Top 31 Valve Fitter Interview Questions and Answers [Updated 2025]
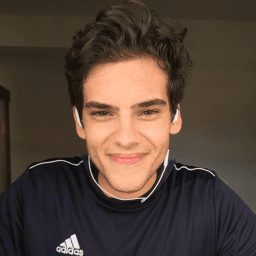
Andre Mendes
•
March 30, 2025
Preparing for a Valve Fitter interview can be daunting, but with the right guidance, you can tackle it confidently. In this blog post, we delve into the most common interview questions for the Valve Fitter role, offering insightful example answers and practical tips to help you respond effectively. Whether you're a seasoned professional or new to the field, this guide is designed to boost your interview readiness and confidence.
Download Valve Fitter Interview Questions in PDF
To make your preparation even more convenient, we've compiled all these top Valve Fitterinterview questions and answers into a handy PDF.
Click the button below to download the PDF and have easy access to these essential questions anytime, anywhere:
List of Valve Fitter Interview Questions
Behavioral Interview Questions
Can you describe a time when you had to work closely with a team to solve a valve fitting issue?
How to Answer
- 1
Think of a specific example involving teamwork in valve fitting.
- 2
Use the STAR method: Situation, Task, Action, Result.
- 3
Highlight your role and contributions within the team.
- 4
Mention any challenges faced and how the team overcame them.
- 5
Emphasize the successful outcome and any lessons learned.
Example Answers
In my last position, our team faced a leak in a critical valve fitting during a major project. I coordinated with the engineers to assess the situation, while the technicians collected necessary tools. Together, we developed a solution to replace the faulty valve. The leak was fixed within hours, allowing the project to stay on schedule.
Tell me about a challenging project you worked on involving valve fittings and how you overcame the obstacles.
How to Answer
- 1
Choose a specific project that had clear challenges related to valve fittings.
- 2
Describe the obstacles you faced in the project and their impact.
- 3
Explain the actions you took to address these challenges.
- 4
Highlight the positive outcome and what you learned.
- 5
Keep your response concise and focused on your role and contributions.
Example Answers
In my previous job, I worked on a pipeline installation project where we had to replace outdated valve fittings. The challenge was that the existing fittings were corroded and difficult to remove. I organized a team to assess and cut through the corrosion using specialized tools. After replacing the fittings, we tested the system thoroughly before finishing the installation. The project was completed ahead of schedule, and I learned the importance of teamwork and thorough preparation.
Don't Just Read Valve Fitter Questions - Practice Answering Them!
Reading helps, but actual practice is what gets you hired. Our AI feedback system helps you improve your Valve Fitter interview answers in real-time.
Personalized feedback
Unlimited practice
Used by hundreds of successful candidates
Have you ever encountered a safety violation related to valve fitting? How did you handle it?
How to Answer
- 1
Start with a clear description of the safety violation you observed.
- 2
Explain the potential risks associated with that violation.
- 3
Detail the steps you took to address the issue immediately.
- 4
Mention any reporting procedures you followed.
- 5
Discuss the outcome and any changes made to prevent future violations.
Example Answers
During a valve fitting project, I noticed a colleague not wearing proper PPE. I approached him, highlighted the risk of injury, and reminded him to wear his safety gear. I reported the incident to our supervisor to ensure it was documented, and we held a safety briefing afterward to reinforce PPE use.
Describe a situation where you had to lead a team in the installation of valve systems. What was the outcome?
How to Answer
- 1
Choose a specific project where you led the installation.
- 2
Mention your role and responsibilities clearly.
- 3
Outline the team's structure and key challenges faced.
- 4
Discuss the outcome, focusing on results achieved.
- 5
Highlight any learning or improvements made as a result.
Example Answers
In my previous role, I led a team of 5 during the installation of a new valve system for a chemical plant. My responsibility was to coordinate the initial design with the engineering team and manage the on-site installation. We faced delays due to unforeseen weather conditions, but by adjusting our schedule and increasing labor hours, we completed the project within a week of the deadline, saving the company significant costs. The valve system has since operated without issues.
Give an example of how you effectively communicated complex valve fitting concepts to non-technical stakeholders.
How to Answer
- 1
Start with a specific situation where communication was needed.
- 2
Choose clear, simple language to explain technical concepts.
- 3
Use analogies or examples to make ideas relatable.
- 4
Ensure to highlight feedback received after your explanation.
- 5
Summarize the outcome of your communication effort.
Example Answers
In a recent project, I had to explain valve functionality to the marketing team. I used a water flow analogy, comparing valves to faucets. After explaining, I asked if they understood, and they confirmed they did. This helped them sell our products more effectively.
Tell me about a time when you had to adapt quickly to a change in project specifications related to valve fitting.
How to Answer
- 1
Describe the situation briefly to set the context.
- 2
Explain the specific change in project specifications.
- 3
Detail how you responded to the change effectively.
- 4
Highlight any tools or techniques you used to adapt.
- 5
Conclude with the outcome and what you learned.
Example Answers
In my last project, we were tasked with retrofitting a valve system for a client. Midway through, they requested a different valve type that required a complete redesign. I quickly reviewed the new specifications, consulted with the team, and adjusted our plans to incorporate the new valves. We managed to rework the schedule, and in two weeks, we delivered the revised system ahead of time.
Describe a time when you identified a potential quality issue in your work on valve systems. What did you do about it?
How to Answer
- 1
Think of a specific instance where you noticed a quality problem.
- 2
Explain how you identified the issue and its potential impact.
- 3
Describe the steps you took to address the issue swiftly.
- 4
Mention any collaboration with team members if applicable.
- 5
End with the outcome and what you learned from the situation.
Example Answers
In my last job, I was inspecting a batch of valve installations and noticed that the sealing surfaces showed signs of wear. I immediately reported this to my supervisor and we decided to halt further installations. I worked with the team to inspect the entire batch and identified a manufacturing defect in the seals, which we corrected before continuing the installation. This prevented any potential leaks in the field.
Can you discuss an innovative method or approach you implemented in your valve fitting work?
How to Answer
- 1
Identify a specific innovation or method you developed.
- 2
Explain the problem that prompted your innovation.
- 3
Describe the process you used to implement the method.
- 4
Share the results or benefits that came from your innovative approach.
- 5
Keep your answer focused and structured for clarity.
Example Answers
I developed a new sealing method using a hybrid material that reduced leaks by 30%. This was in response to recurring issues with traditional sealants failing under high pressure.
Describe how you manage your time to ensure all valve fitting tasks are completed on schedule.
How to Answer
- 1
Prioritize tasks based on deadlines and complexity.
- 2
Break down larger tasks into smaller, manageable steps.
- 3
Allocate specific time blocks for each task in your schedule.
- 4
Use checklists to track progress and ensure nothing is missed.
- 5
Regularly review your progress and adjust your schedule as needed.
Example Answers
I prioritize my valve fitting tasks by their deadlines. I create a checklist that helps me break down larger projects into smaller steps, which I allocate specific time blocks to complete. This way, I can stay on schedule and adjust if I notice I'm falling behind.
How have you continued to develop your skills as a valve fitter?
How to Answer
- 1
Discuss attending workshops and training sessions to stay updated on the latest technologies
- 2
Mention pursuing relevant certifications or qualifications that enhance your technical skills
- 3
Talk about hands-on experience gained through various projects or job roles
- 4
Emphasize keeping up with industry trends and innovations through reading and networking
- 5
Include any mentorship or guidance sought from more experienced fitters to advance skills
Example Answers
I have attended several workshops on new valve technologies and recently completed a certification course in valve maintenance, which has greatly improved my technical knowledge.
Don't Just Read Valve Fitter Questions - Practice Answering Them!
Reading helps, but actual practice is what gets you hired. Our AI feedback system helps you improve your Valve Fitter interview answers in real-time.
Personalized feedback
Unlimited practice
Used by hundreds of successful candidates
Technical Interview Questions
What are the key steps you take when installing a new valve in a piping system?
How to Answer
- 1
Ensure the piping system is depressurized and drained before starting.
- 2
Inspect the valve and surrounding area for any damage or obstructions.
- 3
Align the valve correctly with the pipe flanges before securing it.
- 4
Use appropriate gaskets and hardware to avoid leaks.
- 5
Perform a pressure test after installation to confirm proper operation.
Example Answers
First, I make sure the system is fully depressurized and any fluid is drained. Then, I check the valve and area for any issues. I align the valve with the flanges before tightening it down with the proper gaskets in place. Finally, I conduct a pressure test to ensure everything is functioning correctly.
Can you explain the process you use to troubleshoot and repair a malfunctioning valve?
How to Answer
- 1
Start with identifying symptoms of the malfunction.
- 2
Perform visual inspections for leaks or damage.
- 3
Test valve operation and assess its performance.
- 4
Use tools to disassemble and inspect internal components if needed.
- 5
Reassemble the valve and conduct functional tests before finalizing.
Example Answers
First, I identify the symptoms such as leaks or improper flow. Then I perform a visual inspection for any visible damage. If everything looks good, I test the valve for proper operation. If it still malfunctions, I disassemble it to check the internal components. Finally, after repairs, I reassemble it and run tests to ensure it's functioning correctly.
Don't Just Read Valve Fitter Questions - Practice Answering Them!
Reading helps, but actual practice is what gets you hired. Our AI feedback system helps you improve your Valve Fitter interview answers in real-time.
Personalized feedback
Unlimited practice
Used by hundreds of successful candidates
What industry standards do you follow when fitting valves, and why are they important?
How to Answer
- 1
Identify relevant standards such as ASME, API, or ISO.
- 2
Explain how these standards ensure safety and reliability.
- 3
Mention specific procedures from these standards that you apply.
- 4
Discuss the importance of compliance in avoiding failures and leaks.
- 5
Conclude by emphasizing the role of standards in maintaining industry credibility.
Example Answers
I follow ASME standards when fitting valves, as they provide guidelines for ensuring proper installation and safety. These standards help prevent leaks and mechanical failures, which is crucial in maintaining system integrity.
What tools and equipment do you consider essential for a valve fitter?
How to Answer
- 1
Start by listing hand tools specific to valve fitting such as wrenches and pliers.
- 2
Include measuring tools like calipers and pressure gauges to emphasize precision.
- 3
Mention any power tools or specialized equipment like valve actuators or hydraulic equipment.
- 4
Discuss safety gear since it’s vital in any fitting job.
- 5
Conclude by highlighting how these tools enhance efficiency and safety in the work process.
Example Answers
As a valve fitter, I consider essential tools like adjustable wrenches, pipe wrenches, and pliers for manual adjustments. I also use calipers for precise measurements and pressure gauges to ensure the valves function correctly. Additionally, hydraulic equipment aids in handling larger valves, and I always prioritize safety gear like goggles and gloves.
How do you determine the correct fittings and valve types for specific applications?
How to Answer
- 1
Analyze the media being transported: its type, pressure, and temperature.
- 2
Consider the application environment: is it indoor, outdoor, or corrosive?
- 3
Consult relevant industry standards or specifications for valve selection.
- 4
Evaluate the flow requirements: is it a high flow or low flow situation?
- 5
Discuss with engineering or design teams to align with system designs.
Example Answers
I begin by analyzing the media, such as water or gas, and its properties like pressure and temperature. For instance, high-pressure steam requires specific fittings.
What information do you need to accurately fit a valve in a specific application?
How to Answer
- 1
Identify the fluid type and its properties
- 2
Determine the pressure and temperature conditions
- 3
Assess the flow requirements including flow direction
- 4
Check the valve size and connection type needed
- 5
Understand the specific application or system environment
Example Answers
To accurately fit a valve, I need to know the type of fluid being handled, such as whether it's gas or liquid, as well as its temperature and pressure. This information helps me choose the right valve material and design.
What types of materials do you commonly work with when fitting valves and why?
How to Answer
- 1
Identify common materials used in valve fittings, like metals, plastics, and alloys.
- 2
Explain the reasons for using each material, focusing on durability, pressure ratings, and resistance to corrosion.
- 3
Discuss specific applications where these materials are preferred.
- 4
Mention any relevant industry standards that influence material choice.
- 5
Be prepared to relate your past experience with these materials.
Example Answers
I commonly work with stainless steel, PVC, and bronze when fitting valves. Stainless steel is great for high-pressure systems due to its strength and corrosion resistance. PVC is typically used in chemical applications because it resists many harsh chemicals. Bronze is often preferred in marine environments because it's corrosion-resistant in salty conditions.
How do you perform pressure tests on newly installed valves to ensure they meet safety standards?
How to Answer
- 1
Identify the type of pressure test required, such as hydrostatic or pneumatic.
- 2
Ensure all equipment is calibrated and safety protocols are in place before starting.
- 3
Gradually increase the pressure to the specified test level while monitoring for leaks.
- 4
Document the pressure readings and duration of the test for compliance.
- 5
Inspect the valve thoroughly after the test to ensure it operates correctly and safely.
Example Answers
To perform a pressure test, I first determine if a hydrostatic or pneumatic test is required based on the valve type. I ensure that all equipment, including gauges and connections, are calibrated and that I follow all safety protocols. During the test, I gradually increase the pressure to the specified level while carefully monitoring for any leaks. After the test, I document the pressure readings and inspection results to ensure compliance with safety standards.
What regulatory considerations must be taken into account when fitting valves in a facility?
How to Answer
- 1
Understand relevant industry regulations like ASME and API standards.
- 2
Be aware of local and federal safety regulations such as OSHA requirements.
- 3
Consider environmental regulations that pertain to emissions and spill prevention.
- 4
Ensure compliance with any specific operational procedures outlined in the facility's safety manual.
- 5
Stay updated on any recent changes in regulations that could affect valve fitting.
Example Answers
When fitting valves, I always ensure compliance with ASME standards and follow OSHA regulations to maintain safety. Environmental considerations for emissions also guide my selection of valves.
How do you maintain documentation and records for your valve fitting work?
How to Answer
- 1
Keep a dedicated logbook for daily work.
- 2
Use digital tools for easy record-keeping and backups.
- 3
Document each valve fitting with photos and notes.
- 4
Ensure paperwork is organized by project or client.
- 5
Review documentation regularly for accuracy and completeness.
Example Answers
I maintain a dedicated logbook where I record daily tasks, including details on each valve fitted. I also use a digital spreadsheet to track work progress and ensure all records are backed up.
Don't Just Read Valve Fitter Questions - Practice Answering Them!
Reading helps, but actual practice is what gets you hired. Our AI feedback system helps you improve your Valve Fitter interview answers in real-time.
Personalized feedback
Unlimited practice
Used by hundreds of successful candidates
What safety protocols do you follow while working with hazardous materials related to valve fitting?
How to Answer
- 1
Identify specific safety gear you wear, like gloves and goggles.
- 2
Discuss proper handling techniques to avoid spills or leaks.
- 3
Mention regular training or certification related to hazardous materials.
- 4
Explain the importance of a Material Safety Data Sheet (MSDS).
- 5
Highlight procedures for reporting accidents or unsafe conditions.
Example Answers
I always wear protective gloves and goggles when handling hazardous materials. I ensure I follow proper techniques to minimize spills, and I regularly attend safety training sessions. Additionally, I refer to the MSDS for any chemicals I work with to understand their hazards.
Situational Interview Questions
Imagine you find a serious discrepancy in valve specification during installation. What would you do?
How to Answer
- 1
Identify the specific discrepancy clearly
- 2
Stop the installation process immediately
- 3
Consult the specifications and relevant documentation
- 4
Notify your supervisor and team members about the issue
- 5
Suggest a corrective action or alternative approach
Example Answers
If I find a serious discrepancy, I would first identify the exact nature of the issue. I would then halt the installation immediately and review the specifications. After confirming the discrepancy, I would inform my supervisor and discuss possible corrective actions.
If you were under a tight deadline but discovered a potential defect in the valve installation, how would you proceed?
How to Answer
- 1
Prioritize safety and quality over speed.
- 2
Immediately assess the severity of the defect.
- 3
Communicate clearly with the team and stakeholders.
- 4
Propose a solution and evaluate impact on the deadline.
- 5
Document the defect and your decision process.
Example Answers
I would first assess the defect to determine its impact on safety. If serious, I would halt progress and inform my team right away. My priority is ensuring we deliver a safe end product.
Don't Just Read Valve Fitter Questions - Practice Answering Them!
Reading helps, but actual practice is what gets you hired. Our AI feedback system helps you improve your Valve Fitter interview answers in real-time.
Personalized feedback
Unlimited practice
Used by hundreds of successful candidates
How would you approach a situation where a team member disagrees with your installation method for a valve?
How to Answer
- 1
Listen to the team member's concerns without interrupting.
- 2
Ask questions to understand their perspective and reasoning.
- 3
Explain your method clearly, highlighting the benefits and safety measures.
- 4
Be open to feedback and willing to adapt if there are valid points.
- 5
Aim for a collaborative solution, possibly agreeing to try both methods.
Example Answers
I would first listen to my team member's concerns to understand their viewpoint. Then, I would explain my method, focusing on its advantages. If their points are valid, I'm open to adjusting my approach or even trying a combination of both methods to ensure the best outcome.
You are working on a high-pressure valve system and notice a leak. What steps would you take immediately?
How to Answer
- 1
Identify the source of the leak and assess its severity.
- 2
Immediately notify your supervisor and other team members.
- 3
Shut down the system safely following established protocols.
- 4
Use appropriate personal protective equipment during the assessment.
- 5
Prepare to execute repairs and document the incident for review.
Example Answers
First, I would quickly identify the leak's source and determine how severe it is. Then, I'd notify my supervisor and team to ensure everyone's safety. Next, I'd proceed to shut down the system following our protocols, using my PPE. After that, I would prepare for repairs and make sure to document everything.
If you have multiple valve fittings to complete and time is running short, how do you prioritize your tasks?
How to Answer
- 1
Assess the urgency of each task based on deadlines and operational impact.
- 2
Identify tasks that are critical for safety and functionality.
- 3
Consider the complexity of each fitting and the time required.
- 4
Communicate with your team about prioritization and resource allocation.
- 5
Review any pending tasks and adjust priorities in real-time if necessary.
Example Answers
I start by looking at which valve fittings are most critical for safety and deadlines. I tackle those first, then move to the more complex tasks that can cause delays if not addressed.
What would you do if you realized after installation that you used the wrong valve for a particular application?
How to Answer
- 1
Acknowledge the mistake honestly without making excuses
- 2
Assess the potential impact of the wrong valve on the system
- 3
Communicate promptly with relevant stakeholders about the issue
- 4
Develop a corrective action plan to replace the valve
- 5
Document the error to prevent similar issues in the future
Example Answers
I would first acknowledge the mistake to the team and assess if there are any immediate safety risks. Then, I would communicate the issue to my supervisor and discuss how to replace the wrong valve safely and efficiently.
How would you handle a situation where another department challenges your valve fitting decisions?
How to Answer
- 1
Listen carefully to the concerns raised by the other department.
- 2
Stay calm and professional without becoming defensive.
- 3
Explain your rationale with clear technical reasoning.
- 4
Be open to feedback and willing to reassess your decision.
- 5
Collaborate on finding a solution that meets everyone's needs.
Example Answers
I would first listen to the other department's concerns and fully understand their perspective. Then, I would explain my valve fitting decisions based on technical specifications and industry standards. If necessary, I would be open to reviewing my approach to find a consensus that satisfies both teams.
If you are suddenly out of a specific type of valve you need for a project, what would be your next steps?
How to Answer
- 1
Assess the project timeline and urgency to determine the impact of the shortage.
- 2
Check with suppliers for immediate availability or alternative options.
- 3
Consider using substitute valves that can fit the specifications.
- 4
Communicate with the project team about the issue and potential delays.
- 5
Document the situation to avoid similar issues in the future.
Example Answers
First, I'd evaluate the urgency of the project to see how this shortage might affect our timeline. Then, I would contact suppliers to find out if they have the specific valve in stock or if we can source a similar one that meets the project's requirements.
How would you respond to a request from a customer reporting an issue with a valve you installed?
How to Answer
- 1
Listen carefully to the customer's concern and ask clarifying questions.
- 2
Acknowledge the issue and express willingness to resolve it.
- 3
Assess the information and determine if it requires an immediate site visit.
- 4
Communicate the next steps clearly to the customer.
- 5
Follow up after the issue is resolved to ensure customer satisfaction.
Example Answers
I would start by listening to the customer and asking them to describe the issue in detail. Then, I'd reassure them that I will help resolve it as quickly as possible. I would assess whether I need to visit the site to diagnose the problem or if it can be addressed over the phone.
If a client was unhappy with the valve work done, how would you address their concerns?
How to Answer
- 1
Listen actively to the client's concerns without interrupting.
- 2
Apologize for any inconvenience caused, showing empathy.
- 3
Ask specific questions to understand the exact issue or dissatisfaction.
- 4
Outline steps you can take to resolve the problem and reassure the client.
- 5
Follow up after resolving the issue to ensure client satisfaction.
Example Answers
I would first listen carefully to the client's concerns and apologize for any inconvenience. Then, I would ask specific questions to understand the issue, outline how I will fix it, and ensure they are happy with the resolution before following up later.
Don't Just Read Valve Fitter Questions - Practice Answering Them!
Reading helps, but actual practice is what gets you hired. Our AI feedback system helps you improve your Valve Fitter interview answers in real-time.
Personalized feedback
Unlimited practice
Used by hundreds of successful candidates
Valve Fitter Position Details
Recommended Job Boards
These job boards are ranked by relevance for this position.
Related Positions
- Valver
- Roof Fitter
- Ventilator
- Filler Spreader
- Furnace Worker
- Filter Changer
- Hole Filler
- Vulcanizer
- Kiln Setter
- Riser
Similar positions you might be interested in.
Ace Your Next Interview!
Practice with AI feedback & get hired faster
Personalized feedback
Used by hundreds of successful candidates
Ace Your Next Interview!
Practice with AI feedback & get hired faster
Personalized feedback
Used by hundreds of successful candidates