Top 30 Manufacturing Consultant Interview Questions and Answers [Updated 2025]
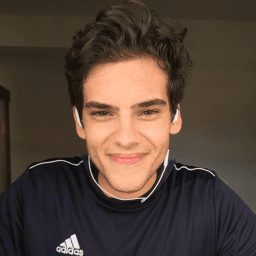
Andre Mendes
•
March 30, 2025
Navigating the job market can be daunting, especially when aiming for a specialized role like Manufacturing Consultant. This blog post is your ultimate guide to acing that crucial interview, featuring the most common questions candidates face. You'll discover example answers and insightful tips on how to respond effectively, ensuring you leave a lasting impression and boost your chances of success. Dive in and prepare to impress!
Download Manufacturing Consultant Interview Questions in PDF
To make your preparation even more convenient, we've compiled all these top Manufacturing Consultantinterview questions and answers into a handy PDF.
Click the button below to download the PDF and have easy access to these essential questions anytime, anywhere:
List of Manufacturing Consultant Interview Questions
Behavioral Interview Questions
Can you describe a time when you identified a major inefficiency in a manufacturing process and how you addressed it?
How to Answer
- 1
Choose a specific example from your experience.
- 2
Highlight the problem and its impact on production.
- 3
Explain the steps you took to identify and analyze the inefficiency.
- 4
Describe the solution you implemented and the outcome.
- 5
Quantify improvements if possible, using metrics or percentages.
Example Answers
In my previous role, I noticed that our assembly line had frequent delays due to a bottleneck in the packing area. I analyzed the workflow and realized that workers spent too much time waiting for materials. I implemented a just-in-time inventory system which reduced downtime by 30%, significantly speeding up overall production.
Tell me about a time when you had to work closely with a team to implement a new manufacturing process.
How to Answer
- 1
Use the STAR method: Situation, Task, Action, Result.
- 2
Describe the specific process you implemented with the team.
- 3
Highlight your role and contributions to the team's efforts.
- 4
Emphasize communication and collaboration aspects.
- 5
Share measurable outcomes or improvements achieved.
Example Answers
In my previous role, our team needed to implement a lean manufacturing process. I coordinated the project by organizing daily stand-up meetings to facilitate communication. My role involved training the team on new techniques and tracking progress. As a result, we increased efficiency by 20% within three months.
Good Candidates Answer Questions. Great Ones Win Offers.
Reading sample answers isn't enough. Top candidates practice speaking with confidence and clarity. Get real feedback, improve faster, and walk into your next interview ready to stand out.
Master your interview answers under pressure
Boost your confidence with real-time practice
Speak clearly and impress hiring managers
Get hired faster with focused preparation
Used by hundreds of successful candidates
Describe a situation where you led a team through a challenging manufacturing project.
How to Answer
- 1
Choose a specific project that had clear challenges
- 2
Explain your leadership style and how it contributed to success
- 3
Highlight the outcome and what was learned from the experience
- 4
Include metrics or data to demonstrate success
- 5
Reflect on team dynamics and collaboration techniques used
Example Answers
In 2021, I led a team in reducing production defects in a new assembly line. We faced significant delays and quality issues initially. By implementing lean techniques and daily stand-ups, we increased efficiency by 30% and reduced defects by 50% in three months. The team learned valuable problem-solving skills throughout this process.
Can you give an example of a conflict you faced with a colleague or client, and how you resolved it?
How to Answer
- 1
Identify a specific conflict situation you experienced
- 2
Explain the roles of the people involved without assigning blame
- 3
Describe the steps you took to resolve the conflict
- 4
Highlight the positive outcome of your resolution efforts
- 5
Emphasize any lessons learned from the experience
Example Answers
In a project, a colleague and I disagreed on the approach to streamline production. I initiated a meeting where we both presented our ideas. By facilitating an open discussion, we reached a compromise that incorporated elements from both approaches, resulting in a successful implementation and improved efficiency.
Describe a time when you had to adapt to a significant change in a manufacturing process or technology.
How to Answer
- 1
Identify a specific change you faced in a previous job.
- 2
Explain how you assessed the impact of the change on operations.
- 3
Describe the steps you took to adapt, including any training or process adjustments.
- 4
Highlight the positive outcomes of your adaptation.
- 5
Keep your answer focused on your role and contributions.
Example Answers
In my last position, we transitioned to a new automated assembly line. I first analyzed how it would affect our production rates and identified training needs for the team. I organized training sessions to ensure everyone was comfortable with the new technology. As a result, we improved production efficiency by 20% within the first month.
Describe a project you managed from start to finish. What were the key challenges and how did you overcome them?
How to Answer
- 1
Choose a relevant project that highlights your skills.
- 2
Outline the project's objectives and scope clearly.
- 3
Identify specific challenges you faced during the project.
- 4
Explain the strategies you used to overcome these challenges.
- 5
Conclude with the project's outcomes and your personal contributions.
Example Answers
I managed a project to implement a new inventory management system. The key challenge was resistance to change from staff. To address this, I organized workshops to explain the benefits and provided hands-on training. This helped increase buy-in, and we successfully rolled out the system on time, resulting in a 20% reduction in inventory costs.
Tell me about a time when you built a strong relationship with a client. What were the key actions you took?
How to Answer
- 1
Choose a specific client interaction that illustrates your relationship-building skills.
- 2
Highlight actions taken to understand the client's needs and preferences.
- 3
Mention how you established trust and communication with the client.
- 4
Include any follow-ups or continued support you provided.
- 5
Emphasize the positive outcome of the relationship.
Example Answers
In a project with a manufacturing client, I took the time to understand their specific production challenges. I set up regular check-in meetings to discuss progress and adjustments. By being responsive to their feedback, I built their trust. The outcome was a successful project that increased their efficiency by 20%.
Describe a time when you brought an innovative idea to a manufacturing team and how it was implemented.
How to Answer
- 1
Choose a specific innovative idea relevant to manufacturing.
- 2
Explain the problem that the idea addressed and why it was needed.
- 3
Detail the steps taken to implement the idea and involve the team.
- 4
Mention the outcome and any metrics that demonstrate success.
- 5
Reflect on what you learned through the process.
Example Answers
In my previous role, I noticed our assembly line had frequent downtime due to manual part retrieval. I proposed implementing a Kanban system to automate part inventory management. I collaborated with the team to set it up, and within three months, we reduced downtime by 30%, leading to increased productivity.
Give an example of how you effectively communicated a complex manufacturing issue to a non-technical audience.
How to Answer
- 1
Identify the complex issue and its key points.
- 2
Simplify the terminology without losing the core message.
- 3
Use analogies or visual aids to clarify concepts.
- 4
Engage the audience with questions to ensure understanding.
- 5
Summarize the key takeaways at the end of the discussion.
Example Answers
In a previous role, I explained a supply chain delay caused by quality control issues. I avoided technical jargon and compared the process to a car assembly line, emphasizing how a single malfunction can halt production. I used a simple graphic to show the workflow and checked for understanding by asking if there were any questions before I summarized the key steps we were taking to resolve the issue.
Good Candidates Answer Questions. Great Ones Win Offers.
Reading sample answers isn't enough. Top candidates practice speaking with confidence and clarity. Get real feedback, improve faster, and walk into your next interview ready to stand out.
Master your interview answers under pressure
Boost your confidence with real-time practice
Speak clearly and impress hiring managers
Get hired faster with focused preparation
Used by hundreds of successful candidates
Technical Interview Questions
What are the key principles of lean manufacturing, and how have you applied them in past roles?
How to Answer
- 1
Identify the main principles of lean manufacturing such as value, value stream, flow, pull, and perfection.
- 2
Provide specific examples of how you implemented these principles in your previous jobs.
- 3
Use metrics or results to highlight the impact of your actions.
- 4
Discuss any tools or methodologies used, like 5S, Kaizen, or Value Stream Mapping.
- 5
Show your understanding of continuous improvement and how it ties into lean practices.
Example Answers
In my previous role at XYZ Corp, I focused on the principle of value by conducting customer feedback sessions to identify what features were most critical. This helped reduce waste and streamline our product offering by 20%.
What experience do you have with Six Sigma methodologies, and can you explain how you have used these in past projects?
How to Answer
- 1
Highlight specific Six Sigma certifications or training you possess
- 2
Describe a project where you applied Six Sigma tools like DMAIC or DMADV
- 3
Mention the impact of your work, using metrics when possible
- 4
Showcase your role in the project, such as leading a team or being a team member
- 5
Be prepared with examples that demonstrate problem-solving and process improvement
Example Answers
I am a certified Six Sigma Green Belt and have led a project using DMAIC to reduce defects in our manufacturing process by 25%, which saved the company $200,000 annually.
Good Candidates Answer Questions. Great Ones Win Offers.
Reading sample answers isn't enough. Top candidates practice speaking with confidence and clarity. Get real feedback, improve faster, and walk into your next interview ready to stand out.
Master your interview answers under pressure
Boost your confidence with real-time practice
Speak clearly and impress hiring managers
Get hired faster with focused preparation
Used by hundreds of successful candidates
How do you approach capacity planning in a manufacturing environment?
How to Answer
- 1
Assess current production capacity and usage rates.
- 2
Analyze future demand forecasts and trends.
- 3
Identify bottlenecks in the manufacturing process.
- 4
Evaluate resource availability including workforce and materials.
- 5
Develop a flexible plan that can adapt to changes in demand.
Example Answers
I start by looking at the current production data to determine our usage rates. Then, I analyze forecasts to anticipate demand. I always check for bottlenecks that could limit capacity and ensure we have enough resources on hand. Finally, I prepare a capacity plan that can be adjusted as needed.
What methodologies do you use for process optimization, and can you provide an example where you applied them successfully?
How to Answer
- 1
Identify key methodologies like Lean, Six Sigma, or Kaizen
- 2
Choose one or two methodologies to focus on and explain their relevance
- 3
Share a specific example with measurable results
- 4
Highlight your role in the project and the impact of your actions
- 5
Conclude with lessons learned or future applications of the methodology
Example Answers
I primarily use Lean methodology which focuses on eliminating waste. In a recent project at a manufacturing plant, I led a Kaizen event where we streamlined the assembly line process, reducing cycle time by 20%. I analyzed workflow, identified bottlenecks, and implemented changes that improved overall efficiency.
What types of data analysis tools do you use in your work, and how do they aid in decision-making?
How to Answer
- 1
Identify specific tools you use, such as Excel, Tableau, or specialized software.
- 2
Explain how each tool is applied in a manufacturing context.
- 3
Highlight how these tools improve efficiency or accuracy in decision-making.
- 4
Discuss any relevant metrics you track with these tools.
- 5
Mention any experience with data visualization or reporting.
Example Answers
I primarily use Excel for data analysis, leveraging pivot tables to summarize production data. This helps identify trends in operational efficiency, guiding our resource allocation effectively.
What manufacturing software solutions have you worked with, and how did they impact your projects?
How to Answer
- 1
Identify specific software you have used.
- 2
Explain your role and how you utilized the software.
- 3
Discuss measurable outcomes or improvements from using the software.
- 4
Connect the software's capabilities to the project's success.
- 5
Be concise and focus on relevant examples.
Example Answers
I have worked with SAP ERP for managing supply chain processes. By using its inventory management features, we reduced stock holding costs by 15% over a six-month period.
How do you ensure alignment between supply chain management and manufacturing operations?
How to Answer
- 1
Establish regular communication between supply chain and manufacturing teams
- 2
Utilize integrated software systems for real-time data sharing
- 3
Align production schedules with supply chain forecasts
- 4
Involve both teams in planning sessions to address potential disruptions
- 5
Use key performance indicators to monitor alignment and address gaps
Example Answers
I ensure alignment by facilitating weekly meetings between supply chain and manufacturing teams, allowing us to discuss forecasts and production schedules collaboratively.
Can you explain how you have used statistical process control (SPC) in your work?
How to Answer
- 1
Identify specific projects where you applied SPC.
- 2
Mention the tools or methods you used for SPC.
- 3
Highlight results or improvements from your SPC efforts.
- 4
Discuss any challenges you faced and how you overcame them.
- 5
Keep the explanation clear and focused, avoid jargon.
Example Answers
In my last role, I implemented SPC using control charts for our assembly line. This helped me identify variations and reduce defects by 15% over six months, improving overall quality.
What experience do you have with implementing automation in manufacturing plants?
How to Answer
- 1
Highlight specific projects where you introduced automation.
- 2
Describe the technology or systems you implemented.
- 3
Discuss the impact on efficiency, cost savings, or production quality.
- 4
Mention collaboration with team members or stakeholders.
- 5
Include any challenges faced and how you overcame them.
Example Answers
In my previous role, I led a project to implement robotic arms on the assembly line which improved production speed by 30%. I worked closely with the engineering team to integrate the systems successfully.
What are some key industry standards you follow in manufacturing consulting, and how do they influence your work?
How to Answer
- 1
Identify 2-3 key industry standards relevant to manufacturing.
- 2
Explain how these standards guide your decision-making and processes.
- 3
Provide examples of how you've implemented these standards in past projects.
- 4
Mention the benefits these standards bring to your clients.
- 5
Keep your response concise and focused on your personal experience.
Example Answers
I follow Lean Manufacturing and Six Sigma as key standards. Lean helps reduce waste in processes, while Six Sigma improves quality by minimizing defects. In my last project, I used Lean methodologies to streamline production, which resulted in a 20% increase in efficiency, saving the client significant costs.
Good Candidates Answer Questions. Great Ones Win Offers.
Reading sample answers isn't enough. Top candidates practice speaking with confidence and clarity. Get real feedback, improve faster, and walk into your next interview ready to stand out.
Master your interview answers under pressure
Boost your confidence with real-time practice
Speak clearly and impress hiring managers
Get hired faster with focused preparation
Used by hundreds of successful candidates
Situational Interview Questions
A client’s production line is facing a significant quality issue with rising defect rates. How would you approach solving this problem?
How to Answer
- 1
Start by gathering data on the defect rates to identify patterns.
- 2
Engage with production staff to understand their perspectives and challenges.
- 3
Evaluate the production process and equipment for potential flaws.
- 4
Implement a trial solution and measure its impact on defect rates.
- 5
Provide recommendations based on data and staff feedback for ongoing improvement.
Example Answers
I would begin by analyzing the defect data to pinpoint when and where the defects occur. Then, I would consult with the production team to gain insights into any issues they are facing. After identifying potential root causes, I would test a targeted solution and monitor the results to ensure the defect rates decline.
If a company needs to reduce manufacturing costs by 20% without sacrificing quality, what strategies would you propose?
How to Answer
- 1
Analyze current manufacturing processes to identify inefficiencies
- 2
Implement lean manufacturing techniques to minimize waste
- 3
Negotiate better rates with suppliers for raw materials
- 4
Invest in technology to automate repetitive tasks and improve productivity
- 5
Enhance employee training to boost efficiency and reduce errors
Example Answers
I would first conduct a thorough analysis of our current processes to find areas where we can streamline operations. Implementing lean techniques could reduce waste and enhance efficiency without compromising quality.
Good Candidates Answer Questions. Great Ones Win Offers.
Reading sample answers isn't enough. Top candidates practice speaking with confidence and clarity. Get real feedback, improve faster, and walk into your next interview ready to stand out.
Master your interview answers under pressure
Boost your confidence with real-time practice
Speak clearly and impress hiring managers
Get hired faster with focused preparation
Used by hundreds of successful candidates
A client is resistant to implementing automation in their manufacturing facility. How would you facilitate and manage this change?
How to Answer
- 1
Start by understanding the client's concerns about automation.
- 2
Present case studies or data showing the benefits of automation.
- 3
Involve stakeholders in discussions to address fears and gather input.
- 4
Propose a pilot project to demonstrate automation's effectiveness.
- 5
Highlight long-term cost savings and efficiency improvements.
Example Answers
First, I would meet with the client to identify their specific concerns with automation. By showing them successful case studies of similar companies, I aim to build trust. Then, I would involve key stakeholders in workshops to discuss the proposed changes, allowing them to voice their fears. Finally, I would suggest starting with a small pilot project to showcase the results before fully implementing.
How would you go about creating a process map for a new manufacturing line in a plant?
How to Answer
- 1
Identify key processes involved in the manufacturing line
- 2
Gather input from stakeholders and team members
- 3
Use flowchart tools to visualize each step
- 4
Include inputs, outputs, and decision points in the map
- 5
Review and refine the map with the team for accuracy
Example Answers
To create a process map for a new manufacturing line, I would first identify the key steps involved in production. Then, I would gather input from the engineering and operations teams to ensure accuracy. I would use a flowchart tool to visualize the processes, making sure to include all relevant inputs and decision points. Finally, I would present the draft map to the team for feedback and make necessary adjustments.
A supplier is consistently late with deliveries, affecting production. How would you handle this situation?
How to Answer
- 1
Assess the impact on production and gather data on the delays.
- 2
Communicate directly with the supplier to understand the root cause.
- 3
Explore potential solutions or alternatives with the supplier.
- 4
Consider developing a contingency plan for future delays.
- 5
Document the situation and review supplier performance regularly.
Example Answers
I would first analyze the extent of the impact on production and gather data on the timing of the delays. Then, I would schedule a meeting with the supplier to discuss the issues they are facing, aiming to understand the root cause. Together, we would explore possible solutions, such as adjusting order schedules or finding temporary alternatives.
What steps would you take to integrate a new technology into an existing production line?
How to Answer
- 1
Assess current production line capabilities and limitations.
- 2
Identify the specific technology needs and benefits.
- 3
Develop a clear integration plan with timelines and milestones.
- 4
Train staff on the new technology and its applications.
- 5
Monitor performance and gather feedback for continuous improvement.
Example Answers
First, I would evaluate the existing production line to understand where the new technology can add value. Next, I'd identify the specific requirements of the new technology to ensure it's a good fit. Then, I would create a step-by-step plan for implementation, including training sessions for staff. Once integrated, I would track the performance metrics and gather feedback to assess effectiveness.
A client is aiming to scale up production by 50% over the next year. How would you assist them in achieving this goal?
How to Answer
- 1
Analyze current production processes to identify bottlenecks.
- 2
Assess resource availability including labor, materials, and machinery.
- 3
Develop a phased production plan for gradual scaling.
- 4
Implement measures for quality control during increased output.
- 5
Provide training for staff on new processes or equipment.
Example Answers
To help the client scale up production by 50%, I would first analyze their current processes to identify any bottlenecks. Then, I would review their resources to ensure they can meet increased demand. After that, I'd create a phased plan to scale up while maintaining quality and efficiency.
A sudden machine breakdown is causing a production halt. What immediate actions would you take?
How to Answer
- 1
Assess the situation to understand the cause of the breakdown.
- 2
Communicate the issue to the team and relevant stakeholders.
- 3
Initiate emergency troubleshooting and repairs if possible.
- 4
Evaluate the impact on production schedules and notify affected areas.
- 5
Implement solutions to minimize downtime and plan for future preventative measures.
Example Answers
First, I would quickly assess the machine to identify the breakdown cause. Then, I would inform the production team and management. If feasible, I would start troubleshooting to fix the issue on the spot, otherwise I would arrange for maintenance to take over. After understanding the downtime impact, I would communicate with affected departments.
How would you design a training program for new employees on a manufacturing line?
How to Answer
- 1
Assess the specific skills needed for the manufacturing line.
- 2
Create a structured training schedule with clear objectives.
- 3
Incorporate hands-on practice alongside theoretical learning.
- 4
Use experienced staff as mentors during the training process.
- 5
Gather feedback and adjust the program based on trainee performance.
Example Answers
I would start by identifying the essential skills required for the manufacturing line, then develop a training schedule that covers these areas in detail. Hands-on practice would be crucial, so I would include exercises where new employees can apply what they've learned while being guided by experienced team members.
A recent audit revealed compliance issues in a client’s plant. How would you address and resolve these issues?
How to Answer
- 1
Identify specific compliance issues found during the audit
- 2
Gather data and input from operational staff to understand root causes
- 3
Develop a clear action plan with timelines and responsibilities
- 4
Implement training sessions for staff to ensure compliance understanding
- 5
Monitor progress and adjust strategies based on results
Example Answers
I would start by reviewing the audit report to pinpoint specific compliance issues. Next, I would conduct interviews with the staff to understand the challenges they face. Then, I would create an action plan that outlines necessary changes, assign tasks, and ensure staff receives proper training on compliance protocols. Finally, I would establish a monitoring system to track the effectiveness of the implemented solutions.
Good Candidates Answer Questions. Great Ones Win Offers.
Reading sample answers isn't enough. Top candidates practice speaking with confidence and clarity. Get real feedback, improve faster, and walk into your next interview ready to stand out.
Master your interview answers under pressure
Boost your confidence with real-time practice
Speak clearly and impress hiring managers
Get hired faster with focused preparation
Used by hundreds of successful candidates
Manufacturing Consultant Position Details
Salary Information
Recommended Job Boards
CareerBuilder
www.careerbuilder.com/jobs-manufacturing-consultantThese job boards are ranked by relevance for this position.
Related Positions
- Manufacturing Technologist
- Manufacturing Associate
- Industrial Technologist
- Industrial Engineering Technologist
- Industrial Engineering Technician
- Additive Manufacturing Technician
- Production Technician
- Production Control Analyst
- Productivity Engineer
- Industrial Technician
Similar positions you might be interested in.
Good Candidates Answer Questions. Great Ones Win Offers.
Master your interview answers under pressure
Boost your confidence with real-time practice
Speak clearly and impress hiring managers
Get hired faster with focused preparation
Used by hundreds of successful candidates
Good Candidates Answer Questions. Great Ones Win Offers.
Master your interview answers under pressure
Boost your confidence with real-time practice
Speak clearly and impress hiring managers
Get hired faster with focused preparation
Used by hundreds of successful candidates