Top 31 Packaging Supervisor Interview Questions and Answers [Updated 2025]
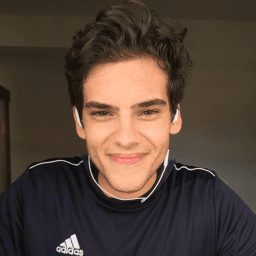
Andre Mendes
•
March 30, 2025
Preparing for a Packaging Supervisor interview can be daunting, but mastering the right questions is crucial to landing the role. In this blog post, we've gathered the most common interview questions for Packaging Supervisors, complete with example answers and insightful tips on how to respond effectively. Dive in to enhance your interview skills and boost your confidence for the big day!
Download Packaging Supervisor Interview Questions in PDF
To make your preparation even more convenient, we've compiled all these top Packaging Supervisorinterview questions and answers into a handy PDF.
Click the button below to download the PDF and have easy access to these essential questions anytime, anywhere:
List of Packaging Supervisor Interview Questions
Situational Interview Questions
If you discovered a significant quality issue late in the packaging process, what steps would you take?
How to Answer
- 1
Immediately halt the packaging process to prevent further issues.
- 2
Assess the impact of the quality issue on finished goods and downstream processes.
- 3
Communicate with relevant team members and management about the issue.
- 4
Implement corrective actions to address the root cause of the problem.
- 5
Document the incident and review processes to prevent future occurrences.
Example Answers
I would first stop the packaging line to avoid shipping defective products. Then, I would quickly assess how many products are affected and inform my team and management. After that, I would investigate the root cause and implement corrective measures before restarting the process.
If an audit revealed non-compliance in your packaging processes, how would you address it?
How to Answer
- 1
Acknowledge the issue quickly and take responsibility.
- 2
Conduct a root cause analysis to find the source of non-compliance.
- 3
Develop a corrective action plan with clear steps and timelines.
- 4
Communicate the changes effectively to the team and stakeholders.
- 5
Implement continuous monitoring to prevent future issues.
Example Answers
I would promptly acknowledge the audit findings and take responsibility. Then, I would analyze the processes to identify the root cause of the non-compliance and create a corrective action plan, setting clear deadlines. Finally, I'd communicate the changes to my team and ensure we monitor our compliance closely moving forward.
Don't Just Read Packaging Supervisor Questions - Practice Answering Them!
Reading helps, but actual practice is what gets you hired. Our AI feedback system helps you improve your Packaging Supervisor interview answers in real-time.
Personalized feedback
Unlimited practice
Used by hundreds of successful candidates
What would you do if a key packaging material became unavailable at the last minute?
How to Answer
- 1
Stay calm and assess the situation quickly
- 2
Contact suppliers to find alternatives or expedited shipping
- 3
Consider using substitute materials that meet standards
- 4
Communicate with your team and stakeholders about the issue
- 5
Develop a contingency plan for future material shortages
Example Answers
If a key packaging material became unavailable, I would first verify the situation and assess how critical it is. I would then immediately contact alternative suppliers to see if they can provide the material quickly. In parallel, I would consider if we have any substitute materials on hand that could be used without compromising quality. I would keep the team informed throughout the process to ensure everyone is aligned.
If you were tasked with reducing packaging costs without compromising quality, how would you approach the situation?
How to Answer
- 1
Analyze current packaging materials and processes to identify inefficiencies.
- 2
Engage with suppliers to explore cost-effective raw materials without sacrificing quality.
- 3
Consider redesigning packaging for better material usage and shipping efficiency.
- 4
Implement a trial run for new solutions to assess impacts on quality and cost.
- 5
Gather feedback from team members involved in the supply chain for insights on improvements.
Example Answers
I would start by examining our current packaging processes to pinpoint areas where we can cut costs, like reducing excess material or streamlining workflows. Then, I'd collaborate with suppliers to find lower-cost materials that meet our quality standards. Afterward, a redesign of our packaging for better efficiency would be a priority.
How would you handle training a new team member who is struggling to learn the packaging processes?
How to Answer
- 1
Assess the specific areas where the new team member is struggling.
- 2
Break down the packaging processes into smaller, manageable steps.
- 3
Use hands-on demonstrations to illustrate each step clearly.
- 4
Provide continuous feedback and encouragement during the training.
- 5
Encourage questions and open communication to address any confusion.
Example Answers
I would first identify the exact processes they're struggling with. Then I would break those down into smaller steps and demonstrate each one, ensuring they understand before moving on. I'd give them tasks to practice and provide feedback along the way.
How would you motivate your team during a particularly exhausting packaging campaign?
How to Answer
- 1
Acknowledge the hard work and effort the team is putting in
- 2
Introduce small rewards or incentives for completing tasks
- 3
Foster a positive team environment with open communication
- 4
Set clear, achievable goals to create a sense of progress
- 5
Organize breaks and team-building activities to refresh morale
Example Answers
I would start by acknowledging the team's hard work and the challenges of the campaign. Then, I would implement a reward system where we celebrate milestones, like a small treat or an extra break for finishing a section. Additionally, I would ensure we have regular check-ins to maintain communication and support each other during the extra effort.
How would you decide to allocate limited resources during peak packaging periods?
How to Answer
- 1
Assess current resource availability and operational needs.
- 2
Prioritize high-demand products that meet customer deadlines.
- 3
Utilize data analytics to forecast peak times and adjust staffing accordingly.
- 4
Implement flexible team structures to shift resources as needed.
- 5
Communicate clearly with your team to ensure everyone understands priorities.
Example Answers
During peak times, I assess the overall demand and prioritize resources for the top-selling products to ensure we meet customer expectations. I also analyze data from previous years to anticipate needs and adjust staff accordingly.
How would you handle a situation where one team member is consistently underperforming?
How to Answer
- 1
Assess the reasons for the underperformance directly with the team member.
- 2
Set clear expectations and objectives for improvement.
- 3
Provide support and resources to help the team member succeed.
- 4
Monitor progress and give constructive feedback regularly.
- 5
Consider a formal performance improvement plan if necessary.
Example Answers
I would first have a one-on-one conversation with the team member to understand the reasons behind their underperformance. Together, we would set clear goals and I would offer my support to help them meet these goals. Regular check-ins would help us track progress.
What steps would you take if you noticed a drop in productivity in your packaging line?
How to Answer
- 1
Analyze the workflow to identify bottlenecks.
- 2
Consult with the team to gather feedback on any issues.
- 3
Check equipment for faults or required maintenance.
- 4
Review inventory levels to ensure materials are not causing delays.
- 5
Implement small adjustments or trials to improve efficiency.
Example Answers
First, I would analyze the workflow to find any potential bottlenecks causing the drop in productivity. Then, I would meet with the team to gather their insights on problems they might be facing. Next, I would check the packaging equipment for any maintenance issues that could be impacting the speed of our line.
How would you approach a situation where a customer has specific packaging requirements that differ from your standard processes?
How to Answer
- 1
Listen carefully to the customer's needs
- 2
Assess feasibility within current processes
- 3
Communicate any potential challenges or limitations
- 4
Propose a flexible solution or adjustment
- 5
Ensure follow-up to confirm satisfaction with the outcome
Example Answers
I would first listen to the customer's specific packaging requirements to fully understand their needs. Then, I would evaluate if we can meet those requirements within our current processes. If there are challenges, I would communicate these clearly and suggest alternative solutions that could work for both parties. Finally, I would follow up with the customer to ensure they are satisfied with the final outcome.
Don't Just Read Packaging Supervisor Questions - Practice Answering Them!
Reading helps, but actual practice is what gets you hired. Our AI feedback system helps you improve your Packaging Supervisor interview answers in real-time.
Personalized feedback
Unlimited practice
Used by hundreds of successful candidates
Behavioral Interview Questions
Can you describe a time when you had to lead a team through a significant packaging change? What was the outcome?
How to Answer
- 1
Choose a specific instance that highlights your leadership.
- 2
Explain the reasons for the packaging change and the challenges faced.
- 3
Describe your role in guiding the team and the strategies you used.
- 4
Discuss the outcome and any measurable improvements.
- 5
Reflect on what you learned from this experience.
Example Answers
In my previous role at XYZ Corp, we had to switch to eco-friendly packaging. I led a team of 5 throughout the transition. I facilitated brainstorming sessions to address challenges and keep everyone aligned. The project was completed ahead of schedule, reducing costs by 15% and increasing customer satisfaction due to our sustainability efforts.
Tell me about a challenging packaging issue you encountered and how you resolved it.
How to Answer
- 1
Select a specific and relevant packaging challenge you faced.
- 2
Explain the context and why it was challenging.
- 3
Describe the steps you took to address the issue.
- 4
Highlight the outcome and what you learned from the experience.
- 5
Connect your experience to how it prepares you for the Packaging Supervisor role.
Example Answers
In my previous role, we faced a problem with a packaging line that consistently produced defects due to misalignment. I analyzed the equipment settings, retrained the operators, and instituted a verification process. This reduced defects by 30% and improved on-time delivery.
Don't Just Read Packaging Supervisor Questions - Practice Answering Them!
Reading helps, but actual practice is what gets you hired. Our AI feedback system helps you improve your Packaging Supervisor interview answers in real-time.
Personalized feedback
Unlimited practice
Used by hundreds of successful candidates
Describe an instance where you had to collaborate with another department to improve the packaging process. What was your approach?
How to Answer
- 1
Identify the specific departments you collaborated with, such as production or quality control.
- 2
Describe the challenge in the packaging process that needed improvement.
- 3
Explain the steps you took to engage with the other department and gather input.
- 4
Highlight the solution you developed together and its impact on the process.
- 5
Use metrics or qualitative outcomes to emphasize the success of the collaboration.
Example Answers
At my previous job, I worked with the quality control department to address a high rate of packaging defects. We arranged a series of meetings to identify the root causes and discovered that a misalignment in machinery settings was contributing to the issue. Together, we adjusted the equipment settings and implemented a new quality check system. This collaboration reduced defects by 30% within two months.
How do you prioritize tasks and manage deadlines in a fast-paced packaging environment?
How to Answer
- 1
Assess urgency and impact of each task before starting.
- 2
Use a priority matrix to categorize tasks.
- 3
Communicate with team members to align on priorities.
- 4
Break down larger tasks into manageable steps.
- 5
Regularly review and adjust priorities as conditions change.
Example Answers
I prioritize tasks in a fast-paced environment by first assessing their urgency and impact. I categorize them using a priority matrix, which helps me see what needs immediate attention. Regular team check-ins ensure everyone is aligned on priorities, and I break larger tasks into smaller steps to manage them effectively.
Can you give an example of how you promoted safety practices within your packaging team?
How to Answer
- 1
Share a specific initiative or program you implemented.
- 2
Mention how you engaged the team in safety discussions.
- 3
Provide data or results showing improved safety metrics.
- 4
Discuss training sessions or workshops you organized.
- 5
Highlight any feedback from team members on the safety changes.
Example Answers
In my previous role, I initiated a weekly safety huddle where we discussed safety protocols in packaging. Over three months, we saw a 30% reduction in workplace incidents.
Tell me about a time you introduced a new packaging technology or method. What impact did it have?
How to Answer
- 1
Start by briefly describing the situation and the need for new technology.
- 2
Explain the new technology or method you introduced clearly.
- 3
Discuss the steps you took to implement it, including team involvement.
- 4
Highlight the measurable impact it had on efficiency or cost savings.
- 5
Conclude with what you learned and any further improvements made.
Example Answers
At my previous job, we were facing high material costs and inefficiencies in our packaging process. I researched and introduced a biodegradable packaging material that reduced costs by 15%. I trained the team on its use and adjusted our machinery accordingly. As a result, we not only saved money but also enhanced our brand's sustainability image.
Describe a time when you had to adapt to significant changes in packaging requirements. How did you manage it?
How to Answer
- 1
Identify a specific instance of change in packaging requirements you faced.
- 2
Explain the impact of the change on operations or the team.
- 3
Describe the steps you took to adapt, such as communication, training, or process adjustments.
- 4
Highlight any positive outcomes or improvements that resulted from your actions.
- 5
Keep the focus on your role and contributions during the change.
Example Answers
In my previous role, we had to switch to eco-friendly packaging materials mid-project. I organized a meeting with the team to discuss the changes and gather input. We quickly sourced new suppliers, updated our assembly line processes, and retrained our staff. As a result, we not only met the new requirements on time but also received positive feedback from customers about our commitment to sustainability.
Can you explain how you incorporate feedback from your team to improve packaging processes?
How to Answer
- 1
Actively seek regular feedback from team members during packaging reviews.
- 2
Implement an open-door policy for team members to voice concerns and suggestions.
- 3
Analyze feedback and identify common themes or issues that can be addressed.
- 4
Collaborate with the team on solutions and test new processes together.
- 5
Follow up with the team to assess the impact of changes made from their feedback.
Example Answers
I conduct regular packaging reviews with my team to gather feedback. I encourage everyone to share their thoughts on current processes. Once I identify common issues, we work together to create and test improvements. After implementing changes, I check back with the team to ensure the solutions are effective.
What do you consider your biggest success as a Packaging Supervisor, and what did you learn from it?
How to Answer
- 1
Choose a specific achievement that highlights your leadership skills
- 2
Explain the challenges you faced and how you overcame them
- 3
Discuss the impact of your success on the team or company
- 4
Share the lessons learned and how they apply to future situations
- 5
Keep your answer concise and focused on measurable outcomes
Example Answers
My biggest success was leading a project that reduced packaging waste by 30%. We faced challenges with supplier quality, but by renegotiating contracts and implementing stricter quality checks, we were able to improve our processes. This experience taught me the importance of adaptability and proactive communication in problem solving.
Don't Just Read Packaging Supervisor Questions - Practice Answering Them!
Reading helps, but actual practice is what gets you hired. Our AI feedback system helps you improve your Packaging Supervisor interview answers in real-time.
Personalized feedback
Unlimited practice
Used by hundreds of successful candidates
Describe your experience using data or analytics to improve packaging processes.
How to Answer
- 1
Focus on specific tools or software you used for data analysis.
- 2
Describe a particular project where data led to measurable improvements.
- 3
Highlight how you identified issues using data and the results of your interventions.
- 4
Mention collaboration with other departments or teams for data collection.
- 5
Quantify results to show the impact on efficiency or cost savings.
Example Answers
In my last role, I used Excel and statistical analysis to track packaging defect rates. By analyzing the data, I identified a specific machine that was causing a 15% increase in defects. After adjusting the machine settings based on data insights, we reduced defects by 30% and saved the company $20,000 annually.
Technical Interview Questions
What factors do you consider when selecting packaging materials for different products?
How to Answer
- 1
Identify the type of product and its specific needs.
- 2
Consider cost-effectiveness for the packaging materials.
- 3
Evaluate the environmental impact of the materials.
- 4
Ensure compliance with safety and regulatory requirements.
- 5
Assess the product's shelf life and storage conditions.
Example Answers
I consider the product type and its fragility. For fragile items, I prioritize protective materials. Cost is also important, so I look for budget-friendly options that do not compromise quality.
What packaging machinery are you experienced with, and how do you ensure it operates efficiently?
How to Answer
- 1
List specific machinery you have operated and your role with it
- 2
Highlight any maintenance tasks you performed to keep machinery running
- 3
Describe your approach to troubleshooting common issues
- 4
Mention any techniques you use to optimize the packing process
- 5
Emphasize teamwork and communication with operators and maintenance staff
Example Answers
I have experience operating shrink wrap machines and conveyor systems. To ensure efficiency, I regularly conduct preventative maintenance checks and manage routine cleaning schedules.
Don't Just Read Packaging Supervisor Questions - Practice Answering Them!
Reading helps, but actual practice is what gets you hired. Our AI feedback system helps you improve your Packaging Supervisor interview answers in real-time.
Personalized feedback
Unlimited practice
Used by hundreds of successful candidates
How do you implement quality control measures in the packaging process?
How to Answer
- 1
Define clear quality standards for packaging materials and final products.
- 2
Implement regular inspections at different stages of the packaging process.
- 3
Train staff on quality awareness and proper packaging techniques.
- 4
Use statistical process control to monitor packaging performance.
- 5
Gather and analyze feedback from customers regarding packaging issues.
Example Answers
I implement quality control by establishing specific standards for materials to ensure they meet safety and durability requirements. We conduct regular inspections of the packaging line to check for defects, and I train my team to spot potential issues before they escalate.
What industry standards and regulations do you need to adhere to as a Packaging Supervisor?
How to Answer
- 1
Identify key regulations relevant to packaging, such as FDA or ISO standards.
- 2
Mention safety regulations regarding materials and processes.
- 3
Discuss the importance of sustainability standards in packaging.
- 4
Highlight the need for quality control standards in production.
- 5
Show awareness of compliance with labeling requirements.
Example Answers
As a Packaging Supervisor, I adhere to FDA regulations for food packaging to ensure safety and compliance. I also follow ISO standards for quality management and sustainability practices.
Can you explain your experience with production planning in relation to packaging schedules?
How to Answer
- 1
Highlight specific production planning methodologies you have used.
- 2
Describe how you have coordinated with other departments to create packaging schedules.
- 3
Provide examples of how you adapted plans based on changes in demand or production.
- 4
Discuss tools or software you used for planning and scheduling.
- 5
Mention a specific achievement related to improving packaging efficiency.
Example Answers
In my previous role, I utilized Lean principles to develop efficient packaging schedules that minimized waste. I coordinated closely with the production team to ensure alignment with manufacturing timelines, adapting quickly to changes in demand by using our scheduling software.
What are your thoughts on sustainable packaging practices, and how have you implemented them in previous roles?
How to Answer
- 1
Define sustainable packaging and its importance to the environment.
- 2
Mention specific materials or techniques you have used that reduce waste.
- 3
Provide an example from your previous experience where you successfully implemented such practices.
- 4
Highlight any metrics or results that demonstrate the impact of your initiatives.
- 5
Express a commitment to continuous improvement in sustainability efforts.
Example Answers
Sustainable packaging is essential for reducing environmental impact. In my last role, I introduced biodegradable materials for our product packaging, which cut down waste by 30%. This change not only improved our brand image but also saved costs.
What metrics do you track to evaluate the efficiency and cost-effectiveness of packaging operations?
How to Answer
- 1
Identify key performance indicators (KPIs) relevant to packaging.
- 2
Include metrics like packaging cycle time, waste percentage, and labor cost per unit.
- 3
Explain how you use these metrics to improve operations.
- 4
Discuss the importance of data analysis in decision making.
- 5
Mention any software tools or systems used to track these metrics.
Example Answers
I track metrics such as packaging cycle time, which helps identify bottlenecks in the process, and waste percentage to minimize material costs. Regularly reviewing these KPIs allows me to implement efficiency improvements.
How do you stay updated with the latest trends and technologies in the packaging industry?
How to Answer
- 1
Subscribe to industry newsletters and publications to get regular updates.
- 2
Attend trade shows and webinars to learn about new technologies.
- 3
Join professional organizations and online forums to network with peers.
- 4
Follow industry leaders and influencers on social media platforms.
- 5
Participate in relevant training programs or workshops to enhance your skills.],
- 6
sampleAnswers
- 7
:
Example Answers
I stay updated by subscribing to industry newsletters like Packaging World and attending annual trade shows where I can see the latest technologies in action.
How do you work with design teams to ensure that packaging design meets functionality and branding requirements?
How to Answer
- 1
Communicate clearly the functionality needs and branding goals at the start.
- 2
Involve design teams early in the packaging development process.
- 3
Set up regular check-ins to review design progress and provide feedback.
- 4
Encourage collaboration between packaging, marketing, and design teams.
- 5
Use prototypes to test functionality and branding alignment before finalizing.
Example Answers
I start by holding a meeting with the design team where I outline our functionality requirements and branding objectives. This helps align everyone's goals from the beginning. I also schedule regular check-ins to discuss progress and provide feedback.
Explain how supply chain management affects packaging operations in your view.
How to Answer
- 1
Discuss the importance of timely delivery of packaging materials.
- 2
Mention how inventory levels influence packaging efficiency.
- 3
Reflect on how demand forecasting impacts packaging decisions.
- 4
Talk about collaboration with suppliers for better packaging solutions.
- 5
Consider the role of technology in integrating supply chain and packaging processes.
Example Answers
Supply chain management is crucial for packaging operations as it ensures that packaging materials are delivered on time. Delays in materials can halt production. Additionally, maintaining proper inventory levels means we can package products efficiently without excess waste or shortages. Accurate demand forecasting also allows us to plan appropriate packaging for upcoming orders.
Don't Just Read Packaging Supervisor Questions - Practice Answering Them!
Reading helps, but actual practice is what gets you hired. Our AI feedback system helps you improve your Packaging Supervisor interview answers in real-time.
Personalized feedback
Unlimited practice
Used by hundreds of successful candidates
Packaging Supervisor Position Details
Salary Information
Recommended Job Boards
CareerBuilder
www.careerbuilder.com/jobs/packaging-supervisorZipRecruiter
www.ziprecruiter.com/Jobs/Packaging-SupervisorThese job boards are ranked by relevance for this position.
Related Positions
Ace Your Next Interview!
Practice with AI feedback & get hired faster
Personalized feedback
Used by hundreds of successful candidates
Ace Your Next Interview!
Practice with AI feedback & get hired faster
Personalized feedback
Used by hundreds of successful candidates