Top 30 Roller Mechanic Interview Questions and Answers [Updated 2025]
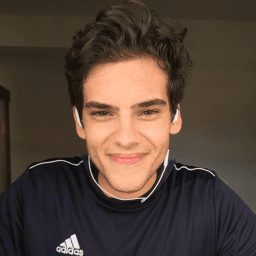
Andre Mendes
•
March 30, 2025
Preparing for a roller mechanic interview can be daunting, but we're here to help you succeed. In this blog post, we cover the most common interview questions for the roller mechanic role, paired with insightful example answers and effective answering tips. Whether you're a seasoned professional or new to the field, this guide will equip you with the confidence and knowledge needed to impress your interviewers.
Download Roller Mechanic Interview Questions in PDF
To make your preparation even more convenient, we've compiled all these top Roller Mechanicinterview questions and answers into a handy PDF.
Click the button below to download the PDF and have easy access to these essential questions anytime, anywhere:
List of Roller Mechanic Interview Questions
Behavioral Interview Questions
Can you describe a challenging repair project you handled and how you approached it?
How to Answer
- 1
Select a specific repair project that was particularly difficult.
- 2
Explain the problem you faced in detail and what made it challenging.
- 3
Describe the steps you took to diagnose and solve the issue.
- 4
Highlight what you learned from the experience and how it improved your skills.
- 5
Conclude with the positive outcome and any feedback received.
Example Answers
I worked on a roller coaster that had a persistent mechanical failure affecting safety. I diagnosed the issue by reviewing the system schematics and conducted a series of tests to pinpoint the malfunctioning component. I replaced a faulty gearbox, which was a complex task that required careful alignment. This project taught me the importance of thorough troubleshooting, and I received commendations for my attention to detail.
Tell me about a time you had to work closely with others on a roller maintenance task. What was your role?
How to Answer
- 1
Choose a specific example from your experience.
- 2
Emphasize teamwork and communication skills.
- 3
Clearly define your role and responsibilities.
- 4
Highlight the outcome of the task.
- 5
Mention any challenges faced and how you overcame them.
Example Answers
In my previous job, I worked on a roller coaster maintenance team where we needed to replace worn-out wheels. I coordinated with two other mechanics to remove the old wheels. My role was to ensure we had the right tools and that safety protocols were followed. We completed the task ahead of schedule and improved the ride's performance.
Don't Just Read Roller Mechanic Questions - Practice Answering Them!
Reading helps, but actual practice is what gets you hired. Our AI feedback system helps you improve your Roller Mechanic interview answers in real-time.
Personalized feedback
Unlimited practice
Used by hundreds of successful candidates
Have you ever had to train a new mechanic? How did you ensure they learned effectively?
How to Answer
- 1
Start with your experience training a new mechanic.
- 2
Mention specific methods you used to teach them.
- 3
Include any tools or resources you provided for learning.
- 4
Discuss how you assessed their understanding and skills.
- 5
Highlight the importance of patience and encouragement.
Example Answers
Yes, I trained a new mechanic recently by first introducing them to basic concepts, then using hands-on demonstrations. I provided them with manuals and online resources they could refer to. Regular check-ins helped assess their progress, and I made sure to encourage them throughout the process.
Describe a situation where you disagreed with a coworker on a maintenance procedure. How did you handle it?
How to Answer
- 1
Stay calm and listen to the coworker's perspective
- 2
Use specific examples to illustrate your disagreement
- 3
Suggest a compromise or a solution
- 4
Focus on the importance of safety and best practices
- 5
Emphasize teamwork and collaboration in resolving the issue
Example Answers
During a maintenance check, I disagreed with a coworker about the correct torque settings for a roller component. I calmly explained my reasoning based on manufacturer guidelines and offered to look it up together. We found that my settings were indeed correct, which helped us both learn from the situation while maintaining a positive working relationship.
Tell me about a time when you had to explain a complex mechanical issue to someone without a technical background.
How to Answer
- 1
Choose a specific example from previous experience.
- 2
Break down the complex issue into simple parts.
- 3
Use analogies to relate mechanical terms to everyday items.
- 4
Be patient and check for understanding during your explanation.
- 5
Focus on the impact of the issue and the solution.
Example Answers
In my last job, I had to explain a roller's hydraulic system failure to a manager who had no technical background. I broke it down by comparing the system to a bike pump, explaining how pressure works. I described the symptoms in clear terms and what we needed to do to fix it. I checked in with them to ensure they understood each step.
Describe a time when you had to learn a new skill or tool quickly to complete a roller repair.
How to Answer
- 1
Start by stating the specific skill or tool you needed to learn.
- 2
Explain the context or urgency of the repair situation.
- 3
Describe the steps you took to learn the new skill or tool quickly.
- 4
Mention any resources you used, like online tutorials or colleagues.
- 5
Conclude with the outcome of the repair and what you learned from the experience.
Example Answers
In my previous job, we had a roller with a malfunctioning hydraulic system. I needed to learn about hydraulic systems quickly to diagnose the issue. I watched tutorial videos online and consulted a colleague who had experience with hydraulics. Within a few hours, I successfully identified the problem and repaired it, which saved our team a significant amount of downtime.
Describe a project where you took the initiative to improve a process or procedure related to roller maintenance.
How to Answer
- 1
Think of a specific instance where you identified a problem in roller maintenance.
- 2
Explain the steps you took to address the issue, including any research or analysis.
- 3
Describe the outcome of your initiative and how it improved efficiency or safety.
- 4
Use quantifiable results if possible, such as time saved or reduced costs.
- 5
Keep your answer structured: Situation, Task, Action, Result (STAR method).
Example Answers
In my previous job, I noticed that our roller inspection process was taking too long. I analyzed the checklist we used and streamlined it by removing redundant checks. This reduced our inspection time by 30% and allowed us to schedule more maintenance sessions each week.
Can you provide an example of when you went above and beyond your regular duties as a roller mechanic?
How to Answer
- 1
Identify a specific situation where you took extra initiative
- 2
Include the actions you took beyond your normal responsibilities
- 3
Explain how your actions benefited the team or project
- 4
Use metrics or specific outcomes if possible
- 5
Keep the answer structured: Situation, Action, Result.
Example Answers
During a major project, the roller was malfunctioning and I stayed overtime to diagnose and repair it, preventing project delays and saving costs.
Discuss a significant challenge you faced in your career and how you overcame it.
How to Answer
- 1
Select a challenge relevant to mechanics or machinery.
- 2
Describe your specific role in addressing the challenge.
- 3
Explain the steps you took to solve the problem.
- 4
Highlight the results and what you learned from the experience.
- 5
Ensure your answer demonstrates problem-solving and technical skills.
Example Answers
In my previous job, we faced a major breakdown of the roller coaster's main lift mechanism. As the lead mechanic, I quickly diagnosed the issue as a faulty motor. I coordinated a team to replace it within 24 hours, minimizing downtime. The coaster was back running smoothly, and I learned the importance of teamwork under pressure.
Don't Just Read Roller Mechanic Questions - Practice Answering Them!
Reading helps, but actual practice is what gets you hired. Our AI feedback system helps you improve your Roller Mechanic interview answers in real-time.
Personalized feedback
Unlimited practice
Used by hundreds of successful candidates
Technical Interview Questions
What types of roller mechanisms have you worked on, and what are the key differences between them?
How to Answer
- 1
Identify specific types of roller mechanisms you've worked on
- 2
Mention key differences such as design, function, and maintenance
- 3
Provide examples of tasks you performed on each type
- 4
Highlight any relevant certifications or training
- 5
Be prepared to discuss how you troubleshoot common issues in each type
Example Answers
I have worked on hydraulic roller systems, gravity roller conveyors, and powered roller systems. Hydraulic rollers are typically used for heavy loads and rely on fluid power, while gravity rollers are simpler and rely on the slope for movement. Powered rollers, on the other hand, use electric motors to move items and require regular maintenance of the electrical components.
How do you diagnose a malfunction in a hydraulic roller system?
How to Answer
- 1
Start by visually inspecting the hydraulic lines for leaks or physical damage.
- 2
Check the hydraulic fluid level and condition; low or contaminated fluid can cause issues.
- 3
Test the pressure at different points in the system to identify where the drop occurs.
- 4
Listen for unusual noises coming from the system that can indicate mechanical failure.
- 5
Use diagnostic tools like a hydraulic pressure gauge to gather data for a more thorough analysis.
Example Answers
I first inspect the hydraulic lines for any visible leaks or damage. Then, I check the fluid levels to ensure there's enough clean fluid. After that, I test the pressure in various parts of the system to pinpoint any failures.
Don't Just Read Roller Mechanic Questions - Practice Answering Them!
Reading helps, but actual practice is what gets you hired. Our AI feedback system helps you improve your Roller Mechanic interview answers in real-time.
Personalized feedback
Unlimited practice
Used by hundreds of successful candidates
What tools do you consider essential for a roller mechanic, and why?
How to Answer
- 1
List specific tools relevant to roller mechanics
- 2
Explain the function of each tool briefly
- 3
Mention why each tool is important for the job
- 4
Include a mix of hand tools and power tools
- 5
Show knowledge of safety equipment as well
Example Answers
As a roller mechanic, I consider wrenches essential for tightening and loosening bolts quickly. A torque wrench helps ensure that bolts are tightened to the correct specifications, preventing mechanical failures. I also think having a multimeter is crucial for diagnosing electrical issues on roller systems.
What safety precautions do you take when working on heavy machinery like rollers?
How to Answer
- 1
Always inspect the machinery before use for any hazards.
- 2
Wear appropriate personal protective equipment such as gloves, goggles, and hearing protection.
- 3
Ensure that you are following lockout/tagout procedures before performing any maintenance.
- 4
Never work alone on heavy machinery; always have a buddy system in place.
- 5
Be aware of your surroundings and make sure the area is clear of bystanders.
Example Answers
I always start by inspecting the roller for any signs of wear or damage. I ensure that I'm wearing my PPE, including gloves and goggles. Before any maintenance, I follow the lockout/tagout procedure to prevent accidental start-up. I also make sure a colleague is around in case of emergencies.
What routine maintenance steps do you recommend for rollers to ensure optimal performance?
How to Answer
- 1
Inspect roller bearings regularly for wear or damage.
- 2
Maintain proper lubrication in all moving parts.
- 3
Check hydraulic fluid levels and replace as necessary.
- 4
Examine tires for wear and proper inflation.
- 5
Keep the machine clean and free of debris.
Example Answers
I recommend inspecting the roller bearings for any signs of wear or damage to prevent breakdowns.
Explain how you would assess and fix a problem with a roller's braking system.
How to Answer
- 1
Start with a visual inspection of the braking system for any obvious signs of wear or damage.
- 2
Test the brakes in a controlled environment to identify specific issues during operation.
- 3
Check the brake fluid level and condition, and refill or replace if necessary.
- 4
Inspect brake pads and rotors for wear, replacing them if they are below the minimum thickness.
- 5
Document all findings and repairs made for future reference.
Example Answers
First, I would visually inspect the braking system for any visible damage or leaks. Then, I would perform a test drive to evaluate the braking performance and listen for any unusual noises. After that, I'd check the brake fluid and inspect the pads and rotors, replacing any worn components as needed. Finally, I'd document the process.
What maintenance standards do you adhere to when working on rollers?
How to Answer
- 1
Mention specific industry standards you follow.
- 2
Include regular inspection procedures.
- 3
Discuss safety protocols related to maintenance.
- 4
Highlight the importance of documentation.
- 5
Explain how you keep up with manufacturer recommendations.
Example Answers
I adhere to ISO 9001 quality standards and conduct regular inspections every 50 hours of operation to ensure rollers are in optimum condition. I always follow safety protocols, using appropriate personal protective equipment, and I document all maintenance work thoroughly.
What understanding do you have of the different mechanical systems within a roller?
How to Answer
- 1
Identify the key mechanical systems in a roller such as the engine, drive system, and hydraulic systems.
- 2
Explain how these systems work together to ensure smooth operation.
- 3
Mention common issues that may arise in these systems and how they can be diagnosed.
- 4
Discuss the importance of regular maintenance for each system.
- 5
Use specific terminology relevant to roller mechanics to demonstrate knowledge.
Example Answers
I understand that rollers have several key mechanical systems, including the engine, which powers the machine, the hydraulic system that controls movement and vibratory functions, and the drive system that connects everything. Regular maintenance is crucial to avoid issues like hydraulic leaks or engine overheating, and I can diagnose problems by checking fluid levels and looking for unusual noises.
How familiar are you with the electrical systems in modern rollers and their troubleshooting?
How to Answer
- 1
Highlight any formal training or certifications related to electrical systems.
- 2
Mention specific models of rollers you haveExperience with.
- 3
Discuss common electrical issues you haveTroubleshot in the past.
- 4
Provide examples of successful repairs or diagnostics.
- 5
Show your willingness to learn about new technologies in roller mechanics.
Example Answers
I have completed a technical training program focused on electrical systems for construction machinery, including rollers. In my last job, I regularly troubleshot electrical issues in a Volvo roller, such as wiring faults and sensor malfunctions, successfully implementing repairs that improved machine performance.
How do you conduct performance testing on rollers after repairs?
How to Answer
- 1
Start with a visual inspection for any obvious issues.
- 2
Check hydraulic systems for leaks and proper pressure.
- 3
Conduct a test run at various speeds and loads.
- 4
Listen for unusual noises during operation.
- 5
Document results and compare them with pre-repair benchmarks.
Example Answers
I begin by visually inspecting the rollers to ensure there are no obvious defects. Next, I check the hydraulic systems for leaks and confirm pressure levels. After that, I conduct a test run by operating the rollers at different speeds and under various loads. During this test, I pay close attention to any unusual noises. Finally, I document all my findings for review.
Don't Just Read Roller Mechanic Questions - Practice Answering Them!
Reading helps, but actual practice is what gets you hired. Our AI feedback system helps you improve your Roller Mechanic interview answers in real-time.
Personalized feedback
Unlimited practice
Used by hundreds of successful candidates
Situational Interview Questions
If you are assigned multiple roller repairs with tight deadlines, how would you prioritize your work?
How to Answer
- 1
Assess the severity and complexity of each repair
- 2
Identify which repairs have the closest deadlines
- 3
Communicate with your team or supervisor about workload
- 4
Start with the repair that impacts operations most
- 5
Keep track of progress and adjust priorities as needed
Example Answers
I would first evaluate each roller repair by its urgency and difficulty. I'd prioritize the ones with the nearest deadlines or those that directly impact our operation. Keeping my supervisor informed would help if I need to shift focus based on any changes.
If you encounter a roller that keeps breaking down unexpectedly, what steps would you take to troubleshoot the issue?
How to Answer
- 1
Identify the frequency and nature of the breakdowns
- 2
Check the most critical systems: engine, hydraulics, and electrical
- 3
Review the maintenance records and previous issues
- 4
Perform a visual inspection for loose or damaged components
- 5
Test the roller under different conditions to replicate the issue.
Example Answers
I would start by noting how often the roller is breaking down and what specific symptoms are occurring. Then, I would check the engine, hydraulic systems, and electrical connections for any obvious faults. I’d look at prior maintenance logs to see if this is a recurring problem and inspect for any signs of wear or damage.
Don't Just Read Roller Mechanic Questions - Practice Answering Them!
Reading helps, but actual practice is what gets you hired. Our AI feedback system helps you improve your Roller Mechanic interview answers in real-time.
Personalized feedback
Unlimited practice
Used by hundreds of successful candidates
A client is unhappy with the performance of a roller you recently repaired. How would you address their concerns?
How to Answer
- 1
Acknowledge the client's concerns openly
- 2
Ask for specific details about the issues they are experiencing
- 3
Offer to inspect the roller personally to identify the problem
- 4
Communicate your plan for resolving the issue promptly
- 5
Follow up with the client after the repair to ensure satisfaction
Example Answers
I would start by listening actively to the client's concerns and ask them to describe the performance issues they are facing. This way, I can identify if it’s a minor fix or something that needs more attention. After understanding the problem, I would schedule a time to inspect the roller and make any necessary repairs as soon as possible. I would also keep the client updated throughout the process to ensure their expectations are managed.
What would you do if a roller suddenly fails during operation, posing a safety risk?
How to Answer
- 1
Immediately stop the operation of the roller to prevent further risk.
- 2
Assess the situation to identify the type of failure and potential hazards.
- 3
Notify the appropriate personnel or supervisor about the incident.
- 4
Follow established safety protocols for equipment failure.
- 5
Document the incident for future reference and analysis.
Example Answers
If a roller fails during operation, I would first stop the machine to avoid any accidents. Then, I would quickly assess the issue to determine the cause of the failure. I would notify my supervisor to ensure we follow the safety procedures in place. After handling the immediate situation, I would document what happened to help with future prevention.
You notice that a particular replacement part often fails in rollers. What would you do?
How to Answer
- 1
Investigate the failure mode to understand why it fails.
- 2
Check if the part's specifications match the application requirements.
- 3
Consult with colleagues or suppliers for insights on common issues.
- 4
Consider alternative parts with better durability.
- 5
Document your findings and suggest improvements to management.
Example Answers
I would first analyze the failure mode to see if there's a pattern in when and how the part fails. After that, I'd compare its specifications to the requirements of the rollers to ensure it's suitable.
How would you handle a situation where a coworker is not following safety protocols while operating rollers?
How to Answer
- 1
Stay calm and assess the situation before reacting.
- 2
Approach your coworker privately to discuss your concerns.
- 3
Emphasize the importance of safety for everyone involved.
- 4
Offer to help them understand the protocols better if needed.
- 5
If the behavior continues, report the issue to a supervisor.
Example Answers
I would first ensure that there is no immediate danger. Then, I would talk to my coworker privately, express my concerns about safety, and remind them about the protocols. If the behavior persisted, I would involve a supervisor to address the issue.
If you are running low on specific replacement parts, how would you approach the repair task?
How to Answer
- 1
Identify the critical parts needed for the repair
- 2
Check for alternative solutions or temporary fixes
- 3
Communicate with your team or supervisor about the parts shortage
- 4
Source parts from local suppliers or distributors if possible
- 5
Document the issue for future reference and procurement needs
Example Answers
I would first identify which critical replacement parts are low and see if any alternative parts can be used. I would then inform my supervisor of the situation and look for local suppliers to get the necessary parts quickly.
How would you handle a situation where a customer is inquiring about the technical specifications of a roller repair?
How to Answer
- 1
Listen carefully to the customer's question
- 2
Clarify any ambiguous terms if needed
- 3
Provide clear and concise specifications
- 4
Use layman's terms for complex concepts
- 5
Offer to send additional information if required
Example Answers
I would listen closely to the customer and make sure I understand their question. Then, I would explain the technical specifications in simple terms, like saying the weight capacity and engine type, avoiding jargon. If needed, I would also offer to follow up with more detailed documents after our call.
How would you handle a situation where a team member is not pulling their weight on a collaborative repair job?
How to Answer
- 1
Communicate directly with the team member to understand their situation
- 2
Share your observations regarding their lack of contribution
- 3
Suggest a division of tasks to clarify responsibilities
- 4
Encourage teamwork by offering support if they are struggling
- 5
Involve a supervisor only if the issue persists and affects the job
Example Answers
I would first speak with the team member privately to find out if there's an issue affecting their performance. If they are facing challenges, I would offer to help or suggest a clearer division of tasks.
You are faced with a roller that has an unusual problem that you have not encountered before. Walk me through your process.
How to Answer
- 1
Start by defining the problem clearly and gathering all relevant information.
- 2
Use your knowledge and experience to rule out common issues first.
- 3
Consult technical manuals or manufacturer guidelines for insights.
- 4
If available, seek advice from colleagues or online forums with similar issues.
- 5
Develop a step-by-step troubleshooting plan to isolate and resolve the issue.
Example Answers
First, I would clearly define the symptoms of the roller's problem and collect all relevant information such as operation logs. Next, I would check for common issues like oil levels or filter clogs. If those don’t resolve it, I would refer to the service manual to look for less common problems and possible solutions. If I'm still stuck, I would reach out to a colleague or industry contacts for advice. Finally, I'd document each step of my troubleshooting to ensure thoroughness.
Don't Just Read Roller Mechanic Questions - Practice Answering Them!
Reading helps, but actual practice is what gets you hired. Our AI feedback system helps you improve your Roller Mechanic interview answers in real-time.
Personalized feedback
Unlimited practice
Used by hundreds of successful candidates
Roller Mechanic Position Details
Recommended Job Boards
ZipRecruiter
www.ziprecruiter.com/Jobs/Roller-MechanicThese job boards are ranked by relevance for this position.
Related Positions
- Tool Mechanic
- Production Mechanic
- Industrial Mechanic
- Conveyor Mechanic
- Machine Repairer
- Rig Mechanic
- Sewing Machine Mechanic
- Pump Mechanic
- Laundry Machine Mechanic
- Scale Mechanic
Similar positions you might be interested in.
Ace Your Next Interview!
Practice with AI feedback & get hired faster
Personalized feedback
Used by hundreds of successful candidates
Ace Your Next Interview!
Practice with AI feedback & get hired faster
Personalized feedback
Used by hundreds of successful candidates