Top 28 Scale Mechanic Interview Questions and Answers [Updated 2025]
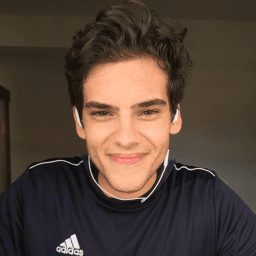
Andre Mendes
•
March 30, 2025
Navigating the interview process for a Scale Mechanic position can be daunting, but we're here to ease your journey. In this updated guide, we delve into the most common interview questions for this specialized role, providing you with example answers and insightful tips on how to respond with confidence and clarity. Equip yourself with the knowledge to leave a lasting impression and secure your dream job.
Download Scale Mechanic Interview Questions in PDF
To make your preparation even more convenient, we've compiled all these top Scale Mechanicinterview questions and answers into a handy PDF.
Click the button below to download the PDF and have easy access to these essential questions anytime, anywhere:
List of Scale Mechanic Interview Questions
Behavioral Interview Questions
Can you describe a time when you had to troubleshoot a significant issue with a scale? What steps did you take to resolve it?
How to Answer
- 1
Identify the specific problem with the scale.
- 2
Explain what initial steps you took to diagnose the issue.
- 3
Describe any testing or adjustments made during troubleshooting.
- 4
Mention any collaboration with team members or experts.
- 5
Conclude with the outcome and what you learned from the experience.
Example Answers
In my previous role, the scale was giving inaccurate readings. I first checked the calibration and discovered it was off. I recalibrated and ran multiple tests to ensure accuracy. I consulted my supervisor for additional insights, and we found a worn-out part that needed replacement. After the fix, the scale worked perfectly, and I learned the importance of regular maintenance checks.
Tell me about an instance where your attention to detail helped you avoid a major mistake in your work as a mechanic.
How to Answer
- 1
Think of a specific situation where details were critical.
- 2
Describe the potential issue you avoided due to your vigilance.
- 3
Explain the steps you took to ensure accuracy.
- 4
Highlight the positive outcome resulting from your attention to detail.
- 5
Keep your answer structured with a clear beginning, middle, and end.
Example Answers
Once, while working on a customer's engine, I noticed a slight misalignment in the timing belt. By double-checking my measurements, I avoided a potential engine failure that could have cost the customer thousands in repairs.
Don't Just Read Scale Mechanic Questions - Practice Answering Them!
Reading helps, but actual practice is what gets you hired. Our AI feedback system helps you improve your Scale Mechanic interview answers in real-time.
Personalized feedback
Unlimited practice
Used by hundreds of successful candidates
Describe a situation where you worked as part of a team to complete a project involving scale maintenance or repair. What was your role?
How to Answer
- 1
Focus on a specific project and your contribution to it
- 2
Highlight collaboration with team members and communication strategies used
- 3
Mention any challenges faced and how the team overcame them
- 4
Include the outcome and what you learned from the experience
- 5
Use specific terminology related to scale maintenance or repair
Example Answers
In my previous job, I collaborated with a team to repair a series of industrial scales. I was responsible for diagnosing specific calibration issues. We held daily check-ins and shared our findings, which facilitated quick problem-solving. We eventually restored all scales to full functionality ahead of schedule, improving productivity by 20%. This taught me the importance of clear communication.
Can you provide an example of how you adapted to a sudden change in work plans or environment while working on scales?
How to Answer
- 1
Identify a specific situation where plans changed unexpectedly
- 2
Explain your initial reaction and how you assessed the new situation
- 3
Describe the steps you took to adapt to the new circumstances
- 4
Highlight any positive outcomes from your adaptability
- 5
Keep your answer focused on your problem-solving and flexibility
Example Answers
During a routine calibration of scales, I was informed that the specifications had changed last minute. I quickly reviewed the new requirements, adjusted my calibration processes, and completed the task on time. This not only ensured compliance but also increased the accuracy of our measurements.
Describe a situation where you had to lead a team in a scale repair project. What challenges did you face?
How to Answer
- 1
Start with the context and objective of the project.
- 2
Briefly explain your role as the team leader.
- 3
Identify specific challenges you encountered.
- 4
Describe the solutions you implemented to overcome those challenges.
- 5
Conclude with the outcome and what you learned.
Example Answers
In a recent scale repair project for a manufacturing facility, I led a team of five. We faced a major challenge when a key component arrived damaged, delaying our timeline. I organized a quick meeting to brainstorm solutions, and we sourced a replacement part, which we obtained faster than expected. The project was completed on time, enhancing our production efficiency by 20%.
Have you ever trained or mentored someone in the role of a Scale Mechanic? What was your approach?
How to Answer
- 1
Highlight specific mentoring experiences you had in the past
- 2
Describe the methods you used to train, like hands-on demonstrations
- 3
Mention any resources or materials that helped facilitate the training
- 4
Emphasize the outcomes, such as improvements in skills or confidence
- 5
Show your adaptability to different learning styles during training
Example Answers
I mentored a junior mechanic by first providing hands-on demonstrations of scale calibration. I created a checklist that detailed each step in the process, which helped him follow along. Over time, he became confident and improved his efficiency.
Can you provide an example of how you effectively managed your time during a busy period with multiple scale repairs?
How to Answer
- 1
Prioritize tasks based on urgency and impact
- 2
Use a scheduling tool to allocate time blocks
- 3
Communicate with team members to delegate when needed
- 4
Reflect on past experiences to identify what worked well
- 5
Stay flexible to adjust the plan as new issues arise
Example Answers
During a busy month, I prioritized repairs by urgency, addressing critical scale malfunctions first. I used a shared calendar to allocate specific time blocks for each repair, ensuring a clear overview of my workload.
Describe your experience with quality control processes in relation to scale accuracy and reliability.
How to Answer
- 1
Highlight specific quality control standards you have implemented.
- 2
Mention any calibration methods you used to ensure scale accuracy.
- 3
Discuss how you handled discrepancies in measurements.
- 4
Provide examples of documentation you maintained for quality processes.
- 5
Emphasize the importance of regular maintenance and inspections.
Example Answers
In my previous role, I implemented ISO 9001 quality standards for our scales. I conducted regular calibrations using certified weights, which helped us maintain accuracy within 0.01 grams. If discrepancies arose, I quickly analyzed the data and recalibrated the scales, ensuring reliability.
Don't Just Read Scale Mechanic Questions - Practice Answering Them!
Reading helps, but actual practice is what gets you hired. Our AI feedback system helps you improve your Scale Mechanic interview answers in real-time.
Personalized feedback
Unlimited practice
Used by hundreds of successful candidates
Technical Interview Questions
What methods do you use for calibrating different types of scales, and how do you ensure accuracy?
How to Answer
- 1
Identify the type of scale you are calibrating.
- 2
Describe the specific calibration method used for that type.
- 3
Mention the use of certified weights for ensuring precision.
- 4
Explain how you perform regular checks and maintenance.
- 5
Highlight any software or tools used for calibration tracking.
Example Answers
For electronic scales, I use a two-point calibration method with certified weights. I perform checks every month to ensure accuracy and utilize software to log calibration data.
What diagnostic tools and techniques do you prefer to use when identifying issues with scales?
How to Answer
- 1
Mention specific diagnostic tools you have experience with
- 2
Explain how you use these tools in the diagnostic process
- 3
Include techniques for troubleshooting issues systematically
- 4
Highlight any relevant certifications or training in diagnostics
- 5
Share a brief example of resolving an issue using these tools
Example Answers
I prefer using multimeters and calibration equipment to diagnose scale issues. I often start with a multimeter to check for electrical faults and follow up with calibration tests to ensure accuracy. For systematic troubleshooting, I document each step to track potential problems. My training includes certification in electronics, which adds to my efficiency in this role.
Don't Just Read Scale Mechanic Questions - Practice Answering Them!
Reading helps, but actual practice is what gets you hired. Our AI feedback system helps you improve your Scale Mechanic interview answers in real-time.
Personalized feedback
Unlimited practice
Used by hundreds of successful candidates
Can you explain your approach to performing routine maintenance on mechanical scales?
How to Answer
- 1
Start with a checklist of maintenance tasks.
- 2
Inspect the scale for visible wear or damage.
- 3
Calibrate the scale regularly to ensure accuracy.
- 4
Lubricate moving parts as needed to avoid friction.
- 5
Document maintenance actions for future reference.
Example Answers
I approach maintenance by first following a checklist that includes inspecting for wear, calibrating the scale, and lubricating moving parts. Regular documentation ensures all actions are recorded.
What experience do you have working with the electrical components of electronic scales?
How to Answer
- 1
Briefly outline relevant education or training in electronics.
- 2
Mention specific work experience with electronic scales or similar devices.
- 3
Highlight your skills in troubleshooting and repairing electrical components.
- 4
Discuss any relevant certifications or courses you've completed.
- 5
Be ready to give examples of how you’ve solved scale-related issues.
Example Answers
I have a diploma in electronics where I learned about circuit design. I've worked for two years at a scale manufacturing company, where I repaired and calibrated various models of electronic scales. I also hold a certification in electrical troubleshooting.
What are the key measurement standards you follow when working on scales, and why are they important?
How to Answer
- 1
Identify key standards such as NIST, ISO, or OIML that are relevant to scales.
- 2
Explain how these standards ensure accuracy and reliability in measurements.
- 3
Discuss the importance of regular calibration and maintenance of scales.
- 4
Mention any software or tools you use to monitor compliance with these standards.
- 5
Emphasize how adherence to standards enhances customer trust and product quality.
Example Answers
I follow NIST and ISO standards for scales because they ensure consistent accuracy. Regular calibration is crucial because it helps maintain measurement integrity and builds client trust.
What systematic approach do you take to troubleshoot issues with weight measurement systems?
How to Answer
- 1
Begin by defining the problem clearly and gathering relevant data.
- 2
Identify potential sources of error, such as calibration, environmental impacts, or equipment malfunctions.
- 3
Test components systematically, starting from the least to most complex.
- 4
Document findings at each step for future reference and learning.
- 5
Communicate results clearly to team members and propose solutions based on your findings.
Example Answers
First, I clearly define the issue by reviewing the weight readings and identifying anomalies. Then, I check the calibration of the scale and explore possible environmental factors affecting measurements. I conduct tests on each component progressively, documenting my findings and discussing them with the team to align on solutions.
How do you assess and implement upgrades or modifications to existing scale systems?
How to Answer
- 1
Identify current system limitations through data analysis and user feedback
- 2
Research latest technologies and industry best practices for potential enhancements
- 3
Develop a clear upgrade plan outlining objectives, timelines, and resources needed
- 4
Involve relevant stakeholders in the decision-making process for buy-in
- 5
Implement changes in phases, allowing for testing and adjustments along the way
Example Answers
To assess upgrades, I first analyze user feedback and system performance metrics to identify limitations. Then, I research new technologies that align with our goals. After creating an upgrade plan with timelines, I involve the team for feedback before implementing changes in phases to ensure smooth integration.
What software tools are you familiar with that aid in the calibration and maintenance of scales?
How to Answer
- 1
List specific software tools you have used.
- 2
Mention your experience with calibration management systems.
- 3
Highlight your familiarity with data analysis tools related to scale performance.
- 4
Include any software used for troubleshooting or diagnostics.
- 5
Express your ability to learn new software quickly.
Example Answers
I have experience with software like Calibration Manager for tracking calibration schedules and results, and I frequently use Excel for analyzing scale data. Additionally, I'm familiar with diagnostic tools like ScaleSoft for troubleshooting.
Situational Interview Questions
If you find that a scale is underreporting weight measurements, what steps would you take to identify and fix the problem?
How to Answer
- 1
Check calibration of the scale with known weights to verify accuracy.
- 2
Inspect the scale for any physical damage or wear that could affect performance.
- 3
Clean the scale and remove any debris that might interfere with weight readings.
- 4
Evaluate the environment for factors like vibration or uneven surfaces impacting readings.
- 5
Consult the manufacturer’s guidelines for troubleshooting and potential firmware updates.
Example Answers
I would start by calibrating the scale using standard weights to ensure it's measuring accurately. If it still underreports, I'd look for any signs of wear or damage on the scale.
Imagine you're faced with a tight deadline to fix a malfunctioning scale. How would you prioritize the tasks at hand?
How to Answer
- 1
Identify the specific issue causing the malfunction.
- 2
Assess the severity of the issue and its impact on operations.
- 3
Prioritize tasks based on urgency and resources available.
- 4
Communicate any necessary updates to stakeholders.
- 5
Document the issue and the solution for future reference.
Example Answers
First, I would identify the malfunction's cause, then assess its impact on operations. Next, I would prioritize fixing the most critical components first, communicate with my team about progress, and document everything for future reference.
Don't Just Read Scale Mechanic Questions - Practice Answering Them!
Reading helps, but actual practice is what gets you hired. Our AI feedback system helps you improve your Scale Mechanic interview answers in real-time.
Personalized feedback
Unlimited practice
Used by hundreds of successful candidates
A client is frustrated because their scale isn't functioning correctly. How would you approach this situation to ensure their concerns are addressed?
How to Answer
- 1
Listen carefully to the client's concerns without interrupting.
- 2
Ask specific questions to understand the scale's issues.
- 3
Provide reassurance that the problem will be resolved.
- 4
Outline the steps you will take to address the issue.
- 5
Follow up to ensure the solution meets the client's needs.
Example Answers
I would first listen to the client to understand exactly what is wrong with the scale. Then I would ask questions to clarify the issue before assuring them that I will resolve it. After identifying the root cause, I would explain the steps I'm taking to fix it and follow up to confirm their satisfaction with the solution.
If you implemented a repair that didn't hold and the scale failed again shortly after, how would you handle it?
How to Answer
- 1
Acknowledge the issue and take responsibility for the failure.
- 2
Assess the root cause of why the repair didn't hold.
- 3
Communicate promptly with your supervisor about the failure.
- 4
Propose a new solution with adjustments based on your assessment.
- 5
Document the process and learnings for future reference.
Example Answers
I would first acknowledge that the repair did not hold and take responsibility. Then, I'd investigate the root cause to understand why it failed. After that, I would inform my supervisor about the situation and propose a revised solution based on my findings. Finally, I would document the incident to help prevent similar issues in the future.
You are working with limited tools and resources to fix a scale. How would you improvise to complete the task?
How to Answer
- 1
Assess the tools and materials available to identify possible solutions
- 2
Break down the problem into smaller parts to focus on specific issues
- 3
Think creatively about alternative uses for existing items
- 4
Prioritize safety to avoid further damage or hazards
- 5
Test the improvisation with caution before full implementation
Example Answers
I would first assess the available tools like screwdrivers or tape. Next, I'd isolate the problem part of the scale, perhaps the calibration mechanism. I might use tape to hold a loose part temporarily while I adjust settings to see if it works correctly before finalizing my fix.
How would you collaborate with other departments, like production or quality assurance, to ensure scale accuracy?
How to Answer
- 1
Establish consistent communication channels with production and quality assurance teams.
- 2
Schedule regular meetings to discuss scale performance and issues.
- 3
Create shared documentation for scale calibration procedures and results.
- 4
Implement checks and balances where both departments validate scale accuracy.
- 5
Encourage feedback loops to improve processes based on real-world application.
Example Answers
I would set up weekly meetings with production and quality assurance to review scale data and address any issues. This collaboration ensures everyone is aligned on scale accuracy and reliability.
In the event of a scale breaking down during a critical measurement period, what immediate actions would you take?
How to Answer
- 1
Assess the situation to confirm the scale is indeed broken
- 2
Notify relevant team members about the breakdown
- 3
Determine if any backup equipment is available for immediate use
- 4
Document the issue and steps taken for future reference
- 5
Follow up on repairs or maintenance after the immediate crisis is handled
Example Answers
First, I would check the scale to confirm it’s non-functional. Then, I'd notify my supervisor and any team members affected. If there's a backup scale available, I'd switch to that for the measurements. I would also document the breakdown and my steps. Afterward, I'd ensure the broken scale is scheduled for repair.
If a particular model of scale had a known recurring issue, how would you approach resolving that challenge for future work?
How to Answer
- 1
Identify the specific issue and gather data on its occurrences
- 2
Collaborate with the team to brainstorm potential solutions
- 3
Test proposed solutions in a controlled environment before full implementation
- 4
Document the findings and adjustments clearly for future reference
- 5
Establish a feedback loop to monitor the effectiveness of the solution
Example Answers
I would first analyze the data on the recurring issue to understand its frequency and impact. Then, I'd work with the team to brainstorm effective solutions and run tests on the best ideas. After implementing a solution, I'd document the process and ensure ongoing feedback to refine the approach.
If you discovered a more efficient method for calibrating scales, how would you propose this change to your superiors?
How to Answer
- 1
Gather data and evidence to support your method
- 2
Consider the potential benefits and risks of the new method
- 3
Prepare a clear and concise presentation
- 4
Suggest a pilot test to demonstrate effectiveness
- 5
Be open to feedback and ready to discuss adjustments
Example Answers
I would start by collecting data that shows the efficiency gains of the new calibration method. Then, I would create a presentation outlining the benefits and suggest a small pilot test to demonstrate the improvements.
Scale Mechanic Position Details
Recommended Job Boards
CareerBuilder
www.careerbuilder.com/jobs/scale-mechanicZipRecruiter
www.ziprecruiter.com/Jobs/Scale-Mechanic/These job boards are ranked by relevance for this position.
Related Positions
- Tool Mechanic
- Production Mechanic
- Industrial Mechanic
- Industrial Maintenance Mechanic
- Machine Repairer
- Roller Mechanic
- Machine Fixer
- Conveyor Mechanic
- Deck Mechanic
- Sewing Machine Mechanic
Similar positions you might be interested in.
Ace Your Next Interview!
Practice with AI feedback & get hired faster
Personalized feedback
Used by hundreds of successful candidates
Ace Your Next Interview!
Practice with AI feedback & get hired faster
Personalized feedback
Used by hundreds of successful candidates