Top 32 Machine Shop Supervisor Interview Questions and Answers [Updated 2025]
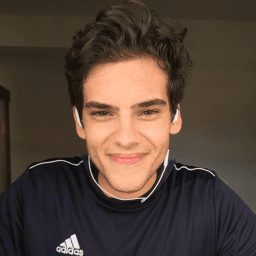
Andre Mendes
•
March 30, 2025
Navigating the interview process for a Machine Shop Supervisor position can be daunting, but preparation is key to success. In this post, we've compiled the most common interview questions for the role, offering insightful example answers and practical tips on how to respond effectively. Whether you're a seasoned professional or new to the field, this guide will help you confidently tackle your next interview and secure your dream job.
Download Machine Shop Supervisor Interview Questions in PDF
To make your preparation even more convenient, we've compiled all these top Machine Shop Supervisorinterview questions and answers into a handy PDF.
Click the button below to download the PDF and have easy access to these essential questions anytime, anywhere:
List of Machine Shop Supervisor Interview Questions
Behavioral Interview Questions
Can you describe a time when you successfully led a team through a challenging project?
How to Answer
- 1
Choose a specific project that had clear challenges.
- 2
Highlight your leadership role and the actions you took.
- 3
Emphasize teamwork, communication, and solutions you implemented.
- 4
Include positive outcomes and what you learned from the experience.
- 5
Keep your answer focused and structured, using the STAR method.
Example Answers
In my previous role, we faced a tight deadline on a custom order. I organized daily team meetings to track progress and address any issues. We divided the tasks based on each member's strengths, which increased efficiency. We completed the project on time and received positive feedback from the client.
Can you describe an instance where clear communication was vital to a project’s success?
How to Answer
- 1
Choose a relevant project from your experience
- 2
Highlight the specific communication methods used
- 3
Explain the challenges faced due to poor communication
- 4
Describe the positive outcome resulting from clear communication
- 5
Reflect on what you learned and how it shaped your approach
Example Answers
In my previous role, we had a project where our team was building a custom part for a client. I organized daily stand-up meetings to ensure everyone was aligned on the tasks. There was a misunderstanding initially about the specifications, but by clarifying these in our meetings, we avoided costly rework and delivered on time, which increased client satisfaction.
Don't Just Read Machine Shop Supervisor Questions - Practice Answering Them!
Reading helps, but actual practice is what gets you hired. Our AI feedback system helps you improve your Machine Shop Supervisor interview answers in real-time.
Personalized feedback
Unlimited practice
Used by hundreds of successful candidates
Tell me about a conflict you experienced in the shop and how you resolved it.
How to Answer
- 1
Identify a specific conflict situation you've faced.
- 2
Explain the roles of the people involved and the circumstances.
- 3
Describe the steps you took to resolve the conflict clearly.
- 4
Emphasize the positive outcome and what you learned.
- 5
Keep the story focused and relevant to the supervisor role.
Example Answers
In a previous job, I noticed a disagreement between two machinists over the correct setup for a CNC machine. I facilitated a meeting where each could voice their perspective, then we reviewed the setup documentation together. This collaboration led to a mutually agreed method which increased efficiency. Both machinists appreciated being heard and there was better teamwork afterward.
Provide an example of how you promoted safety in the machine shop.
How to Answer
- 1
Share a specific safety initiative you led or participated in.
- 2
Explain how you communicated safety protocols to your team.
- 3
Describe any training sessions or workshops you organized.
- 4
Mention any safety equipment or measures you implemented.
- 5
Include any measurable outcomes, like reduced accidents or increased safety compliance.
Example Answers
In my previous role, I initiated a weekly safety briefing where we discussed potential hazards and reviewed safety protocols. This led to a 30% reduction in near misses over six months.
Describe a situation where teamwork was crucial for achieving your goals in the shop.
How to Answer
- 1
Identify a specific project that required collaboration.
- 2
Explain the roles of different team members and your role.
- 3
Highlight the challenges faced and how teamwork helped overcome them.
- 4
Conclude with the successful outcome and what you learned about teamwork.
- 5
Keep it focused on the shop environment.
Example Answers
During a major equipment overhaul, my team and I had to coordinate closely. I was in charge of scheduling while my colleagues handled maintenance tasks. We encountered unexpected delays, but by communicating openly and adjusting our roles, we completed the project two days ahead of schedule, emphasizing the importance of teamwork.
Explain how you handled an underperforming employee.
How to Answer
- 1
Identify the specific performance issues with clear examples.
- 2
Communicate directly with the employee to understand their perspective.
- 3
Set clear expectations and create an improvement plan together.
- 4
Provide regular feedback and support during the improvement process.
- 5
Document the process and outcomes for future reference.
Example Answers
In my previous role, an employee was consistently missing deadlines on projects. I had a candid conversation to understand their challenges and found they were overloaded. Together, we prioritized tasks and set realistic deadlines. I followed up regularly, providing support and feedback, which resulted in their improved performance over time.
Tell me about a difficult decision you made in relation to production schedules.
How to Answer
- 1
Identify a specific situation that had significant impact.
- 2
Explain the factors you considered in making your decision.
- 3
Discuss the outcome and what you learned from it.
- 4
Use clear and concise language.
- 5
Highlight your problem-solving skills and leadership.
Example Answers
In my previous role, we faced a significant delay due to a machine breakdown. I had to decide whether to expedite a larger order and risk upsetting our relationship with other clients or to push back the timeline. I chose to negotiate with the larger client for a delayed delivery while keeping other clients satisfied. This decision maintained our long-term relationships and taught me the importance of communication.
Describe how you have trained new employees on machine operation.
How to Answer
- 1
Explain your training methodology clearly and concisely
- 2
Provide examples of specific machines used in training
- 3
Mention the importance of safety protocols during training
- 4
Discuss how you assess new employees' understanding and skills
- 5
Highlight any follow-up support or mentorship provided
Example Answers
I create a structured training schedule that includes both classroom instruction and hands-on experience. For example, I trained new hires on the CNC machine by first demonstrating its operation and safety features, then guiding them through their first run while monitoring their progress closely.
Don't Just Read Machine Shop Supervisor Questions - Practice Answering Them!
Reading helps, but actual practice is what gets you hired. Our AI feedback system helps you improve your Machine Shop Supervisor interview answers in real-time.
Personalized feedback
Unlimited practice
Used by hundreds of successful candidates
Describe a time when you mentored a colleague or subordinate.
How to Answer
- 1
Choose a specific example that highlights your mentoring skills.
- 2
Explain the context and the challenge your colleague faced.
- 3
Detail your approach to mentoring and how you supported them.
- 4
Share the outcome and what your colleague learned.
- 5
Emphasize the impact of your mentoring on the team's performance.
Example Answers
I mentored a new machinist who struggled with setting up CNC machines. I guided him through the setup process step-by-step and provided resources. With practice, he improved drastically and became one of our top machine operators, boosting production efficiency.
Technical Interview Questions
What factors do you consider when selecting materials for machining?
How to Answer
- 1
Assess the mechanical properties needed for the part such as strength and hardness.
- 2
Consider the machinability of the material, including tool wear and cutting speed.
- 3
Evaluate the cost and availability of the material in your region.
- 4
Take into account the finished product's environmental and operational conditions.
- 5
Ensure the material complies with relevant industry standards and regulations.
Example Answers
When selecting materials, I focus on mechanical properties like strength and hardness to ensure they meet product specifications. I also evaluate machinability to minimize tool wear and costs.
How do you ensure compliance with safety and environmental regulations?
How to Answer
- 1
Conduct regular training sessions for staff on safety protocols
- 2
Implement a checklist for safety and environmental compliance reviews
- 3
Establish clear reporting procedures for safety incidents and near-misses
- 4
Stay updated with local regulations and adapt policies accordingly
- 5
Encourage a culture of safety where employees feel responsible for compliance
Example Answers
I conduct monthly training sessions that cover the latest safety protocols and environmental regulations to keep everyone informed and compliant.
Don't Just Read Machine Shop Supervisor Questions - Practice Answering Them!
Reading helps, but actual practice is what gets you hired. Our AI feedback system helps you improve your Machine Shop Supervisor interview answers in real-time.
Personalized feedback
Unlimited practice
Used by hundreds of successful candidates
What steps do you take when troubleshooting machine issues?
How to Answer
- 1
Identify the symptoms of the issue
- 2
Check the machine's manual for troubleshooting tips
- 3
Inspect relevant components for wear or damage
- 4
Run diagnostic tests or use monitoring tools
- 5
Collaborate with team members for insights or advice
Example Answers
First, I identify any symptoms such as unusual noises or performance drops. Then, I refer to the machine's manual for troubleshooting guidance. After that, I inspect parts like belts and gears for wear and damage before running any diagnostics.
What machining processes are you most familiar with?
How to Answer
- 1
Identify the machining processes you know best and have hands-on experience with.
- 2
Discuss popular processes like turning, milling, grinding, and drilling.
- 3
Mention any CNC machining experience, as it's highly relevant.
- 4
Highlight any specialized techniques or tools you've worked with.
- 5
Provide examples of projects where you applied these machining processes.
Example Answers
I have extensive experience with CNC milling and turning. In my previous role, I supervised a team that handled complex machining tasks, ensuring high quality and efficiency.
How do you prioritize machine maintenance in your shop?
How to Answer
- 1
Assess machine usage to identify critical equipment needing regular checks
- 2
Implement a maintenance schedule based on manufacturer recommendations and usage data
- 3
Prioritize preventive maintenance over reactive repairs whenever possible
- 4
Involve your team in reporting issues and provide training on maintenance protocols
- 5
Use a tracking system to monitor maintenance history and schedule upcoming tasks
Example Answers
I prioritize machine maintenance by assessing our most frequently used machines and scheduling regular preventive checks based on their operational hours.
What methods do you use to ensure product quality in machining?
How to Answer
- 1
Implement a systematic inspection process at each stage of production
- 2
Utilize calibrated tools and equipment to guarantee accuracy
- 3
Train and involve operators in quality checks to foster accountability
- 4
Analyze data from past production runs to identify areas of improvement
- 5
Encourage feedback from the team on quality issues to foster a proactive culture
Example Answers
I ensure product quality by implementing regular inspections at every stage of machining, using calibrated tools for precision, and involving operators in quality checks to create accountability.
Can you explain how you develop production schedules based on orders?
How to Answer
- 1
Assess order volumes and deadlines to prioritize tasks.
- 2
Evaluate available resources and capabilities within the shop.
- 3
Incorporate lead times for materials and any external factors.
- 4
Communicate with team members to ensure alignment on schedules.
- 5
Be flexible and ready to adjust schedules based on real-time changes.
Example Answers
To develop production schedules, I start by analyzing the order volumes and deadlines to prioritize jobs. Then, I assess our machine capabilities and workforce availability. I ensure I account for lead times on materials and communicate with my team to align on our schedule, making adjustments as necessary.
What software tools do you use for machining or shop management?
How to Answer
- 1
Mention specific software you are familiar with like CAD, CAM, or ERP systems.
- 2
Explain how you have used these tools to improve efficiency or productivity.
- 3
Discuss any experience with software for inventory management or scheduling.
- 4
Highlight any integration of software tools with machine tools or processes.
- 5
Be prepared to discuss your familiarity with updates or new tools in the industry.
Example Answers
I have experience using Mastercam for CAM programming, which has helped streamline our machining operations, reducing setup times significantly.
What manufacturing standards are you familiar with and how do you apply them?
How to Answer
- 1
Identify key manufacturing standards relevant to machining such as ISO 9001 or AS9100.
- 2
Discuss how you implement these standards in daily operations to ensure quality.
- 3
Provide examples of how you’ve trained staff on these standards.
- 4
Mention any specific tools or processes you use to maintain compliance.
- 5
Explain the benefits of these standards for productivity and safety.
Example Answers
I am familiar with ISO 9001 and AS9100. In my previous role, I implemented ISO 9001 processes by conducting regular quality audits and ensuring documentation was up to date, which improved compliance and accountability in our operations.
Explain the importance of calibration in machining tools and how you approach it.
How to Answer
- 1
Define calibration and its role in precision machining.
- 2
Emphasize the impact of calibration on product quality and safety.
- 3
Describe your process for calibrating tools to ensure accuracy.
- 4
Mention any specific tools or systems you use for calibration.
- 5
Share experiences where proper calibration prevented issues.
Example Answers
Calibration is essential to ensure that machining tools operate with precision, which directly affects product quality. I regularly check and adjust our tools before production runs, using certified standards to verify accuracy. This not only maintains quality but also reduces scrap rates.
Don't Just Read Machine Shop Supervisor Questions - Practice Answering Them!
Reading helps, but actual practice is what gets you hired. Our AI feedback system helps you improve your Machine Shop Supervisor interview answers in real-time.
Personalized feedback
Unlimited practice
Used by hundreds of successful candidates
Situational Interview Questions
What would you do if a machine breaks down during a critical production run?
How to Answer
- 1
Assess the situation quickly to determine the impact of the breakdown.
- 2
Communicate immediately with the team and inform relevant stakeholders.
- 3
Implement a contingency plan or shift to backup machinery if available.
- 4
Work with maintenance to diagnose and fix the issue efficiently.
- 5
Monitor the production schedule closely to minimize delays.
Example Answers
I would first assess how severe the breakdown is and its impact on production. Next, I would inform my team and management about the situation. If we have backup machines, I would switch to them to keep production going. I’d collaborate with maintenance to repair the broken machine as quickly as possible and ensure we keep track of the production delays.
How would you handle a situation where you are short-staffed during peak production?
How to Answer
- 1
Assess the immediate needs and prioritize tasks.
- 2
Communicate with your team to understand each person's workload.
- 3
Consider temporary adjustments like overtime or shifting shifts.
- 4
Keep stakeholders informed about the situation and any impacts.
- 5
Focus on maintaining quality and safety even with reduced staff.
Example Answers
I would first assess which tasks are critical and prioritize those. Then I would talk to my team about their current workloads and see who can take on extra duties. I would also consider offering overtime or shifting schedules to cover gaps. Keeping my managers updated is important to manage expectations.
Don't Just Read Machine Shop Supervisor Questions - Practice Answering Them!
Reading helps, but actual practice is what gets you hired. Our AI feedback system helps you improve your Machine Shop Supervisor interview answers in real-time.
Personalized feedback
Unlimited practice
Used by hundreds of successful candidates
How would you respond to a team member who is resistant to feedback?
How to Answer
- 1
Seek to understand their perspective first
- 2
Provide specific examples of the feedback
- 3
Emphasize the benefits of the feedback for their growth
- 4
Encourage open communication and dialogue
- 5
Follow up to show support and track progress
Example Answers
I would first ask them about their feelings on the feedback to understand their perspective. Then, I'd share specific examples of why the feedback is important for their development. I would also highlight how acting on the feedback could help them succeed in their role.
Imagine you notice that production is consistently behind schedule. How would you address this?
How to Answer
- 1
Analyze the root cause of the delays by reviewing production data.
- 2
Communicate with the team to gather input on obstacles they face.
- 3
Implement a prioritization system for tasks and resource allocation.
- 4
Monitor progress regularly and adjust strategies as needed.
- 5
Foster a team environment that encourages proactive problem-solving.
Example Answers
I would first review the production reports to identify patterns in the delays. Then, I would hold a meeting with the team to discuss their challenges and gather insights. Based on this information, I would implement a prioritization system to ensure critical tasks are completed on time and closely monitor our progress weekly.
What actions would you take if you witnessed a safety violation on the shop floor?
How to Answer
- 1
Immediately address the situation to ensure everyone's safety.
- 2
Document the violation with specific details.
- 3
Report the violation to your supervisor or safety officer.
- 4
Encourage a culture of safety by discussing the violation with the team.
- 5
Follow up to ensure corrective actions are taken.
Example Answers
If I witnessed a safety violation, I would first intervene to ensure no one is at risk. Then, I'd document the incident and report it to my supervisor for further action.
How would you handle an issue where a customer is dissatisfied with a product?
How to Answer
- 1
Listen carefully to the customer's concerns without interrupting
- 2
Apologize for the inconvenience and show empathy
- 3
Ask for specific details about the issue to understand it fully
- 4
Offer a solution, such as repair, replacement, or refund
- 5
Follow up with the customer to ensure their satisfaction after the issue is resolved
Example Answers
I would first listen to the customer's concerns and apologize for their dissatisfaction. Then, I would ask for specific details to understand the issue better and offer a solution that suits them, like a replacement or a refund. Finally, I would follow up to make sure they are happy with the resolution.
How would you approach training for a new piece of machinery that your shop has acquired?
How to Answer
- 1
Assess the machine specifications and capabilities thoroughly
- 2
Develop a structured training program with clear objectives
- 3
Utilize experienced staff to lead hands-on training sessions
- 4
Provide documentation and resources for reference
- 5
Create a feedback loop for continuous improvement of the training process
Example Answers
I would start by reviewing the machine's manual and specifications to understand its operations. Then, I'd design a training program that outlines key skills staff need to learn. Experienced operators would lead practical sessions, and I'd ensure everyone has access to a detailed guide for reference. After training, I'd gather feedback to improve future sessions.
If your budget for supplies was cut, how would you manage the shop's needs?
How to Answer
- 1
Prioritize critical supplies based on immediate needs
- 2
Negotiate with suppliers for better pricing or discounts
- 3
Implement a tracking system for inventory to manage usage
- 4
Encourage staff to suggest cost-saving measures
- 5
Explore alternative materials or resources that may be more affordable
Example Answers
In response to a budget cut, I would first assess which supplies are essential for daily operations and prioritize those. Then, I would reach out to suppliers to negotiate better prices and look for bulk purchasing options. Implementing an inventory tracking system would help us monitor our usage and avoid waste.
What would you do if you found a new technique that could improve efficiency but required changes to procedures?
How to Answer
- 1
Evaluate the benefits of the new technique against the current procedures
- 2
Consult with your team to gather input and address potential concerns
- 3
Develop a clear plan for implementing the new procedure smoothly
- 4
Provide training and resources to support the transition
- 5
Communicate regularly with all stakeholders about the changes and expected outcomes
Example Answers
I would analyze the new technique's potential impact on efficiency and gather feedback from my team to ensure everyone is on board with the changes. Then, I would outline a step-by-step implementation plan including training sessions to ensure a smooth transition.
What strategies would you implement if you were tasked with improving shop productivity?
How to Answer
- 1
Assess current workflows to identify bottlenecks
- 2
Engage with the team to gather input and suggestions
- 3
Implement lean manufacturing techniques to reduce waste
- 4
Utilize data analytics to track productivity metrics
- 5
Set clear goals and monitor progress regularly
Example Answers
I would start by analyzing our current workflows to spot any bottlenecks that are causing delays. By talking to the team, I can gather their insights and ideas for improvement. Implementing lean manufacturing techniques would also help us cut down on waste and enhance efficiency. Finally, I would establish clear goals and track our progress using productivity metrics.
Don't Just Read Machine Shop Supervisor Questions - Practice Answering Them!
Reading helps, but actual practice is what gets you hired. Our AI feedback system helps you improve your Machine Shop Supervisor interview answers in real-time.
Personalized feedback
Unlimited practice
Used by hundreds of successful candidates
How would you decide where to allocate limited resources when running multiple projects?
How to Answer
- 1
Identify the project's impact on overall goals
- 2
Evaluate deadlines and urgency of each project
- 3
Assess available skills and resources for each task
- 4
Communicate with your team to understand their needs
- 5
Create a prioritization matrix to visualize options
Example Answers
I would prioritize projects based on their alignment with our business goals and potential ROI. Next, I would consider the deadlines and urgency of each project to ensure timely delivery.
Machine Shop Supervisor Position Details
Recommended Job Boards
CareerBuilder
www.careerbuilder.com/jobs/machine-shop-supervisorThese job boards are ranked by relevance for this position.
Related Positions
Ace Your Next Interview!
Practice with AI feedback & get hired faster
Personalized feedback
Used by hundreds of successful candidates
Ace Your Next Interview!
Practice with AI feedback & get hired faster
Personalized feedback
Used by hundreds of successful candidates