Top 31 Instrument Technician Apprentice Interview Questions and Answers [Updated 2025]
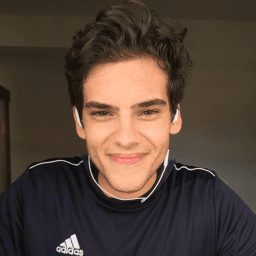
Andre Mendes
•
March 30, 2025
Preparing for an Instrument Technician Apprentice interview can be daunting, but with the right guidance, you can confidently tackle the most common questions in the field. This blog post is your comprehensive guide to mastering the interview process, offering insightful example answers and practical tips to help you respond effectively. Get ready to impress your interviewers and secure your apprenticeship with these essential strategies and insights.
Download Instrument Technician Apprentice Interview Questions in PDF
To make your preparation even more convenient, we've compiled all these top Instrument Technician Apprenticeinterview questions and answers into a handy PDF.
Click the button below to download the PDF and have easy access to these essential questions anytime, anywhere:
List of Instrument Technician Apprentice Interview Questions
Behavioral Interview Questions
Can you provide an example of a time when you worked successfully in a team to accomplish a technical task?
How to Answer
- 1
Choose a specific project or task involving teamwork.
- 2
Briefly describe your role in the team.
- 3
Highlight the technical challenge you faced together.
- 4
Explain how you collaborated and communicated.
- 5
Mention the outcome and what you learned from the experience.
Example Answers
During my last semester in school, I worked on a team project to design a control system for a robotics competition. I was responsible for programming the sensors and ensuring they communicated with the main controller. We faced challenges with sensor calibration, but through regular meetings and troubleshooting sessions, we resolved the issues and successfully built a functioning robot that won the competition. I learned the importance of clear communication in a team.
Describe a situation where you encountered a technical problem. How did you solve it?
How to Answer
- 1
Identify a specific technical problem you faced.
- 2
Explain the steps you took to analyze and understand the issue.
- 3
Discuss the solution you implemented and why it was effective.
- 4
Mention any tools or resources you used to assist in solving the problem.
- 5
Highlight any lessons learned from the experience that you apply in future situations.
Example Answers
During my internship, I noticed a pressure gauge was faulty and showing inconsistent readings. I assessed the wiring and discovered loose connections, which I repaired. After fixing the connections, the gauge began working properly, and I learned to always check wiring first when dealing with electronic issues.
Don't Just Read Instrument Technician Apprentice Questions - Practice Answering Them!
Reading helps, but actual practice is what gets you hired. Our AI feedback system helps you improve your Instrument Technician Apprentice interview answers in real-time.
Personalized feedback
Unlimited practice
Used by hundreds of successful candidates
Have you ever had a disagreement with a colleague regarding a technical approach? How did you handle it?
How to Answer
- 1
Stay calm and professional throughout the disagreement.
- 2
Listen to your colleague's perspective fully before responding.
- 3
Clearly explain your viewpoint with supporting details.
- 4
Seek common ground or a compromise if possible.
- 5
Follow up to ensure the issue is resolved and both parties are satisfied.
Example Answers
Yes, I had a disagreement with a colleague about the method to calibrate a pressure sensor. I listened to his reasoning and then shared my approach based on the manufacturer's specifications. We decided to test both methods, and ultimately chose the one that provided the best accuracy.
Tell me about a time when you had to learn a new skill or technique quickly. What steps did you take?
How to Answer
- 1
Choose a specific skill relevant to instrumentation or your previous experience
- 2
Use the STAR method: Situation, Task, Action, Result
- 3
Emphasize your ability to adapt and learn under pressure
- 4
Mention any resources or support you utilized
- 5
Conclude with the positive outcome or what you gained from the experience
Example Answers
During my last job, we had a last-minute request to calibrate a new type of sensor. I quickly researched the calibration procedure, watched an instructional video, and practiced with a colleague. As a result, we completed the task ahead of schedule and ensured accuracy in our measurements.
Give an example of how you adapted to a significant change in a project or workplace.
How to Answer
- 1
Identify the change clearly and briefly.
- 2
Describe your initial reaction and feelings about the change.
- 3
Explain the actions you took to adapt to the change.
- 4
Discuss the outcome or result of your adaptation.
- 5
Reflect on what you learned from the experience.
Example Answers
In my previous job, our team switched from analog to digital equipment. At first, I was overwhelmed by the new technology, but I took online courses to learn the software needed. After a week, I was able to assist my team and help others with the transition, resulting in a smoother workflow.
Describe a time when you took the initiative to improve a process or system in your previous work or studies.
How to Answer
- 1
Think of a specific example related to your previous role or studies
- 2
Explain the problem you identified and why it needed improvement
- 3
Describe the action you took to make the improvement
- 4
Highlight the positive outcome resulting from your initiative
- 5
Use clear and concise language to convey your points
Example Answers
In my last job as a lab assistant, I noticed that our data entry process was prone to errors and took too much time. I proposed a digital tracking system using a spreadsheet, which automated calculations. This reduced data entry errors by 30% and saved hours each week.
Can you give an example of how you handled feedback from a supervisor on your work?
How to Answer
- 1
Choose a specific instance where you received feedback.
- 2
Explain your initial reaction to the feedback.
- 3
Describe the actions you took in response to the feedback.
- 4
Share the outcome or what you learned from the experience.
- 5
Emphasize your willingness to grow and learn from feedback.
Example Answers
In my last job, my supervisor pointed out that my wiring on a project was not neat. Initially, I felt a bit defensive, but I listened carefully. I then researched best practices for cable management and took on a small project to practice. The next time I worked on wiring, I applied those techniques and received positive feedback.
How do you manage your time when you have multiple tasks to complete?
How to Answer
- 1
Prioritize tasks based on their deadlines and importance
- 2
Break larger tasks into smaller, manageable steps
- 3
Use a planner or digital tool to keep track of your tasks
- 4
Set specific time blocks for focused work on each task
- 5
Review and adjust your plan as needed throughout the day
Example Answers
I prioritize my tasks by deadlines and importance. I use a planner to list everything and break larger tasks into smaller steps. This helps me stay on track and manage my time effectively.
Describe a time when a project you were involved in did not go as planned. What did you learn?
How to Answer
- 1
Choose a specific project with clear outcomes.
- 2
Explain the initial plan and what went wrong.
- 3
Focus on your personal contribution and actions.
- 4
Discuss what you learned and how it changed your approach.
- 5
Keep it positive and emphasize growth.
Example Answers
During a school project on instrumentation calibration, we underestimated the time required for testing. We ended up rushing and missed some critical validations. I learned the importance of thorough planning and time management. Now, I always include buffer time in my schedules.
What motivates you to pursue a career as an Instrument Technician?
How to Answer
- 1
Identify your interest in technology and instrumentation.
- 2
Share a personal story or experience related to the field.
- 3
Emphasize your desire for hands-on work and problem-solving.
- 4
Discuss the importance of precision and safety in the role.
- 5
Mention your long-term career goals in the industry.
Example Answers
I have always been fascinated by technology and how it works. In high school, I really enjoyed my electronics class where we built circuits. I love hands-on work and figuring out how to solve problems, which I believe is key for an Instrument Technician.
Don't Just Read Instrument Technician Apprentice Questions - Practice Answering Them!
Reading helps, but actual practice is what gets you hired. Our AI feedback system helps you improve your Instrument Technician Apprentice interview answers in real-time.
Personalized feedback
Unlimited practice
Used by hundreds of successful candidates
Technical Interview Questions
What are the basic principles of operation for common types of measurement instruments?
How to Answer
- 1
Identify common measurement instruments like thermocouples, pressure gauges, and flow meters
- 2
Explain the basic operating principle of each instrument clearly and concisely
- 3
Use specific examples to illustrate your points
- 4
Keep your answers structured: define the instrument, explain the principle, and mention applications
- 5
Be prepared to discuss advantages and limitations of these instruments
Example Answers
Thermocouples are based on the thermoelectric effect, where a voltage is generated at the junction of two different metals and this voltage correlates with temperature. They are widely used in temperature measurement.
Explain the process of calibrating a sensor. Why is it important?
How to Answer
- 1
Start with a clear definition of calibration.
- 2
Outline the steps involved in the calibration process.
- 3
Discuss the importance of calibration in ensuring accurate measurements.
- 4
Mention potential consequences of not calibrating.
- 5
Conclude with an example of a sensor that requires regular calibration.
Example Answers
Calibration is adjusting a sensor to ensure its readings are accurate. The process involves comparing the sensor's output to a known standard and making adjustments as necessary. It's important because accurate measurements ensure safety and efficiency in processes. Without calibration, sensors can give false readings, leading to errors in operations. For example, temperature sensors in industrial settings need regular calibration to maintain reliability.
Don't Just Read Instrument Technician Apprentice Questions - Practice Answering Them!
Reading helps, but actual practice is what gets you hired. Our AI feedback system helps you improve your Instrument Technician Apprentice interview answers in real-time.
Personalized feedback
Unlimited practice
Used by hundreds of successful candidates
What safety measures should you take when working with electrical instruments?
How to Answer
- 1
Always wear appropriate personal protective equipment such as gloves and safety goggles.
- 2
Ensure that all tools and instruments are properly insulated and in good condition before use.
- 3
Disconnect power sources before servicing or working on any electrical instruments.
- 4
Use lockout/tagout procedures to prevent accidental re-energization of equipment.
- 5
Be aware of your surroundings and ensure the workspace is dry and clear of obstacles.
Example Answers
I prioritize safety by wearing gloves and goggles, checking my tools for insulation, and disconnecting power sources before I start any work.
Describe the steps you would take to troubleshoot a malfunctioning instrument.
How to Answer
- 1
Identify the symptoms and gather information about the malfunction.
- 2
Check for power supply issues and ensure the instrument is properly powered.
- 3
Inspect connections and ensure all wiring is intact and properly connected.
- 4
Use diagnostic tools such as multimeters or calibration equipment to test the instrument.
- 5
Consult equipment manuals or schematics for specific troubleshooting procedures.
Example Answers
First, I would gather any information on the symptoms, such as error messages. Then, I'd check the power supply to ensure the instrument is receiving the needed voltage. Next, I'd inspect all connections to make sure nothing is loose or damaged. I would then use a multimeter to test important points in the circuit, and finally consult the manual for detailed troubleshooting guidance.
What industry standards are relevant to instrumentation? Can you name a few?
How to Answer
- 1
Familiarize yourself with key standards such as ISA, IEC, and ANSI.
- 2
Mention specific standards like ISA-5.1 for instrumentation symbols.
- 3
Include safety and quality standards relevant to the field.
- 4
Demonstrate understanding of how these standards impact daily operations.
- 5
Practice articulating the importance of these standards in your work.
Example Answers
In instrumentation, relevant standards include ISA-5.1, which covers instrumentation symbols and identification. Another important standard is IEC 61508 for functional safety, which ensures safe instrumentation practices.
What knowledge do you have regarding electrical circuits and their components?
How to Answer
- 1
Briefly describe basic electrical concepts like voltage, current, and resistance.
- 2
Mention common components such as resistors, capacitors, and inductors.
- 3
Explain how these components interact in a circuit.
- 4
Discuss the basics of circuit diagrams and how to read them.
- 5
Include any personal experience with circuits or related projects.
Example Answers
I understand that voltage is the potential difference, current is the flow of electrons, and resistance opposes this flow. I am familiar with components like resistors, which limit current, capacitors, which store energy, and inductors, which store magnetic energy. I've also practiced reading circuit diagrams during my electronics classes.
Are you familiar with any software used for instrument control or data logging? Please explain.
How to Answer
- 1
Identify relevant software you have used or learned about.
- 2
Mention specific features of the software that relate to instrument control or data logging.
- 3
Include any hands-on experiences or projects where you applied these software tools.
- 4
If you lack direct experience, discuss your willingness to learn new technologies.
- 5
Relate your software knowledge to the role of an instrument technician.
Example Answers
I have used LabVIEW in my previous coursework, where I learned to create data logging applications for instrument readings. It helped me understand how to visualize data in real time.
How would you analyze data obtained from instruments to ensure its accuracy?
How to Answer
- 1
Verify calibration of the instruments before data collection
- 2
Use statistical methods to identify anomalies or outliers
- 3
Cross-check data with established benchmarks or standards
- 4
Implement regular maintenance checks on instrumentation
- 5
Document all findings and discrepancies for further analysis
Example Answers
I would start by ensuring that all instruments are properly calibrated against known standards. Then, I would analyze the data using statistical methods to spot any outliers. This helps in identifying any potential inaccuracies in the data collected.
What regular maintenance steps would you take to ensure the longevity of an instrument?
How to Answer
- 1
Inspect instruments regularly for physical wear or damage.
- 2
Calibrate instruments according to manufacturer specifications.
- 3
Clean instruments frequently to prevent dust and contamination.
- 4
Replace worn or faulty components before they fail.
- 5
Document maintenance activities and any irregularities.
Example Answers
I would inspect instruments for damage, calibrate them as needed, clean them regularly, replace any worn parts promptly, and keep detailed records of maintenance.
What diagnostic tools do you consider essential for an instrument technician, and why?
How to Answer
- 1
Identify key diagnostic tools commonly used in the industry.
- 2
Explain the purpose and function of each tool briefly.
- 3
Relate the tools to common tasks or problems faced by instrument technicians.
- 4
Mention any personal experience you have using these tools.
- 5
Highlight how these tools enhance safety and efficiency in your work.
Example Answers
I consider a multimeter essential for an instrument technician because it allows me to measure voltage, current, and resistance accurately. It's crucial for troubleshooting electrical issues and verifying circuit conditions.
Don't Just Read Instrument Technician Apprentice Questions - Practice Answering Them!
Reading helps, but actual practice is what gets you hired. Our AI feedback system helps you improve your Instrument Technician Apprentice interview answers in real-time.
Personalized feedback
Unlimited practice
Used by hundreds of successful candidates
Can you discuss some recent technological advancements in instrumentation?
How to Answer
- 1
Identify one or two key advancements in instrumentation technology.
- 2
Explain how these advancements improve accuracy or efficiency.
- 3
Relate the advancements to current industry needs or trends.
- 4
Use specific examples or applications of the technologies.
- 5
Keep your response concise and to the point.
Example Answers
One recent advancement is the use of wireless transmitters for sensor data. These devices enhance accuracy and reduce installation costs by eliminating the need for wiring. They are particularly useful in remote locations for monitoring critical processes.
Situational Interview Questions
Imagine you have multiple deadlines approaching for instrument maintenance. How would you prioritize your tasks?
How to Answer
- 1
List all tasks and deadlines clearly.
- 2
Assess the criticality of each task based on safety and operational impact.
- 3
Estimate the time required for each task and identify any dependencies.
- 4
Communicate with team members to understand their priorities.
- 5
Start with high-priority tasks that have the nearest deadlines.
Example Answers
I would first list all the maintenance tasks along with their deadlines. Then, I would evaluate which tasks are critical for safety and which ones have the highest operational impact. After that, I would talk to my team to align on priorities and begin with the tasks that need immediate attention.
You're given a task to work on a project with a team. One member isn't contributing. What would you do?
How to Answer
- 1
Identify the reasons for the member's lack of contribution
- 2
Communicate directly with the unresponsive team member
- 3
Offer help or seek to understand their challenges
- 4
Involve the team leader if the issue persists
- 5
Maintain a positive team dynamic and stay focused on goals
Example Answers
I would first reach out to the team member to understand why they aren't contributing. Perhaps they're facing personal issues or need assistance. If they continue to be unresponsive, I would discuss the situation with our team leader to find a solution, while ensuring the team remains focused and motivated.
Don't Just Read Instrument Technician Apprentice Questions - Practice Answering Them!
Reading helps, but actual practice is what gets you hired. Our AI feedback system helps you improve your Instrument Technician Apprentice interview answers in real-time.
Personalized feedback
Unlimited practice
Used by hundreds of successful candidates
If you discovered a critical error in a report that had already been submitted, how would you address the situation?
How to Answer
- 1
Acknowledge the error immediately with honesty.
- 2
Assess the impact of the error on the report's conclusions.
- 3
Communicate the findings to your supervisor promptly.
- 4
Suggest corrective measures to resolve the issue.
- 5
Follow up to ensure the correction is processed properly.
Example Answers
I would first admit the error to my supervisor as soon as I find it. Then, I would evaluate how this mistake affects the overall report and its conclusions. After understanding the impact, I would inform my team and suggest a revision to correct the error promptly.
If you were assigned to install a new type of instrument you are unfamiliar with, what steps would you take to ensure the installation is successful?
How to Answer
- 1
Research the instrument specifications and installation guidelines beforehand
- 2
Consult with experienced colleagues or supervisors for insights
- 3
Familiarize yourself with necessary tools and safety precautions required for the installation
- 4
Conduct a site preparation and check compatibility with existing systems
- 5
Perform a test run or simulation before final installation, if possible
Example Answers
I would start by reading the instrument's manual thoroughly to understand its specifications and installation requirements. Then, I would ask a more experienced technician for advice on best practices and potential pitfalls. After that, I would ensure I have all the necessary tools and safety equipment prepared before I begin the installation.
You need to explain a complex technical issue to a non-technical client. How would you approach this?
How to Answer
- 1
Break down the technical issue into simple concepts
- 2
Use analogies or real-world examples to illustrate points
- 3
Avoid technical jargon and use everyday language
- 4
Check for understanding and ask if they have questions
- 5
Be patient and prepared to rephrase if needed
Example Answers
I would start by identifying the core issue and breaking it down into simpler parts. For example, if explaining a sensor's function, I might compare it to a thermometer that tells us the temperature. I would avoid terms like 'calibration' and just say it's like adjusting the thermometer to get accurate readings. Then I'd ask if they had any questions to ensure they understand.
If you need to complete an urgent calibration but lack the necessary tools, how would you handle it?
How to Answer
- 1
Assess the urgency and importance of the calibration
- 2
Check if any alternative tools or methods are available
- 3
Communicate the situation to your supervisor or team
- 4
Prioritize obtaining the necessary tools as quickly as possible
- 5
Document the issue and follow up with a plan to prevent future occurrences
Example Answers
I would first evaluate how urgent the calibration is, then I would look for any alternative tools in the workshop or consult with colleagues. If necessary, I would inform my supervisor about the situation, and emphasize getting the right tools while documenting the issue for future reference.
A customer requests a solution that you believe is not the best option. How would you address their request?
How to Answer
- 1
Acknowledge the customer's request positively
- 2
Explain your concerns clearly and respectfully
- 3
Provide an alternative solution that addresses their needs
- 4
Ask for their perspective to engage them in the discussion
- 5
Focus on the benefits of the alternative solution
Example Answers
I appreciate your suggestion and see why you'd want that. However, I have concerns about its long-term effectiveness. I recommend we consider another option that has proven results. What do you think?
If a team member is consistently missing deadlines, what approach would you take to address the issue?
How to Answer
- 1
Have a one-on-one conversation to understand the reasons behind the missed deadlines.
- 2
Be empathetic and listen actively to their challenges or workload.
- 3
Discuss how their missed deadlines affect the team and project.
- 4
Collaborate to find solutions, such as adjusting workload or providing help.
- 5
Set clear expectations and follow-up regularly to ensure progress.
Example Answers
I would first talk to the team member privately to understand their side and what challenges they are facing. It’s important to listen and empathize with them. Then, I would discuss how their missed deadlines impact our work and together we would come up with a plan to support them in meeting future deadlines.
You find a defect in a newly installed instrument. What steps would you take to rectify the issue?
How to Answer
- 1
Immediately notify your supervisor about the defect.
- 2
Document the details of the defect, including location and nature.
- 3
Isolate the instrument to prevent further operation until resolved.
- 4
Perform troubleshooting steps to identify the root cause.
- 5
Follow the manufacturer's guidelines to repair or replace the faulty components.
Example Answers
First, I would inform my supervisor about the defect to ensure safety and compliance. Then, I would document the defect's details fully. I would isolate the instrument to prevent any operation until it is fixed. Next, I would troubleshoot the issue and identify the root cause and finally, follow the guidelines for repair or replacement.
How would you respond if you noticed a colleague not following safety protocols?
How to Answer
- 1
Address the situation calmly and privately if possible.
- 2
Express concern for their safety and the safety of the team.
- 3
Refer to specific safety protocols they may be overlooking.
- 4
Encourage them to correct the behavior and ask if they need help.
- 5
If necessary, report the behavior to a supervisor for further action.
Example Answers
I would approach my colleague privately and say, 'I noticed you weren't wearing your safety gloves while working, which could lead to injuries. Can I help you remember to follow the protocol?'
Don't Just Read Instrument Technician Apprentice Questions - Practice Answering Them!
Reading helps, but actual practice is what gets you hired. Our AI feedback system helps you improve your Instrument Technician Apprentice interview answers in real-time.
Personalized feedback
Unlimited practice
Used by hundreds of successful candidates
Instrument Technician Apprentice Position Details
Salary Information
Recommended Job Boards
These job boards are ranked by relevance for this position.
Related Positions
Ace Your Next Interview!
Practice with AI feedback & get hired faster
Personalized feedback
Used by hundreds of successful candidates
Ace Your Next Interview!
Practice with AI feedback & get hired faster
Personalized feedback
Used by hundreds of successful candidates