Top 33 Quality Control Manager Interview Questions and Answers [Updated 2025]
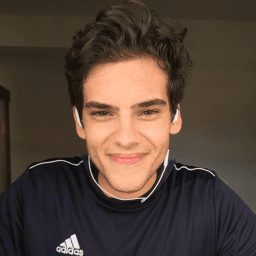
Andre Mendes
•
March 30, 2025
In the dynamic landscape of quality management, securing a role as a Quality Control Manager requires not only technical expertise but also the ability to articulate your skills and experience effectively. This blog post dives into the most common interview questions for this pivotal role, offering insightful example answers and practical tips to help you navigate your interview with confidence and poise. Get ready to enhance your interview skills and make a lasting impression.
Download Quality Control Manager Interview Questions in PDF
To make your preparation even more convenient, we've compiled all these top Quality Control Managerinterview questions and answers into a handy PDF.
Click the button below to download the PDF and have easy access to these essential questions anytime, anywhere:
List of Quality Control Manager Interview Questions
Behavioral Interview Questions
Describe a time when you led a team through a quality control challenge. What was your approach and what was the outcome?
How to Answer
- 1
Start with a specific situation you faced.
- 2
Explain the role you played in leading the team.
- 3
Describe the actions you took to address the quality issue.
- 4
Include specific tools or methodologies used, like Six Sigma or Root Cause Analysis.
- 5
Conclude with the results achieved and lessons learned.
Example Answers
In my last position, we noticed a recurring defect in our product line. I led a cross-functional team where we conducted a Root Cause Analysis to identify the issue. We implemented new inspection protocols and trained the staff. As a result, we reduced defects by 30% within three months.
Tell me about a time you identified a flaw in a production process. How did you address it?
How to Answer
- 1
Choose a specific example from your experience.
- 2
Clearly describe the flaw and its impact on production.
- 3
Explain the steps you took to investigate and address the flaw.
- 4
Highlight any collaboration with team members or departments.
- 5
Conclude with the results or improvements that followed your actions.
Example Answers
In my previous role, I noticed a recurring defect in a product that was traced back to a faulty machine calibration. I immediately conducted an inspection and found that the calibration settings were incorrect. I collaborated with the maintenance team to recalibrate the machine and instituted a weekly check to ensure accuracy. As a result, the defect rate dropped by 30%.
Don't Just Read Quality Control Manager Questions - Practice Answering Them!
Reading helps, but actual practice is what gets you hired. Our AI feedback system helps you improve your Quality Control Manager interview answers in real-time.
Personalized feedback
Unlimited practice
Used by hundreds of successful candidates
Have you ever had to mentor a team member who was struggling with quality control processes? How did you help them?
How to Answer
- 1
Identify the specific challenges the team member faced
- 2
Describe the steps you took to mentor and support them
- 3
Highlight any resources or tools you used in the mentoring process
- 4
Explain the outcome of the mentoring and any improvements seen
- 5
Share any feedback you received from the mentee on your support
Example Answers
I noticed a team member struggling with our inspection processes. I first sat down with them to understand their specific difficulties. Together, we reviewed the inspection checklist and I provided additional training sessions on our quality standards. After a few weeks, I saw a significant improvement in their performance and they expressed gratitude for the personalized support.
Can you give an example of how you collaborated with other departments to ensure product quality?
How to Answer
- 1
Identify the departments you collaborated with, such as production or R&D.
- 2
Describe the specific project or issue that required collaboration.
- 3
Explain your role in facilitating communication and cooperation.
- 4
Highlight the outcome or improvement in product quality due to teamwork.
- 5
Make it relatable to the potential challenges in quality control.
Example Answers
In my previous role, I collaborated closely with the production and R&D teams on a new product launch. My role involved organizing regular meetings to discuss quality metrics and feedback from the production line, which helped us identify design flaws early. As a result, we improved overall product quality and reduced returns by 15%.
Describe a situation where your efforts reduced defects in the final product. What measures did you take?
How to Answer
- 1
Select a specific project where you improved quality.
- 2
Explain the initial defect rate and the goal you aimed for.
- 3
Detail the steps you took to identify and fix the issues.
- 4
Quantify the results achieved after your measures.
- 5
Highlight any tools or techniques you used during the process.
Example Answers
In a project for a manufacturing line, we had a defect rate of 10%. I introduced a new inspection process using statistical sampling. This helped us identify the root causes of defects, leading to a reduction in defects to 2% over three months.
Tell me about a time you had to persuade management to invest in better quality control resources.
How to Answer
- 1
Use the STAR technique: Situation, Task, Action, Result.
- 2
Present clear data or examples that illustrate the need for better resources.
- 3
Emphasize the positive impact on quality and bottom line.
- 4
Be specific about what resources you proposed and why.
- 5
Show collaboration and how you involved stakeholders.
Example Answers
In my previous role, we had frequent quality issues that led to customer complaints. I gathered data showing that a 15% increase in our testing resources would reduce defects by 30%. After presenting a cost-benefit analysis and outlining the potential revenue savings, management agreed and we implemented the changes.
Can you provide an example of how you used feedback from quality audits to improve processes?
How to Answer
- 1
Identify a specific audit conducted.
- 2
Highlight the feedback received and its implications.
- 3
Describe the changes made to address the feedback.
- 4
Explain the positive outcomes from those changes.
- 5
Relate the improvements to overall quality goals.
Example Answers
During a recent quality audit, we found that our defect rate in production was higher than acceptable. The audit highlighted issues with our assembly procedures. We implemented new training sessions for assembly line workers. As a result, our defect rate dropped by 30% within three months, significantly improving product quality.
What is your proudest achievement in quality management? How did you achieve it?
How to Answer
- 1
Choose a specific achievement that had a significant impact.
- 2
Quantify the results of your achievement to showcase effectiveness.
- 3
Explain the steps you took to achieve this outcome.
- 4
Focus on your leadership and problem-solving skills.
- 5
Relate the achievement to the job you are applying for.
Example Answers
My proudest achievement was reducing product defects by 30% within a year. I achieved this by implementing a new quality tracking system and conducting regular training sessions for staff on quality standards.
Describe how you have implemented training programs to enhance the quality awareness of employees.
How to Answer
- 1
Identify specific training programs you developed or improved.
- 2
Provide examples of topics or skills covered in the training.
- 3
Discuss the methods used to engage employees during the training.
- 4
Highlight measurable outcomes or feedback from participants.
- 5
Mention any ongoing support or resources provided after the training.
Example Answers
At my last job, I created a quality awareness training program that included interactive workshops and e-learning modules focusing on quality standards and best practices. After the training, we saw a 20% decline in defects reported.
Don't Just Read Quality Control Manager Questions - Practice Answering Them!
Reading helps, but actual practice is what gets you hired. Our AI feedback system helps you improve your Quality Control Manager interview answers in real-time.
Personalized feedback
Unlimited practice
Used by hundreds of successful candidates
Tell me about a conflict you faced regarding quality standards and how you resolved it.
How to Answer
- 1
Identify a specific quality conflict you encountered.
- 2
Describe the stakeholders involved and their differing views.
- 3
Explain your approach to resolve the conflict, emphasizing communication.
- 4
Highlight the outcome and any improvements made post-resolution.
- 5
Consider including metrics or data to showcase success.
Example Answers
In my previous role, we faced a conflict when the production team wanted to use a new material that did not meet our quality standards. I organized a meeting with the production head and the quality assurance team to discuss the risks. By presenting data on past defects from that material, we agreed to conduct a controlled test first, which revealed significant issues. We ultimately decided against using the material, which improved our product quality.
Technical Interview Questions
What quality control standards are you familiar with, and how have you implemented them in your previous roles?
How to Answer
- 1
Identify specific quality control standards like ISO 9001 or Six Sigma.
- 2
Provide a specific example of a task or project where you applied these standards.
- 3
Discuss measurable results or improvements that came from implementing these standards.
- 4
Be clear about your role in the implementation process.
- 5
Connect the standards to the goals of the organization you worked for.
Example Answers
I am familiar with ISO 9001 and have implemented it in my previous role at XYZ Corp. I led a team to establish quality management procedures that resulted in a 20% reduction in defects over six months.
Can you explain how you would conduct a root cause analysis for a recurring quality issue?
How to Answer
- 1
Start by gathering data on the quality issue.
- 2
Identify and interview relevant stakeholders to gather insights.
- 3
Use tools like the 5 Whys or Fishbone Diagram to analyze causes.
- 4
Develop and test potential solutions to address the root cause.
- 5
Create a plan for monitoring the effectiveness of the solution.
Example Answers
I would begin by collecting all instances of the quality issue to find patterns. Then, I would interview the production team to understand their perspective, utilizing a Fishbone Diagram to categorize potential causes. After identifying the root cause, I would implement a corrective action and monitor its effect over time to ensure it resolves the issue.
Don't Just Read Quality Control Manager Questions - Practice Answering Them!
Reading helps, but actual practice is what gets you hired. Our AI feedback system helps you improve your Quality Control Manager interview answers in real-time.
Personalized feedback
Unlimited practice
Used by hundreds of successful candidates
What quality control tools and software have you used, and how have they improved your workflow?
How to Answer
- 1
Identify specific quality control tools and software you have experience with.
- 2
Explain how each tool improved efficiency or quality in your work.
- 3
Mention any metrics or outcomes that demonstrate the impact of these tools.
- 4
Be prepared to discuss how you trained others or implemented these tools in your team.
- 5
Use examples from recent roles to keep your answer relevant and fresh.
Example Answers
In my previous role, I used Minitab for statistical analysis, which helped us identify process variations. This resulted in a 15% reduction in defects over six months.
What key performance indicators (KPIs) do you consider essential for measuring quality performance?
How to Answer
- 1
Identify industry-specific KPIs relevant to quality control.
- 2
Explain why each KPI is important for measuring quality.
- 3
Use examples or scenarios to illustrate the impact of KPIs.
- 4
Be prepared to discuss how KPIs can guide decision-making.
- 5
Mention how you would track and report on these KPIs.
Example Answers
I believe essential KPIs for measuring quality performance include defect rates, process compliance rates, and customer satisfaction scores. Defect rates show the percentage of products failing quality checks, which directly impacts production efficiency. Process compliance rates help ensure that we adhere to our quality standards, while customer satisfaction scores indicate the effectiveness of quality management from the customer's perspective.
What is your experience with regulatory compliance related to quality control? Give specific examples.
How to Answer
- 1
Identify key regulations relevant to your industry.
- 2
Discuss specific projects where you ensured compliance.
- 3
Highlight tools and methodologies you used for compliance monitoring.
- 4
Mention any training or guidance you provided to staff.
- 5
Include measurable outcomes that demonstrate success.
Example Answers
In my previous role, I was responsible for ensuring compliance with ISO 9001 standards in our manufacturing processes. I conducted regular audits and implemented corrective actions when necessary, which led to a 30% reduction in non-conformities over a year.
What inspection techniques do you prefer for different stages of production?
How to Answer
- 1
Identify key stages in the production process: incoming materials, in-process, and finished goods.
- 2
Match inspection techniques to each stage: destructive testing for incoming materials, visual inspections during processes, and comprehensive testing for finished products.
- 3
Emphasize the importance of statistical quality control for ongoing monitoring.
- 4
Discuss the use of technology such as automated inspection systems or software for data analysis.
- 5
Highlight your experience with specific tools or techniques that improve efficiency and accuracy.
Example Answers
At the incoming materials stage, I prefer to use destructive testing to analyze the properties of raw materials. During the production phase, I implement visual inspections combined with automated systems to ensure quality. Finally, for finished products, I conduct comprehensive functional tests to verify they meet specifications.
What industry standards do you consider most important in your quality control practice?
How to Answer
- 1
Identify key quality standards relevant to your industry, such as ISO 9001 or Six Sigma.
- 2
Discuss how these standards ensure product quality and compliance.
- 3
Provide examples of how you've implemented these standards in previous roles.
- 4
Mention any certifications you hold related to quality management.
- 5
Emphasize the impact of these standards on customer satisfaction and operational efficiency.
Example Answers
In my previous role, I prioritized ISO 9001 as it provides a framework for consistently meeting customer requirements and enhancing satisfaction. I implemented regular audits and training sessions to ensure compliance, which significantly reduced product defects.
What types of testing methods are essential for ensuring product reliability?
How to Answer
- 1
Identify key testing methods relevant to your industry
- 2
Explain the purpose and benefits of each method
- 3
Provide examples of how you have used these methods in your experience
- 4
Mention any standards or frameworks that guide your testing
- 5
Highlight the importance of regular testing and updates based on results
Example Answers
In the electronics industry, we primarily use stress testing to assess reliability under extreme conditions, alongside functional testing to ensure each component performs as expected. I implemented these methods in my last project, which improved our product's durability by 30%.
How important is documentation in quality control, and what practices do you follow?
How to Answer
- 1
Emphasize the role of documentation in ensuring consistency and compliance.
- 2
Discuss how documentation aids in traceability and auditing processes.
- 3
Mention specific practices like SOPs, checklists, and quality reports.
- 4
Highlight the importance of training staff on documentation standards.
- 5
Include an example of how good documentation resolved an issue.
Example Answers
Documentation is fundamental in quality control as it ensures consistency and keeps us compliant with standards. I utilize standard operating procedures (SOPs) and checklists extensively, which help maintain quality across all processes. Regular training for the team on these documentation practices is crucial. For instance, when we faced a quality deviation, our detailed records helped us pinpoint the root cause quickly.
How do you stay updated with the latest trends and technologies in quality control?
How to Answer
- 1
Subscribe to leading quality control journals and publications for the latest research
- 2
Join professional organizations like ASQ for networking and resources
- 3
Attend industry conferences and workshops to learn about new tools
- 4
Follow quality control thought leaders on social media for insights
- 5
Participate in webinars and online courses to enhance your skills
Example Answers
I subscribe to quality control journals like the Journal of Quality in Maintenance Engineering and regularly attend webinars offered by ASQ. This helps me stay informed about the latest trends and technologies in the field.
Don't Just Read Quality Control Manager Questions - Practice Answering Them!
Reading helps, but actual practice is what gets you hired. Our AI feedback system helps you improve your Quality Control Manager interview answers in real-time.
Personalized feedback
Unlimited practice
Used by hundreds of successful candidates
What experience do you have with Six Sigma or Lean methodologies in quality control?
How to Answer
- 1
Highlight specific methodologies you have used.
- 2
Mention any certifications you hold related to Six Sigma or Lean.
- 3
Discuss a project where you applied these methodologies successfully.
- 4
Quantify results if possible to showcase impact.
- 5
Explain how you train or mentor others in these practices.
Example Answers
I am a certified Six Sigma Green Belt and have led multiple projects where I applied DMAIC principles. In one project, we reduced defects by 30%, which saved the company significant costs.
Situational Interview Questions
If two of your team members disagree on the best approach to a quality issue, how would you facilitate a resolution?
How to Answer
- 1
Listen to both perspectives without bias.
- 2
Encourage open dialogue between the team members.
- 3
Identify the key issues in the disagreement.
- 4
Facilitate a brainstorming session to explore solutions.
- 5
Lead the discussion towards consensus or a compromise.
Example Answers
I would first listen to both team members individually to understand their points of view. Then, I would bring them together to discuss their ideas openly, focusing on the facts. By identifying the key issues, we can brainstorm potential solutions together and find a compromise that addresses everyone's concerns.
If you identify a critical defect in a product just before it is scheduled for shipment, what steps would you take?
How to Answer
- 1
Immediately halt the shipment process to prevent defects from leaving the facility
- 2
Document the defect with detailed notes and evidence for further analysis
- 3
Communicate the issue to relevant stakeholders, including your team and management
- 4
Assess the impact of the defect on the product and decide on corrective actions
- 5
Implement the solutions and conduct thorough testing before resuming shipment
Example Answers
First, I would stop the shipment to ensure no defective products are sent out. Then, I would thoroughly document the defect and share my findings with my team and management. We would discuss the potential impacts and decide on an effective corrective action. Once we fix the issue, I would ensure the product is retested before any shipments resume.
Don't Just Read Quality Control Manager Questions - Practice Answering Them!
Reading helps, but actual practice is what gets you hired. Our AI feedback system helps you improve your Quality Control Manager interview answers in real-time.
Personalized feedback
Unlimited practice
Used by hundreds of successful candidates
Imagine you receive complaints from customers about product defects. How would you communicate this issue to your team?
How to Answer
- 1
Acknowledge the issue and emphasize its importance.
- 2
Gather all relevant data about the complaints.
- 3
Set up a team meeting to discuss the defects openly.
- 4
Encourage team input on potential solutions and improvements.
- 5
Follow up on action items and ensure accountability.
Example Answers
I would immediately acknowledge the customer complaints in a team meeting, present the specific data and trends from the complaints, and then open the floor for discussion on how we can address these defects collectively.
If you are overwhelmed with multiple quality issues, how would you prioritize which ones to address first?
How to Answer
- 1
Identify the impact of each issue on customer satisfaction and product safety
- 2
Evaluate the frequency of occurrence for each quality issue
- 3
Consider compliance with industry regulations and standards
- 4
Assess the resources available to address the issues
- 5
Consult with team members or stakeholders for input on prioritization
Example Answers
I would first look at the issues impacting customer safety and satisfaction the most. Next, I would prioritize issues based on how often they occur, focusing on frequent and critical issues. Lastly, I would bring the team together to discuss resource availability and get their insights on each issue's priority.
How would you approach evaluating a new vendor's quality control processes before engaging them?
How to Answer
- 1
Request the vendor's quality control documentation to review their processes.
- 2
Conduct an on-site audit to observe their quality control in action.
- 3
Ask for references from other clients to assess their past performance.
- 4
Evaluate their compliance with industry standards and certifications.
- 5
Discuss their corrective and preventive actions for past quality issues.
Example Answers
I would start by reviewing the vendor's quality control documentation to understand their processes. Then, I would conduct an on-site audit to see their quality control firsthand and gather insights. Additionally, I would ask for references from other clients and evaluate any relevant certifications they hold.
How would you foster a culture of quality within your team?
How to Answer
- 1
Communicate the importance of quality in every aspect of the work.
- 2
Implement regular training sessions to reinforce quality standards.
- 3
Encourage team feedback and suggestions for improvement.
- 4
Recognize and reward team members who exemplify quality focus.
- 5
Create clear processes and guidelines to minimize errors.
Example Answers
I would communicate the significance of quality at every team meeting and integrate quality metrics into our KPIs, ensuring everyone understands their role in maintaining high standards.
If you discover that a significant batch of products is defective, how would you develop an action plan?
How to Answer
- 1
Immediately assess the scope of the defect and the number of affected products.
- 2
Gather a cross-functional team to discuss the issue and identify root causes.
- 3
Develop corrective actions to address the defects and prevent recurrence.
- 4
Communicate transparently with stakeholders about the issue and your plan.
- 5
Implement the action plan and monitor results to ensure effectiveness.
Example Answers
First, I would quickly assess the affected batch to understand the extent of the defect. Then, I'd call a meeting with relevant team members from production, engineering, and QA to analyze root causes. After identifying the issue, we would draft corrective actions and communicate them clearly to management and customers, followed by implementing the plan and reviewing the outcomes.
If you discover unethical practices affecting product quality, how would you deal with the situation?
How to Answer
- 1
Identify and document the unethical practices clearly
- 2
Report the findings to your immediate supervisor or quality oversight committee
- 3
Follow company policies on ethical concerns and escalate if necessary
- 4
Suggest corrective actions and preventive measures
- 5
Ensure that your approach prioritizes integrity and company standards
Example Answers
If I discover unethical practices, I will first document everything in detail. I'll report my findings to my supervisor immediately, following our company’s ethical guidelines. I will also suggest specific corrective actions to prevent future occurrences.
In a scenario where a product recall is necessary, how would you manage communications with stakeholders?
How to Answer
- 1
Identify key stakeholders such as customers, suppliers, and regulatory bodies.
- 2
Prepare a clear and concise message about the recall situation.
- 3
Establish a communication timeline and stick to it to keep stakeholders informed.
- 4
Designate a spokesperson to ensure consistent messaging.
- 5
Set up a feedback mechanism to address stakeholder concerns and queries.
Example Answers
I would first identify all key stakeholders, including customers and suppliers. Then, I would prepare a straightforward message explaining the recall and what steps we are taking. I would set a timeline for updates and ensure a designated spokesperson communicates with everyone consistently. Finally, I would implement a system for stakeholders to voice their concerns.
If a new quality issue arises with a product that had previously passed inspections, how would you investigate it?
How to Answer
- 1
Review inspection records to identify passed criteria and understand the quality checks performed.
- 2
Gather a cross-functional team including production, engineering, and quality assurance for diverse insights.
- 3
Conduct a root cause analysis using techniques like the 5 Whys or Fishbone Diagram.
- 4
Test and analyze samples of the defective product to replicate and understand the issue.
- 5
Implement corrective actions and monitor the results to prevent recurrence.
Example Answers
I would first review the inspection records to determine what criteria the product passed. Then, I would involve a cross-functional team to share insights. Using a root cause analysis, we would identify the underlying issue and replicate it with defective samples before implementing corrective actions.
Don't Just Read Quality Control Manager Questions - Practice Answering Them!
Reading helps, but actual practice is what gets you hired. Our AI feedback system helps you improve your Quality Control Manager interview answers in real-time.
Personalized feedback
Unlimited practice
Used by hundreds of successful candidates
How would you integrate sustainable practices into your quality management systems?
How to Answer
- 1
Assess current quality management processes for environmental impact
- 2
Incorporate sustainability metrics in quality criteria
- 3
Train staff on sustainable practices and their importance in quality control
- 4
Establish a feedback loop for continuous improvement focused on sustainability
- 5
Collaborate with suppliers to ensure sustainable materials and processes
Example Answers
To integrate sustainable practices, I would first evaluate our existing QC processes to identify any areas with environmental impact. Then, I would define specific sustainability metrics to include in our quality control criteria. Training staff on these practices would ensure everyone is aligned on sustainability's role in quality management.
Quality Control Manager Position Details
Salary Information
Recommended Job Boards
CareerBuilder
www.careerbuilder.com/jobs-quality-control-managerThese job boards are ranked by relevance for this position.
Related Positions
Ace Your Next Interview!
Practice with AI feedback & get hired faster
Personalized feedback
Used by hundreds of successful candidates
Ace Your Next Interview!
Practice with AI feedback & get hired faster
Personalized feedback
Used by hundreds of successful candidates