Top 30 Fabrication Supervisor Interview Questions and Answers [Updated 2025]
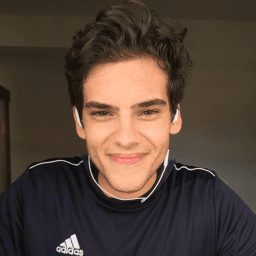
Andre Mendes
•
March 30, 2025
Preparing for a Fabrication Supervisor interview can be daunting, but we're here to help. In this post, you'll find a curated list of the most common interview questions for this critical role, complete with example answers and practical tips for responding effectively. Whether you’re a seasoned professional or new to the field, this guide is designed to boost your confidence and help you navigate the interview process successfully.
Download Fabrication Supervisor Interview Questions in PDF
To make your preparation even more convenient, we've compiled all these top Fabrication Supervisorinterview questions and answers into a handy PDF.
Click the button below to download the PDF and have easy access to these essential questions anytime, anywhere:
List of Fabrication Supervisor Interview Questions
Behavioral Interview Questions
Can you describe a time when you had to lead a team through a significant change in the fabrication process?
How to Answer
- 1
Identify a specific change that occurred in the fabrication process.
- 2
Explain your role in leading the team through this change.
- 3
Highlight the challenges faced and how you overcame them.
- 4
Discuss the outcome of the change and its impact on the team and projects.
- 5
Mention any feedback received from your team or management after the change.
Example Answers
In my previous role, we adopted a new CNC machine that required a different programming approach. I organized training sessions to ensure everyone was comfortable with the new software. Initially, there was resistance due to the learning curve, but after a few weeks, productivity increased by 20% and the team felt confident with the new process.
Tell me about a challenging fabrication project you managed and how you overcame difficulties.
How to Answer
- 1
Choose a specific project that had significant challenges.
- 2
Outline the main difficulties faced during the project.
- 3
Explain the steps you took to overcome these challenges.
- 4
Highlight the outcomes and what you learned from the experience.
- 5
Keep it focused on your role and contributions.
Example Answers
On a recent project to fabricate a large metal structure, we faced unexpected delays due to material shortages. I coordinated with suppliers to expedite deliveries and reallocated resources to keep our timeline on track. As a result, we completed the project on time and maintained quality standards.
Don't Just Read Fabrication Supervisor Questions - Practice Answering Them!
Reading helps, but actual practice is what gets you hired. Our AI feedback system helps you improve your Fabrication Supervisor interview answers in real-time.
Personalized feedback
Unlimited practice
Used by hundreds of successful candidates
Describe an instance where you resolved a conflict between team members on the fabrication floor.
How to Answer
- 1
Identify the specific conflict and the parties involved
- 2
State your role in facilitating the resolution
- 3
Explain the steps you took to mediate the situation
- 4
Highlight the outcome and how it improved team dynamics
- 5
Emphasize the importance of clear communication in conflict resolution
Example Answers
In a recent project, two welders had a disagreement about the measurements on a part. I organized a meeting where each could present their views, encouraged them to listen to each other, and guided them to a compromise by reviewing the specifications together. As a result, they reached an agreement that satisfied both and improved their collaboration.
Tell me about a time when you had to communicate complex fabrication concepts to non-technical personnel.
How to Answer
- 1
Identify the audience's level of understanding and tailor your explanation accordingly.
- 2
Use analogies or relatable examples that simplify the concepts.
- 3
Break down the information into smaller, digestible parts.
- 4
Encourage questions to ensure clarity and understanding.
- 5
Summarize key points at the end to reinforce understanding.
Example Answers
In my previous job, I had to explain a new CNC machine operation to the assembly team. I related the machine's movements to how a person operates a drawing tool, making it easier for them to visualize. I broke down each step and encouraged them to ask questions, ensuring they fully understood before proceeding.
How have you handled underperforming team members in your fabrication team?
How to Answer
- 1
Identify the specific performance issues with clear examples.
- 2
Communicate directly with the team member to understand their challenges.
- 3
Set measurable improvement goals and provide necessary resources or training.
- 4
Monitor progress and provide regular feedback to motivate improvement.
- 5
If issues persist, follow company protocols for performance management formally.
Example Answers
I noticed one of my fabricators was consistently missing deadlines. I met with him to discuss his challenges and discovered he needed more training on a specific machine. I arranged for a refresher training session, set a goal for him to improve his output by 20%, and provided weekly feedback until he met the objectives.
Describe a situation where you implemented a training program for your team. What was the result?
How to Answer
- 1
Choose a specific training program you developed or led
- 2
Explain the goals and reasons for the training
- 3
Describe the implementation process and who was involved
- 4
Highlight measurable results or improvements after the training
- 5
Reflect on lessons learned or adjustments made post-training
Example Answers
In my previous role, I identified a gap in our team's welding skills, which affected production. I developed a comprehensive training program focusing on TIG welding techniques, set clear objectives, and involved senior welders as mentors. After the program, we observed a 20% increase in weld quality ratings and a reduction in rework.
Give an example of how you set goals for your fabrication team and what steps you took to achieve them.
How to Answer
- 1
Identify a specific goal relevant to fabrication, such as increasing efficiency or reducing waste.
- 2
Explain how you communicated the goal to your team and ensured everyone understood their role.
- 3
Describe the metrics you used to track progress toward the goal.
- 4
Mention any obstacles your team faced and how you helped overcome them.
- 5
Conclude with the outcome and what you learned from the experience.
Example Answers
Last year, I set a goal to reduce waste in our fabrication process by 20%. I communicated this through team meetings and provided training on best practices. We tracked our waste metrics weekly and made adjustments as needed. When we faced a machine breakdown, I organized extra shifts to catch up. Ultimately, we achieved a 25% reduction in waste, which saved us costs and improved efficiency.
Describe a time when you had to quickly adapt your work processes in response to unexpected changes?
How to Answer
- 1
Identify a specific unexpected change you faced.
- 2
Explain the immediate impact on your work processes.
- 3
Describe the steps you took to adapt to the change.
- 4
Highlight the outcome of your adaptation.
- 5
Conclude with what you learned from the experience.
Example Answers
In my previous role, we experienced a sudden supply chain disruption when a key supplier went out of business. I quickly assessed our inventory levels and identified alternative suppliers. I coordinated with the purchasing team to expedite orders from the new suppliers, which allowed us to continue production without major delays. As a result, we met our delivery deadlines and maintained customer satisfaction. I learned the importance of having backup suppliers in place.
Give an example of how you used emotional intelligence to lead your team through a crisis.
How to Answer
- 1
Identify a specific crisis situation where your team faced challenges.
- 2
Explain how you recognized team members' emotions and concerns.
- 3
Describe the actions you took to address these emotions and provide support.
- 4
Highlight the outcome of your leadership during the crisis.
- 5
Reflect on what you learned and how it improved team dynamics.
Example Answers
When our production line faced a major equipment failure, I noticed my team was anxious and stressed. I held a quick meeting to listen to their concerns, reassuring them that we would work together to find a solution. We developed a clear plan and divided tasks among team members based on their strengths, which helped regain their confidence. Ultimately, we fixed the issue and met our deadline, strengthening our teamwork.
Don't Just Read Fabrication Supervisor Questions - Practice Answering Them!
Reading helps, but actual practice is what gets you hired. Our AI feedback system helps you improve your Fabrication Supervisor interview answers in real-time.
Personalized feedback
Unlimited practice
Used by hundreds of successful candidates
Technical Interview Questions
How do you prioritize tasks in a fabrication project with changing deadlines?
How to Answer
- 1
Assess the urgency and impact of each task on the project timeline.
- 2
Communicate with team members to understand their workloads and dependencies.
- 3
Use a project management tool to track deadlines and progress.
- 4
Be flexible and ready to adjust priorities as new information comes in.
- 5
Document changes in priority to keep the team aligned.
Example Answers
I prioritize tasks by first assessing which of them are critical to project milestones. I then communicate with my team to understand their workloads, adjusting priorities dynamically based on deadlines and dependencies.
What types of materials do you have experience working with in fabrication, and how do different materials affect fabrication processes?
How to Answer
- 1
Identify key materials used in fabrication like metals, plastics, and composites.
- 2
Explain how material properties like strength, flexibility, and heat resistance affect production methods.
- 3
Mention specific fabrication techniques used for each material type.
- 4
Consider including any relevant industry standards or practices.
- 5
Relate your experience with real examples to demonstrate your expertise.
Example Answers
I have extensive experience working with various metals, including steel and aluminum. Steel's high strength allows for heavy-duty applications, while aluminum's lightweight properties make it ideal for components requiring reduced weight. I commonly use welding for steel and laser cutting for aluminum to achieve precision.
Don't Just Read Fabrication Supervisor Questions - Practice Answering Them!
Reading helps, but actual practice is what gets you hired. Our AI feedback system helps you improve your Fabrication Supervisor interview answers in real-time.
Personalized feedback
Unlimited practice
Used by hundreds of successful candidates
Can you explain the types of fabrication equipment you are proficient with, and any maintenance practices you follow?
How to Answer
- 1
Identify key fabrication equipment you have worked with, such as laser cutters, CNC machines, or welding equipment.
- 2
Mention specific techniques or applications you have experience with for each type of equipment.
- 3
Discuss routine maintenance practices you adhere to, highlighting safety and operational efficiency.
- 4
Provide examples that demonstrate how your experience leads to improved outcomes in production.
- 5
Be concise and focus on your hands-on experience and understanding of equipment care.
Example Answers
I am proficient with CNC machines and have operated laser cutters extensively. For CNC, I regularly check and calibrate tools to ensure precision, and for laser cutters, I clean the optics daily to maintain cut quality.
What steps do you take to ensure quality control in fabrication processes?
How to Answer
- 1
Establish clear quality standards for materials and processes
- 2
Implement regular inspections at various stages of fabrication
- 3
Train team members on quality control practices and importance
- 4
Use statistical process control to monitor fabrication consistency
- 5
Document all findings and improvements for audit trails and learning
Example Answers
I focus on quality by establishing clear standards for each material and technique we use. We conduct inspections at key points during the fabrication process to catch any issues early.
How do you approach optimizing fabrication processes for efficiency and cost-effectiveness?
How to Answer
- 1
Assess current processes to identify bottlenecks
- 2
Implement lean manufacturing principles to reduce waste
- 3
Utilize data analytics to monitor performance metrics
- 4
Encourage team input for process improvements
- 5
Invest in training for employees to enhance skills
Example Answers
I start by mapping out the existing fabrication processes to pinpoint any bottlenecks. Then, I apply lean principles to streamline workflows and eliminate waste, resulting in reduced costs and better efficiency.
What are the key regulatory compliance issues in fabrication that a supervisor must be aware of?
How to Answer
- 1
Understand local, state, and federal regulations related to fabrication processes
- 2
Be familiar with safety standards such as OSHA regulations
- 3
Ensure compliance with environmental regulations regarding waste disposal
- 4
Know the standards for material handling and storage
- 5
Stay updated on industry-specific compliance requirements
Example Answers
A Fabrication Supervisor must be aware of OSHA regulations to ensure worker safety, as well as local environmental laws concerning waste disposal. This helps in maintaining a safe and compliant work environment.
What are the different fabrication methods you are familiar with and in what scenarios do you apply them?
How to Answer
- 1
List common fabrication methods such as welding, machining, and 3D printing.
- 2
Provide specific examples of when you would use each method.
- 3
Mention the advantages and limitations of each method.
- 4
Relate your answer to the industry or projects you have worked on.
- 5
Be prepared to discuss safety and quality control measures.
Example Answers
I am familiar with welding, machining, and 3D printing. I use welding for strong joints in structural components, machining for precision parts, and 3D printing for prototyping because of its speed and flexibility.
How do you interpret engineering drawings and specifications to ensure accurate fabrication?
How to Answer
- 1
Break down the drawing into sections and identify key components
- 2
Cross-reference specifications with drawings for consistency
- 3
Check for any notes or revisions that might affect fabrication
- 4
Use 3D modeling tools if available to visualize the end product
- 5
Communicate with engineers to clarify any uncertainties
Example Answers
I start by breaking down the engineering drawing into manageable sections and identifying critical components. Then I cross-check these with the specifications to ensure everything aligns. I always look for notes or revisions that may impact the fabrication process.
How do you conduct a cost analysis for a fabrication project before undertaking it?
How to Answer
- 1
Identify all materials required for the project and their costs.
- 2
Estimate labor costs based on the project's scope and duration.
- 3
Include overhead costs such as utilities and equipment usage.
- 4
Consider external factors like market conditions affecting material prices.
- 5
Document all assumptions and calculations for transparency.
Example Answers
I start by listing all materials needed for fabrication and researching current prices. Then, I estimate the labor costs using our team's hourly rates multiplied by the projected hours. I also add overhead costs such as electricity and machine maintenance. Finally, I keep detailed notes on my calculations and any market factors that could affect costs.
Can you walk us through your troubleshooting process when a fabrication machine fails?
How to Answer
- 1
Start by identifying the specific issue or symptoms of the failure.
- 2
Check the machine's manual for troubleshooting steps.
- 3
Inspect all relevant components for visible wear or damage.
- 4
Run diagnostic tests if available or initiate a simple restart if appropriate.
- 5
Document findings and share with the team for future reference.
Example Answers
First, I identify the issue by observing the machine and checking for error codes. Then, I consult the manual for specific troubleshooting steps related to those codes. I also inspect any related components for wear or damage, and if diagnostics are available, I run them to pinpoint the issue. Lastly, I document everything to help improve future responses.
Don't Just Read Fabrication Supervisor Questions - Practice Answering Them!
Reading helps, but actual practice is what gets you hired. Our AI feedback system helps you improve your Fabrication Supervisor interview answers in real-time.
Personalized feedback
Unlimited practice
Used by hundreds of successful candidates
Situational Interview Questions
If you receive a sudden order requiring immediate fabrication, how would you rearrange your team's priorities?
How to Answer
- 1
Assess the urgency and scale of the new order immediately
- 2
Communicate with the team to inform and gather input on current tasks
- 3
Reprioritize tasks by evaluating deadlines and resource availability
- 4
Allocate resources efficiently, possibly pulling from less urgent projects
- 5
Follow up and adjust as needed based on team feedback and progress
Example Answers
First, I would assess the urgency of the new order and its impact on our current commitments. Then, I would gather the team for a quick meeting to discuss reallocating resources and tasks based on our availability. We might push back some less critical projects to ensure we meet this new demand effectively.
Imagine you find a safety violation in your fabrication area. What steps would you take immediately?
How to Answer
- 1
Assess the situation to understand the nature of the violation
- 2
Immediately address the violation if it poses an imminent danger
- 3
Notify your supervisor or safety officer about the issue
- 4
Document the violation and the actions taken
- 5
Implement corrective measures to prevent future occurrences
Example Answers
First, I would assess the situation to determine the severity of the safety violation. If it's a serious hazard, I would correct it right away to ensure safety. Then, I would inform my supervisor, document what happened, and start working on solutions to prevent it from happening again.
Don't Just Read Fabrication Supervisor Questions - Practice Answering Them!
Reading helps, but actual practice is what gets you hired. Our AI feedback system helps you improve your Fabrication Supervisor interview answers in real-time.
Personalized feedback
Unlimited practice
Used by hundreds of successful candidates
If your team appears demotivated after a failed project, how would you address their concerns?
How to Answer
- 1
Hold a team meeting to openly discuss feelings and thoughts.
- 2
Encourage team members to share their perspectives without judgment.
- 3
Identify lessons learned from the project and highlight growth opportunities.
- 4
Set new, achievable goals to reinvigorate motivation.
- 5
Offer support and resources to help the team move forward.
Example Answers
I would start by organizing a team meeting where everyone can express their feelings about the project. This encourages open communication. I'd facilitate a discussion on what we can learn from the failure, helping the team see it as a growth opportunity.
How would you handle a situation where your project budget is significantly cut?
How to Answer
- 1
Assess the impact of the budget cut on project scope and timelines
- 2
Identify essential tasks and prioritize them based on project goals
- 3
Communicate openly with stakeholders about the changes and their implications
- 4
Explore cost-saving measures or alternative solutions to minimize impact
- 5
Consider reallocating resources or negotiating for additional funding if needed
Example Answers
In the event of a budget cut, I would first analyze which aspects of the project are affected the most. I would then identify the critical tasks that align with our main objectives and focus our efforts there. Open communication with my team and stakeholders would be key to ensure we are all aligned on the changes and understand their impact.
During fabrication, you discover that a critical part is defective. What action do you take to resolve the issue?
How to Answer
- 1
Assess the extent of the defect and its impact on the project.
- 2
Communicate the issue immediately to all relevant team members.
- 3
Determine if the part can be repaired or if it needs to be replaced.
- 4
Implement corrective actions and document the process.
- 5
Ensure quality checks are reinforced to prevent future defects.
Example Answers
First, I would assess the defect's impact on the project and gather my team to discuss it. If the part is repairable, I'd coordinate the repairs; if not, I would order a replacement and adjust the project timeline accordingly. I would also document the defect and the steps taken to resolve it to aid in future inspections.
How would you implement new fabrication technology in your team while minimizing disruption?
How to Answer
- 1
Assess the current skills of your team before implementation
- 2
Introduce technology gradually, starting with pilot projects
- 3
Provide thorough training sessions for all team members
- 4
Establish a feedback loop to address concerns and suggestions
- 5
Communicate openly about the benefits of the new technology
Example Answers
I would start by evaluating the team's current skill levels and identify any training needs. Next, I'd implement the new technology through a pilot project to minimize disruption. Training sessions would be organized to ensure everyone is up to speed, and I'd encourage team feedback throughout the process to make adjustments as needed.
If two projects need the same resources at the same time, how do you decide which one gets priority?
How to Answer
- 1
Evaluate project deadlines and urgency
- 2
Consider the impact on revenue and stakeholders
- 3
Review resource availability and constraints
- 4
Communicate with project leads to understand priorities
- 5
Make a decision based on strategic alignment and long-term goals
Example Answers
I assess the urgency of each project's deadline and determine which one has the most immediate impact. If one project could generate revenue sooner, I prioritize that one.
If your team is working at maximum capacity and a new order comes in, how would you manage this?
How to Answer
- 1
Assess current workload and priorities clearly
- 2
Communicate with the team about the new order
- 3
Explore options to redistribute tasks or extend shifts
- 4
Discuss with management for possible support or outsourcing
- 5
Maintain customer relations by providing realistic timelines
Example Answers
First, I would evaluate our current projects and see if any tasks can be prioritized or streamlined. Then, I would discuss with the team to see if we can work overtime or adjust schedules. If necessary, I'd inform management about our capacity and seek guidance on how to proceed. Finally, I would communicate with the customer, ensuring they understand when we can fulfill their order.
How would you handle a situation where a client is unhappy with the fabricated product?
How to Answer
- 1
Listen carefully to the client's concerns without interruption.
- 2
Acknowledge their feelings and validate their frustration.
- 3
Assess the situation by asking clarifying questions.
- 4
Propose a solution or corrective action that addresses their issue.
- 5
Follow up after resolution to ensure satisfaction.
Example Answers
I would first listen to the client's concerns and let them express their frustrations. I would then acknowledge their dissatisfaction and assure them that I take their issue seriously. Next, I would ask specific questions to understand the problem fully and offer a clear plan to rectify the issue, whether it be a repair, replacement, or adjustment.
If you need to collaborate with a different department to meet a fabrication deadline, how would you approach it?
How to Answer
- 1
Identify the specific department needed for collaboration
- 2
Schedule a meeting to discuss the deadline and requirements
- 3
Clearly communicate your goals and the impact of the deadline
- 4
Be open to their suggestions and constraints
- 5
Follow up with a summary to ensure alignment and accountability
Example Answers
I would first identify the relevant department and reach out to schedule a meeting. During the meeting, I would explain our fabrication deadline and discuss how we can collaborate effectively. I would ensure to listen to their concerns and work together to find a solution that meets both of our needs.
Don't Just Read Fabrication Supervisor Questions - Practice Answering Them!
Reading helps, but actual practice is what gets you hired. Our AI feedback system helps you improve your Fabrication Supervisor interview answers in real-time.
Personalized feedback
Unlimited practice
Used by hundreds of successful candidates
Fabrication Supervisor Position Details
Recommended Job Boards
CareerBuilder
www.careerbuilder.com/jobs/fabrication-supervisorZipRecruiter
www.ziprecruiter.com/Jobs/Fabrication-SupervisorThese job boards are ranked by relevance for this position.
Related Positions
Ace Your Next Interview!
Practice with AI feedback & get hired faster
Personalized feedback
Used by hundreds of successful candidates
Ace Your Next Interview!
Practice with AI feedback & get hired faster
Personalized feedback
Used by hundreds of successful candidates