Top 31 Conveyor Installer Interview Questions and Answers [Updated 2025]
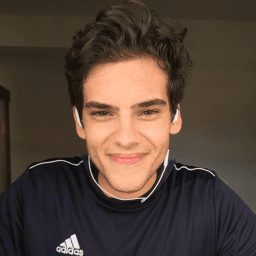
Andre Mendes
•
March 30, 2025
Preparing for a conveyor installer interview can be daunting, but we've got you covered. In this post, we present the most common interview questions for the conveyor installer role, complete with example answers and actionable tips to help you respond confidently and effectively. Whether you're a seasoned professional or new to the field, this guide will equip you with the insights needed to impress potential employers.
Download Conveyor Installer Interview Questions in PDF
To make your preparation even more convenient, we've compiled all these top Conveyor Installerinterview questions and answers into a handy PDF.
Click the button below to download the PDF and have easy access to these essential questions anytime, anywhere:
List of Conveyor Installer Interview Questions
Technical Interview Questions
How do you troubleshoot a conveyor system that has suddenly stopped working?
How to Answer
- 1
Check the power supply to the conveyor system first.
- 2
Look for any physical obstructions on the conveyor belt.
- 3
Inspect the emergency stop button to see if it has been activated.
- 4
Examine the motor and any belts for signs of wear or damage.
- 5
Refer to the system manual for specific troubleshooting steps.
Example Answers
First, I would check if the conveyor is receiving power. If the power is on, I’d inspect the belt for any blockages. Next, I would see if the emergency stop is engaged before examining the motor for any faults.
Can you explain the steps you take during the installation of a belt conveyor?
How to Answer
- 1
Start by gathering all necessary tools and equipment.
- 2
Ensure the installation site is prepared and clean.
- 3
Assemble the conveyor frame according to specifications.
- 4
Install the belt and all related components correctly.
- 5
Test the system to verify proper operation and make adjustments.
Example Answers
First, I gather the required tools and ensure the installation site is ready. Then, I assemble the conveyor frame per the plans and carefully install the belt and components. Finally, I run tests to confirm everything works correctly.
Don't Just Read Conveyor Installer Questions - Practice Answering Them!
Reading helps, but actual practice is what gets you hired. Our AI feedback system helps you improve your Conveyor Installer interview answers in real-time.
Personalized feedback
Unlimited practice
Used by hundreds of successful candidates
What routine maintenance tasks do you recommend for ensuring the longevity of a conveyor system?
How to Answer
- 1
Regularly inspect belts for wear and tear
- 2
Lubricate moving parts at scheduled intervals
- 3
Check alignment of rollers and pulleys
- 4
Clean the conveyor system to remove debris
- 5
Monitor and adjust tension on the belts appropriately
Example Answers
To maintain a conveyor system, I recommend inspecting belts for any signs of damage regularly. It's crucial to lubricate all moving parts and ensure that everything is aligned properly to prevent unnecessary wear. Additionally, keeping the system clean and checking belt tension can greatly enhance its longevity.
What types of conveyor systems are you most experienced with, and what are their key components?
How to Answer
- 1
Identify specific types of conveyor systems you have worked on.
- 2
Mention key components such as belts, pulleys, motors, and sensors.
- 3
Include examples of industries where you used these systems.
- 4
Explain your role in installing or maintaining these systems.
- 5
Be ready to discuss any troubleshooting or performance improvements you've implemented.
Example Answers
I have extensive experience with belt conveyors and roller conveyors. Key components include the drive motor, pulleys, and the belt itself. I've primarily worked in the manufacturing sector where I installed and maintained these systems, ensuring they operated efficiently.
What industry regulations do you follow when installing conveyor systems?
How to Answer
- 1
Research specific regulations like OSHA and ANSI standards for conveyor safety.
- 2
Mention any relevant local or state regulations that apply to conveyor systems.
- 3
Discuss the importance of complying with safety and operational guidelines.
- 4
Explain how you ensure equipment is compliant during the installation process.
- 5
Highlight ongoing training or certifications related to conveyor system safety.
Example Answers
I follow OSHA regulations for workplace safety and ANSI standards for conveyor system design. I also ensure compliance with local codes that govern equipment installation, checking each component before installation to meet the specifications.
What role do pneumatic systems play in conveyor installations, and how do you handle them?
How to Answer
- 1
Explain what pneumatic systems are and their importance in conveyor installations.
- 2
Discuss specific applications of pneumatic systems in conveyors, such as pushing or lifting loads.
- 3
Mention safety considerations when working with pneumatic systems.
- 4
Describe your experience with maintenance and troubleshooting of pneumatic components.
- 5
Emphasize teamwork and communication when integrating pneumatic systems into conveyor projects.
Example Answers
Pneumatic systems are essential in conveyor installations for tasks like moving and positioning loads. I ensure they are installed correctly, focusing on safety by following protocols to avoid leaks. I have experience in troubleshooting issues and maintaining these systems to keep operations smooth.
How do you calculate the load capacity required for a specific conveyor system?
How to Answer
- 1
Identify the maximum weight of items to be transported.
- 2
Consider the conveyor length and any incline or decline.
- 3
Account for the speed of the conveyor and frequency of use.
- 4
Factor in safety margins based on industry standards.
- 5
Use manufacturer's guidelines or design software for precise calculations.
Example Answers
To calculate load capacity, I first determine the weight of the items being transported, then assess the conveyor's length and any slopes. I also consider the required speed and add a safety factor based on standard practices.
What methods do you use to ensure the alignment of conveyor components?
How to Answer
- 1
Perform regular inspections to check for misalignment in components
- 2
Use laser alignment tools for precise measurements
- 3
Adjust tension and load to ensure even distribution
- 4
Follow manufacturer specifications for installation and alignment
- 5
Document any alignment adjustments for future reference
Example Answers
I use laser alignment tools to ensure that all conveyor components are precisely aligned. This helps prevent wear and ensures smooth operation.
Can you walk us through the assembly process of a roller conveyor?
How to Answer
- 1
Start with gathering all necessary components and tools.
- 2
Explain the base frame assembly first, ensuring stability.
- 3
Detail how to install the rollers and ensure they spin freely.
- 4
Include how to attach the conveyor belt and ensure proper tension.
- 5
Finish with safety checks and testing for functionality.
Example Answers
First, I gather the frame, rollers, and tools. I assemble the base frame, securing it tightly. Next, I install the rollers, making sure they are level and can rotate freely. After that, I attach the conveyor belt, adjusting it for the right tension. Lastly, I perform a safety check and test the conveyor to ensure it operates smoothly.
What tools do you consider essential for a conveyor installation project?
How to Answer
- 1
List specific tools used in conveyor installation.
- 2
Mention safety equipment to emphasize responsibility.
- 3
Explain the purpose of each tool briefly.
- 4
Consider tools for both assembly and alignment.
- 5
Tailor your answer to show familiarity with various conveyor systems.
Example Answers
For conveyor installation, essential tools include a socket set for assembling components, a level to ensure alignment, and a torque wrench to meet specifications. Safety gear like gloves and goggles are also crucial.
Don't Just Read Conveyor Installer Questions - Practice Answering Them!
Reading helps, but actual practice is what gets you hired. Our AI feedback system helps you improve your Conveyor Installer interview answers in real-time.
Personalized feedback
Unlimited practice
Used by hundreds of successful candidates
Behavioral Interview Questions
Can you describe a time when you worked as part of a team to install a conveyor system? What was your role?
How to Answer
- 1
Choose a specific project to discuss.
- 2
Clearly define your role in the team.
- 3
Highlight your contributions and skills used.
- 4
Mention any challenges faced and how the team overcame them.
- 5
Conclude with the outcome of the installation and what you learned.
Example Answers
In a recent project for a warehouse, I was part of a team that installed a conveyor system. My role was to handle the alignment of the conveyor components. We faced a challenge with uneven flooring, but by collaborating, we adjusted the supports to ensure everything was level. The installation was completed on time, and it improved our efficiency significantly.
Describe a challenging installation project you managed. How did you overcome the difficulties you faced?
How to Answer
- 1
Select a specific project that had notable challenges.
- 2
Explain the nature of the challenges clearly and briefly.
- 3
Describe the steps you took to address the difficulties.
- 4
Highlight any teamwork or communication strategies used.
- 5
Mention the outcome and any lessons learned from the experience.
Example Answers
In one project, we had to install a conveyor system in a tight space. The challenge was limited access for heavy equipment. I coordinated with my team to use smaller tools and developed a phased approach to manage the installation process effectively. This ensured that we completed the project on time and without damage.
Don't Just Read Conveyor Installer Questions - Practice Answering Them!
Reading helps, but actual practice is what gets you hired. Our AI feedback system helps you improve your Conveyor Installer interview answers in real-time.
Personalized feedback
Unlimited practice
Used by hundreds of successful candidates
Have you ever led a team during a conveyor installation? How did you ensure everyone was on track?
How to Answer
- 1
Describe your leadership role and responsibilities clearly
- 2
Mention specific communication methods you used with your team
- 3
Explain how you set goals and milestones for the project
- 4
Discuss how you handled any challenges during the installation
- 5
Conclude with what the outcome was and any feedback from the team
Example Answers
In my last project, I led a team of four during the installation of a conveyor system. I held daily briefings to communicate our goals and any updates. We set clear milestones to ensure we stayed on track. When we faced scheduling challenges, I reorganized our tasks and kept the morale high by encouraging open communication. The project finished ahead of schedule and we received positive feedback from management.
Tell me about a time when you had to address safety concerns on a job site. What steps did you take?
How to Answer
- 1
Identify a specific safety issue you encountered.
- 2
Explain your immediate response to the concern.
- 3
Describe any actions you took to resolve the issue.
- 4
Mention how you communicated with the team about the concern.
- 5
Share the outcome and any lessons learned.
Example Answers
On a warehouse installation job, I noticed loose cables on the floor creating a tripping hazard. I immediately flagged the issue to my supervisor and redirected the team until the cables were secured. We taped them down and I then led a quick safety briefing about keeping walkways clear. As a result, we completed the project without any accidents.
Give an example of a situation where you had to quickly adapt your installation plan. What happened?
How to Answer
- 1
Think of a specific incident where a change was necessary
- 2
Describe the initial plan and what the unexpected changes were
- 3
Explain how you assessed the new situation and what actions you took
- 4
Highlight the outcome and what you learned from it
- 5
Keep it concise and focus on your problem-solving skills
Example Answers
During an installation project, I found that the conveyor was too long for the designated space due to unanticipated structural changes. I quickly reevaluated the layout, discussed alternatives with the team, and decided to use a more compact conveyor model. This minimized downtime and kept the project on schedule.
Describe a time when you received feedback on your installation work. How did you respond?
How to Answer
- 1
Think of a specific project where you received feedback.
- 2
Explain the feedback clearly, including who gave it and why it mattered.
- 3
Describe your immediate reaction to the feedback.
- 4
Talk about the steps you took to improve based on that feedback.
- 5
Emphasize what you learned and how it helped you in future installations.
Example Answers
During a recent conveyor installation, my supervisor pointed out that I had installed a component incorrectly. I was initially surprised, but I listened carefully to the feedback. I reviewed the installation manual and corrected the mistake immediately. This experience taught me the importance of double-checking my work, which I now apply to every installation.
Can you provide an example of how you effectively communicated with clients or stakeholders during a project?
How to Answer
- 1
Think of a specific project where communication was key.
- 2
Mention the stakeholders or clients involved.
- 3
Describe the communication methods you used, like meetings, emails or reports.
- 4
Highlight how your communication helped in solving a problem or achieving a goal.
- 5
Conclude with the positive impact of your communication on the project outcome.
Example Answers
On a recent installation project, I was in charge of coordinating with the client and the technical team. I set up weekly meetings to update the client on progress and gather their feedback. This ensured we were aligned on expectations, and any issues were resolved promptly. Ultimately, the project was completed ahead of schedule, which the client appreciated.
Tell me about a time when you implemented a new technique or technology in your conveyor installations.
How to Answer
- 1
Select a specific instance where you used a new technique.
- 2
Describe the technique and why it was needed.
- 3
Explain the implementation process clearly.
- 4
Highlight the outcomes or improvements from the implementation.
- 5
Mention any feedback or recognition you received.
Example Answers
In my last job, I introduced a modular conveyor system design that reduced installation time by 30%. I researched the system, received training, and led the transition. The team adapted well, and our project manager praised the efficiency gains.
Describe how you prioritize tasks during a conveyor installation project.
How to Answer
- 1
Assess the project requirements and timeline
- 2
Identify critical tasks that impact overall progress
- 3
Delegate tasks based on team member strengths
- 4
Use a checklist to track task completion
- 5
Schedule regular check-ins to update progress
Example Answers
I start by reviewing the project plan and deadline, then identify key tasks such as site preparation and equipment assembly. I prioritize tasks that are time-sensitive and delegate roles among my team based on their skills. Using a checklist helps us monitor progress and adjust if needed.
What project are you most proud of in your career as a conveyor installer, and why?
How to Answer
- 1
Choose a specific project that highlights your skills.
- 2
Explain your role and contributions in detail.
- 3
Discuss the challenges faced and how you overcame them.
- 4
Mention the positive impact the project had on the company or team.
- 5
Keep the answer focused on your achievements and learning.
Example Answers
I am most proud of the project where I installed a complex conveyor system in a packaging facility. I led the team and coordinated with other departments to ensure the installation was seamless. We faced tight deadlines, but I implemented a detailed schedule that kept us on track. As a result, we improved the production efficiency by 20% after the installation.
Don't Just Read Conveyor Installer Questions - Practice Answering Them!
Reading helps, but actual practice is what gets you hired. Our AI feedback system helps you improve your Conveyor Installer interview answers in real-time.
Personalized feedback
Unlimited practice
Used by hundreds of successful candidates
Situational Interview Questions
If two team members disagree on the installation approach for a conveyor, how would you handle the situation?
How to Answer
- 1
Listen to both team members' viewpoints without interruption.
- 2
Encourage a discussion to explore each perspective.
- 3
Identify common goals and ensure everyone's focus is on project success.
- 4
If needed, involve a supervisor for a third-party perspective.
- 5
Conclude with a clear plan that incorporates the best elements from both approaches.
Example Answers
I would first listen to both team members to understand their arguments. Then, I'd facilitate a discussion to help them find common ground. If they still can't agree, I would suggest involving a supervisor to help guide the decision.
Suppose your team is falling behind on an installation deadline due to unforeseen circumstances. What steps would you take to address this?
How to Answer
- 1
Assess the specific reasons for the delay quickly
- 2
Communicate with team members for input and ideas
- 3
Reprioritize tasks and set a new timeline
- 4
Consider allocating additional resources or overtime if necessary
- 5
Keep the client updated to manage expectations
Example Answers
First, I would identify the specific issues causing the delay and discuss them with my team. Then, we would prioritize our tasks to focus on critical elements of the installation. If needed, I would consider reallocating resources or extending working hours to meet the deadline. Lastly, I would ensure to keep the client informed about our progress.
Don't Just Read Conveyor Installer Questions - Practice Answering Them!
Reading helps, but actual practice is what gets you hired. Our AI feedback system helps you improve your Conveyor Installer interview answers in real-time.
Personalized feedback
Unlimited practice
Used by hundreds of successful candidates
If a client has unrealistic expectations about the installation timeline, how would you manage their expectations?
How to Answer
- 1
Listen to the client's timeline concerns carefully.
- 2
Provide clear, evidence-based estimates of realistic timelines.
- 3
Explain the factors that influence the installation time.
- 4
Offer a detailed plan that breaks down each phase of the installation.
- 5
Maintain open communication throughout the process to update the client.
Example Answers
I would first listen to the client's concerns to fully understand their expectations. Then, I would provide them with a realistic timeline based on my past experiences, explaining the reasons behind each phase of the installation process.
Imagine you're working with a new team member who is struggling to keep up. What would you do to assist them?
How to Answer
- 1
Assess their specific struggles and understand where they need help.
- 2
Offer to pair up and work together on tasks to provide real-time support.
- 3
Share resources or training materials that could aid their understanding.
- 4
Encourage open communication and check in regularly on their progress.
- 5
Be patient and provide positive reinforcement to build their confidence.
Example Answers
I would first talk to them to find out where they are struggling and offer to assist with those specific tasks. Then, I would suggest working together on a few projects to help them learn the ropes faster.
If you realized the installation would exceed the budget, what actions would you take to rectify this?
How to Answer
- 1
Assess the reasons for the budget overrun promptly.
- 2
Communicate with stakeholders about the situation and implications.
- 3
Consider alternative solutions or adjustments to the installation plan.
- 4
Negotiate with suppliers or subcontractors for better pricing.
- 5
Document all changes and decisions for transparency.
Example Answers
I would first identify the exact reasons for exceeding the budget and discuss it with my team. Then, I would communicate with the client to explain the situation and propose cost-saving measures to bring the project back on track.
If a critical piece of equipment fails during installation, what immediate steps would you take?
How to Answer
- 1
Assess the situation to understand the severity of the failure
- 2
Communicate with your team to inform them of the issue
- 3
Stop all operations related to the installation until the issue is resolved
- 4
Check for backup equipment or alternative solutions
- 5
Contact maintenance or repairs personnel if necessary
Example Answers
First, I would quickly assess the situation to figure out what went wrong. Then, I would inform my team about the failure and pause all installation activities to ensure safety. I would look for any backup equipment we might have or alternative plans we can implement, and if needed, I'd call in maintenance for support.
How would you approach training a new technician on conveyor installation processes?
How to Answer
- 1
Start with a safety orientation to ensure the new technician understands safety protocols.
- 2
Use a step-by-step demonstration of the installation process to provide a clear model.
- 3
Encourage hands-on practice while you supervise, allowing them to build confidence.
- 4
Provide resources such as installation manuals and diagrams for reference.
- 5
Set up follow-up evaluations to assess their understanding and provide feedback.
Example Answers
I would begin by ensuring the new technician understands all safety protocols. Then, I'd demonstrate the installation process step-by-step, ensuring they can see each part in action. After that, I'd let them try it hands-on while I supervise to give guidance. I would also give them manuals to look at for reference and check their progress regularly with feedback.
If a client requests a modification to the conveyor design after installation has begun, how would you handle it?
How to Answer
- 1
Acknowledge the client's request and its importance.
- 2
Assess the feasibility of the modification considering current work.
- 3
Communicate any impacts on timelines or costs clearly.
- 4
Discuss alternative solutions if the modification is not practical.
- 5
Ensure documentation of the agreed changes for clarity.
Example Answers
I would first listen to the client and understand their needs clearly. Then, I'd evaluate the design to see if the change is feasible or if it will impact the project timeline or cost. If it's possible, I'd discuss these implications with the client and get their approval before proceeding.
During an installation, you notice that safety protocols are not being followed. What would you do?
How to Answer
- 1
Assess the situation to determine the severity of the safety violation.
- 2
Communicate immediately with the team about the observed safety issue.
- 3
Refer to company safety policies and procedures to verify correct protocols.
- 4
If necessary, stop the installation until safety is restored.
- 5
Report the incident to a supervisor or safety officer for further action.
Example Answers
I would first assess the situation to understand the risks involved. Then, I would immediately inform my team about the safety protocols being overlooked to ensure everyone is aware. If the issue poses a serious risk, I would stop work to ensure no one is in danger and report the situation to my supervisor.
If project stakeholders have conflicting requirements, how would you facilitate a resolution?
How to Answer
- 1
Identify the key stakeholders involved in the conflict.
- 2
Listen to each party's requirements and concerns without bias.
- 3
Encourage open communication to understand the rationale behind each requirement.
- 4
Find common ground or compromise that meets the essential needs of all parties.
- 5
Document the agreed resolution and follow-up to ensure satisfaction.
Example Answers
First, I would gather all stakeholders to understand their individual concerns. I would listen actively to each party, clarifying their needs. Then, I would facilitate a discussion to explore potential compromises, aiming to align on a solution that addresses the main issues of each group.
Don't Just Read Conveyor Installer Questions - Practice Answering Them!
Reading helps, but actual practice is what gets you hired. Our AI feedback system helps you improve your Conveyor Installer interview answers in real-time.
Personalized feedback
Unlimited practice
Used by hundreds of successful candidates
How would you allocate resources effectively in a project with limited manpower?
How to Answer
- 1
Assess the project tasks and prioritize them based on urgency and importance
- 2
Identify critical skills needed for the project and assign the right team members
- 3
Break down large tasks into smaller, manageable parts for better resource allocation
- 4
Implement clear communication to keep the team aligned on roles and responsibilities
- 5
Regularly review progress and adjust resource allocation as necessary
Example Answers
I would start by prioritizing the most critical tasks that need immediate attention. By breaking down the work into smaller parts, I can allocate my limited team members more effectively according to their strengths.
Conveyor Installer Position Details
Recommended Job Boards
ZipRecruiter
www.ziprecruiter.com/Jobs/Conveyor-InstallationThese job boards are ranked by relevance for this position.
Related Positions
- Conveyor Belt Installer
- Conveyor Mechanic
- Tool Setter
- Outfitter
- Conveyor Loader
- Conveyor Worker
- Elevator Installer
- Pump Installer
- Window Installer
- Software Installer
Similar positions you might be interested in.
Ace Your Next Interview!
Practice with AI feedback & get hired faster
Personalized feedback
Used by hundreds of successful candidates
Ace Your Next Interview!
Practice with AI feedback & get hired faster
Personalized feedback
Used by hundreds of successful candidates