Top 30 Technical Operator Interview Questions and Answers [Updated 2025]
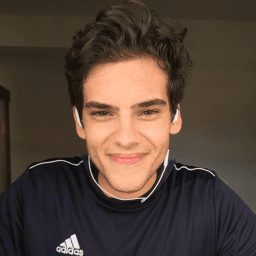
Andre Mendes
•
March 30, 2025
Navigating the competitive landscape of technical operator job interviews can be daunting, but preparation is key. This blog post compiles the most common interview questions for the Technical Operator role, complete with example answers and insightful tips on how to respond effectively. Whether you're a seasoned professional or new to the field, this guide will help you confidently tackle your next interview with ease.
Download Technical Operator Interview Questions in PDF
To make your preparation even more convenient, we've compiled all these top Technical Operatorinterview questions and answers into a handy PDF.
Click the button below to download the PDF and have easy access to these essential questions anytime, anywhere:
List of Technical Operator Interview Questions
Behavioral Interview Questions
Describe a time when you had to work closely with a team to complete a technical project. What was your role, and how did the team perform?
How to Answer
- 1
Choose a specific project that highlights your teamwork and technical skills.
- 2
Clearly explain your role and what responsibilities you had.
- 3
Discuss how the team collaborated and how you contributed to the overall success.
- 4
Mention any challenges faced and how the team overcame them.
- 5
Conclude with the outcome of the project and what you learned from the experience.
Example Answers
In my last role, I worked on a project to upgrade our network infrastructure. I was the lead technician responsible for configuring new routers. My team and I held weekly meetings to discuss our progress. We faced issues with compatibility, but we worked collaboratively to troubleshoot and ultimately completed the project on time, improving network performance by 30%.
Can you give an example of a conflict you faced while working on a technical operation? How did you resolve it?
How to Answer
- 1
Identify a specific conflict from your experience.
- 2
Explain the context and the parties involved.
- 3
Describe the steps you took to resolve the conflict.
- 4
Emphasize the outcome and what you learned.
- 5
Keep the focus on your role in resolving the issue.
Example Answers
In a previous project, my team was divided over which software tool to use for data analysis. I organized a meeting where each side presented their case, facilitated the discussion to focus on the project's goals, and we ultimately agreed to combine features from both tools, which improved our efficiency. This taught me the importance of collaborative decision-making.
Don't Just Read Technical Operator Questions - Practice Answering Them!
Reading helps, but actual practice is what gets you hired. Our AI feedback system helps you improve your Technical Operator interview answers in real-time.
Personalized feedback
Unlimited practice
Used by hundreds of successful candidates
Tell me about a time when you had to quickly adapt to a change in the technical specifications of a project. How did you manage it?
How to Answer
- 1
Choose a specific instance where a change occurred
- 2
Explain what the change was and why it was necessary
- 3
Describe how you assessed the impact of the change
- 4
Discuss the steps you took to adapt to the new specifications
- 5
Highlight the positive outcome of your adaptability
Example Answers
In my last project, the client changed the software requirements just a week before launch. I quickly set up a meeting with the team to assess the impact, reorganized our task priorities, and we worked overtime to implement the new features. We successfully delivered the project on time, and the client was very pleased with the results.
Describe a situation where you had to communicate complex technical information to a non-technical team member. How did you ensure they understood?
How to Answer
- 1
Identify the technical concept you needed to explain
- 2
Use analogies or simple terms to relate it to their knowledge
- 3
Encourage questions to clarify their understanding
- 4
Provide visual aids if possible, like diagrams or charts
- 5
Summarize the key points at the end to reinforce understanding
Example Answers
In my previous role, I had to explain the process of network security to a marketing team member. I compared it to locking the doors of a store and used simple terms. I asked if they had questions throughout, and I used a diagram to illustrate the concept. At the end, I summarized by saying that just like a store needs security to protect its goods, our network needs measures to protect its data.
Provide an example of when you identified a technical improvement in your previous role. What was the impact?
How to Answer
- 1
Describe the specific technical issue you noticed.
- 2
Explain the solution you proposed or implemented.
- 3
Include any tools or methods used in your improvement.
- 4
Quantify the impact on efficiency or productivity when possible.
- 5
Mention any feedback received from your team or management.
Example Answers
In my last role, I noticed that our data backup process was taking too long, which risked data loss. I researched and proposed switching to an incremental backup strategy, which reduced the backup time by 60%. This allowed our team to access data quicker, and management appreciated the improved data security.
Tell me about a time you improved the quality of the technical operations process. What steps did you take?
How to Answer
- 1
Choose a specific example from your experience.
- 2
Describe the initial problem with the process.
- 3
Explain the steps you took to improve it.
- 4
Share the measurable outcomes or results.
- 5
Wrap up by reflecting on what you learned from the experience.
Example Answers
In my previous role, the technical support response time was slow due to lack of tracking. I implemented a ticketing system that streamlined issue reporting. As a result, we reduced response time by 40% within three months. This taught me the value of proper tools for efficiency.
Describe a time when you had to learn a new technology or process quickly. How did you approach the learning curve?
How to Answer
- 1
Identify a specific technology or process you learned.
- 2
Explain the context or challenge you faced.
- 3
Describe your method for learning, such as hands-on practice or online resources.
- 4
Highlight any support you received from colleagues or mentors.
- 5
Conclude with the positive outcome or results of your learning.
Example Answers
At my previous job, I was tasked to learn a new software for project management quickly. I set aside an hour each day to explore the tutorials offered online and practiced using the software on a small project. I also reached out to a colleague who was familiar with it for quick tips. Within two weeks, I was able to lead a project using the new software, improving our team's efficiency.
Give an example of a complex problem you solved on a technical operation. What was the outcome?
How to Answer
- 1
Identify a specific technical problem you faced.
- 2
Explain the steps you took to analyze and address the problem.
- 3
Highlight the tools or methods used in your solution.
- 4
Describe the outcome, focusing on measurable results.
- 5
Reflect on what you learned and how it improved operations.
Example Answers
In my previous role, we encountered a significant downtime issue on our production line due to equipment failure. I analyzed the operation logs and identified a pattern of overheating in one of our machines. After investigating, I implemented a cooling system upgrade and adjusted our maintenance schedule. As a result, downtime was reduced by 30% over the next three months, greatly increasing our productivity.
Describe a situation where your attention to detail prevented a technical error from occurring.
How to Answer
- 1
Think of a specific technical project where you caught a mistake.
- 2
Detail the steps you took to identify and correct the error.
- 3
Explain the outcome and its impact on the project or team.
- 4
Use the STAR method: Situation, Task, Action, Result.
- 5
Keep the answer focused on your role and contributions.
Example Answers
In my previous role, I was preparing a software deployment. During testing, I noticed that a critical configuration file was not updated. I immediately alerted the team and we corrected it before going live. This attention to detail prevented a major outage for our users.
Don't Just Read Technical Operator Questions - Practice Answering Them!
Reading helps, but actual practice is what gets you hired. Our AI feedback system helps you improve your Technical Operator interview answers in real-time.
Personalized feedback
Unlimited practice
Used by hundreds of successful candidates
Technical Interview Questions
Explain how you would set up and calibrate a piece of machinery that you are unfamiliar with.
How to Answer
- 1
Research the machinery type and model beforehand if possible
- 2
Refer to the manufacturer's manual for setup instructions
- 3
Check all connections and safety features before powering on
- 4
Use test runs to gradually adjust settings and calibrate
- 5
Document any changes made during setup for future reference
Example Answers
I would start by consulting the manufacturer's manual to understand the setup process. Next, I would ensure all connections are secure and check that safety protocols are in place. After powering on, I would conduct test runs and adjust the settings carefully until the machinery is calibrated correctly. Finally, I would document the process for future use.
What are the steps you take to troubleshoot a malfunctioning piece of equipment?
How to Answer
- 1
Gather information about the issue from operators or logs.
- 2
Inspect the equipment for visible signs of damage or wear.
- 3
Check connections and settings to ensure they are correct.
- 4
Run diagnostic tests or troubleshoot according to the manual.
- 5
Document findings and repeat steps if needed for further analysis.
Example Answers
I first gather information from the operators about when the issue occurs. Then, I inspect the equipment for physical damage and check all connections. After that, I consult the manual for troubleshooting steps and perform any diagnostic tests available.
Don't Just Read Technical Operator Questions - Practice Answering Them!
Reading helps, but actual practice is what gets you hired. Our AI feedback system helps you improve your Technical Operator interview answers in real-time.
Personalized feedback
Unlimited practice
Used by hundreds of successful candidates
What safety protocols do you follow when operating or maintaining machinery?
How to Answer
- 1
Identify and follow the manufacturer's safety instructions.
- 2
Always wear appropriate personal protective equipment (PPE) such as gloves, goggles, and helmets.
- 3
Ensure the machinery is properly locked out and tagged out before maintenance.
- 4
Conduct regular safety checks and reports on machinery.
- 5
Stay alert and focused while operating equipment, avoiding distractions.
Example Answers
I always follow the manufacturer's safety guidelines and wear the necessary PPE like gloves and safety goggles while operating the machinery. This helps to minimize risk.
Can you explain the basics of how a PLC (Programmable Logic Controller) works and its applications in technical operations?
How to Answer
- 1
Start with a clear definition of PLC and its purpose.
- 2
Explain the main components: CPU, input/output modules, and programming software.
- 3
Describe the process flow: input scanning, logic execution, output updating.
- 4
Mention typical applications in industry: automation, control processes, machinery operation.
- 5
Keep your response concise and focus on practical examples.
Example Answers
A PLC, or Programmable Logic Controller, is a digital computer used for automation of industrial processes. It consists of a CPU that processes inputs from sensors and sends outputs to actuators based on the programmed logic. Common applications include controlling conveyor belts in manufacturing or managing lighting systems in buildings.
What software tools are you proficient in for operating or maintaining technical systems?
How to Answer
- 1
Identify the key software tools relevant to the role
- 2
Discuss your level of expertise with each tool
- 3
Provide examples of how you've used these tools in past roles
- 4
Mention any certifications or trainings related to the software
- 5
Highlight how these tools improved operations or efficiency in your experience.
Example Answers
I am proficient in SCADA systems, particularly Ignition and Wonderware. In my last role, I used these tools daily to monitor and control plant operations, which enhanced our response time to system alerts by 30%.
How do you approach reading and interpreting technical diagrams or schematics?
How to Answer
- 1
Familiarize yourself with symbols and notations used in the diagram.
- 2
Break down the diagram into smaller sections for easier understanding.
- 3
Look for labels and legends that provide additional context.
- 4
Identify the main components and their relationships.
- 5
Practice interpreting different types of diagrams to build your skills.
Example Answers
I start by familiarizing myself with the standard symbols used in the schematic. Then, I break it down section by section, ensuring I understand the function of each part before connecting them together.
What is your experience with setting up preventive maintenance schedules? Can you provide an example?
How to Answer
- 1
Briefly explain your understanding of preventive maintenance.
- 2
Describe the process you followed to create a maintenance schedule.
- 3
Use a specific example from your experience that highlights your role.
- 4
Mention any tools or software you used to manage the schedules.
- 5
Highlight the impact your preventive maintenance had on operations.
Example Answers
In my previous role at XYZ Company, I devised a preventive maintenance schedule for our production equipment. I started by analyzing past breakdown data to identify critical machines. I then set up a monthly maintenance plan using an Excel sheet and shared it with the team. This reduced downtime by 30% over six months.
What type of equipment or machinery do you have the most experience with, and how do you keep up to date with new advancements?
How to Answer
- 1
Identify specific equipment or machinery you have hands-on experience with.
- 2
Mention relevant technical skills or certifications relating to the equipment.
- 3
Discuss how you stay informed about industry trends, such as through workshops or online courses.
- 4
Give examples of how you've applied this knowledge in practical scenarios.
- 5
Express enthusiasm for learning and adapting to new technologies.
Example Answers
I have the most experience with CNC machining equipment. I’ve worked extensively with Haas and Siemens systems. To stay updated, I regularly attend industry trade shows and have completed online courses in advanced CNC programming.
How do you approach implementing automation in technical operations? What are the key considerations?
How to Answer
- 1
Identify repetitive tasks that can be automated
- 2
Evaluate the tools and technologies available for automation
- 3
Consider the impact on the team and workflow
- 4
Test automation solutions in a controlled environment
- 5
Gather feedback and continuously improve the automation process
Example Answers
I start by analyzing our daily operations to find repetitive tasks that waste time. Next, I research suitable automation tools that align with our current systems. I implement small pilot projects to see how they affect our workflow and make adjustments based on team feedback to ensure effective integration.
What are the compliance standards you follow in technical operations related to your industry?
How to Answer
- 1
Identify key compliance standards relevant to your role and industry
- 2
Mention regulatory bodies or standards such as ISO, OSHA, or GDPR
- 3
Provide examples of how you ensure compliance in your daily operations
- 4
Discuss the importance of compliance in maintaining safety and quality
- 5
Be ready to cite any specific tools or documentation you use for compliance tracking
Example Answers
In my role, I follow ISO 9001 for quality management and adhere to OSHA standards for workplace safety. I ensure compliance by conducting regular audits and training my team on these standards.
Don't Just Read Technical Operator Questions - Practice Answering Them!
Reading helps, but actual practice is what gets you hired. Our AI feedback system helps you improve your Technical Operator interview answers in real-time.
Personalized feedback
Unlimited practice
Used by hundreds of successful candidates
Situational Interview Questions
If a machine you are responsible for suddenly stops working during production, how would you handle the situation?
How to Answer
- 1
Stay calm and assess the situation quickly.
- 2
Check for any immediate indicators of what caused the stop.
- 3
Inform your supervisor and relevant team members about the issue.
- 4
Try resetting the machine or follow standard troubleshooting steps.
- 5
Document the incident and the actions taken for future reference.
Example Answers
I would first remain calm and assess the machine to see if there are any warning lights or displays indicating the issue. Then, I'd inform my supervisor while trying to reset the machine as per the troubleshooting guidelines.
Imagine you are the only technical operator on duty and you notice that a machine requires immediate maintenance. How would you prioritize your tasks?
How to Answer
- 1
Assess the urgency of the machine issue and potential impact on production.
- 2
Notify relevant personnel or a supervisor about the issue if possible.
- 3
Check if any other machines need urgent attention as well.
- 4
Plan and prepare for the maintenance task by gathering necessary tools.
- 5
Document the issue and update maintenance logs after resolving the problem.
Example Answers
First, I would quickly assess the severity of the machine problem and its effect on production. If it's critical, I would notify my supervisor while gathering the necessary tools for the maintenance.
Don't Just Read Technical Operator Questions - Practice Answering Them!
Reading helps, but actual practice is what gets you hired. Our AI feedback system helps you improve your Technical Operator interview answers in real-time.
Personalized feedback
Unlimited practice
Used by hundreds of successful candidates
While operating a machine, you notice a safety hazard. How would you respond?
How to Answer
- 1
Immediately stop the machine to prevent accidents.
- 2
Assess the situation to understand the nature of the hazard.
- 3
Report the hazard to a supervisor or safety officer without delay.
- 4
Follow company protocols for addressing safety issues.
- 5
Document the incident if required for safety compliance.
Example Answers
I would stop the machine right away to ensure no one gets hurt. Then, I would assess the hazard and report it to my supervisor immediately, making sure to follow our safety procedures.
You have limited resources and are required to maintain production efficiency. How do you prioritize tasks and resource allocation?
How to Answer
- 1
Identify the most critical tasks that directly impact production.
- 2
Assess the resources available and their current utilization.
- 3
Rank tasks based on urgency and importance to production goals.
- 4
Communicate with your team to understand any additional insights.
- 5
Adjust plans based on real-time feedback and performance metrics.
Example Answers
I prioritize tasks by focusing on those that are essential to maintaining production, such as equipment maintenance and quality checks. I review current resource allocations and adjust them to ensure critical tasks have the necessary support.
Suppose you have multiple machines under your supervision and one starts showing errors. How would you manage your time to address all tasks?
How to Answer
- 1
Prioritize the errors based on severity and impact on operations
- 2
Quickly assess which machines can operate normally while resolving issues
- 3
Communicate with your team to delegate tasks if possible
- 4
Document the issues and resolutions for future reference
- 5
Stay calm and focused to make clear decisions under pressure
Example Answers
I would first assess the error severity to prioritize which machine needs immediate attention. If the faulty machine could lead to significant downtime, I would address it first, while checking if others can continue operations without interruption. I would also inform my team and delegate some tasks if necessary to expedite the resolution process.
You notice an inefficiency in the current operational process. How would you approach proposing a solution to management?
How to Answer
- 1
Identify the specific inefficiency and gather data to quantify the impact.
- 2
Research potential solutions or best practices from similar organizations.
- 3
Prepare a clear and concise presentation of your findings and proposal.
- 4
Be ready to discuss the benefits and potential return on investment of your proposed solution.
- 5
Engage management by aligning your proposal with company goals and priorities.
Example Answers
I noticed that the equipment downtime has increased by 20% over the last month. I analyzed the logs and found that a specific machine often requires maintenance. I propose we schedule preventative maintenance every two weeks instead of once a month. This could reduce downtime significantly.
If you were assigned to work with another department unfamiliar with technical aspects on a joint project, how would you facilitate effective collaboration?
How to Answer
- 1
Start by understanding the other department's goals and concerns
- 2
Use simple language to explain technical concepts clearly
- 3
Establish regular communication through meetings or updates
- 4
Encourage feedback and questions to ensure understanding
- 5
Create visual aids or documentation to support your explanations
Example Answers
I would first meet with the team to discuss their goals for the project and what they expect. Then, I'd offer to explain any technical terms in simple language and encourage them to ask questions during our collaboration. I'd also set up weekly check-ins to keep everyone informed and aligned.
A supervisor asks you to make a technical decision that you believe is not optimal. How do you handle the situation?
How to Answer
- 1
Listen to the supervisor's reasoning fully before responding.
- 2
Clearly communicate your concerns with specific examples.
- 3
Suggest an alternative solution that addresses the potential issues.
- 4
Use data or past experiences to support your viewpoint.
- 5
Remain respectful and open to discussion.
Example Answers
I would first listen carefully to my supervisor's reasoning, then express my concerns by highlighting specific issues I see with the decision. I would suggest an alternative approach that I believe could achieve better results and support my suggestions with data or relevant examples.
A critical piece of equipment fails right before a deadline. Describe your plan of action.
How to Answer
- 1
Prioritize assessing the failure quickly and thoroughly.
- 2
Identify if the equipment can be repaired immediately or if a workaround is available.
- 3
Communicate with your team and management about the situation and proposed solutions.
- 4
Explore alternative equipment or resources that could fulfill the need temporarily.
- 5
Keep a clear timeline of actions to minimize downtime and meet the deadline.
Example Answers
First, I would assess what failed and determine if it can be repaired on-site quickly. If it can't, I would look for a workaround or backup equipment that can be used. I would inform my team and management about the issue and what I am doing to resolve it. Meanwhile, I would set up a timeline for all actions to ensure we stay on track with our deadline.
If you were overseeing a team of operators, how would you delegate tasks to ensure efficiency and coverage?
How to Answer
- 1
Assess the strengths and weaknesses of each team member
- 2
Prioritize tasks based on urgency and complexity
- 3
Assign roles that align with individual skills and interests
- 4
Establish clear communication and expectations
- 5
Monitor progress and be ready to adjust assignments as needed
Example Answers
I would first evaluate my team's skills and experience. Then, I would prioritize our tasks and assign them based on who is best suited for each. Regular check-ins would help me ensure everything is on track.
Don't Just Read Technical Operator Questions - Practice Answering Them!
Reading helps, but actual practice is what gets you hired. Our AI feedback system helps you improve your Technical Operator interview answers in real-time.
Personalized feedback
Unlimited practice
Used by hundreds of successful candidates
Technical Operator Position Details
Recommended Job Boards
CareerBuilder
www.careerbuilder.com/jobs/technical-operatorZipRecruiter
www.ziprecruiter.com/Jobs/Technical-OperatorThese job boards are ranked by relevance for this position.
Related Positions
Ace Your Next Interview!
Practice with AI feedback & get hired faster
Personalized feedback
Used by hundreds of successful candidates
Ace Your Next Interview!
Practice with AI feedback & get hired faster
Personalized feedback
Used by hundreds of successful candidates