Top 30 Factory Supervisor Interview Questions and Answers [Updated 2025]
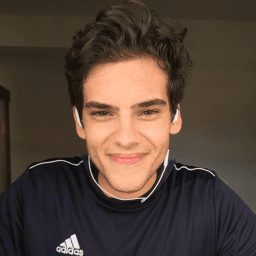
Andre Mendes
•
March 30, 2025
Navigating the competitive landscape of factory supervision demands not only technical expertise but also exceptional leadership skills. In this blog post, we delve into the most common interview questions faced by aspiring Factory Supervisors. With expert-crafted example answers and insightful tips, you'll be equipped to convey your qualifications confidently and effectively, setting the stage for success in your next interview.
Download Factory Supervisor Interview Questions in PDF
To make your preparation even more convenient, we've compiled all these top Factory Supervisorinterview questions and answers into a handy PDF.
Click the button below to download the PDF and have easy access to these essential questions anytime, anywhere:
List of Factory Supervisor Interview Questions
Behavioral Interview Questions
Can you describe a time when you had to lead a team through a challenging project in the factory?
How to Answer
- 1
Select a specific project and clearly outline the challenges faced.
- 2
Explain your role and the actions you took as a leader.
- 3
Discuss how you motivated your team and resolved conflicts.
- 4
Highlight the results achieved and what you learned from the experience.
- 5
Use the STAR method: Situation, Task, Action, Result.
Example Answers
In a previous factory project, we had to meet an unexpected production deadline due to client demands. As the supervisor, I organized daily briefings to ensure everyone was aligned and motivated. We implemented overtime shifts and streamlined processes to meet our goals. Ultimately, we completed the project on time and improved our production efficiency by 15%. This taught me the importance of team communication and flexibility.
Tell me about a situation where you identified a significant operational issue and how you resolved it.
How to Answer
- 1
Identify a specific issue you faced in a previous role.
- 2
Explain the impact of the issue on operations or productivity.
- 3
Describe the steps you took to analyze and resolve the problem.
- 4
Highlight any collaboration with team members or management.
- 5
Conclude with the positive results of your actions and any lessons learned.
Example Answers
In my previous job, we faced frequent machine breakdowns that slowed production lines. I analyzed the maintenance logs and found that preventive maintenance was being overlooked. I worked with the team to develop a schedule for regular checks, which reduced breakdowns by 30% in three months.
Don't Just Read Factory Supervisor Questions - Practice Answering Them!
Reading helps, but actual practice is what gets you hired. Our AI feedback system helps you improve your Factory Supervisor interview answers in real-time.
Personalized feedback
Unlimited practice
Used by hundreds of successful candidates
Give an example of how you have successfully managed a team conflict in the workplace.
How to Answer
- 1
Identify the conflicting parties and listen to their perspectives
- 2
Facilitate a discussion to encourage open communication
- 3
Focus on finding common ground and shared goals
- 4
Guide the team to a collaborative solution
- 5
Follow up to ensure the conflict is resolved and relationships are restored
Example Answers
In my previous role, two team members disagreed on project priorities. I organized a meeting where each could share their viewpoint, which was critical to understanding their positions. We then discussed our shared objective of meeting the project deadline and agreed on a compromise that allowed us to combine their ideas effectively.
Describe an experience when you implemented a new safety protocol in the factory.
How to Answer
- 1
Identify a specific safety protocol you implemented.
- 2
Explain the reason for the change and its importance.
- 3
Describe the steps you took to implement the protocol.
- 4
Highlight how you ensured team compliance and training.
- 5
Mention the results or improvements observed post-implementation.
Example Answers
In my previous role, I implemented a new lockout/tagout protocol after noticing safety incidents during maintenance. I conducted risk assessments to highlight hazards, trained the team using workshops, and monitored compliance through regular audits. As a result, we saw a 40% decrease in safety incidents over 6 months.
Have you ever faced a situation where product quality was compromised? How did you handle it?
How to Answer
- 1
Describe the situation clearly and briefly.
- 2
Explain the cause of the quality compromise.
- 3
Detail the steps you took to address the issue.
- 4
Highlight any collaboration with your team or other departments.
- 5
Conclude with the outcome and what you learned from the experience.
Example Answers
In my previous role, we discovered a batch of products that did not meet quality standards due to a machine malfunction. I quickly gathered a team to identify the problem, fixed the machine, and we re-inspected all products. We then implemented additional checks to prevent this from happening again. This resulted in a 30% improvement in product quality in the following months.
How have you contributed to the professional development of your team members in the past?
How to Answer
- 1
Identify specific training or mentoring programs you initiated.
- 2
Share examples of individual coaching sessions that led to growth.
- 3
Mention how you encouraged certification or skill advancement.
- 4
Discuss creating opportunities for team members to take on new challenges.
- 5
Highlight feedback and performance reviews that promoted development.
Example Answers
In my previous role, I developed a mentorship program where more experienced workers guided new hires, which improved retention and skills across the board.
Tell me about a time you had to adapt to a significant change in your work environment.
How to Answer
- 1
Choose a specific change that was impactful.
- 2
Explain the situation clearly and concisely.
- 3
Describe the actions you took to adapt.
- 4
Highlight any positive outcomes or lessons learned.
- 5
Keep the focus on your adaptability and problem-solving skills.
Example Answers
At my previous job, we switched to a new production scheduling software. I took the initiative to learn the system ahead of time and organized a training session for my team. This helped everyone transition smoothly, and we maintained our production targets during the change.
Describe a time when you initiated an innovative practice or technology in your workplace.
How to Answer
- 1
Choose a specific innovation you implemented.
- 2
Explain the problem that prompted the innovation.
- 3
Describe the steps you took to implement it.
- 4
Highlight the positive outcomes and any metrics of success.
- 5
Emphasize teamwork and how you engaged others.
Example Answers
In my previous role, I noticed inefficiencies in our inventory process. I researched and introduced a digital inventory management system. I trained the team on the new software and we saw a 30% decrease in inventory discrepancies within three months.
Don't Just Read Factory Supervisor Questions - Practice Answering Them!
Reading helps, but actual practice is what gets you hired. Our AI feedback system helps you improve your Factory Supervisor interview answers in real-time.
Personalized feedback
Unlimited practice
Used by hundreds of successful candidates
Technical Interview Questions
What methodologies do you employ for process improvement in a factory environment?
How to Answer
- 1
Mention specific methodologies like Lean, Six Sigma, or Kaizen.
- 2
Provide examples of how you've implemented these methodologies in past roles.
- 3
Discuss the importance of data analysis in identifying areas for improvement.
- 4
Emphasize collaboration with team members for effective process enhancement.
- 5
Highlight any measurable outcomes from the improvements you've made.
Example Answers
I utilize Lean methodologies to streamline processes by eliminating waste. For example, in my previous role, I reduced scrap rates by 15% through a Value Stream Mapping exercise.
Can you explain how to create an effective production schedule?
How to Answer
- 1
Analyze demand forecasts to determine production needs.
- 2
Identify capacity constraints and resource availability.
- 3
Break down the production process into specific tasks and timelines.
- 4
Utilize scheduling software to optimize the schedule.
- 5
Regularly review and adjust the schedule based on performance and feedback.
Example Answers
To create an effective production schedule, I start by analyzing demand forecasts to ensure we meet customer needs. Then, I assess our capacity and resources to identify any constraints. I break the production into tasks and assign realistic timelines, using scheduling software for optimization. Regular reviews help me adjust the schedule as needed.
Don't Just Read Factory Supervisor Questions - Practice Answering Them!
Reading helps, but actual practice is what gets you hired. Our AI feedback system helps you improve your Factory Supervisor interview answers in real-time.
Personalized feedback
Unlimited practice
Used by hundreds of successful candidates
What experience do you have with maintenance management systems or tools?
How to Answer
- 1
Identify specific systems or tools you have used.
- 2
Mention any certifications or training relevant to these tools.
- 3
Describe the impact of these systems on your previous roles.
- 4
Share specific examples of issues you resolved using these tools.
- 5
Explain how you collaborated with teams to enhance maintenance processes.
Example Answers
I have experience using CMMS tools like SAP PM and Maintenance Connection. In my last role, I implemented SAP PM which improved our maintenance scheduling by 30%, allowing us to reduce machine downtime significantly.
What are the key regulations that impact factory operations, and how do you ensure compliance?
How to Answer
- 1
Identify relevant regulations such as OSHA, EPA, and local labor laws
- 2
Discuss how you keep up-to-date with changes in regulations
- 3
Explain methods for training staff on compliance policies
- 4
Describe audits and inspections you conduct
- 5
Share examples of compliance challenges and solutions you've implemented
Example Answers
In my experience, key regulations like OSHA for workplace safety and EPA for environmental standards are crucial. I subscribe to industry updates to stay informed about changes. I ensure compliance by conducting regular training sessions for my staff and performing internal audits quarterly to identify any issues.
Describe your understanding and experience with lean manufacturing principles.
How to Answer
- 1
Define lean manufacturing and emphasize its goal of minimizing waste.
- 2
Share specific lean tools you've used, such as 5S or Kaizen.
- 3
Illustrate with a concrete example of a successful lean initiative you led.
- 4
Highlight the impact of lean practices on efficiency or quality.
- 5
Mention any training or certifications in lean methodologies.
Example Answers
Lean manufacturing is focused on eliminating waste and improving processes. In my previous role, I implemented 5S, resulting in a 20% increase in productivity and a cleaner work environment. Our team adopted continuous improvement through weekly Kaizen meetings.
How do you utilize data analytics to improve production efficiency?
How to Answer
- 1
Identify key performance indicators (KPIs) relevant to production.
- 2
Use data analytics tools to monitor production metrics in real-time.
- 3
Analyze historical data to identify trends and bottlenecks.
- 4
Implement process adjustments based on data insights.
- 5
Communicate findings clearly to the team to drive changes.
Example Answers
I track KPIs like cycle time and defect rates using a dashboard that updates in real-time. This helps me identify trends. For example, by analyzing last month's data, I spotted a bottleneck in the packaging stage, which I resolved by reallocating resources, increasing efficiency by 15%.
What strategies do you use to control manufacturing costs?
How to Answer
- 1
Identify key areas where costs can be reduced such as materials, labor, and overhead.
- 2
Implement lean manufacturing principles to minimize waste and improve efficiency.
- 3
Regularly analyze production data to find trends and areas for cost-cutting.
- 4
Engage employees in cost-saving initiatives and ideas for improving processes.
- 5
Negotiate with suppliers to get better rates on bulk materials.
Example Answers
I focus on lean manufacturing practices which allow us to minimize waste and improve efficiency, thereby reducing costs significantly.
What methods do you use for effective inventory management in a factory?
How to Answer
- 1
Utilize a first-in, first-out (FIFO) method to minimize waste.
- 2
Implement regular cycle counting to ensure accuracy of stock levels.
- 3
Adopt inventory management software for real-time tracking.
- 4
Set reorder points and safety stock levels to avoid stockouts.
- 5
Conduct regular reviews of inventory processes to identify improvements.
Example Answers
I focus on FIFO to ensure we use older stock first, reducing waste. Plus, I schedule monthly cycle counts to keep our records accurate.
What is your approach to implementing cross-training among factory workers?
How to Answer
- 1
Identify key areas where cross-training will improve efficiency and flexibility.
- 2
Assess current skills of workers to determine training needs.
- 3
Create a structured training program with clear goals and timelines.
- 4
Encourage peer-to-peer learning and mentorship among workers.
- 5
Evaluate the effectiveness of cross-training and adjust the program as necessary.
Example Answers
At my previous job, I first identified key roles where cross-training could enhance production. I then assessed each worker’s skills and created a tailored training program. We paired experienced workers with novices for mentorship, fostering a collaborative environment.
Situational Interview Questions
If you notice a significant drop in production output, what steps would you take to address it?
How to Answer
- 1
Immediately gather data to identify the cause of the drop.
- 2
Engage with team members to collect insights on any issues they are facing.
- 3
Assess machinery and equipment for any malfunctions or downtime.
- 4
Review inventory levels to ensure materials are not the bottleneck.
- 5
Develop an action plan with clear steps to rectify the situation.
Example Answers
First, I would analyze production metrics to pinpoint the reason for the drop. Then, I would talk with my team to gather their input on any challenges they are encountering. If necessary, I would inspect the equipment to rule out any malfunctions and check material availability to ensure there are no supply issues. Finally, I would create a targeted action plan to address any identified problems swiftly.
How would you handle a situation where a critical piece of machinery fails unexpectedly?
How to Answer
- 1
Stay calm and assess the situation quickly.
- 2
Communicate with your team about the issue and potential impact.
- 3
Initiate emergency protocols if necessary.
- 4
Determine if the issue can be fixed in-house or if external help is needed.
- 5
Document the incident and review for future prevention.
Example Answers
If a critical piece of machinery fails, I would first remain calm and assess the situation to understand the severity. Then, I would inform my team about the failure and discuss the next steps. If urgent, I would initiate our emergency protocols and contact maintenance. I would also document the incident for future reference.
Don't Just Read Factory Supervisor Questions - Practice Answering Them!
Reading helps, but actual practice is what gets you hired. Our AI feedback system helps you improve your Factory Supervisor interview answers in real-time.
Personalized feedback
Unlimited practice
Used by hundreds of successful candidates
What would you do if you found out that a team member was not meeting their performance standards?
How to Answer
- 1
Assess the situation without jumping to conclusions
- 2
Communicate with the team member privately
- 3
Identify specific performance issues and seek their perspective
- 4
Offer support and resources to help improve performance
- 5
Set clear expectations and follow up regularly
Example Answers
I would first talk to the team member to understand their perspective on the performance issues. If they are facing challenges, I would offer my support and resources to help them succeed. Together, we would set clear goals and I would follow up regularly to monitor their progress.
If a new production line is introduced, how would you ensure that workers are trained efficiently?
How to Answer
- 1
Assess the specific skills required for the new production line
- 2
Develop a clear training program with step-by-step instructions
- 3
Utilize experienced workers to mentor and support new trainees
- 4
Implement hands-on training sessions to reinforce learning
- 5
Gather feedback and adjust the training program as necessary
Example Answers
I would first assess what skills are needed for the new production line, then create a structured training program. I would involve experienced workers to mentor new hires and use hands-on training to ensure they understand. Finally, I would collect feedback to continuously improve the training process.
How would you manage a disagreement between two team members about how to complete a task?
How to Answer
- 1
Listen to both team members' perspectives without bias.
- 2
Encourage a solution-focused discussion to explore different options.
- 3
Identify common goals and emphasize teamwork.
- 4
Facilitate a compromise by seeking input from both sides.
- 5
Make a decision based on the most effective approach for the team.
Example Answers
I would first listen to each team member to understand their viewpoints. Then, I would encourage them to discuss their ideas together, focusing on our common goal. If necessary, I would help them find a compromise that incorporates their best ideas.
If you observe unsafe behavior on the floor, what actions would you take?
How to Answer
- 1
Immediately address the unsafe behavior to ensure safety.
- 2
Gather information on the specific unsafe action observed.
- 3
Document the incident and actions taken for reference.
- 4
Report the behavior to higher management or safety officers.
- 5
Suggest training or safety improvements to prevent future incidents.
Example Answers
I would first intervene immediately to stop the unsafe behavior and ensure that no one is harmed. Then, I would gather details about what occurred and document it. After that, I'd report it to management so they can address any underlying issues.
How would you respond if a customer complained about defects in their order?
How to Answer
- 1
Acknowledge the customer's concern immediately
- 2
Apologize for the inconvenience caused
- 3
Ask for specific details about the defects
- 4
Explain how you will resolve the issue
- 5
Follow up with the customer to ensure satisfaction
Example Answers
I would thank the customer for bringing the issue to my attention, apologize for the inconvenience, and ask for specific details about the defect. Then I would assure them that I will investigate the matter and take corrective action to ensure it doesn't happen again.
If your department is facing a shortage of staff, how would you allocate resources to prioritize production?
How to Answer
- 1
Assess the critical production areas needing immediate attention
- 2
Identify which tasks can be temporarily paused or delegated
- 3
Communicate with your team to gather input and ensure transparency
- 4
Utilize flexible scheduling to maximize available workforce
- 5
Implement overtime or shift adjustments to meet demand
Example Answers
In a staff shortage, I would first evaluate production lines to identify which products have the highest demand. Then, I would reprioritize tasks, possibly delaying lower-priority work, and ask team members for their feedback on where they can best contribute during this period.
What steps would you take to analyze and optimize workflow in a bottleneck area?
How to Answer
- 1
Identify and map out the workflow process to locate the bottleneck clearly
- 2
Collect data on production metrics such as cycle time, wait time, and throughput
- 3
Engage with team members to gather insights and observations about the bottleneck
- 4
Experiment with solutions like reallocating resources or adjusting schedules and monitor changes
- 5
Review results regularly and make adjustments to continuously improve the workflow
Example Answers
First, I would map the entire workflow to identify exactly where the bottleneck occurs. Then, I would gather data on the production metrics associated with that area, such as the time it takes to complete tasks there. I would also talk to the team to get their insights. After analyzing this information, I would implement a trial solution and monitor its effectiveness over time.
How would you prepare your team for an emergency evacuation situation?
How to Answer
- 1
Conduct regular training sessions on emergency procedures.
- 2
Ensure all team members know evacuation routes and assembly points.
- 3
Assign specific roles to team members during an evacuation.
- 4
Keep emergency equipment accessible and in good condition.
- 5
Review and update the evacuation plan regularly based on feedback.
Example Answers
I would start by holding monthly training sessions to familiarize everyone with the emergency procedures. We would practice the evacuation routes and ensure everyone knows the assembly area outside.
Don't Just Read Factory Supervisor Questions - Practice Answering Them!
Reading helps, but actual practice is what gets you hired. Our AI feedback system helps you improve your Factory Supervisor interview answers in real-time.
Personalized feedback
Unlimited practice
Used by hundreds of successful candidates
How would you communicate with upper management about a significant production delay?
How to Answer
- 1
Prepare a clear brief outlining the reason for the delay
- 2
Provide specific data and metrics to support your explanation
- 3
Suggest potential solutions and a recovery plan
- 4
Maintain a professional and solution-oriented tone
- 5
Keep the communication concise and focused on key points
Example Answers
I would first prepare a brief report detailing the cause of the production delay, including specific data on affected timelines. I would also outline a recovery plan to minimize the impact on our overall production goals and share this with upper management promptly.
Factory Supervisor Position Details
Recommended Job Boards
CareerBuilder
www.careerbuilder.com/jobs-factory-supervisorZipRecruiter
www.ziprecruiter.com/Jobs/Factory-SupervisorThese job boards are ranked by relevance for this position.
Related Positions
Ace Your Next Interview!
Practice with AI feedback & get hired faster
Personalized feedback
Used by hundreds of successful candidates
Ace Your Next Interview!
Practice with AI feedback & get hired faster
Personalized feedback
Used by hundreds of successful candidates