Top 30 Valver Interview Questions and Answers [Updated 2025]
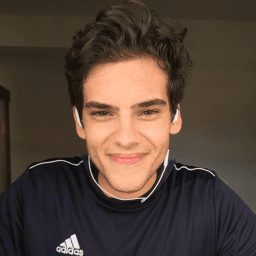
Andre Mendes
•
March 30, 2025
Preparing for a Valver interview can be daunting, but this post will equip you with the most common questions candidates face. Dive in to discover expertly crafted example answers and insightful tips to enhance your responses. Whether you're a seasoned professional or new to the field, this guide is designed to boost your confidence and help you impress your interviewers with effective communication.
Download Valver Interview Questions in PDF
To make your preparation even more convenient, we've compiled all these top Valverinterview questions and answers into a handy PDF.
Click the button below to download the PDF and have easy access to these essential questions anytime, anywhere:
List of Valver Interview Questions
Behavioral Interview Questions
Tell me about a time when you encountered a significant problem in your work. How did you approach resolving it?
How to Answer
- 1
Start by clearly stating the problem you faced.
- 2
Describe the context to provide background.
- 3
Explain the steps you took to investigate and resolve the issue.
- 4
Highlight the outcome and what you learned.
- 5
Keep it focused and concise, ideally under 2 minutes.
Example Answers
In my previous role, our project was behind schedule due to unexpected technical challenges. I first gathered the team to identify the key issues. We brainstormed potential solutions, and I led us in prioritizing tasks based on impact. By reallocating resources and adjusting our timeline, we managed to deliver the project just in time, and I learned the value of team collaboration in crisis.
Can you describe a time when you had to work closely with a team to complete a challenging project?
How to Answer
- 1
Choose a specific project with clear challenges.
- 2
Focus on your role and contributions to teamwork.
- 3
Highlight communication and collaboration efforts.
- 4
Emphasize the outcomes and what was learned.
- 5
Be concise and keep it relevant to the position.
Example Answers
In my last role, our team was tasked with launching a new product under a tight deadline. I took on the role of coordinator, ensuring everyone was aligned on tasks. We held daily check-ins, which helped us tackle issues quickly. In the end, we launched on time, and the product exceeded initial sales goals. This taught me the importance of strong teamwork and communication.
Don't Just Read Valver Questions - Practice Answering Them!
Reading helps, but actual practice is what gets you hired. Our AI feedback system helps you improve your Valver interview answers in real-time.
Personalized feedback
Unlimited practice
Used by hundreds of successful candidates
Describe an instance where you had to take the lead on a project. What was your approach?
How to Answer
- 1
Choose a specific project that highlights your leadership skills
- 2
Explain your role and responsibilities clearly
- 3
Discuss the challenges you faced and how you overcame them
- 4
Highlight collaboration with team members and stakeholders
- 5
Finish with the outcome and what you learned from the experience
Example Answers
In my previous role, I led a project to implement a new CRM system. I organized the team, set clear goals, and scheduled regular check-ins. We faced resistance from some team members, so I facilitated discussions to address concerns. The project was completed on time and improved our customer tracking significantly.
Can you give an example of a time when you had to adapt to a significant change in your work environment?
How to Answer
- 1
Think of a specific instance when change occurred.
- 2
Describe what the change was and how it impacted you.
- 3
Highlight the actions you took to adapt to the change.
- 4
Emphasize the positive outcomes from your adaptation.
- 5
Keep your answer concise and focused on your role.
Example Answers
In my last job, our team underwent a major software transition from a legacy system to a cloud-based solution. I organized training sessions for the team to get everyone up to speed, and I took the initiative to learn the new platform myself. This helped us complete our projects on time and improve our efficiency.
Describe a time you contributed to a significant improvement in a process related to valve operation.
How to Answer
- 1
Identify the specific process you improved
- 2
Explain what the challenge was
- 3
Describe the steps you took to implement the improvement
- 4
Quantify the results where possible
- 5
Mention any collaborative efforts with your team or other departments
Example Answers
In my previous role, we faced frequent valve failures causing downtime. I analyzed the maintenance schedule and realized it was outdated. I proposed implementing a predictive maintenance strategy based on usage data, which we calibrated over three months. This reduced downtime by 30% and increased production efficiency.
How have you prioritized safety in your previous roles related to valve management?
How to Answer
- 1
Discuss specific safety protocols you followed.
- 2
Mention any training or certifications related to safety.
- 3
Provide an example of a safety incident and how you managed it.
- 4
Highlight collaboration with safety teams or engineers.
- 5
Emphasize continuous improvement practices you implemented.
Example Answers
In my last role, I strictly followed all valve inspection protocols to ensure compliance with safety standards. I undertook safety training and was part of a committee that reviewed safety incidents regularly.
Can you discuss a time when you trained others on valve testing techniques? What were the outcomes?
How to Answer
- 1
Choose a specific training experience to discuss
- 2
Highlight the techniques you taught clearly
- 3
Explain the training method you used, such as hands-on practice or demonstrations
- 4
Emphasize the positive outcomes or improvements seen after the training
- 5
Mention any feedback received from trainees or supervisors
Example Answers
I trained a group of new technicians on valve testing using a hands-on approach. After conducting three sessions, the team improved their testing accuracy by 30%, and I received positive feedback from my supervisor about the enhanced team performance.
Provide an example of a challenging deadline you met. How did you manage your time?
How to Answer
- 1
Think of a specific project with a tight deadline.
- 2
Outline your planning process before starting the task.
- 3
Describe any tools or methods you used for time management.
- 4
Mention how you communicated with your team during this time.
- 5
Highlight the outcome and what you learned from the experience.
Example Answers
In my previous role, we had a project with a two-week deadline for a client presentation. I created a detailed timeline, breaking the work into daily tasks. I used Trello to track progress and checked in with the team daily to address any obstacles. We completed the project on time, and the client praised our work.
Tell me about a time when you identified an inefficiency in the valve production process. What did you do to address it?
How to Answer
- 1
Identify a specific example from your experience
- 2
Describe the inefficiency clearly and its impact
- 3
Explain the steps you took to investigate and address it
- 4
Highlight the results or improvements achieved
- 5
Use metrics or specific outcomes to demonstrate success
Example Answers
In my previous role, I noticed that the valve assembly line was experiencing delays due to frequent material shortages. I analyzed the supply chain process and found that certain parts were being ordered too late. I collaborated with the procurement team to establish a better forecasting method for inventory that reduced shortages by 30%.
Don't Just Read Valver Questions - Practice Answering Them!
Reading helps, but actual practice is what gets you hired. Our AI feedback system helps you improve your Valver interview answers in real-time.
Personalized feedback
Unlimited practice
Used by hundreds of successful candidates
Technical Interview Questions
What are the key factors to consider when selecting a valve for a specific application?
How to Answer
- 1
Identify the medium flowing through the valve.
- 2
Consider the pressure and temperature conditions.
- 3
Evaluate the required flow control precision.
- 4
Account for the installation environment and space constraints.
- 5
Review compatibility with materials and maintenance requirements.
Example Answers
When selecting a valve, I first consider the medium, whether it's gas or liquid, as this impacts valve type. Then, I analyze the pressure and temperature rated for the system to ensure safety and performance. Additionally, flow control precision is key for applications with strict requirements.
Explain the standard procedures you follow for testing valve performance.
How to Answer
- 1
Start with a brief overview of the testing process.
- 2
Outline specific tests you perform, such as leakage test and functional test.
- 3
Mention the equipment and standards used for testing.
- 4
Discuss how you document results and any troubleshooting steps.
- 5
Emphasize safety protocols you adhere to during testing.
Example Answers
I begin testing by conducting a visual inspection of the valve, checking for any obvious defects. Then, I perform a leakage test using a pressure gauge and a soap solution. Next, I carry out a functional test to ensure the valve opens and closes smoothly. I document each step in a test report and address any discrepancies immediately, following safety protocols throughout.
Don't Just Read Valver Questions - Practice Answering Them!
Reading helps, but actual practice is what gets you hired. Our AI feedback system helps you improve your Valver interview answers in real-time.
Personalized feedback
Unlimited practice
Used by hundreds of successful candidates
What materials do you consider best for valve construction, and why?
How to Answer
- 1
Identify key materials commonly used for valves like stainless steel, brass, and plastic.
- 2
Explain the advantages of each material in terms of durability, corrosion resistance, and application.
- 3
Mention specific applications where each material excels.
- 4
Consider environmental factors affecting material choice, like temperature and pressure.
- 5
Be prepared to discuss trade-offs between costs and performance.
Example Answers
I believe stainless steel is ideal for valves due to its excellent corrosion resistance and durability, making it suitable for high-pressure applications and harsh environments.
What industry standards and regulations are critical to comply with in valve manufacturing?
How to Answer
- 1
Identify key standards like ISO 9001 for quality management.
- 2
Mention industry-specific regulations such as ASME for pressure equipment.
- 3
Discuss safety standards like API for petroleum and natural gas.
- 4
Include environmental regulations relevant to manufacturing processes.
- 5
Be prepared to discuss how compliance affects design and production.
Example Answers
In valve manufacturing, key industry standards include ISO 9001 for overall quality management, ASME standards for pressure equipment, and API standards specifically for valves used in the petroleum industry. Compliance with these ensures product safety and reliability.
How do you diagnose a malfunctioning valve in a pipeline system?
How to Answer
- 1
Start by gathering data about the valve's performance
- 2
Check for visible leaks around the valve and connections
- 3
Use diagnostic tools like pressure gauges and flow meters
- 4
Perform a manual inspection of the valve for any physical damage
- 5
Review the operational history of the valve for patterns of failure
Example Answers
To diagnose a malfunctioning valve, I first gather data on its performance metrics such as pressure and flow readings. Then, I inspect the valve visually for leaks or signs of wear. Using a pressure gauge, I check if the pressure upstream and downstream is within expected ranges. If there are anomalies, I analyze whether it might be a sealing issue or a mechanical failure.
What steps would you follow to ensure the correct installation of a valve in a high-pressure system?
How to Answer
- 1
Review the valve and system specifications carefully before installation
- 2
Ensure all necessary tools and safety equipment are ready and functional
- 3
Follow the manufacturer’s installation instructions precisely
- 4
Check for compatibility of the valve with the system materials
- 5
Conduct pressure tests after installation to verify integrity and prevent leaks
Example Answers
First, I would review the valve specifications and the high-pressure system requirements. Then, I’d gather all necessary tools and confirm our safety measures are in place. Following the manufacturer’s instructions meticulously is crucial, and I’d ensure the valve is compatible with the materials in use. Finally, I would perform thorough pressure tests to check for any leaks.
How do you calibrate valves and what instruments do you typically use?
How to Answer
- 1
Start by explaining the importance of valve calibration for accurate control.
- 2
Describe the steps you take to perform calibration including any pre-checks.
- 3
Mention the specific instruments you use like pressure gauges and test rigs.
- 4
Highlight the necessity of following manufacturer specifications during calibration.
- 5
Conclude with any safety measures you take while calibrating valves.
Example Answers
To calibrate valves, I first ensure they are clean and in good working condition. I use a pressure gauge to measure the output precisely, adjusting the valve position according to the manufacturer's specifications until the desired flow rate is achieved. I always check for leaks and ensure safety procedures are followed.
What is your understanding of valve actuation systems and their importance in automation?
How to Answer
- 1
Define valve actuation systems clearly, mentioning the key components.
- 2
Explain the types of actuators commonly used, such as electric, pneumatic, and hydraulic.
- 3
Discuss the role of valve actuation in automation, emphasizing control and safety.
- 4
Mention real-world applications to illustrate the importance in industries.
- 5
Keep your explanation concise, focusing on clarity and relevance.
Example Answers
Valve actuation systems consist of devices that control the opening and closing of valves based on automation signals. Common types include electric actuators for precision control and pneumatic actuators for quick response times. They are critical in automation for efficient fluid control and ensuring system safety, such as in chemical processing facilities.
What role does fluid dynamics play in valve design and function?
How to Answer
- 1
Understand key fluid dynamics principles like flow rate and pressure drop.
- 2
Discuss how these principles influence valve sizing and selection.
- 3
Mention the impact of turbulence and laminar flow on valve performance.
- 4
Highlight the importance of fluid characteristics like viscosity and density.
- 5
Relate how simulations and tests in fluid dynamics optimize valve design.
Example Answers
Fluid dynamics is crucial in valve design as it helps us understand the flow rate and pressure drop across the valve. This informs how we size the valves for specific applications and ensures optimal performance while minimizing energy loss.
How would you conduct a failure analysis on a valve that failed during operation?
How to Answer
- 1
Gather relevant data on the valve's operating conditions at the time of failure.
- 2
Inspect the failed valve thoroughly for physical damage and signs of wear.
- 3
Review maintenance records and previous performance for anomalies.
- 4
Identify possible causes such as material defects, improper installation, or operational issues.
- 5
Document findings and recommend corrective actions to prevent future failures.
Example Answers
I would start by collecting all data regarding the valve's operating conditions leading up to the failure. Next, I would conduct a physical inspection to look for any visible damage or signs of wear. I would also check maintenance records for any previous issues. After analyzing all this information, I would determine possible causes like material defects or installation errors, and finally, I would document my findings and suggest improvements.
Don't Just Read Valver Questions - Practice Answering Them!
Reading helps, but actual practice is what gets you hired. Our AI feedback system helps you improve your Valver interview answers in real-time.
Personalized feedback
Unlimited practice
Used by hundreds of successful candidates
What criteria do you consider critical when evaluating a valve's performance after testing?
How to Answer
- 1
Focus on flow rate and pressure drop as key performance indicators.
- 2
Evaluate leak tightness to ensure no unwanted flow occurs.
- 3
Assess response time to changes in operation conditions.
- 4
Consider durability and resistance to wear and corrosion.
- 5
Examine user feedback for real-world performance insights.
Example Answers
I consider flow rate and pressure drop critical. If a valve does not meet the specified flow rate with an acceptable pressure drop, it's not functioning efficiently. Additionally, I always check for leak tightness since any leakage can lead to system failures.
Situational Interview Questions
Imagine you are behind schedule on a critical valve installation. How would you communicate this to your clients and what steps would you take to rectify the situation?
How to Answer
- 1
Be proactive in communication; inform clients as soon as possible.
- 2
Clearly explain the reasons for the delay without making excuses.
- 3
Outline a specific plan of action to get back on schedule.
- 4
Provide an updated timeline for the completion of the installation.
- 5
Offer to discuss any concerns or questions the client may have.
Example Answers
I would first contact the client immediately to inform them about the delay. I would explain that unforeseen issues arose during installation. Then I would outline a plan to expedite the work by reallocating resources and increasing labor hours, and provide a revised timeline for completion.
If you noticed that a colleague was bypassing safety protocols during valve testing, what would you do?
How to Answer
- 1
Assess the situation quickly and ensure immediate safety.
- 2
Document your observations clearly and factually.
- 3
Address the issue directly with the colleague to understand their actions.
- 4
Report the incident to a supervisor if the behavior continues.
- 5
Encourage a culture of safety and open communication.
Example Answers
I would first assess whether anyone is in immediate danger and ensure that the situation is safe. Then, I would document what I observed and speak to my colleague to understand why they bypassed the protocols. If the issue persists, I would escalate it to a supervisor.
Don't Just Read Valver Questions - Practice Answering Them!
Reading helps, but actual practice is what gets you hired. Our AI feedback system helps you improve your Valver interview answers in real-time.
Personalized feedback
Unlimited practice
Used by hundreds of successful candidates
A client is unhappy with the performance of a valve you provided. How would you handle the situation?
How to Answer
- 1
Listen actively to the client's concerns to understand the issue clearly
- 2
Acknowledge the client's feelings and express your commitment to resolving the issue
- 3
Ask specific questions to gather detailed information about the performance problem
- 4
Propose a solution, such as troubleshooting steps or sending a replacement valve
- 5
Follow up after the resolution to ensure the client is satisfied with the outcome
Example Answers
I would first listen carefully to the client's specific concerns about the valve's performance. After understanding their issue, I would acknowledge their frustration and assure them I am committed to finding a solution. I'd ask detailed questions to pinpoint the problem, then suggest troubleshooting steps or offer to replace the valve. Finally, I'd follow up to ensure their satisfaction with the resolution.
In a situation where there are conflicting specifications for a valve from different departments, how would you decide on the best course of action?
How to Answer
- 1
Identify the key stakeholders involved in the conflicting specifications.
- 2
Gather all specifications and clarify the requirements from each department.
- 3
Evaluate the impact of each specification on performance, safety, and cost.
- 4
Facilitate a meeting with stakeholders to discuss and negotiate the requirements.
- 5
Document the agreed-upon specifications for future reference.
Example Answers
I would start by identifying all stakeholders involved in the specifications. Next, I would gather the conflicting specs from each department. After evaluating the impact on performance and costs, I would arrange a meeting to discuss these differences and reach a consensus.
You are assigned a team to develop a new valve prototype, but some members are not cooperating. What strategies would you employ to enhance teamwork?
How to Answer
- 1
Identify the root cause of the lack of cooperation
- 2
Facilitate open communication among team members
- 3
Set clear roles and responsibilities for each member
- 4
Encourage team bonding activities to build trust
- 5
Establish regular check-ins to monitor progress and address issues
Example Answers
I would start by having one-on-one conversations with team members to understand the reasons behind their lack of cooperation. Then, I would hold a team meeting to discuss our project goals and ensure everyone is clear on their roles. To build trust, we could engage in team-building activities outside of work.
You discover that a batch of valves has a manufacturing defect that could lead to failure. What actions do you take?
How to Answer
- 1
Immediately report the issue to your supervisor and quality control team
- 2
Isolate the affected batch to prevent further distribution
- 3
Assess the severity of the defect and gather data on potential impacts
- 4
Communicate with production teams to halt any use of the defective valves
- 5
Develop a corrective action plan to rectify the defect and prevent recurrence
Example Answers
First, I would inform my supervisor and the quality control team about the defect to ensure proper action is taken. Then, I would isolate the affected valves to stop them from being shipped or used. After that, I would assess how severe the defect is and document my findings before we discuss further steps.
You are tasked with improving the quality assurance process for valves. What specific measures would you implement?
How to Answer
- 1
Assess the current quality assurance process to identify weaknesses.
- 2
Implement standardized testing protocols for all valve types.
- 3
Introduce error tracking and reporting systems for defects.
- 4
Train staff on quality standards and inspection techniques.
- 5
Regularly review and update quality control measures based on feedback.
Example Answers
I would first conduct a thorough assessment of the existing quality assurance process to pinpoint specific areas for improvement, such as testing and defect tracking. Next, I would establish standardized testing protocols for all valve products to ensure consistency and reliability.
If you were given a limited budget to redesign a valve, how would you prioritize your spending?
How to Answer
- 1
Identify key areas for improvement like performance or durability
- 2
Consider cost-effective materials that maintain quality
- 3
Focus on features that provide maximum benefit to users
- 4
Engage with stakeholders to understand essential needs
- 5
Ensure compliance with safety and regulatory standards
Example Answers
I would first invest in high-quality materials that enhance durability and performance, ensuring the valve lasts longer and requires less frequent replacements. Next, I would prioritize features that increase user safety and compliance, followed by cost-effective solutions for aesthetic improvements.
You need to collaborate with a supplier to improve the quality of valve components. What steps would you take to ensure effective communication?
How to Answer
- 1
Establish clear communication channels and points of contact.
- 2
Schedule regular meetings to discuss progress and concerns.
- 3
Use collaboration tools for document sharing and updates.
- 4
Set measurable quality targets and review them together.
- 5
Encourage open feedback to address issues promptly.
Example Answers
I would first establish a primary contact with the supplier to streamline communication. We would schedule bi-weekly meetings to review quality targets and performance. Using tools like Slack and shared documents would ensure we are always on the same page.
Valver Position Details
Related Positions
- Valve Fitter
- Ventilator
- Flanger
- Perforator
- Door Puller
- Door Opener
- Valve Maker
- Valve Mechanic
- Valve Grinder
- Valve Technician
Similar positions you might be interested in.
Ace Your Next Interview!
Practice with AI feedback & get hired faster
Personalized feedback
Used by hundreds of successful candidates
Ace Your Next Interview!
Practice with AI feedback & get hired faster
Personalized feedback
Used by hundreds of successful candidates