Top 30 Instrument Worker Interview Questions and Answers [Updated 2025]
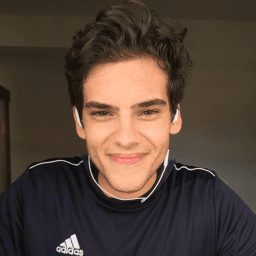
Andre Mendes
•
March 30, 2025
Preparing for an interview as an Instrument Worker? Our comprehensive guide has you covered with the most common interview questions you might encounter. Dive into expertly crafted example answers and insightful tips on how to respond effectively, ensuring you make a lasting impression. Whether you're a seasoned professional or new to the field, this post will help you confidently navigate your next interview.
Download Instrument Worker Interview Questions in PDF
To make your preparation even more convenient, we've compiled all these top Instrument Workerinterview questions and answers into a handy PDF.
Click the button below to download the PDF and have easy access to these essential questions anytime, anywhere:
List of Instrument Worker Interview Questions
Technical Interview Questions
Explain the different types of sensors you have worked with and their applications in the field.
How to Answer
- 1
Identify key sensor types you have experience with, such as temperature, pressure, flow, etc.
- 2
Explain their specific applications in your past work or projects.
- 3
Use clear and concise language to describe how each sensor works.
- 4
Mention any brands or models you are familiar with to demonstrate expertise.
- 5
Relate your experience to the job role and how it can benefit the employer.
Example Answers
I have worked extensively with temperature sensors like thermocouples and RTDs, which are critical for monitoring process temperatures in a chemical plant. Their accuracy is essential for safety and efficiency.
What are the procedures you follow for calibrating an instrument? Can you explain your process?
How to Answer
- 1
Start by explaining the importance of calibration for accuracy and reliability.
- 2
Describe the specific instruments you have calibrated and mention relevant standards.
- 3
Outline your process step by step, including preparation, adjustment, and verification.
- 4
Mention tools and equipment used during calibration.
- 5
Conclude with how you document the results and ensure compliance.
Example Answers
I first review the manufacturer's specifications and the calibration standards required. For example, when calibrating a pressure sensor, I ensure it’s cleaned and properly connected. Next, I use a reference instrument to compare readings and make adjustments if necessary. Finally, I record the calibration results in our system and verify the instrument's performance post-calibration.
Good Candidates Answer Questions. Great Ones Win Offers.
Reading sample answers isn't enough. Top candidates practice speaking with confidence and clarity. Get real feedback, improve faster, and walk into your next interview ready to stand out.
Master your interview answers under pressure
Boost your confidence with real-time practice
Speak clearly and impress hiring managers
Get hired faster with focused preparation
Used by hundreds of successful candidates
What instrumentation standards and regulations are you familiar with?
How to Answer
- 1
Identify key standards relevant to instrumentation like ISA, IEC, and ISO.
- 2
Mention any specific regulations you have worked with such as OSHA or EPA.
- 3
Explain your experience with standard operating procedures or compliance inspections.
- 4
Highlight familiarity with industry-specific standards like those in oil and gas or pharmaceuticals.
- 5
Be prepared to provide examples of how you've applied these standards in previous roles.
Example Answers
I am familiar with ISA 5.1 for instrument symbols and IEC 61508 for functional safety. In my previous role, I ensured compliance with OSHA regulations during equipment installations.
How do you perform diagnostics on electronic instruments? What tools do you use?
How to Answer
- 1
Explain your diagnostic process step-by-step.
- 2
Mention specific tools you commonly use.
- 3
Provide examples of issues you've diagnosed successfully.
- 4
Discuss how you ensure accuracy in your diagnostics.
- 5
Highlight your experience with both hardware and software diagnostics.
Example Answers
I start diagnostics by visually inspecting connections and components. I typically use a multimeter for voltage and continuity tests, and I might also use an oscilloscope for more complex signals. Recently, I diagnosed a faulty sensor by monitoring its output with these tools, which helped me identify a wiring issue.
Are you comfortable reading and interpreting electrical schematics? Can you provide an example?
How to Answer
- 1
Start by affirming your comfort with electrical schematics.
- 2
Mention any formal training or relevant experience you have.
- 3
Provide a specific example where you successfully interpreted a schematic.
- 4
Explain the significance of that interpretation in your work.
- 5
Conclude with how it helped you solve a problem or improve a process.
Example Answers
Yes, I am very comfortable reading and interpreting electrical schematics. In my previous role, I worked on a project where I had to read a complex wiring diagram to troubleshoot a malfunctioning circuit. By analyzing the schematic, I identified a faulty connection that was causing the issue, leading to a quick resolution and improved system performance.
How do you ensure instruments are calibrated according to industry standards?
How to Answer
- 1
Familiarize yourself with the relevant industry standards for calibration.
- 2
Document the calibration process and keep a maintenance log.
- 3
Use certified calibration equipment and check its validity.
- 4
Schedule regular calibration checks based on manufacturer recommendations.
- 5
Stay updated on any changes in standards and ensure compliance.
Example Answers
I ensure instruments are calibrated by strictly following industry standards like ISO 17025, documenting every calibration in a maintenance log, and scheduling checks regularly based on the manufacturer's guidelines.
What software tools are you proficient in for instrument management and data analysis?
How to Answer
- 1
Identify key software tools used in the industry such as DCS, SCADA, and data analysis software.
- 2
Mention specific versions or types of software you have experience with.
- 3
Provide examples of how you used these tools in previous roles.
- 4
Highlight any certifications or training you have related to these tools.
- 5
Be prepared to discuss the impact of using these tools on project outcomes.
Example Answers
I am proficient in software like Honeywell's DCS for instrument control and MindSphere for data analysis. In my previous role, I utilized DCS to streamline monitoring processes, which improved efficiency by 20%.
What is your approach to troubleshooting issues with control systems?
How to Answer
- 1
Begin by gathering information on the issue from users and logs
- 2
Check for obvious signs like alarms or error messages
- 3
Isolate the components of the control system to identify the faulty part
- 4
Test the system step by step to replicate the issue
- 5
Document your findings and solutions for future reference
Example Answers
I start by collecting as much information as possible from users and the system logs. Then I check for any alarms or error messages displayed. After that, I isolate different components to pinpoint where the problem lies. Once I can replicate the issue, I perform tests to validate my findings, and finally, I document everything for future reference.
What routine maintenance tasks do you believe are essential for instrumentation?
How to Answer
- 1
Identify key instruments and their specific maintenance needs
- 2
Discuss calibration checks and their frequency
- 3
Mention the importance of cleaning and inspection tasks
- 4
Talk about documentation and record-keeping for maintenance
- 5
Highlight the role of troubleshooting and identifying issues early
Example Answers
Routine maintenance for instrumentation includes regular calibration checks every month, cleaning sensors, and ensuring all connections are tight and free from corrosion.
What is your experience with pneumatic instruments? Can you share specific applications?
How to Answer
- 1
Start by describing your overall experience with pneumatic instruments.
- 2
Mention specific types of pneumatic instruments you have worked with.
- 3
Include examples of applications where you used these instruments.
- 4
Discuss any troubleshooting or maintenance you performed.
- 5
Highlight any relevant training or certifications related to pneumatic systems.
Example Answers
I have over 5 years of experience working with pneumatic instruments, specifically in the installation and maintenance of air compressors and actuators. One application was in a manufacturing plant where I used pneumatic valves to control pressurization in production lines. I also performed regular maintenance and troubleshooting on these systems, ensuring they operated efficiently.
Good Candidates Answer Questions. Great Ones Win Offers.
Reading sample answers isn't enough. Top candidates practice speaking with confidence and clarity. Get real feedback, improve faster, and walk into your next interview ready to stand out.
Master your interview answers under pressure
Boost your confidence with real-time practice
Speak clearly and impress hiring managers
Get hired faster with focused preparation
Used by hundreds of successful candidates
What safety protocols do you always follow when working with instruments?
How to Answer
- 1
Always wear appropriate PPE such as gloves and safety glasses.
- 2
Ensure that all instruments are calibrated and in good working condition before use.
- 3
Follow lockout/tagout procedures when maintaining equipment.
- 4
Be aware of your surroundings and any potential hazards.
- 5
Document any safety incidents or near misses immediately.
Example Answers
I always wear gloves and safety glasses when handling instruments to protect myself from hazardous materials.
Behavioral Interview Questions
Can you describe a time when you had to troubleshoot an instrument failure? What steps did you take?
How to Answer
- 1
Choose a real example from your experience.
- 2
Clearly outline the instrument and its failure.
- 3
Explain the troubleshooting steps you followed.
- 4
Highlight the outcome and any lessons learned.
- 5
Keep your answer focused and structured.
Example Answers
In my previous job, the pressure sensor in a gas pipeline failed. I inspected the calibration settings and discovered the sensor's output was inconsistent. I replaced the faulty sensor and recalibrated the system, restoring normal operations. This experience taught me the importance of regular maintenance checks.
Good Candidates Answer Questions. Great Ones Win Offers.
Reading sample answers isn't enough. Top candidates practice speaking with confidence and clarity. Get real feedback, improve faster, and walk into your next interview ready to stand out.
Master your interview answers under pressure
Boost your confidence with real-time practice
Speak clearly and impress hiring managers
Get hired faster with focused preparation
Used by hundreds of successful candidates
Tell me about a situation when you had to learn a new tool or technology to complete your job. How did you approach it?
How to Answer
- 1
Identify the tool or technology you learned and why it was necessary.
- 2
Explain your learning process: did you study manuals, take courses, or seek help?
- 3
Describe any challenges you faced during the learning phase.
- 4
Mention how your new knowledge positively impacted your job performance.
- 5
Conclude with what you learned about adapting to new tools.
Example Answers
In my previous role, I needed to learn PLC programming to troubleshoot a machine issue. I started by reviewing the manufacturer's manual, then took an online course to grasp the basics. A challenge was understanding the specific coding structure, but I reached out to a colleague for help. As a result, I reduced downtime by 30% and felt more confident in handling similar tasks.
Describe a time when you took the lead on an instrumentation issue. What was the outcome?
How to Answer
- 1
Identify a clear situation where you led a project or resolved an issue.
- 2
Explain the instrumentation problem you faced and its impact.
- 3
Describe specific actions you took to lead the resolution.
- 4
Highlight collaboration with team members or stakeholders.
- 5
Conclude with the positive outcome and any lessons learned.
Example Answers
In my previous role, we faced a malfunction in our gas detection system that could have halted production. I organized a team to diagnose the issue, led troubleshooting efforts, and coordinated with vendors for quick parts replacement. We resolved the issue in two days, minimizing downtime and enhancing system reliability.
Give an example of a conflict with a coworker regarding instrumentation tasks. How did you handle it?
How to Answer
- 1
Identify a specific conflict related to instrumentation.
- 2
Describe your role and the other person's perspective.
- 3
Explain your approach to resolving the issue.
- 4
Emphasize communication and collaboration.
- 5
Conclude with the outcome and what you learned.
Example Answers
In my previous job, I disagreed with a coworker about the calibration method for a pressure transmitter. They preferred a manual method while I believed an automated approach would be more efficient. I suggested we try both methods on a trial basis to compare results. After our tests, we found the automated method saved time and improved accuracy, so we adopted it as a team.
Can you give an example of how you received constructive criticism at work? How did you respond?
How to Answer
- 1
Pick a specific instance where you received feedback.
- 2
Explain the nature of the criticism and why it was important.
- 3
Describe how you implemented the feedback in your work.
- 4
Reflect on the outcome or what you learned from the experience.
- 5
Keep your response focused and to the point.
Example Answers
In my previous job as an Instrument Technician, my supervisor pointed out that I needed to improve my documentation accuracy. I took this seriously, so I started double-checking my records against the instrument calibration logs. This not only improved my documentation but also enhanced my attention to detail, which led to better team communication.
Tell me about a time when you identified a problem before anyone else did and took action. What was the result?
How to Answer
- 1
Use the STAR method: Situation, Task, Action, Result.
- 2
Focus on a specific instance in your previous roles.
- 3
Highlight your observations and analytical skills.
- 4
Emphasize the actions you took and their impact.
- 5
Conclude with a positive outcome or lesson learned.
Example Answers
In my last position as an Instrument Technician, I noticed that a particular gauge was giving inconsistent readings. I investigated and found that it was due to faulty wiring. I reported this to my supervisor, and we replaced the wiring, which improved device accuracy and prevented a potential operational failure.
Describe an instance where you had to update your skills or knowledge on instrumentation. How did you go about it?
How to Answer
- 1
Explain the context of the situation clearly
- 2
Mention a specific skill or knowledge area you updated
- 3
Describe the resources you used to learn (courses, manuals, etc.)
- 4
Highlight any practical application of your new skills
- 5
Reflect on how this improvement benefited your work
Example Answers
In my previous job, we transitioned from analog to digital instrumentation systems. I recognized the need to update my skills, so I enrolled in an online course about digital sensors and control systems. I applied what I learned by successfully migrating our monitoring system, which improved accuracy and response time by 20%.
Situational Interview Questions
If you discovered a malfunctioning instrument during a critical operation, what steps would you take to address the issue immediately?
How to Answer
- 1
Prioritize safety for yourself and others in the area
- 2
Assess the extent of the malfunction quickly
- 3
Communicate the issue to your team and supervisors immediately
- 4
Implement a temporary workaround if safe and possible
- 5
Document the malfunction for future analysis and reporting
Example Answers
First, I would ensure everyone's safety by shutting down non-essential operations. Then, I would examine the instrument to determine the issue and let my team know about the malfunction promptly. If possible, I would implement a temporary workaround while waiting for a qualified technician.
How would you prioritize multiple instrumentation tasks with tight deadlines?
How to Answer
- 1
List all tasks and their deadlines
- 2
Evaluate the impact of each task on overall operations
- 3
Communicate with team members to understand urgency
- 4
Use a prioritization matrix if needed
- 5
Stay flexible and ready to adjust priorities
Example Answers
I would start by listing all instrumentation tasks and their respective deadlines. Then, I would assess which tasks have the greatest impact on our operations and communicate with my team to clarify urgencies. This helps ensure that my priorities align with team goals.
Good Candidates Answer Questions. Great Ones Win Offers.
Reading sample answers isn't enough. Top candidates practice speaking with confidence and clarity. Get real feedback, improve faster, and walk into your next interview ready to stand out.
Master your interview answers under pressure
Boost your confidence with real-time practice
Speak clearly and impress hiring managers
Get hired faster with focused preparation
Used by hundreds of successful candidates
Imagine you have a new team member who needs to learn about instrument setup. How would you train them?
How to Answer
- 1
Start with a clear overview of the instrument and its purpose
- 2
Demonstrate the setup process step-by-step
- 3
Encourage hands-on practice while supervising
- 4
Provide resources for further reading or videos
- 5
Schedule regular follow-up sessions to address questions
Example Answers
I would begin by explaining the instrument's purpose and how it fits into our workflow. Then, I would demonstrate the setup process and allow the new team member to try it themselves while I supervise.
What would you do if a key instrument fails during an important test? Outline your response plan.
How to Answer
- 1
Stay calm and assess the situation quickly.
- 2
Check backup instruments or alternative methods for measurement.
- 3
Notify your supervisor and relevant team members immediately.
- 4
Document the failure and any actions taken.
- 5
Implement a temporary solution if possible while aiming for a permanent fix.
Example Answers
If a key instrument fails, I would first stay calm and quickly assess the issue. I would check if we have a backup instrument or an alternative tool available. Next, I would inform my supervisor about the failure and update the team. I would document the incident and what steps I took, and if possible, I'd implement a temporary solution to keep testing moving forward.
How would you approach a situation where the instrumentation budget is cut? What solutions would you propose?
How to Answer
- 1
Evaluate the critical needs of the instrumentation and prioritize them.
- 2
Seek alternative funding sources or cost-sharing with other departments.
- 3
Propose a phased or scaled implementation of projects to spread costs over time.
- 4
Encourage teamwork to identify cost-saving measures without compromising quality.
- 5
Communicate openly with stakeholders about the impact of budget cuts and propose realistic solutions.
Example Answers
In a situation where the instrumentation budget is cut, I would first assess which projects are critical and which can be deferred. Then, I'd look for alternative funding or partnerships with other departments to share costs. Additionally, I might propose implementing expensive projects in phases to manage cash flow more effectively.
If you noticed that an instrument's readings were consistently off, what steps would you take to ensure data accuracy?
How to Answer
- 1
Verify the calibration of the instrument
- 2
Check for any physical damage or obstruction
- 3
Review the data collection process for any errors
- 4
Consult the technical manual for troubleshooting steps
- 5
Document findings and take corrective action if necessary
Example Answers
I would first verify if the instrument is calibrated correctly. If it’s not, I would recalibrate it according to the manufacturer’s guidelines. I would also check for any obstructions or physical damage that may affect readings.
How would you handle incomplete documentation for an instrument setup? What actions would you take?
How to Answer
- 1
Identify the missing information clearly.
- 2
Communicate with team members involved in the setup.
- 3
Refer to standard procedures or previous setups for guidance.
- 4
Document any discrepancies for future reference.
- 5
Ensure compliance with safety and operational regulations.
Example Answers
I would first identify exactly what information is missing from the documentation. Then, I would reach out to the team members who were involved in the setup to gather any details they might have. If necessary, I would consult previous setups or standard operating procedures to fill in the gaps. I would also document the incomplete areas to ensure we have a record of what was missing for future reference.
How would you work with other departments to solve a complex instrumentation issue that affects multiple teams?
How to Answer
- 1
Identify the key departments involved in the issue
- 2
Initiate open communication to gather insights and concerns
- 3
Propose a collaborative meeting to discuss the problem
- 4
Facilitate brainstorming sessions to explore solutions
- 5
Document the agreed action plan and follow up regularly
Example Answers
I would first identify which departments are impacted by the instrumentation issue. Then, I would set up a meeting with representatives from each team to understand their perspectives. During the meeting, I would encourage brainstorming to come up with potential solutions, and ensure we document our action plan for follow-up.
If you found a more efficient method for instrumentation setup, how would you propose it to your supervisor?
How to Answer
- 1
Identify the key benefits of the new method clearly.
- 2
Prepare a brief presentation or summary with supporting data.
- 3
Suggest a trial implementation period to test the new method.
- 4
Be open to feedback and ready to discuss concerns.
- 5
Schedule a formal meeting to discuss your proposal.
Example Answers
I would first outline the key benefits like time savings and increased accuracy. Then, I'd prepare a summary of my findings and propose a trial period to test the method. I'd make sure to be receptive to feedback from my supervisor.
You receive conflicting data from two instruments measuring the same parameter. Describe your next steps.
How to Answer
- 1
Identify the instruments and confirm their calibration status.
- 2
Evaluate the measurement conditions and determine if any external factors could affect the readings.
- 3
Consult the technical documentation for both instruments to understand their operational limits.
- 4
Cross-check the readings against a reliable reference or standard measurement if available.
- 5
Communicate with your team or supervisor about the discrepancy and seek their input.
Example Answers
First, I would check both instruments to ensure they are calibrated correctly. Then, I would consider any external factors that might affect the readings. If needed, I'd look at the technical specifications and possibly compare them against a known standard.
Good Candidates Answer Questions. Great Ones Win Offers.
Reading sample answers isn't enough. Top candidates practice speaking with confidence and clarity. Get real feedback, improve faster, and walk into your next interview ready to stand out.
Master your interview answers under pressure
Boost your confidence with real-time practice
Speak clearly and impress hiring managers
Get hired faster with focused preparation
Used by hundreds of successful candidates
Instrument Worker Position Details
Recommended Job Boards
CareerBuilder
www.careerbuilder.com/jobs/instrument-workerZipRecruiter
www.ziprecruiter.com/Jobs/-Instrument-WorkerThese job boards are ranked by relevance for this position.
Related Positions
Good Candidates Answer Questions. Great Ones Win Offers.
Master your interview answers under pressure
Boost your confidence with real-time practice
Speak clearly and impress hiring managers
Get hired faster with focused preparation
Used by hundreds of successful candidates
Good Candidates Answer Questions. Great Ones Win Offers.
Master your interview answers under pressure
Boost your confidence with real-time practice
Speak clearly and impress hiring managers
Get hired faster with focused preparation
Used by hundreds of successful candidates