Top 33 Belt Fixer Interview Questions and Answers [Updated 2025]
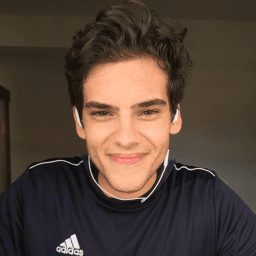
Andre Mendes
•
March 30, 2025
Preparing for a 'Belt Fixer' interview can be daunting, but we've got you covered. In this updated guide, you'll find a collection of the most common interview questions for this specialized role, complete with example answers and expert tips to help you respond with confidence. Dive in to enhance your interview skills and set yourself up for success in securing your next opportunity.
Download Belt Fixer Interview Questions in PDF
To make your preparation even more convenient, we've compiled all these top Belt Fixerinterview questions and answers into a handy PDF.
Click the button below to download the PDF and have easy access to these essential questions anytime, anywhere:
List of Belt Fixer Interview Questions
Situational Interview Questions
If you run out of a critical repair part, what would you do to complete the job?
How to Answer
- 1
Identify if there are alternative parts that can be used temporarily.
- 2
Communicate with your supervisor or team about the issue immediately.
- 3
Check inventory and see if the part can be sourced from a nearby location.
- 4
Consider whether a work-around solution can keep the system operational.
- 5
Document the issue for future reference and follow up on obtaining the required part.
Example Answers
If I run out of a critical repair part, I would first see if there's an alternative part available that could work in the meantime. I would inform my supervisor about the situation and check if we can source the part from a nearby facility. If possible, I would look for a temporary fix to keep the system running until we get the correct part.
How would you manage your stress levels during a particularly challenging belt repair task?
How to Answer
- 1
Stay organized by breaking the task into smaller steps
- 2
Practice deep breathing to maintain focus during difficult moments
- 3
Take short breaks to prevent burnout and regain clarity
- 4
Seek assistance from colleagues if the task becomes overwhelming
- 5
Maintain a positive mindset by reminding yourself of past successes
Example Answers
I manage stress during challenging tasks by breaking them into smaller, more manageable steps. If things get tough, I take a short break to clear my mind.
Don't Just Read Belt Fixer Questions - Practice Answering Them!
Reading helps, but actual practice is what gets you hired. Our AI feedback system helps you improve your Belt Fixer interview answers in real-time.
Personalized feedback
Unlimited practice
Used by hundreds of successful candidates
If a customer has unrealistic expectations about a belt repair turnaround time, how would you address this?
How to Answer
- 1
Listen carefully to the customer's expectations without interrupting.
- 2
Empathize with the customer and acknowledge their concerns.
- 3
Clearly explain the typical repair time and what factors influence it.
- 4
Provide a realistic timeframe based on current workload and urgency.
- 5
Offer alternatives or solutions if possible, such as express services.
Example Answers
I would first listen to the customer's timeline to understand their needs, then empathize by saying I understand how important it is to them. I would explain our usual repair time and why it might take longer, and I would offer to expedite if possible.
If you find a belt that continuously slips even after repairs, what steps would you take to address this?
How to Answer
- 1
Inspect the belt for signs of wear and damage.
- 2
Check the belt tension and alignment to ensure proper fit.
- 3
Examine pulleys and related components for defects or misalignment.
- 4
Consider the load and conditions affecting the belt performance.
- 5
Replace the belt if it is beyond repair or does not meet specifications.
Example Answers
I would first inspect the belt for visible wear or tears and check its tension. Next, I'd look at the pulleys to see if they are aligned correctly. If everything seems fine, I'd evaluate the working conditions that might be causing slippage.
Imagine you have multiple belt repairs to do in a limited time. How would you prioritize your tasks?
How to Answer
- 1
Assess the severity of each repair to identify urgent needs.
- 2
Consider the impact of each repair on overall operations.
- 3
Estimate the time each repair will take and prioritize accordingly.
- 4
Group similar repairs to maximize efficiency.
- 5
Communicate with team members to align on priorities if needed.
Example Answers
I would first identify which belts are most critical to operations. If any are necessary for ongoing work, I'd prioritize those to minimize downtime. Then I would assess how long each repair takes to organize the most efficient workflow.
If you notice a hazard while working on a belt repair, what actions would you take?
How to Answer
- 1
Always stop work immediately when a hazard is identified.
- 2
Secure the area to prevent others from entering the hazard zone.
- 3
Assess the risk and determine the best method to address the hazard.
- 4
Report the hazard to a supervisor or safety officer as soon as possible.
- 5
Take necessary actions to mitigate the hazard before resuming work.
Example Answers
If I notice a hazard while working on a belt repair, I would first stop all work to ensure safety. Then, I would secure the area to keep others away and assess the risk involved. After that, I would report the issue to my supervisor and work on mitigating the hazard, such as using proper tools or safety equipment, before resuming the repair.
If a belt repair will take longer than expected, how would you communicate this to your supervisor?
How to Answer
- 1
Assess the reasons for the delay and gather all relevant information.
- 2
Provide an estimated time for completion based on your assessment.
- 3
Communicate the delay as soon as possible to keep your supervisor informed.
- 4
Be honest about the issues causing the delay without making excuses.
- 5
Offer potential solutions or alternatives if applicable.
Example Answers
I would inform my supervisor immediately, explaining the specific reasons for the delay and providing a new estimated completion time. I would ensure they have all the relevant information so we can discuss any impact on the workflow.
You are tasked with fixing a belt with a unique design that you've never worked on before. How would you approach this situation?
How to Answer
- 1
Research the unique belt design to understand its components and mechanics
- 2
Identify any specific materials used and their properties
- 3
Check for user manuals or documentation related to the belt
- 4
Consult with colleagues or experts who may have experience with similar designs
- 5
Test small adjustments gradually to avoid further damage
Example Answers
I would start by researching the specific design of the belt online to learn about its components. Then, I would look for any available user manuals. If needed, I would consult a colleague who has experience with unusual designs before making any adjustments cautiously.
Imagine you are juggling multiple belt repairs at the same time. How would you manage your time effectively?
How to Answer
- 1
Prioritize the repairs based on urgency and complexity
- 2
Break down each repair task into smaller steps
- 3
Set specific time blocks for each belt repair
- 4
Use a timer to keep track of time for each task
- 5
Stay organized with notes on each belt's requirements
Example Answers
I would start by assessing which belt repairs are most urgent and prioritize those. Then, I would break down each repair into smaller tasks and set specific time blocks to work on each one. Using a timer helps me stay focused, and I keep detailed notes on what each repair requires.
If a client is unhappy with a previous belt repair, how would you handle the situation?
How to Answer
- 1
Listen to the client calmly and understand their concerns
- 2
Apologize for any inconvenience caused and show empathy
- 3
Ask specific questions to identify the issue with the repair
- 4
Offer a solution, such as a redo or a discount
- 5
Ensure follow-up to confirm the client's satisfaction after the resolution
Example Answers
I would first listen to the client's concerns carefully, apologize for the inconvenience, and ask what specific issues they are facing with the repair. Then, I would suggest fixing the belt at no extra cost and ensure they are satisfied with the result before leaving the shop.
Don't Just Read Belt Fixer Questions - Practice Answering Them!
Reading helps, but actual practice is what gets you hired. Our AI feedback system helps you improve your Belt Fixer interview answers in real-time.
Personalized feedback
Unlimited practice
Used by hundreds of successful candidates
If you had to improve the belt repair process, what changes would you propose?
How to Answer
- 1
Identify key pain points in the current process.
- 2
Suggest specific tools or technologies to enhance efficiency.
- 3
Propose a structured training program for staff.
- 4
Introduce a system for tracking and analyzing repair data.
- 5
Emphasize the importance of preventive maintenance.
Example Answers
I would start by mapping out the current belt repair steps to identify where delays occur. Incorporating a digital tracking tool can help monitor repairs and streamline communication. Additionally, I believe training staff on new techniques could improve repair quality and speed.
Behavioral Interview Questions
Can you give an example of constructive feedback you received on your belt repair work and how you applied it?
How to Answer
- 1
Choose a clear example of feedback you received.
- 2
Explain the specific issue the feedback addressed.
- 3
Describe the steps you took to implement the feedback.
- 4
Highlight any improvements or positive outcomes resulting from your changes.
- 5
Keep it concise and relevant to belt repair.
Example Answers
I once received feedback that my stitching was too loose on belt repairs, which could lead to the belts not holding up well over time. I took this advice to heart and researched proper tension techniques for stitching. After applying tighter stitches, I noticed that the durability of my repairs improved significantly, and customers appreciated the quality.
Describe a situation where you took initiative in improving the belt repair process.
How to Answer
- 1
Think of a specific project where you identified a problem in the belt repair process.
- 2
Explain the steps you took to assess the situation and develop a solution.
- 3
Highlight your collaborative efforts, especially if you worked with a team.
- 4
Mention the positive outcome and improvements made to the process.
- 5
Keep your answer structured: situation, action, result.
Example Answers
While working at Company XYZ, I noticed that our belt repair time was significantly delayed due to outdated equipment. I proposed an upgrade to a more efficient machine, conducted cost analysis, and presented it to management. After approval, we reduced repair time by 30%.
Don't Just Read Belt Fixer Questions - Practice Answering Them!
Reading helps, but actual practice is what gets you hired. Our AI feedback system helps you improve your Belt Fixer interview answers in real-time.
Personalized feedback
Unlimited practice
Used by hundreds of successful candidates
Can you describe a time when you successfully repaired a broken belt under a tight deadline?
How to Answer
- 1
Start with a clear context of the situation.
- 2
Explain the specific challenge of the tight deadline.
- 3
Describe the steps you took in the repair process.
- 4
Highlight any tools or techniques used that were effective.
- 5
Finish with the outcome and what you learned from the experience.
Example Answers
In my previous job, a conveyor belt broke just before a shipment was due. The deadline was two hours away. I quickly assessed the damage and used a splicing kit to repair the belt. I worked efficiently and communicated with my team to prioritize the repair. We finished the repair with 15 minutes to spare, and the shipment went out on time. I learned the importance of staying calm under pressure.
Tell me about a situation where you had to collaborate with others to fix a belt issue.
How to Answer
- 1
Start with a clear description of the belt issue encountered.
- 2
Explain the team dynamics and roles of each member involved.
- 3
Discuss the collaborative steps taken to identify the root cause of the problem.
- 4
Highlight your specific contributions and how they helped resolve the issue.
- 5
Conclude with the positive outcome and what you learned from the experience.
Example Answers
In my previous role, we faced a recurring issue with a conveyor belt malfunction. I coordinated with the maintenance team and operators to understand the problem. Together, we found that the tension was improperly set. I suggested conducting regular tension checks, which led to a 30% decrease in downtime. This collaboration improved our workflow significantly.
Describe a change in protocol or procedure that you had to adapt to while fixing belts.
How to Answer
- 1
Identify a specific change you faced while working with belts.
- 2
Explain how you learned about the new protocol or procedure.
- 3
Describe the challenges you encountered adapting to the change.
- 4
Discuss the outcome and what you learned from the experience.
- 5
Keep your answer focused and relevant to belt fixing.
Example Answers
In my previous job, we switched to a new belt material that required different handling. I learned about it through training sessions. Initially, I struggled with adjusting the tension during installation, but after a few tries, I adapted and found that the new material held up better. This taught me the importance of being flexible with new methods.
Give an example of how your attention to detail helped you identify a problem during a belt repair.
How to Answer
- 1
Think of a specific repair incident that required careful observation.
- 2
Describe the process you used to identify the problem, focusing on detail.
- 3
Include the outcome of fixing the problem due to your attention to detail.
- 4
Keep it concise, use clear language, and highlight your skills.
- 5
Make sure the example reflects common issues faced in belt repair.
Example Answers
During a routine belt repair, I noticed uneven wear on the belt surface. By closely examining the alignment and tension, I discovered that a roller was misaligned. Correcting this not only fixed the current issue but also prevented future damage.
Have you ever disagreed with a supervisor about the best way to fix a belt? How did you resolve it?
How to Answer
- 1
Describe the situation clearly and briefly.
- 2
Explain your perspective and why you disagreed.
- 3
Highlight your communication approach with the supervisor.
- 4
Emphasize collaboration in finding a solution.
- 5
Conclude with the outcome and what you learned.
Example Answers
In a recent situation, I disagreed with my supervisor on using a temporary patch for a worn-out belt. I explained that a new belt would ensure long-term reliability. We discussed both options, and eventually, we agreed to replace the belt, which improved performance significantly.
Describe a time when you went above and beyond to fix a belt issue.
How to Answer
- 1
Identify a specific incident related to a belt issue.
- 2
Highlight the steps you took to investigate the problem.
- 3
Explain the extra effort you made beyond normal responsibilities.
- 4
Emphasize the positive outcome of your actions.
- 5
Mention any feedback you received from your team or supervisor.
Example Answers
At my previous job, a crucial conveyor belt in the packaging line broke down unexpectedly. I took the initiative to stay after hours to troubleshoot the issue. I called our suppliers for a quick part delivery and personally installed the new belt. This not only minimized downtime but also impressed my supervisor who praised my dedication.
Have you ever led a team in a belt repair project? What was the outcome?
How to Answer
- 1
Start with the context of the project and your role as a leader.
- 2
Describe specific challenges the team faced during the repair process.
- 3
Highlight your leadership actions, such as delegating tasks or improving team coordination.
- 4
Share the outcome, focusing on results or improvements after the project.
- 5
Reflect on what you learned from the experience and how it can apply to future projects.
Example Answers
In my previous job, I led a team of five in a belt repair project where we had to fix a major conveyor system. We faced delays due to broken tools and miscommunication. I arranged daily check-in meetings to clarify roles and streamline our efforts. As a result, we completed the project on time, and the system's efficiency improved by 20%. I learned the importance of clear communication.
Don't Just Read Belt Fixer Questions - Practice Answering Them!
Reading helps, but actual practice is what gets you hired. Our AI feedback system helps you improve your Belt Fixer interview answers in real-time.
Personalized feedback
Unlimited practice
Used by hundreds of successful candidates
Technical Interview Questions
What regulations do you need to be aware of when repairing industrial belts?
How to Answer
- 1
Familiarize yourself with OSHA regulations for workplace safety.
- 2
Understand any local environmental regulations regarding material disposal.
- 3
Know industry-specific standards, like ANSI or ISO, that apply to belt repairs.
- 4
Stay updated on any manufacturer guidelines pertaining to their belts and equipment.
- 5
Be aware of any electrical safety standards if the belts integrate with motors or electrical systems.
Example Answers
I need to be aware of OSHA regulations to ensure worker safety during repairs, as well as any environmental laws for proper disposal of materials. Additionally, I follow ANSI standards that might apply to the specific industrial belts I work with.
What methods do you use to test a belt after completing repairs to ensure it's safe to operate?
How to Answer
- 1
Inspect the belt visually for any signs of damage or misalignment
- 2
Conduct a tension test to ensure the belt has the correct tension
- 3
Run the belt at low speed to check for smooth operation and any unusual noises
- 4
Check alignment with the pulleys and ensure they are properly seated
- 5
Perform a load test to verify the belt can handle operational conditions without slipping
Example Answers
After repairing the belt, I visually inspect it for any misalignments or defects. I then perform a tension test to confirm it's at the right tightness. If everything looks good, I run the belt at low speed to check for smooth operation and listen for any unusual noises.
Don't Just Read Belt Fixer Questions - Practice Answering Them!
Reading helps, but actual practice is what gets you hired. Our AI feedback system helps you improve your Belt Fixer interview answers in real-time.
Personalized feedback
Unlimited practice
Used by hundreds of successful candidates
What are the most common methods you use to repair different types of conveyor belts?
How to Answer
- 1
Identify the type of conveyor belt you are discussing.
- 2
List specific repair methods for each type, such as vulcanization for rubber belts.
- 3
Mention the importance of the material and environment in repair choice.
- 4
Include safety considerations during repair processes.
- 5
Share any personal experience that illustrates your familiarity with these methods.
Example Answers
For rubber conveyor belts, I often use vulcanization, which involves heating the rubber to bond the material. For fabric belts, I typically use mechanical fasteners or sewing techniques. Safety is key, so I always ensure the belt is properly shut off and locked out before starting any repair work.
Which tools do you consider essential for a belt fixing job and why?
How to Answer
- 1
Identify specific tools like belt tensioners and cutting tools.
- 2
Explain the purpose and function of each tool.
- 3
Mention how these tools improve efficiency and quality.
- 4
Consider safety tools and their importance in the job.
- 5
Be concise but cover a variety of tools used in belt fixing.
Example Answers
Essential tools for belt fixing include a tensioner for adjusting belt tightness, cutting tools for customizing belt lengths, and measuring tapes for accurate dimensions. These tools ensure the belt runs smoothly and lasts longer.
What types of materials do you usually work with when repairing belts, and how do they differ?
How to Answer
- 1
Identify specific materials you have experience with such as leather, canvas, or synthetic.
- 2
Explain the unique properties of each material, like durability or flexibility.
- 3
Discuss how material choice affects the repair methods you use.
- 4
Mention any tools or techniques that are specific to certain materials.
- 5
Share a brief example of a past repair involving those materials.
Example Answers
I typically work with leather, canvas, and synthetic materials. Leather is durable but can be hard to repair, while canvas is easier to work with due to its flexibility. Synthetic materials often require special adhesives. For example, I once repaired a leather belt that needed stitching and reinforcement due to wear.
Can you explain the safety standards you follow when working on belt repairs?
How to Answer
- 1
Identify key safety regulations relevant to belt repairs
- 2
Explain the use of personal protective equipment (PPE)
- 3
Mention the importance of lockout/tagout procedures
- 4
Discuss regular safety training and updates
- 5
Highlight the role of proper tools and equipment in safety
Example Answers
I always adhere to OSHA regulations, ensuring I wear appropriate PPE like gloves and goggles. I implement lockout/tagout procedures to safely work on belts without risking accidental machine start-up.
How do you diagnose issues in a conveyor belt system?
How to Answer
- 1
Start by visually inspecting the entire system for obvious signs of wear or damage.
- 2
Check for abnormal noises that could indicate problems with the motor or rollers.
- 3
Monitor the belt alignment and tension to ensure proper operation.
- 4
Use diagnostic tools like infrared cameras or vibration analyzers if necessary.
- 5
Document any issues and the steps taken to investigate them for future reference.
Example Answers
I begin with a visual inspection to look for visible damage or wear on the belt and components. Next, I listen for abnormal sounds during operation, indicating potential motor or roller issues. I also verify the belt's alignment and tension since misalignment can cause a range of problems.
What quality assurance processes do you put in place when fixing belts?
How to Answer
- 1
Start by mentioning initial inspections of the belt to identify damages.
- 2
Emphasize the importance of using standardized repair protocols.
- 3
Discuss testing the belt after repairs to ensure functionality.
- 4
Highlight documentation of repairs for future reference.
- 5
Mention the role of regular maintenance checks post-repair.
Example Answers
I begin with an initial inspection to check for any significant damage. Then, I follow standardized protocols for the repair process. After fixing, I test the belt to ensure it operates correctly before returning it. I also document all repairs for tracking.
What preventive maintenance practices do you recommend to avoid future belt failures?
How to Answer
- 1
Perform regular inspections to check for wear and tear on belts.
- 2
Ensure proper tensioning of the belts according to manufacturer specifications.
- 3
Lubricate pulleys and bearings to reduce friction and wear.
- 4
Monitor operating temperatures to prevent overheating.
- 5
Replace belts at recommended intervals even if they appear fine.
Example Answers
I recommend conducting regular inspections to identify any signs of wear. It's crucial to ensure that belts are properly tensioned, as this can prevent slippage and excessive strain.
What types of machinery are belts typically attached to, and how does this affect repair techniques?
How to Answer
- 1
Identify common machines using belts like conveyors, engines, and industrial equipment.
- 2
Mention how belt type affects repair, such as flat belts versus V-belts.
- 3
Discuss the relevance of machine size and function to the repair process.
- 4
Provide examples of tools needed for different belt repairs.
- 5
Emphasize the importance of understanding belt tension and alignment during repair.
Example Answers
Belts are commonly found on machines like conveyor systems, automotive engines, and various industrial equipment. The type of belt, such as flat belts or V-belts, dictates the repair approach, including the need for tension adjustments and alignment checks. For instance, when repairing a V-belt on an engine, you would need specific tools like a tension gauge.
Don't Just Read Belt Fixer Questions - Practice Answering Them!
Reading helps, but actual practice is what gets you hired. Our AI feedback system helps you improve your Belt Fixer interview answers in real-time.
Personalized feedback
Unlimited practice
Used by hundreds of successful candidates
How do environmental factors like temperature and humidity affect belt materials and repairs?
How to Answer
- 1
Discuss how heat can cause materials to expand, affecting tension.
- 2
Mention that high humidity can promote corrosion of metal parts.
- 3
Explain that cold temperatures can make materials brittle and prone to cracking.
- 4
Emphasize the importance of adjusting repair methods based on weather conditions.
- 5
Consider specific examples of belt materials and their reactions to environmental changes.
Example Answers
Temperature affects belt materials by causing expansion in warm conditions, which can impact the tension. High humidity can lead to rust in metal belts, while cold temperatures could make rubber belts brittle. It's crucial to consider these factors when planning repairs.
What steps do you take when troubleshooting a belt that has started to malfunction?
How to Answer
- 1
Identify the type of malfunction, such as slippage or tearing.
- 2
Check belt tension and alignment to ensure proper function.
- 3
Inspect for physical damage or wear on both the belt and pulleys.
- 4
Clean the belt and pulleys to remove any debris or build-up.
- 5
Test after making adjustments to confirm the issue is resolved.
Example Answers
First, I investigate the type of malfunction, whether it's slippage or tearing. Then, I check the belt tension and alignment, followed by a physical inspection for wear. If necessary, I clean the belt and pulleys and conduct a test run to ensure everything works well.
Belt Fixer Position Details
Related Positions
- Belt Changer
- Belt Dresser
- Belt Lacer
- Maintenance Man
- Maintenance Repairer
- Lubricator
- Maintenance Machinist
- Size Changer
- Grease Packer
- Belt Maker
Similar positions you might be interested in.
Ace Your Next Interview!
Practice with AI feedback & get hired faster
Personalized feedback
Used by hundreds of successful candidates
Ace Your Next Interview!
Practice with AI feedback & get hired faster
Personalized feedback
Used by hundreds of successful candidates