.
- 5
Conclude with the positive outcomes or improvements achieved.],
- 6
sampleAnswers=[
Example Answers
In my previous role, I led a team through a successful ISO 9001 audit. I organized weekly prep meetings to review documentation and ensure everyone understood their responsibilities. By fostering open communication, we identified potential gaps and fixed them ahead of the audit. As a result, we passed the audit with zero non-conformances, which improved our quality certification status significantly.
Don't Just Read Quality Systems Specialist Questions - Practice Answering Them!
Reading helps, but actual practice is what gets you hired. Our AI feedback system helps you improve your Quality Systems Specialist interview answers in real-time.
Personalized feedback
Unlimited practice
Used by hundreds of successful candidates
Tell me about a time you had to work closely with other departments to implement a quality management system. How did you manage the collaboration?
How to Answer
- 1
Choose a specific project with clear objectives.
- 2
Highlight cross-departmental communication methods used.
- 3
Mention how you addressed challenges during collaboration.
- 4
Explain the outcomes or improvements achieved.
- 5
Reflect on what you learned from the experience.
Example Answers
In my previous role at ABC Corp, I led a project to implement a new quality management system across production and quality assurance teams. I organized weekly cross-department meetings to ensure alignment and shared updates. When conflicts arose, I facilitated discussions to find common ground. As a result, we reduced defect rates by 15% within three months.
Describe a time when there was a disagreement regarding a quality issue. How did you handle it?
How to Answer
- 1
Provide a specific example with a clear context.
- 2
Explain the differing viewpoints and why there was a disagreement.
- 3
Discuss the steps you took to resolve the issue with the team.
- 4
Highlight the outcome and any lessons learned.
- 5
Emphasize your skills in communication and collaboration.
Example Answers
In one project, the engineering team and I disagreed on the tolerance levels for a critical part. They believed the current tolerances were acceptable, but I found they were leading to defects. I organized a meeting to discuss the issue, presenting data from our quality checks. After discussing the pros and cons, we decided to adjust the tolerances. This collaboration improved our product quality and strengthened team relationships.
Can you talk about a time when you had to communicate difficult quality findings to executive management? How did you approach it?
How to Answer
- 1
Prepare by understanding the quality findings thoroughly
- 2
Use clear and straightforward language
- 3
Focus on the impact of the findings on the organization
- 4
Present possible solutions alongside the findings
- 5
Practice emotional intelligence to manage reactions
Example Answers
In my previous role, I discovered a significant quality issue affecting product reliability. I prepared a detailed report outlining the issue, its potential impacts on customer satisfaction, and presented it to the executive team. I also proposed an action plan to address the problem, which helped ease concerns and demonstrated our commitment to quality.
Give an example of a creative solution you developed to solve a quality system challenge.
How to Answer
- 1
Identify a specific quality issue you faced.
- 2
Explain the creative solution you implemented.
- 3
Highlight the impact of your solution on the quality system.
- 4
Use metrics or qualitative results to demonstrate success.
- 5
Be concise and focus on your role in the solution.
Example Answers
At my previous job, we had frequent errors in our QC reporting process. I created an automated reporting tool using Excel macros that reduced errors by 50% and saved our team 10 hours a week in manual data entry. This not only improved accuracy but also increased our productivity.
Describe a situation where your attention to detail made a significant impact on the quality outcome.
How to Answer
- 1
Think of a specific project where small details were crucial.
- 2
Outline the steps you took to ensure accuracy.
- 3
Explain the outcome and how it benefited the team or project.
- 4
Use quantifiable results if possible to illustrate the impact.
- 5
Keep it concise and focused on your role in the situation.
Example Answers
In a recent project audit, I noticed discrepancies in our data reporting. I took the initiative to review all reports against source documents. This attention to detail identified errors that could have led to financial misstatements. As a result, we corrected the reports, maintaining our compliance and saving the company from potential penalties.
What’s a major quality system project you managed, and how did you ensure it was executed successfully?
How to Answer
- 1
Choose a specific project that had clear quality system objectives.
- 2
Describe your role and key responsibilities in the project.
- 3
Explain the strategies you used to monitor progress and ensure compliance.
- 4
Highlight the results and improvements achieved after project completion.
- 5
Mention any challenges faced and how you overcame them.
Example Answers
I managed the implementation of a new quality management system for our manufacturing process. My role involved leading a cross-functional team to define quality objectives and establish benchmarks. We used regular project meetings to track progress. Ultimately, we reduced defects by 30% within six months.
Talk about a time when you had to manage multiple competing quality projects. How did you prioritize?
How to Answer
- 1
Identify the key projects and their impact on the organization.
- 2
Discuss how you assessed urgency versus importance.
- 3
Explain the criteria you used to prioritize tasks.
- 4
Mention any tools or methods you used for tracking progress.
- 5
Highlight the outcome and any lessons learned from the experience.
Example Answers
In my previous role, I had three quality improvement projects due at the same time. I first assessed their impact on compliance and customer satisfaction. I prioritized the project with the nearest deadline and highest risk. I used a prioritization matrix to visualize this. Ultimately, we met all deadlines and improved our quality scores.
Describe a time when you had to make a tough decision regarding a quality issue with limited information.
How to Answer
- 1
Use the STAR method: Situation, Task, Action, Result
- 2
Emphasize the impact of the quality issue on the project or product
- 3
Highlight your decision-making process and how you assessed risks
- 4
Mention any collaboration with team members or stakeholders
- 5
Conclude with the result and what you learned from the experience
Example Answers
In a previous role, we discovered a potential defect in a batch of products that were about to be shipped. The situation was critical as we had limited time to conduct thorough testing. I gathered the team quickly and assessed the data we had, while also considering the potential impact on our customers. I decided to halt the shipment and conduct a focused review. Ultimately, this decision saved our company from a significant recall and reinforced our quality standards. My proactive approach helped the team understand the importance of quality over speed.
Don't Just Read Quality Systems Specialist Questions - Practice Answering Them!
Reading helps, but actual practice is what gets you hired. Our AI feedback system helps you improve your Quality Systems Specialist interview answers in real-time.
Personalized feedback
Unlimited practice
Used by hundreds of successful candidates
Technical Interview Questions
What are the key elements of ISO 9001, and how have you applied them in your previous roles?
How to Answer
- 1
Identify the main principles of ISO 9001: customer focus, leadership, involvement of people, process approach, improvement, evidence-based decision making, relationship management.
- 2
Prepare specific examples from your experience that demonstrate these principles in action.
- 3
Highlight measurable outcomes of applying ISO 9001 elements in your work.
- 4
Be concise and relate your experience directly to the position you are applying for.
- 5
Show your understanding of how ISO 9001 can improve quality and efficiency.
Example Answers
In my previous role, I implemented a quality management system based on ISO 9001, focusing on customer feedback to enhance service delivery. This resulted in a 20% increase in customer satisfaction ratings.
How do you conduct a root cause analysis to address quality issues? Can you walk us through a specific example?
How to Answer
- 1
Identify the quality issue clearly with data and evidence.
- 2
Gather a team to brainstorm potential causes using techniques like the 5 Whys or Fishbone diagram.
- 3
Analyze data and conduct tests to confirm the root cause.
- 4
Develop corrective actions addressing the root cause.
- 5
Implement and monitor the effectiveness of the actions taken.
Example Answers
In my previous role, we had a recurring defect in one of our products. I first gathered data to confirm the issue's frequency. Then, I organized a team meeting where we used the Fishbone diagram to explore potential causes. After investigating, we discovered the defect was due to a specific machine calibration error. We recalibrated the machine and monitored the product quality, leading to a significant reduction in defects.
Don't Just Read Quality Systems Specialist Questions - Practice Answering Them!
Reading helps, but actual practice is what gets you hired. Our AI feedback system helps you improve your Quality Systems Specialist interview answers in real-time.
Personalized feedback
Unlimited practice
Used by hundreds of successful candidates
What is your approach to maintaining accurate documentation within a quality management system?
How to Answer
- 1
Regularly review and update documents to reflect current practices
- 2
Implement version control to track changes in documentation
- 3
Ensure all team members are trained on documentation standards
- 4
Conduct periodic audits to verify the accuracy of documents
- 5
Utilize a centralized document management system for easy access and control
Example Answers
I ensure accurate documentation by regularly reviewing and updating our procedures to match our current practices. I also implement version control, so every change is tracked, and everyone is trained on our documentation standards to avoid inconsistencies.
What is process validation, and why is it important in quality systems? Can you provide an example of how you've conducted it?
How to Answer
- 1
Define process validation clearly and mention its purpose.
- 2
Explain the importance of ensuring consistent quality and compliance with regulations.
- 3
Mention stages of process validation: installation qualification, operational qualification, and performance qualification.
- 4
Provide a specific example of a process you validated in a previous role.
- 5
Highlight the outcomes or benefits achieved from your validation efforts.
Example Answers
Process validation is the process of demonstrating that a manufacturing process consistently produces a product meeting its specifications. It is crucial for ensuring product quality and compliance with FDA regulations. In my previous role, I validated a sterile filtration process by first performing installation qualification to ensure equipment was installed correctly, then operational qualification to assess the operating conditions, and finally performance qualification to confirm it performs as intended. This validation reduced defects and improved customer satisfaction.
What process do you follow to implement corrective and preventive actions (CAPA) in a quality system?
How to Answer
- 1
Begin by defining the problem clearly and gathering data to understand its root cause.
- 2
Use tools like the 5 Whys or Fishbone Diagram to analyze the issue.
- 3
Develop a corrective action plan outlining steps to address the root cause.
- 4
Implement the corrective actions and monitor their effectiveness.
- 5
Document the process and review to identify areas for further improvement.
Example Answers
First, I identify the problem and collect relevant data to define it accurately. Then I apply tools like the 5 Whys to uncover the root cause. Based on this, I create a corrective action plan with specific steps to rectify the issue. After implementing these actions, I ensure to monitor their effectiveness and document everything for future review.
What quality management software tools are you familiar with, and how have you used them in the past?
How to Answer
- 1
Identify specific quality management tools you have used
- 2
Explain how you used each tool in particular projects
- 3
Mention any results or improvements due to the tools
- 4
Include collaboration aspects when applicable
- 5
Be concise and relate it to the role you're applying for
Example Answers
I am familiar with tools like Minitab and Qualityze. In my last project, I used Minitab for statistical analysis to identify process variations, which helped us reduce defects by 15%.
How do you ensure supplier excellence and quality compliance within the supply chain?
How to Answer
- 1
Establish clear quality standards and communicate them to suppliers
- 2
Conduct regular audits and assessments of supplier processes
- 3
Implement a performance measurement system for tracking supplier quality
- 4
Provide training and support to suppliers to enhance their quality practices
- 5
Develop strong relationships and open communication channels with suppliers
Example Answers
I ensure supplier excellence by establishing clear quality standards and conducting regular audits to assess their compliance. I also collaborate with suppliers, providing them with training to improve their practices.
How do you stay updated with the latest quality standards and industry regulations relevant to your role?
How to Answer
- 1
Subscribe to relevant industry journals and newsletters for regular updates.
- 2
Attend workshops and seminars on new quality standards.
- 3
Join professional organizations related to quality systems for networking and resources.
- 4
Participate in online courses or training sessions to deepen your knowledge.
- 5
Follow key influencers and organizations on social media for real-time information.
Example Answers
I subscribe to industry newsletters and follow quality standards organizations to stay informed about the latest regulations. Additionally, I attend at least two workshops a year to refine my expertise.
Can you explain how you use statistical process control (SPC) in quality management?
How to Answer
- 1
Start with a brief definition of SPC to establish understanding.
- 2
Mention specific tools such as control charts and their purpose in monitoring processes.
- 3
Give a concrete example of how you've applied SPC in a past role.
- 4
Discuss how SPC helps in identifying variations and maintaining process stability.
- 5
Conclude with the impact of SPC on quality improvement and decision making.
Example Answers
In my previous role, I used statistical process control (SPC) by implementing control charts to monitor the production line of our product. This allowed us to identify any variations in the process early on and correct them before they led to defects.
Can you walk me through your process for executing a quality audit from start to finish?
How to Answer
- 1
Start with a clear plan, identify the scope and objectives of the audit.
- 2
Gather relevant documents and historical data before the audit starts.
- 3
Conduct the audit by observing processes, interviewing personnel, and reviewing data.
- 4
Document findings precisely, noting any non-conformities and areas for improvement.
- 5
Conclude with an audit report and follow up on action items and corrections.
Example Answers
To execute a quality audit, I first plan the audit by defining its scope and objectives. Then, I gather all necessary documents like previous audit reports and quality manuals. During the audit, I observe processes and interview team members, documenting any findings meticulously. Finally, I generate a report summarizing the results and ensure follow-up on any issues identified.
Don't Just Read Quality Systems Specialist Questions - Practice Answering Them!
Reading helps, but actual practice is what gets you hired. Our AI feedback system helps you improve your Quality Systems Specialist interview answers in real-time.
Personalized feedback
Unlimited practice
Used by hundreds of successful candidates
Situational Interview Questions
Imagine you discover a significant non-conformance in the quality system. What steps would you take to address it?
How to Answer
- 1
First, assess the severity and impact of the non-conformance
- 2
Document the findings with relevant evidence and details
- 3
Notify relevant stakeholders and management promptly
- 4
Develop a corrective action plan to resolve the issue
- 5
Implement the plan and follow up to ensure compliance
Example Answers
Upon discovering a significant non-conformance, I would first assess its impact on the quality system by gathering data and understanding the potential risks. Then, I would document all findings clearly before notifying management and relevant stakeholders. Following this, I would work on a corrective action plan that addresses the root cause and ensures it does not recur. Finally, I would implement the plan and monitor the situation closely.
You are faced with a new regulatory requirement that impacts your quality systems. How would you ensure compliance?
How to Answer
- 1
Identify the specific regulatory requirement and its implications for existing quality systems
- 2
Engage with relevant stakeholders to gather insights and ensure mutual understanding
- 3
Develop an action plan that includes necessary changes to processes, documentation, and training
- 4
Implement the changes with a clear timeline and responsibilities assigned
- 5
Monitor compliance post-implementation and adjust the plan based on feedback and audits
Example Answers
First, I would thoroughly review the new regulatory requirement to understand what changes are needed. Next, I'd meet with the quality team and affected departments to discuss the impact. Then, I would create a detailed action plan to update our quality procedures and documents, ensuring that everyone is trained on the new requirements. Finally, I would set up a monitoring process to ensure compliance and make adjustments as necessary.
Don't Just Read Quality Systems Specialist Questions - Practice Answering Them!
Reading helps, but actual practice is what gets you hired. Our AI feedback system helps you improve your Quality Systems Specialist interview answers in real-time.
Personalized feedback
Unlimited practice
Used by hundreds of successful candidates
Suppose you need to prioritize multiple quality risks. How would you determine which one to address first?
How to Answer
- 1
Identify the potential impact of each risk on product quality and customer satisfaction
- 2
Assess the likelihood of each risk occurring based on current data
- 3
Consider regulatory compliance implications for each risk
- 4
Evaluate resources available to mitigate each risk
- 5
Prioritize based on a combination of impact, likelihood, and resources
Example Answers
I would first assess the impact of each risk on the product quality and how it affects customer satisfaction. Then I would look at the likelihood of each risk occurring. Next, I would factor in compliance issues and available resources to tackle the risks, ultimately prioritizing the one that poses the highest overall risk to our quality systems.
How would you approach developing a continuous improvement culture within a new team?
How to Answer
- 1
Encourage open communication by creating a safe space for ideas and feedback.
- 2
Implement regular team meetings to discuss improvement opportunities.
- 3
Utilize data and metrics to identify areas needing improvement.
- 4
Recognize and reward team members for contributions to process enhancements.
- 5
Provide training and resources on continuous improvement methodologies.
Example Answers
To develop a continuous improvement culture, I would start by fostering open communication, allowing team members to share their ideas freely. Regular meetings would be held to identify potential areas for improvement. We would use performance data to guide our discussions and celebrate contributions to enhancements.
You are informed of an upcoming internal audit. How would you prepare your team and the documentation?
How to Answer
- 1
Review previous audit findings and compliance requirements
- 2
Organize a team meeting to discuss expectations and roles
- 3
Conduct a mock audit to identify gaps in documentation
- 4
Ensure all relevant documents and records are updated and accessible
- 5
Communicate openly with the team about the importance of the audit
Example Answers
I would start by reviewing the previous audit findings and compliance requirements. Then, I'd hold a team meeting to clarify everyone's roles and responsibilities. A mock audit would help us assess our readiness and identify any gaps in our documentation before the real audit.
How would you manage and communicate a significant change to the quality management system to minimize resistance?
How to Answer
- 1
Engage stakeholders early by communicating the reasons for the change.
- 2
Provide clear and detailed plans on how the change will be implemented.
- 3
Offer training and support to ease the transition.
- 4
Solicit feedback and address concerns promptly to build trust.
- 5
Highlight the benefits of the change for the team and the organization.
Example Answers
To manage a significant change to the quality management system, I would first engage all stakeholders by explaining the rationale behind the change. Then, I would create a detailed implementation plan and ensure everyone receives the necessary training and support. I would regularly solicit feedback to understand concerns and reassure the team by emphasizing the benefits of the change.
A new employee joins your department. How would you ensure they are effectively trained in quality system procedures?
How to Answer
- 1
Develop a structured onboarding plan that includes all necessary procedures.
- 2
Pair the new employee with a mentor for hands-on training.
- 3
Utilize checklists and documentation to track training progress.
- 4
Conduct regular feedback sessions to address questions and concerns.
- 5
Incorporate practical scenarios to help them understand real-world applications.
Example Answers
I would create a detailed onboarding plan that outlines all quality system procedures and schedule training sessions. Pairing the new employee with an experienced mentor would facilitate hands-on learning, ensuring they grasp the essential processes.
How would you handle critical feedback from a customer regarding quality issues in your products?
How to Answer
- 1
Acknowledge the customer's feedback sincerely.
- 2
Ask clarifying questions to understand the issue fully.
- 3
Take responsibility for the quality issue and apologize if necessary.
- 4
Outline steps you will take to investigate and resolve the issue.
- 5
Follow up with the customer once the issue is addressed.
Example Answers
I would start by sincerely acknowledging the customer's feedback and thanking them for bringing it to my attention. Then, I would ask clarifying questions to fully understand the specifics of the quality issue they experienced. I would take responsibility and apologize for any inconvenience caused. After that, I would explain the steps I would take to resolve the issue, including involving the quality team. Finally, I would ensure to follow up with the customer after the resolution to confirm their satisfaction.
Imagine there’s an urgent quality defect discovered post-release. What immediate actions would you take?
How to Answer
- 1
Assess the severity and impact of the defect quickly.
- 2
Notify relevant stakeholders immediately about the issue.
- 3
Initiate a containment plan to stop further use of the defective product.
- 4
Gather a cross-functional team to investigate the root cause.
- 5
Document all findings and actions taken for future reference.
Example Answers
First, I'd assess how serious the defect is and its impact on users. Then, I'd alert the product team and senior management right away. Next, I'd implement a containment procedure to prevent further distribution until we resolve the issue. Finally, I would organize a meeting to investigate the root cause with key stakeholders.
If tasked with improving quality performance metrics, what initial steps would you take?
How to Answer
- 1
Analyze current quality metrics to identify trends and issues
- 2
Engage with stakeholders to understand their perceptions of quality
- 3
Conduct a root cause analysis of past quality issues
- 4
Set clear, measurable objectives for improvement
- 5
Implement a continuous feedback loop to monitor performance against metrics
Example Answers
First, I would analyze the existing quality performance metrics to pinpoint key areas that need improvement. Then, I would consult with relevant stakeholders to gather their insights on how quality impacts their work.
Don't Just Read Quality Systems Specialist Questions - Practice Answering Them!
Reading helps, but actual practice is what gets you hired. Our AI feedback system helps you improve your Quality Systems Specialist interview answers in real-time.
Personalized feedback
Unlimited practice
Used by hundreds of successful candidates
Quality Systems Specialist Position Details
Salary Information
Recommended Job Boards
These job boards are ranked by relevance for this position.
Related Positions
Ace Your Next Interview!
Practice with AI feedback & get hired faster
Personalized feedback
Used by hundreds of successful candidates
Ace Your Next Interview!
Practice with AI feedback & get hired faster
Personalized feedback
Used by hundreds of successful candidates