Top 29 Tool Setter Interview Questions and Answers [Updated 2025]
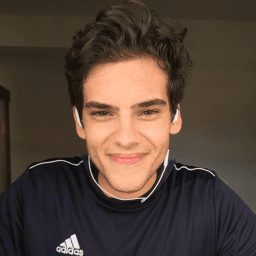
Andre Mendes
•
March 30, 2025
Preparing for a Tool Setter interview can be daunting, but we've got you covered with the most common questions and expert advice on crafting effective responses. This post is designed to help you stand out by providing insightful example answers and practical tips tailored to the Tool Setter role. Dive in to gain the confidence and knowledge you need to impress your interviewers and secure the job.
Download Tool Setter Interview Questions in PDF
To make your preparation even more convenient, we've compiled all these top Tool Setterinterview questions and answers into a handy PDF.
Click the button below to download the PDF and have easy access to these essential questions anytime, anywhere:
List of Tool Setter Interview Questions
Behavioral Interview Questions
Can you describe a time when you resolved a significant issue with a tool setup?
How to Answer
- 1
Identify a specific situation where you had a tool setup problem
- 2
Explain the actions you took to troubleshoot and resolve the issue
- 3
Highlight any teamwork or communication that was involved
- 4
Mention the outcome and what you learned from the experience
- 5
Keep your response focused and relevant to the role of a Tool Setter
Example Answers
In my previous role, I noticed inconsistent measurements during a tool setup for a critical production run. I quickly investigated the tool calibration and discovered it was off by 0.01 inches. I recalibrated the tool and re-verified the setup. The production run proceeded without further issues, leading to a 20% increase in efficiency.
How have you worked within a team to improve the efficiency of a production process?
How to Answer
- 1
Identify specific challenges the team faced in production.
- 2
Describe your role and the actions you took to address these challenges.
- 3
Mention how you collaborated with team members to implement solutions.
- 4
Highlight any measurable improvements in efficiency resulting from your actions.
- 5
Conclude with a reflection on the importance of teamwork in achieving goals.
Example Answers
In my previous job, our production line was facing downtime due to tool changes. I suggested a team meeting to analyze our current processes. We developed a standardized checklist for tool setups, which reduced changeover time by 20%. This collaboration not only improved our efficiency but also fostered better communication within the team.
Don't Just Read Tool Setter Questions - Practice Answering Them!
Reading helps, but actual practice is what gets you hired. Our AI feedback system helps you improve your Tool Setter interview answers in real-time.
Personalized feedback
Unlimited practice
Used by hundreds of successful candidates
Tell me about a situation where you had to adapt quickly to a change in tooling specifications.
How to Answer
- 1
Choose a specific example from your past experience.
- 2
Explain the context clearly to set the stage.
- 3
Describe the challenge you faced due to the change.
- 4
Highlight the steps you took to adapt effectively.
- 5
Conclude with the positive outcome or lesson learned.
Example Answers
In my previous role, we received last-minute changes to the tooling specifications for a key project. I quickly gathered the team to reassess our resources. We brainstormed alternative tools and workflows. I led the effort to implement a new tool setup within the deadline, which improved efficiency and met customer expectations.
Describe an instance where your attention to detail prevented a tool malfunction.
How to Answer
- 1
Think of a specific situation where you noticed a potential issue.
- 2
Explain how you identified the problem and the steps you took.
- 3
Highlight the outcome and how it impacted the work process.
- 4
Use metrics or results if possible to quantify the success.
- 5
Keep the answer focused on your role and actions.
Example Answers
In a previous role, I noticed unusual wear on a cutting tool during routine maintenance. I checked the operating parameters and discovered the speed was set too high. I adjusted it back to the recommended setting, preventing potential tool breakage and ensuring smooth production for the rest of the shift.
Can you give an example of a conflict you had with another team member regarding tool settings and how you resolved it?
How to Answer
- 1
Describe the specific conflict clearly and briefly.
- 2
Explain the impact of the disagreement on the work process.
- 3
Share your approach to open communication to resolve the issue.
- 4
Highlight the solution you reached and how it improved teamwork.
- 5
Reflect on what you learned from the experience.
Example Answers
During a project, a colleague and I disagreed on the correct tool settings for a machining operation, which caused delays. I suggested a meeting to discuss our methods, where we both presented our data. We eventually agreed on a compromise setting based on the best features of both our strategies, leading to faster machining times and a better working relationship.
How have you contributed to training new employees on tool setup procedures?
How to Answer
- 1
Share specific training methods you used, like hands-on demonstrations.
- 2
Discuss any written materials or guides you developed to aid training.
- 3
Mention how you tailored training to individual learning styles.
- 4
Highlight your approach to providing ongoing support after initial training.
- 5
Provide an example of successfully integrating a new employee into the team.
Example Answers
I used hands-on demonstrations to show new employees the tool setup process, ensuring they understood each step. I also created a quick reference guide that they could use during their first few setups.
What motivated you to pursue a career as a Tool Setter?
How to Answer
- 1
Reflect on personal interests in machinery and precision work
- 2
Highlight any relevant experiences or education that sparked this choice
- 3
Mention the satisfaction of problem-solving and efficiency improvement
- 4
Connect your motivation to industry demand for skilled tool setters
- 5
Emphasize your desire to contribute to quality manufacturing processes
Example Answers
I've always had a passion for machinery and enjoyed working on hands-on projects. In college, I took courses in machining that solidified my interest in precision work, and I realized how critical tool setters are in achieving quality production.
Technical Interview Questions
What types of tools and machinery have you worked with in your previous roles?
How to Answer
- 1
List specific tools and machinery relevant to a Tool Setter position
- 2
Mention your level of expertise with each tool or machinery
- 3
Highlight any particular projects or tasks you completed using these tools
- 4
Include any safety certifications or training related to the tools
- 5
If applicable, discuss how you adapted to new tools quickly
Example Answers
I have worked extensively with CNC lathes and milling machines, where I operated and set up various tooling systems. I have a strong understanding of precision measuring tools like calipers and micrometers, which I used in a high-volume production environment. Additionally, I have completed training in tool maintenance and safety practices.
Can you explain the process you follow to set up a new tool on a machine?
How to Answer
- 1
Review work order and specifications before starting
- 2
Gather all necessary tools and materials including the new tool
- 3
Ensure the machine is powered down and locked out for safety
- 4
Install the new tool, aligning it according to the machine's specifications
- 5
Conduct test runs to verify setup before production starts
Example Answers
First, I review the work order and specifications to understand the requirements. Then, I gather the new tool and necessary materials. I ensure the machine is powered down and locked out for safety. After that, I install the tool, aligning it as specified. Finally, I run some tests to confirm everything is set before starting production.
Don't Just Read Tool Setter Questions - Practice Answering Them!
Reading helps, but actual practice is what gets you hired. Our AI feedback system helps you improve your Tool Setter interview answers in real-time.
Personalized feedback
Unlimited practice
Used by hundreds of successful candidates
What preventative maintenance steps do you consider essential for tooling?
How to Answer
- 1
Inspect tooling regularly for wear and damage.
- 2
Clean tooling after each use to prevent buildup.
- 3
Lubricate moving parts according to manufacturer guidelines.
- 4
Maintain a log of maintenance performed on each tool.
- 5
Calibrate tools periodically to ensure precision.
Example Answers
I believe regular inspection for wear and damage is crucial, along with cleaning tooling after each use to avoid buildup. Lubricating moving parts as per the manufacturer's instructions also helps maintain efficiency.
How do you verify the accuracy of the tool settings after setup?
How to Answer
- 1
Use calibration tools to measure the tool offset.
- 2
Run a trial cut to check for accuracy and consistency.
- 3
Inspect the dimensions of the produced part against specifications.
- 4
Adjust settings based on measurement results if necessary.
- 5
Document the verification process for future reference.
Example Answers
I verify tool settings by first using a dial indicator to check the offsets, then I run a trial cut and measure the part to ensure it meets specifications. If adjustments are needed, I make those and document everything.
What machining processes are you most familiar with, and how have you applied that knowledge?
How to Answer
- 1
Identify key machining processes you know well, like turning, milling, or grinding.
- 2
Highlight specific machines or tools you have experience with.
- 3
Mention any relevant certifications or training.
- 4
Provide a brief example of a project where you used this knowledge.
- 5
Emphasize the impact of your work on efficiency or product quality.
Example Answers
I am most familiar with CNC milling and turning. In my last role, I operated a CNC lathe to create precision components for automotive parts. This experience taught me the importance of machine calibration and how it directly affects production quality.
What troubleshooting techniques do you use when a tool is not producing the expected results?
How to Answer
- 1
Start by reviewing the tool's setup to ensure it meets specifications.
- 2
Check for any wear or damage on the tool that could affect performance.
- 3
Inspect the material being used for inconsistencies or defects.
- 4
Run diagnostics to identify any mechanical or electrical issues.
- 5
Consult the manufacturer's guidelines for troubleshooting procedures.
Example Answers
I first check the tool's setup to ensure everything is aligned correctly. Then, I inspect for any visible wear or damage that could be affecting its performance. If everything looks good, I check the materials being used for any defects.
What methods do you employ to ensure tool setups are precise and consistent?
How to Answer
- 1
Use calibrated measuring tools to verify dimensions before starting.
- 2
Adhere to standard operating procedures for each setup to maintain consistency.
- 3
Document each setup process and results for future reference.
- 4
Regularly maintain and inspect tools to prevent wear-related inaccuracies.
- 5
Utilize visual aids, such as setup sheets, to ensure all steps are followed.
Example Answers
I always use calibrated calipers and micrometers to measure tools before setup. Following the standard operating procedures helps me to maintain precision. I document each setup to create a reference for myself and the team.
What experience do you have with CAD/CAM software in relation to tool setting?
How to Answer
- 1
Highlight specific CAD/CAM software you have used.
- 2
Describe how you used the software to enhance tool setting.
- 3
Mention any relevant projects or tasks you completed.
- 4
Emphasize collaboration with engineers or designers.
- 5
Discuss any training or certifications you have related to the software.
Example Answers
I have used SolidWorks and Mastercam extensively in my previous position, where I created tool paths and set specifications for milling operations.
What industry standards and best practices do you follow in tool setting?
How to Answer
- 1
Mention specific standards such as ISO or ANSI relevant to tool setting.
- 2
Highlight the importance of precision measurement tools like calipers or micrometers.
- 3
Discuss routine maintenance checks to ensure tools are in optimal condition.
- 4
Emphasize proper documentation of tool settings for consistency and traceability.
- 5
Include safety protocols to ensure safe handling and operation of tools.
Example Answers
I follow ISO standards for tool setting, using calipers and micrometers for precision. I also perform routine maintenance and document settings to maintain consistency.
How do you stay up to date with new technologies and advancements in tool setting?
How to Answer
- 1
Regularly read industry publications and journals.
- 2
Attend trade shows and workshops related to tool setting.
- 3
Participate in online forums and professional groups.
- 4
Follow influential figures and organizations on social media.
- 5
Complete relevant online courses and certifications.
Example Answers
I subscribe to industry journals and newsletters, attend annual trade shows, and engage in online forums to share insights with other professionals.
Don't Just Read Tool Setter Questions - Practice Answering Them!
Reading helps, but actual practice is what gets you hired. Our AI feedback system helps you improve your Tool Setter interview answers in real-time.
Personalized feedback
Unlimited practice
Used by hundreds of successful candidates
Situational Interview Questions
If you were tasked with reducing the setup time for a tool without sacrificing quality, what steps would you take?
How to Answer
- 1
Analyze the current setup process to identify bottlenecks
- 2
Implement standard operating procedures for consistency
- 3
Use templates or checklists to streamline steps
- 4
Train staff on efficient setup techniques
- 5
Regularly review and refine the process based on feedback
Example Answers
I would start by reviewing the current setup process to find any bottlenecks. Then, I would create standard operating procedures to ensure everyone follows the same efficient steps. Using a checklist would help us not skip any essential tasks.
How would you handle a situation where a tool failed during a critical production run?
How to Answer
- 1
Immediately assess the situation to determine the extent of the failure
- 2
Communicate clearly with the team to inform them about the issue
- 3
Implement a backup plan or switch to alternative tools if available
- 4
Document the failure for future reference and analysis
- 5
Review the tool's maintenance history to prevent future issues
Example Answers
If a tool failed, I would first assess the failure to understand its impact. I'd then inform my team right away so everyone is on the same page. If we have spare tools, I'd switch to those to minimize downtime. After resolving the issue, I'd document what happened to avoid similar issues in the future.
Don't Just Read Tool Setter Questions - Practice Answering Them!
Reading helps, but actual practice is what gets you hired. Our AI feedback system helps you improve your Tool Setter interview answers in real-time.
Personalized feedback
Unlimited practice
Used by hundreds of successful candidates
Imagine you have a tight deadline and realize that the tool you need requires extensive setup. How would you manage the situation?
How to Answer
- 1
Assess the time needed for the setup against the deadline
- 2
Prioritize tasks that can run concurrently during the setup
- 3
Communicate with your team about any potential delays
- 4
Consider alternative tools or solutions that may require less setup
- 5
Stay organized and focused to minimize distractions during the setup
Example Answers
I would first evaluate how long the setup will take and if it's feasible within the deadline. If not, I'd look for simpler tools we have on hand that could meet the requirements.
If a team member disagrees with your tool setup method, how would you address their concerns?
How to Answer
- 1
Listen actively to their concerns without interrupting
- 2
Ask clarifying questions to understand their perspective
- 3
Share the reasoning behind your method clearly
- 4
Be open to feedback and willing to compromise if necessary
- 5
Suggest a trial period to test both setups for effectiveness
Example Answers
I would start by listening to their concerns fully, then ask questions to clarify their points. After that, I'd explain my approach and the reasons behind it. If they still have reservations, I'd propose a trial period to evaluate both methods and see which yields better results.
How would you determine if newer tools being introduced require additional training for the staff?
How to Answer
- 1
Evaluate the complexity of the new tools compared to existing ones
- 2
Gather feedback from experienced staff on their comfort level with new tools
- 3
Conduct a skills assessment to identify gaps in knowledge for new tools
- 4
Review manufacturer specifications and training resources available
- 5
Implement a pilot program to test usability and identify training needs
Example Answers
I would start by comparing the new tools' features with the tools we already use. If they are significantly more complex, I would consult with our staff to see if they feel confident using them before making a training decision.
What actions would you take if you noticed a potential safety hazard while setting up a tool?
How to Answer
- 1
Immediately stop the setup process to prevent any accidents.
- 2
Assess the hazard to determine its severity and type.
- 3
Notify the supervisor or safety officer about the issue right away.
- 4
Use appropriate signage or barriers to warn others in the area.
- 5
Follow company protocols for addressing safety hazards.
Example Answers
If I notice a safety hazard, I would stop what I'm doing right away. Then, I'd assess the situation and inform my supervisor. I'd put up warning signs to ensure everyone is aware of the hazard until it's resolved.
How would you prioritize tasks if assigned multiple setups at the same time?
How to Answer
- 1
Assess the urgency and importance of each setup
- 2
Check the production schedule for deadlines
- 3
Communicate with team members to understand dependencies
- 4
Organize tasks based on equipment availability
- 5
Use a checklist to track progress and adjust priorities as needed
Example Answers
I would evaluate each setup's deadlines and talk to my supervisor about priorities, then tackle the most critical setups first based on urgency.
How would you incorporate feedback from production operators regarding tool performance?
How to Answer
- 1
Establish a regular feedback loop with operators through scheduled meetings or surveys.
- 2
Encourage operators to provide specific examples of tool issues and successes.
- 3
Analyze the feedback to identify patterns or recurring problems.
- 4
Collaborate with operators to develop solutions or adjustments to tools.
- 5
Communicate the changes implemented based on feedback to build trust and engagement.
Example Answers
I would schedule bi-weekly meetings with production operators to discuss tool performance. I would encourage them to share specific examples of any issues they face, and then I would analyze the feedback to identify patterns. Together, we would work on potential solutions, and I would ensure to communicate any changes made based on their input.
If you noticed that a tool setup method is consistently leading to production downtime, how would you address this?
How to Answer
- 1
Identify the root cause of the downtime through data analysis.
- 2
Consult with the team to gather feedback on the setup method.
- 3
Develop a revised setup procedure aimed at reducing time and errors.
- 4
Test the new method in a controlled environment before full implementation.
- 5
Monitor the outcomes and adjust the procedure as necessary based on results.
Example Answers
I would start by analyzing the production data to pinpoint where the downtime is happening. Then, I would consult with my colleagues to gather their insights on the current setup method. Based on this feedback, I would draft a new setup procedure, test it, and monitor its effectiveness to ensure it resolves the issue.
If resources were limited, how would you ensure that tool setting is still performed effectively?
How to Answer
- 1
Prioritize tool setting tasks based on critical production needs
- 2
Implement efficient scheduling to maximize resource utilization
- 3
Leverage existing tools and machinery to reduce setup time
- 4
Train team members to be versatile and handle multiple tasks
- 5
Establish clear communication to quickly address any issues
Example Answers
In a resource-constrained environment, I would first prioritize tool setting tasks based on their impact on production. I would implement efficient scheduling to ensure we make the most of the available time and resources.
Don't Just Read Tool Setter Questions - Practice Answering Them!
Reading helps, but actual practice is what gets you hired. Our AI feedback system helps you improve your Tool Setter interview answers in real-time.
Personalized feedback
Unlimited practice
Used by hundreds of successful candidates
Tecnical Interview Questions
How do you determine which tool is the most suitable for a particular job?
How to Answer
- 1
Analyze the material being worked on and its properties
- 2
Consider the precision requirements of the job
- 3
Evaluate the machining process and its specific needs
- 4
Review tool condition and compatibility with the machine
- 5
Consult tool catalogs and previous job experiences for guidance
Example Answers
I start by identifying the material type and hardness. Then, I assess the required precision for the job. This helps me choose the right tool that can handle the task efficiently.
Tool Setter Position Details
Salary Information
Recommended Job Boards
CareerBuilder
www.careerbuilder.com/jobs-tool-setterZipRecruiter
www.ziprecruiter.com/Jobs/Tool-SetterThese job boards are ranked by relevance for this position.
Related Positions
- Pin Setter
- Tool Mechanic
- Pin Pusher
- Pin Puller
- Conveyor Installer
- Conveyor Belt Installer
- Scale Mechanic
- Fixer
- Machine Fixer
- Machine Repairer
Similar positions you might be interested in.
Ace Your Next Interview!
Practice with AI feedback & get hired faster
Personalized feedback
Used by hundreds of successful candidates
Ace Your Next Interview!
Practice with AI feedback & get hired faster
Personalized feedback
Used by hundreds of successful candidates